Your Ultimate Guide to Sourcing Scrub Dress
Guide to Scrub Dress
- Introduction: Navigating the Global Market for scrub dress
- Understanding scrub dress Types and Variations
- Key Industrial Applications of scrub dress
- Strategic Material Selection Guide for scrub dress
- In-depth Look: Manufacturing Processes and Quality Assurance for scrub dress
- Comprehensive Cost and Pricing Analysis for scrub dress Sourcing
- Spotlight on Potential scrub dress Manufacturers and Suppliers
- Essential Technical Properties and Trade Terminology for scrub dress
- Navigating Market Dynamics, Sourcing Trends, and Sustainability in the scrub dress Sector
- Frequently Asked Questions (FAQs) for B2B Buyers of scrub dress
- Strategic Sourcing Conclusion and Outlook for scrub dress
Introduction: Navigating the Global Market for scrub dress
The global healthcare sector increasingly demands reliable, comfortable, and durable scrub dresses that meet diverse clinical needs and regional preferences. For international B2B buyers in Africa, South America, the Middle East, and Europe—markets characterized by unique regulatory frameworks, climate considerations, and cultural expectations—sourcing the right scrub dress is both a strategic and operational imperative. As frontline medical apparel, scrub dresses must balance functionality, hygiene standards, and wearer comfort, making informed sourcing decisions critical to supplier partnerships and patient care outcomes.
This comprehensive guide delves into the multifaceted world of scrub dress procurement, offering actionable insights across key dimensions:
- Diverse Types & Styles: From classic two-piece sets to modern unisex and antimicrobial designs tailored for various healthcare environments.
- Material Selection: Evaluating fabric options such as breathable cotton blends, sustainable Tencel, and performance-enhancing synthetics aligned with durability and comfort.
- Manufacturing & Quality Control: Understanding production methods, compliance with international standards, and rigorous quality assurance protocols that ensure consistent product excellence.
- Supplier Landscape: Identifying reputable manufacturers and private-label partners across Asia, Europe, and emerging markets, with an emphasis on ethical sourcing and tariff-aware strategies.
- Cost Analysis & Market Trends: Navigating pricing structures, tariff impacts, and evolving global trade dynamics shaping supply chain resilience.
- FAQs & Best Practices: Addressing common buyer concerns and providing practical tips for seamless procurement and inventory management.
By equipping buyers with this deep market intelligence and operational know-how, the guide empowers organizations to optimize their sourcing strategies, mitigate risks related to tariffs and supply disruptions, and ultimately secure scrub dresses that elevate healthcare delivery standards across continents.
Understanding scrub dress Types and Variations
Type Name | Key Distinguishing Features | Primary B2B Applications | Brief Pros & Cons for Buyers |
---|---|---|---|
Classic A-Line Scrub Dress | Fitted bodice with a slight flare at the skirt; knee-length | Hospitals, clinics, general healthcare settings | Pros: Timeless style, comfortable fit; Cons: Limited mobility for some tasks |
Tunic-Style Scrub Dress | Loose fit with side slits and pockets; often mid-thigh length | Dental offices, veterinary clinics, outpatient care | Pros: Enhanced mobility and storage; Cons: May appear less formal |
Zip-Front Scrub Dress | Front zipper closure for easy wear; often with structured seams | Surgical centers, emergency rooms, specialized care units | Pros: Quick on/off, professional look; Cons: Slightly higher production cost |
Eco-Friendly Scrub Dress | Made from sustainable or recycled fabrics; often blended materials | Organizations emphasizing sustainability and CSR | Pros: Appeals to eco-conscious buyers, regulatory compliance; Cons: Higher unit cost |
Plus-Size Scrub Dress | Extended sizing with ergonomic tailoring for comfort | Inclusive healthcare providers, large workforce environments | Pros: Inclusive fit, improved comfort; Cons: Requires broader inventory management |
Classic A-Line Scrub Dress
This style features a fitted bodice that gently flares out into an A-line skirt, typically knee-length, balancing professionalism and comfort. It suits traditional hospital and clinic environments where a neat, standardized appearance is important. For B2B buyers, the classic A-line dress offers reliability and broad appeal but may limit mobility for more physically demanding roles. When sourcing, consider fabric durability and ease of care to maintain long-term value.
Tunic-Style Scrub Dress
Characterized by a loose fit with side slits and multiple pockets, the tunic-style scrub dress prioritizes mobility and utility. It is ideal for outpatient clinics, dental offices, and veterinary practices where ease of movement and storage are critical. Buyers should evaluate fabric blends that resist staining and maintain breathability. This type’s casual aesthetic may not fit all institutional dress codes but enhances day-to-day worker productivity.
Zip-Front Scrub Dress
Featuring a front zipper closure and often with structured seams, this scrub dress variation is designed for quick changes and a polished appearance. It is preferred in high-intensity settings like surgical centers and emergency rooms where fast dressing and professional presentation are essential. B2B purchasers should weigh the slightly higher manufacturing costs against benefits in user convenience and durability, ensuring suppliers offer quality zippers and reinforced stitching.
Eco-Friendly Scrub Dress
Made from sustainable materials such as organic cotton blends or recycled polyester, eco-friendly scrub dresses appeal to organizations focused on corporate social responsibility and environmental impact. These are increasingly popular in European and Middle Eastern markets with strict sustainability mandates. Buyers must factor in higher unit costs and confirm certifications like GOTS or OEKO-TEX. Partnering with manufacturers specializing in sustainable textiles can ensure compliance and brand alignment.
Plus-Size Scrub Dress
Offering extended sizing with ergonomic tailoring, plus-size scrub dresses support workforce inclusivity and comfort. This type is crucial for healthcare providers with diverse staff demographics across Africa, South America, and Europe. Buyers need to manage inventory complexity but gain in employee satisfaction and reduced turnover. Attention to fabric stretch and reinforcement in high-stress areas enhances garment longevity and wearer comfort.
Related Video: WWL Surgical Scrub and Gowning -A Step by Step Guide
Key Industrial Applications of scrub dress
Industry/Sector | Specific Application of scrub dress | Value/Benefit for the Business | Key Sourcing Considerations for this Application |
---|---|---|---|
Healthcare | Surgical and clinical staff uniforms | Infection control, professional appearance, durability | Fabric antimicrobial properties, comfort, compliance with medical standards, easy laundering |
Pharmaceuticals | Cleanroom and laboratory personnel attire | Contamination prevention, regulatory compliance | Material certifications (e.g., ISO cleanroom standards), chemical resistance, sourcing reliable manufacturers |
Hospitality & Wellness | Spa and wellness center staff uniforms | Comfort, hygiene, brand consistency | Breathable fabrics, colorfastness, customization options |
Veterinary Services | Veterinary clinics and animal care staff uniforms | Protection from biological contaminants, ease of cleaning | Durable, stain-resistant materials, ergonomic design |
Educational Institutions | Medical and nursing training uniforms | Practicality for training environments, hygiene | Cost-effectiveness, durability, supplier reliability |
Healthcare
In hospitals and clinics across Africa, South America, the Middle East, and Europe, scrub dresses serve as essential uniforms for surgical and clinical staff. Their primary role is to maintain hygiene and reduce infection risks during patient care. For B2B buyers, sourcing scrubs with antimicrobial fabrics and certifications that meet international medical standards is critical. Additionally, comfort and durability are vital to withstand frequent laundering and long shifts, ensuring staff remain professional and focused.
Pharmaceuticals
In pharmaceutical manufacturing and research labs, scrub dresses are used to prevent contamination and maintain sterile environments. International buyers, especially in regions with strict regulatory frameworks like Europe and the Middle East, must prioritize materials that comply with cleanroom standards such as ISO classifications. Chemical resistance and fabric durability are also essential to protect staff and maintain product integrity, making supplier reliability and certification verification key sourcing factors.
Hospitality & Wellness
Spa and wellness centers require staff uniforms that combine comfort and hygiene while reinforcing brand identity. Scrub dresses in this sector must be breathable and easy to maintain, supporting long working hours in warm climates typical of many African and South American countries. B2B buyers should focus on fabric quality that ensures colorfastness and durability, along with customization options for logo embroidery or color schemes that align with corporate branding.
Veterinary Services
Veterinary clinics and animal care facilities use scrub dresses to protect staff from biological contaminants and facilitate easy cleaning after exposure to animal fluids. For international buyers, especially in regions with varying climate conditions like Indonesia and Germany, sourcing scrubs made from stain-resistant, durable materials with ergonomic designs enhances staff comfort and safety. Supplier flexibility to provide specialized fabrics and sizes is also important for this niche market.
Educational Institutions
Medical and nursing schools rely on scrub dresses as practical uniforms for students during clinical training. These garments must balance cost-effectiveness with durability to withstand rigorous use and frequent washing. B2B buyers in emerging markets in Africa and South America benefit from suppliers offering bulk purchasing options and consistent quality, ensuring that educational institutions can maintain hygiene standards and professional appearance without compromising budget constraints.
Related Video: LABORATORY APPARATUS AND THEIR USES
Strategic Material Selection Guide for scrub dress
When selecting materials for scrub dresses, international B2B buyers must balance performance, cost, manufacturing feasibility, and compliance with regional standards. Scrub dresses require fabrics that offer comfort, durability, and ease of maintenance, while also meeting healthcare hygiene and safety standards. Below is a detailed analysis of four common fabric materials used in scrub dresses, highlighting their properties, pros and cons, and regional considerations for buyers in Africa, South America, the Middle East, and Europe.
Cotton
Key Properties:
Cotton is a natural fiber known for its breathability, moisture absorption, and softness. It offers moderate durability and is comfortable in warm climates, making it suitable for long shifts in healthcare settings.
Pros & Cons:
Cotton is hypoallergenic and easy to dye, supporting vibrant colors and prints. However, it wrinkles easily and has lower resistance to stains and microbial growth compared to synthetic blends. Pure cotton scrubs may shrink or lose shape after repeated washing, increasing long-term costs.
Impact on Application:
Cotton is ideal for environments where comfort and breathability are priorities, such as tropical or subtropical regions (e.g., parts of Africa and South America). It is less suitable for high-contamination zones without antimicrobial treatment.
Regional Considerations:
Buyers in Europe (e.g., Germany) and the Middle East often require compliance with standards like OEKO-TEX® and GOTS for organic cotton, ensuring chemical safety and sustainability. African and South American buyers may prioritize cost-effective, locally sourced cotton blends, but should verify supplier certifications to avoid substandard quality.
Polyester-Cotton Blends (Poly-Cotton)
Key Properties:
Poly-cotton blends combine the breathability of cotton with the durability and wrinkle resistance of polyester. Typically, blends range from 65% polyester/35% cotton to 50/50.
Pros & Cons:
These blends are more durable and colorfast than pure cotton, with better resistance to shrinking and stretching. They dry faster and are easier to maintain. However, polyester content reduces breathability and may cause discomfort in hot climates if not properly engineered.
Impact on Application:
Poly-cotton blends are widely used for scrub dresses in diverse climates due to their balance of comfort and durability. They perform well in high-wear hospital environments and are compatible with industrial laundering.
Regional Considerations:
European buyers often require compliance with REACH regulations for chemical safety in polyester fibers. Middle Eastern markets may prefer blends with higher polyester content for durability under frequent washing. African and South American buyers should consider local laundering capabilities and climate when selecting blend ratios.
Spandex/Elastane Blends
Key Properties:
Adding 3-5% spandex or elastane to fabric blends provides stretchability and shape retention. This enhances mobility and comfort for healthcare workers during long shifts.
Pros & Cons:
Spandex blends improve fit and reduce garment deformation but increase manufacturing complexity and cost. They may retain heat and reduce breathability, which can be uncomfortable in hot or humid environments.
Impact on Application:
Ideal for scrub dresses requiring flexibility and a modern fit, especially in surgical or emergency care settings where movement is critical. Not recommended for extremely hot climates unless combined with moisture-wicking fabrics.
Regional Considerations:
European buyers often expect spandex blends to meet Oeko-Tex® standards for skin safety. In the Middle East and parts of South America, buyers should verify that stretch fabrics are compatible with local laundering practices to prevent premature wear. African buyers may prioritize durability over stretch due to cost constraints.
Tencel (Lyocell)
Key Properties:
Tencel is a sustainable, semi-synthetic fiber derived from wood pulp. It is highly breathable, moisture-wicking, and naturally antimicrobial, offering excellent comfort and hygiene.
Pros & Cons:
Tencel fabrics are soft, resistant to wrinkles, and environmentally friendly. However, they are more expensive and require careful sourcing to ensure certifications like FSC or PEFC for sustainable forestry. Manufacturing complexity is higher, and supply chains can be less established.
Impact on Application:
Tencel is suitable for premium scrub dresses targeting eco-conscious healthcare facilities and regions with strict environmental regulations. Its antimicrobial properties add value in infection control.
Regional Considerations:
European buyers, especially in Germany, prioritize sustainability certifications and eco-labels. Middle Eastern buyers are increasingly interested in sustainable textiles but may face supply constraints. African and South American buyers should weigh cost versus sustainability benefits and explore blended options to optimize price.
Material | Typical Use Case for scrub dress | Key Advantage | Key Disadvantage/Limitation | Relative Cost (Low/Med/High) |
---|---|---|---|---|
Cotton | Comfortable, breathable scrubs for warm climates | Natural fiber, breathable, hypoallergenic | Wrinkles easily, less durable, shrinks | Medium |
Polyester-Cotton Blend | Durable, easy-care scrubs for diverse environments | Durable, wrinkle-resistant, colorfast | Reduced breathability, may trap heat | Medium |
Spandex/Elastane Blend | Flexible, form-fitting scrubs for active healthcare roles | Stretchable, retains shape, enhances comfort | Higher cost, less breathable, complex to sew | High |
Tencel (Lyocell) | Premium, sustainable scrubs with antimicrobial properties | Eco-friendly, soft, moisture-wicking | Higher cost, supply chain complexity | High |
This guide helps B2B buyers strategically select scrub dress materials that align with their target markets’ climate, regulatory requirements, and cost constraints, while ensuring product performance and compliance across diverse international regions.
In-depth Look: Manufacturing Processes and Quality Assurance for scrub dress
Manufacturing Processes for Scrub Dress: Key Stages and Techniques
The production of scrub dresses involves a meticulous sequence of manufacturing stages, each critical to delivering a garment that meets stringent healthcare standards while satisfying buyer specifications. Understanding these phases allows international B2B buyers—from Africa, South America, the Middle East, and Europe—to better evaluate potential suppliers and ensure product quality, compliance, and timely delivery.
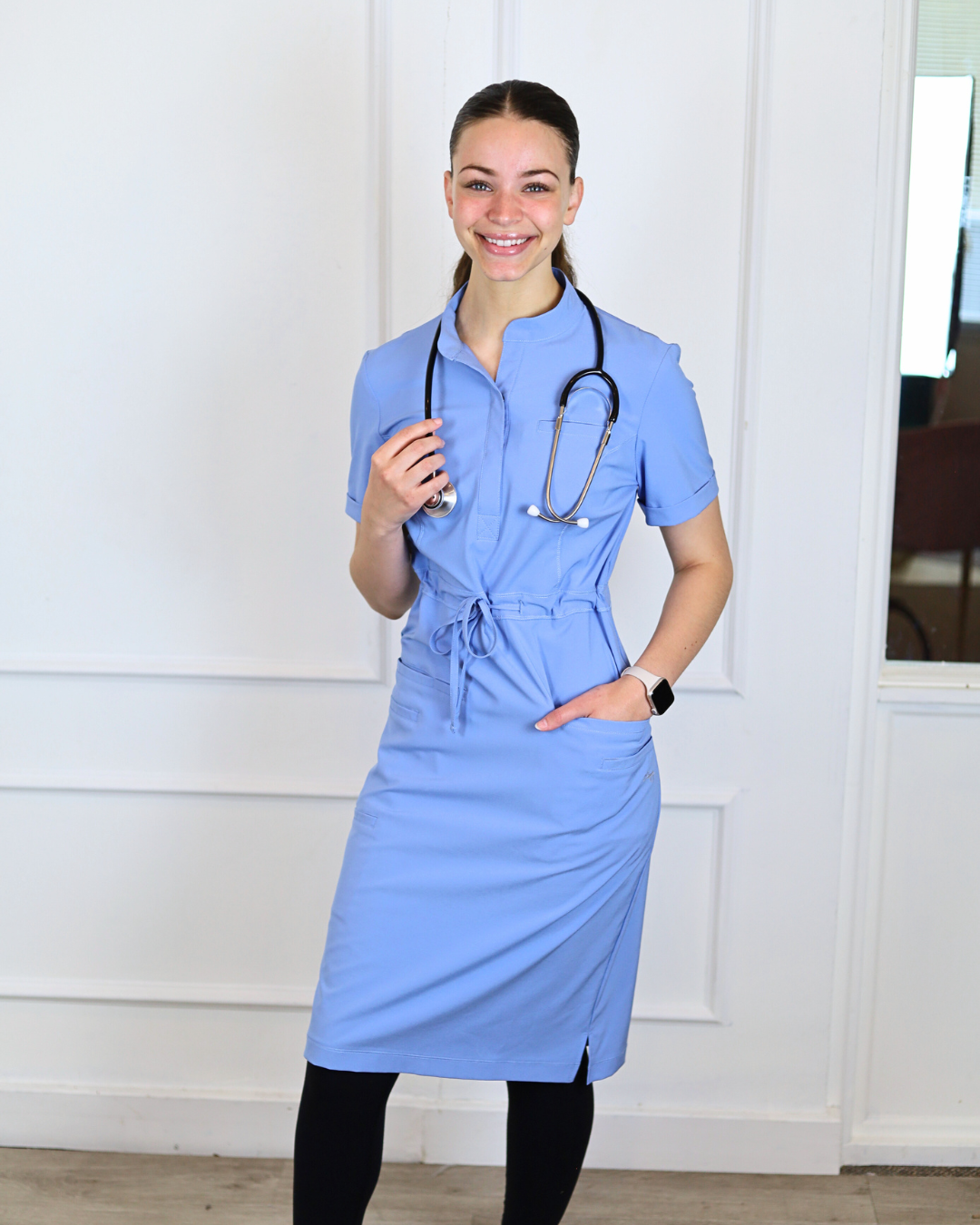
Illustrative Image (Source: Google Search)
1. Material Preparation
Material preparation is the foundation of quality scrub dress manufacturing. This stage involves:
- Fabric Selection and Inspection: Scrubs typically use fabrics such as cotton-polyester blends, polyester microfibers, or antimicrobial-treated textiles. The fabric must be inspected for defects, color consistency, and tensile strength.
- Pre-treatment: Depending on the fabric type, processes like washing, heat-setting, or chemical finishing (e.g., anti-wrinkle, anti-bacterial coatings) are applied to enhance performance.
- Cutting: Fabric is laid out in multiple layers and cut using manual or automated cutting machines (e.g., CNC cutters) to ensure precision and reduce waste.
2. Forming and Assembly
This stage transforms raw fabric pieces into the scrub dress shape:
- Sewing and Stitching: Skilled operators or automated sewing machines assemble the cut pieces using reinforced stitching patterns that ensure durability, especially at stress points like seams and pockets.
- Patterning: Scrub dress designs often include functional features such as multiple pockets, side vents, and adjustable closures. These are integrated during assembly with precision.
- Embroidery and Labeling: Branding, size tags, and compliance labels are added here, often using automated embroidery machines.
3. Finishing
Finishing is essential to ensure the garment meets aesthetic and functional standards:
- Pressing and Folding: Garments are pressed to remove wrinkles and folded for packaging.
- Quality Inspection: Initial visual and tactile inspections confirm fabric integrity and garment construction.
- Packaging: Scrubs are packed individually or in bulk, depending on buyer requirements, with consideration for hygiene and transport safety.
Quality Assurance and Control (QA/QC) Framework for Scrub Dresses
Implementing a robust QA/QC process is non-negotiable in the scrub dress supply chain. Healthcare apparel demands high standards for hygiene, durability, and comfort, making quality control a critical factor for B2B buyers sourcing internationally.
Relevant International and Industry Standards
- ISO 9001: The globally recognized quality management system standard ensures that manufacturers maintain consistent production processes and continuous improvement.
- EN 13795 (Europe): Specifies requirements for surgical clothing and drapes, including scrub dresses, focusing on barrier performance and cleanliness.
- CE Marking: Indicates conformity with health, safety, and environmental protection standards in the European Economic Area (EEA).
- ASTM and AAMI Standards (USA): Although more US-centric, these standards are often referenced globally for healthcare textiles.
- Local Regulatory Compliance: Buyers in regions like the Middle East, South America, and Africa should verify compliance with local medical textile regulations or certifications.
QC Checkpoints Across Manufacturing
Quality control is divided into stages aligned with production milestones:
- Incoming Quality Control (IQC): Inspection of raw materials—fabrics, threads, trims—to verify they meet agreed specifications before production starts.
- In-Process Quality Control (IPQC): Continuous monitoring during sewing and assembly to detect defects early, such as stitching errors or fabric inconsistencies.
- Final Quality Control (FQC): Comprehensive evaluation of finished scrub dresses, including dimensional checks, seam strength tests, color fastness, and visual inspections.
Common Testing Methods
- Dimensional Accuracy: Measurement of garment sizes against technical specifications.
- Colorfastness Testing: Ensures colors resist fading or bleeding during washing.
- Tensile and Seam Strength Tests: Verify durability under stress.
- Microbial Barrier Testing: For scrubs with antimicrobial claims, tests confirm efficacy.
- Chemical Residue Testing: Ensures no harmful substances remain on the fabric.
Strategies for B2B Buyers to Verify Supplier Quality Control
For international buyers, particularly from diverse regions like Africa, South America, the Middle East, and Europe, verifying the supplier’s quality control capabilities is essential to mitigate risk and ensure compliance.
1. Conducting Supplier Audits
- On-site Factory Audits: Visiting the manufacturing facility to observe production workflows, quality control procedures, and worker conditions.
- Remote Audits: Using video conferencing and digital tools when travel is impractical.
- Third-Party Audits: Engaging independent inspection agencies (e.g., SGS, Bureau Veritas) to perform unbiased assessments.
2. Reviewing Quality Documentation
- Quality Control Reports: Regular reports on IQC, IPQC, and FQC results provide transparency.
- Certificates of Compliance: Verifications for ISO 9001, CE marking, and other relevant standards.
- Test Reports: Lab results for fabric performance, safety, and durability.
3. Sampling and Pilot Runs
Requesting pre-production samples or pilot batches allows buyers to assess product quality firsthand before committing to large orders.
QC and Compliance Nuances for International Buyers
International buyers must navigate varying regulatory landscapes and tariff complexities, which impact sourcing decisions for scrub dresses.
- Tariff Impact on Material Selection: Due to recent global tariff changes, especially affecting synthetic fibers and certain fabric blends, buyers should confirm suppliers source materials from compliant origins to avoid customs delays and additional costs.
- Regional Certification Requirements: For example, European buyers must ensure CE compliance, while buyers in the Middle East might require conformity with Gulf Cooperation Council (GCC) standards.
- Sustainability and Ethical Production: Increasingly important in Europe and parts of South America, these factors influence supplier selection and quality expectations.
- Language and Communication: Clear documentation and understanding of quality terms are vital across diverse languages and cultures.
- Logistics and Lead Times: Quality control also entails reliable packaging and shipment practices to preserve garment integrity during transit.
Conclusion
For international B2B buyers sourcing scrub dresses, a deep understanding of manufacturing processes and rigorous quality assurance frameworks is critical to successful partnerships. By focusing on detailed manufacturing stages, adherence to international and industry standards, and thorough supplier verification methods—including audits and testing—buyers can confidently select suppliers who deliver compliant, durable, and high-quality scrub dresses suited for their regional market demands. This strategic approach not only mitigates risks but also strengthens supply chain resilience in an increasingly complex global trade environment.
Related Video: Garments Full Production Process | Order receive to Ex-Factory | Episode 2
Comprehensive Cost and Pricing Analysis for scrub dress Sourcing
Breakdown of Cost Components in Scrub Dress Sourcing
Understanding the detailed cost structure behind sourcing scrub dresses is essential for international B2B buyers aiming to optimize procurement budgets and ensure product quality. The primary cost components include:
-
Materials: Fabric choice significantly influences cost. Common materials like cotton-polyester blends balance comfort and durability but vary in price depending on origin, certifications (e.g., GOTS organic cotton), and fabric weight. Specialty antimicrobial or moisture-wicking fabrics command premiums, especially when certified for healthcare standards.
-
Labor: Labor costs depend on the manufacturing country and factory expertise. Regions like Southeast Asia may offer competitive labor rates, while European manufacturers might charge more but provide higher quality assurance and compliance with labor laws.
-
Manufacturing Overhead: This includes factory utilities, equipment depreciation, and indirect expenses. Factories with advanced machinery or sustainable production lines may have higher overheads, reflected in unit costs.
-
Tooling and Sampling: Initial setup costs such as pattern making, sample creation, and customization tooling are often one-time fees amortized over order volumes. Complex designs or multiple size fittings increase these costs.
-
Quality Control (QC): Rigorous QC processes—ranging from fabric inspection to final garment checks—add to the cost but reduce returns and reputational risks. Certified factories with ISO or OEKO-TEX standards may charge premiums for thorough QC.
-
Logistics and Duties: Shipping costs vary greatly depending on freight mode (air, sea, or land), distance, and geopolitical factors. Tariffs, especially for goods crossing borders with complex trade regulations (e.g., EU import duties or Middle East customs), can add significant expenses.
-
Supplier Margin: Manufacturers and suppliers include margins to cover profit and risk. Margins can fluctuate based on supplier reputation, exclusivity, and buyer relationship.
Key Price Influencers Impacting Scrub Dress Procurement
Several factors dynamically affect the final pricing of scrub dresses in B2B transactions:
-
Order Volume and Minimum Order Quantities (MOQs): Larger orders typically secure better per-unit pricing due to economies of scale. However, buyers from emerging markets may face challenges meeting high MOQs, necessitating negotiation or flexible lot sizes.
-
Product Specifications and Customization: Features such as embroidery, logo placement, special stitching, or tailored fits increase costs. Buyers should evaluate whether customization adds measurable value versus standard styles.
-
Material Quality and Certifications: Premium fabrics with certifications (e.g., antimicrobial, organic) increase costs but may justify higher price points in regulated healthcare environments or discerning markets.
-
Supplier Reliability and Capacity: Established suppliers with proven track records may charge more but offer consistent quality and adherence to delivery schedules. New or smaller suppliers might offer lower prices but carry higher risk.
-
Incoterms and Payment Terms: Shipping terms (FOB, CIF, DDP) affect who bears logistics and customs costs. Buyers should clarify these terms to avoid unexpected expenses. Payment terms like letters of credit or advance payments can also influence pricing.
Strategic Tips for International B2B Buyers
-
Negotiate Beyond Price: Focus on total value including lead times, quality guarantees, and after-sales support. For buyers in Africa, South America, the Middle East, and Europe, building long-term supplier partnerships can unlock volume discounts and flexibility.
-
Consider Total Cost of Ownership (TCO): Analyze all associated costs—not just unit price. For example, faster shipping may increase freight cost but reduce inventory holding expenses and stockouts.
-
Leverage Regional Trade Agreements: Buyers in Europe or the Middle East should explore sourcing from countries benefiting from preferential trade agreements to reduce tariffs and customs delays.
-
Prioritize Quality Certifications: In healthcare markets, compliance with international standards impacts acceptance and resale value. Investing slightly more in certified products can prevent costly rejections.
-
Plan for Tariff and Regulatory Changes: Recent shifts in global trade policies emphasize the need for agile sourcing strategies. Diversifying suppliers across regions can mitigate risks related to tariffs, especially for buyers importing from Asia.
-
Request Detailed Cost Breakdowns: Transparency on material costs, labor rates, and overheads enables better negotiation and benchmarking.
Indicative Pricing Disclaimer
Pricing for scrub dresses varies widely based on material selection, order volume, customization level, and sourcing region. Indicative FOB prices for basic scrub dresses typically range from $5 to $15 per unit. Premium features, certifications, or small batch production can push prices higher. Buyers should obtain formal quotations tailored to their specifications and factor in all logistical and tariff-related costs for accurate budgeting.
By meticulously analyzing these cost components and price influencers, international B2B buyers can strategically source scrub dresses that meet quality standards and budget requirements, while navigating the complexities of global trade and regional market nuances.
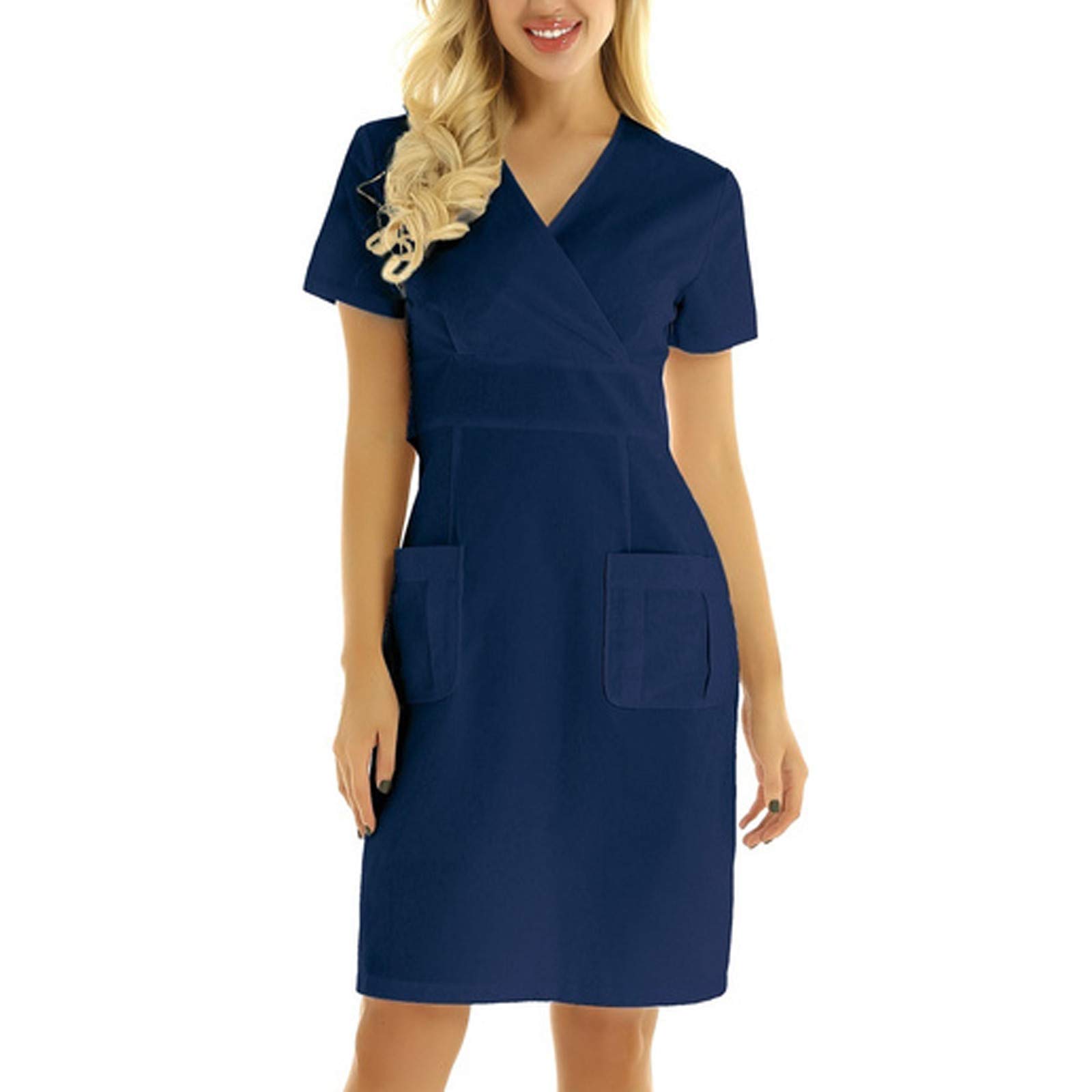
Illustrative Image (Source: Google Search)
Spotlight on Potential scrub dress Manufacturers and Suppliers
This section offers a look at a few manufacturers active in the ‘scrub dress’ market. This is a representative sample for illustrative purposes; B2B buyers must conduct their own extensive due diligence before any engagement. Information is synthesized from public sources and general industry knowledge.
Essential Technical Properties and Trade Terminology for scrub dress
When sourcing scrub dresses for international markets, understanding the key technical properties and trade terminology is essential for making informed purchasing decisions. These insights ensure product quality, compliance, and smooth transactions across diverse regions such as Africa, South America, the Middle East, and Europe.
Critical Technical Properties of Scrub Dress
1. Fabric Composition and Grade
Scrub dresses are typically made from blends of cotton, polyester, or specialty fibers like Tencel. The fabric grade defines durability, comfort, and ease of care. For example, a 65% polyester/35% cotton blend offers wrinkle resistance and breathability, ideal for healthcare environments. Buyers should confirm fabric certifications (e.g., OEKO-TEX, GOTS) to meet sustainability and safety standards required in their markets.
2. Fabric Weight (GSM – Grams per Square Meter)
GSM indicates fabric thickness and weight, affecting durability and comfort. A typical scrub dress ranges from 150 to 220 GSM. Heavier fabrics (200+ GSM) provide enhanced durability but may reduce breathability, while lighter fabrics improve comfort but may wear out faster. B2B buyers must balance these factors based on end-user needs and climate considerations.
3. Colorfastness and Dye Quality
Colorfastness measures how well fabric retains color after washing or exposure to light. Scrub dresses require high colorfastness to withstand frequent laundering in hospital settings. Poor dye quality can lead to fading and unprofessional appearance, impacting brand reputation. Request lab test reports or certifications to ensure compliance with colorfastness standards.
4. Dimensional Stability (Shrinkage Tolerance)
Dimensional stability defines how much a garment changes size after washing. Scrub dresses with low shrinkage tolerance (typically below 3%) maintain consistent fit and professional look. This specification is vital for buyers seeking to minimize returns and complaints, especially when selling to regions with limited consumer ability to exchange products.
5. Seam Strength and Stitching Quality
Strong seams and quality stitching enhance garment longevity. Common standards include double-needle stitching or reinforced seams at stress points like shoulders and pockets. Buyers should verify production techniques and conduct random quality audits to ensure durability, which is critical for bulk orders serving busy healthcare professionals.
6. Antimicrobial and Moisture-Wicking Properties (Optional)
Advanced scrub dresses may feature antimicrobial finishes or moisture-wicking fabrics to improve hygiene and wearer comfort. These properties are increasingly demanded in global healthcare markets and can justify premium pricing. Verify the use of certified chemical treatments and their compliance with local regulations, especially in the Middle East and Europe.
Common Trade Terminology for Scrub Dress Sourcing
OEM (Original Equipment Manufacturer)
An OEM produces scrub dresses based on the buyer’s specifications, including design, fabric choice, and branding. This model is preferred by international buyers seeking private-label products to differentiate their offerings in competitive markets.
MOQ (Minimum Order Quantity)
MOQ is the smallest quantity a manufacturer agrees to produce in one order. Understanding MOQ is crucial for budgeting and inventory planning. Smaller buyers from emerging markets should negotiate MOQ to avoid overstocking, while larger buyers leverage economies of scale.
RFQ (Request for Quotation)
An RFQ is a formal inquiry sent to suppliers asking for detailed price and production terms based on specified requirements. Providing clear technical specifications in the RFQ accelerates supplier responses and helps buyers compare offers accurately.
Incoterms (International Commercial Terms)
Incoterms define responsibilities for shipping, insurance, and customs between buyer and seller. Common terms include FOB (Free On Board) and CIF (Cost, Insurance, Freight). International buyers must understand Incoterms to manage logistics costs and risks effectively.
Lead Time
Lead time refers to the duration from order confirmation to product delivery. It impacts inventory planning and market responsiveness. Buyers should confirm lead times upfront, especially when sourcing from distant manufacturing hubs, to avoid stockouts or delayed launches.
Substantial Transformation
This trade concept determines the country of origin for customs purposes, based on where the product undergoes its key manufacturing process. It affects tariff rates and compliance, especially important under evolving 2025 trade policies. Buyers should ensure clarity on origin to optimize costs and avoid shipment delays.
By mastering these technical properties and trade terms, B2B buyers can enhance product quality, streamline procurement, and navigate complex international trade environments with confidence. This knowledge is particularly valuable for buyers from diverse regions aiming to meet local regulations, cost targets, and end-user expectations in healthcare apparel.
Navigating Market Dynamics, Sourcing Trends, and Sustainability in the scrub dress Sector
Market Overview & Key Trends
The global scrub dress market is experiencing dynamic growth, driven by the expanding healthcare sector worldwide and rising demand for functional, comfortable, and professional medical apparel. For international B2B buyers from regions such as Africa, South America, the Middle East, and Europe—including markets like Indonesia and Germany—understanding regional healthcare infrastructure growth, regulatory compliance, and sourcing nuances is essential.
Key market drivers include increasing healthcare workforce numbers, heightened awareness of infection control, and the need for durable, easy-to-maintain uniforms. Technological advancements such as antimicrobial fabric treatments and moisture-wicking textiles are rapidly gaining traction, enhancing scrub dress performance and wearer comfort. Buyers are also noticing a shift toward customization capabilities, with manufacturers offering tailored fits and branding options to meet institutional identity requirements.
From a sourcing perspective, supply chain diversification is critical amid ongoing geopolitical uncertainties and tariff fluctuations, particularly for buyers reliant on Asian manufacturing hubs. Regions like Southeast Asia and Eastern Europe are emerging as alternative production bases, balancing cost competitiveness and quality standards. Digital platforms facilitating direct manufacturer communication and streamlined order management are becoming indispensable tools, enabling buyers to maintain agility and transparency.
Additionally, the market is responding to evolving regulatory standards on textile safety and labor practices, making supplier compliance a top priority. Buyers should prioritize manufacturers with certifications such as ISO 13485 (for medical devices and related products) and OEKO-TEX Standard 100, which ensure product safety and quality.
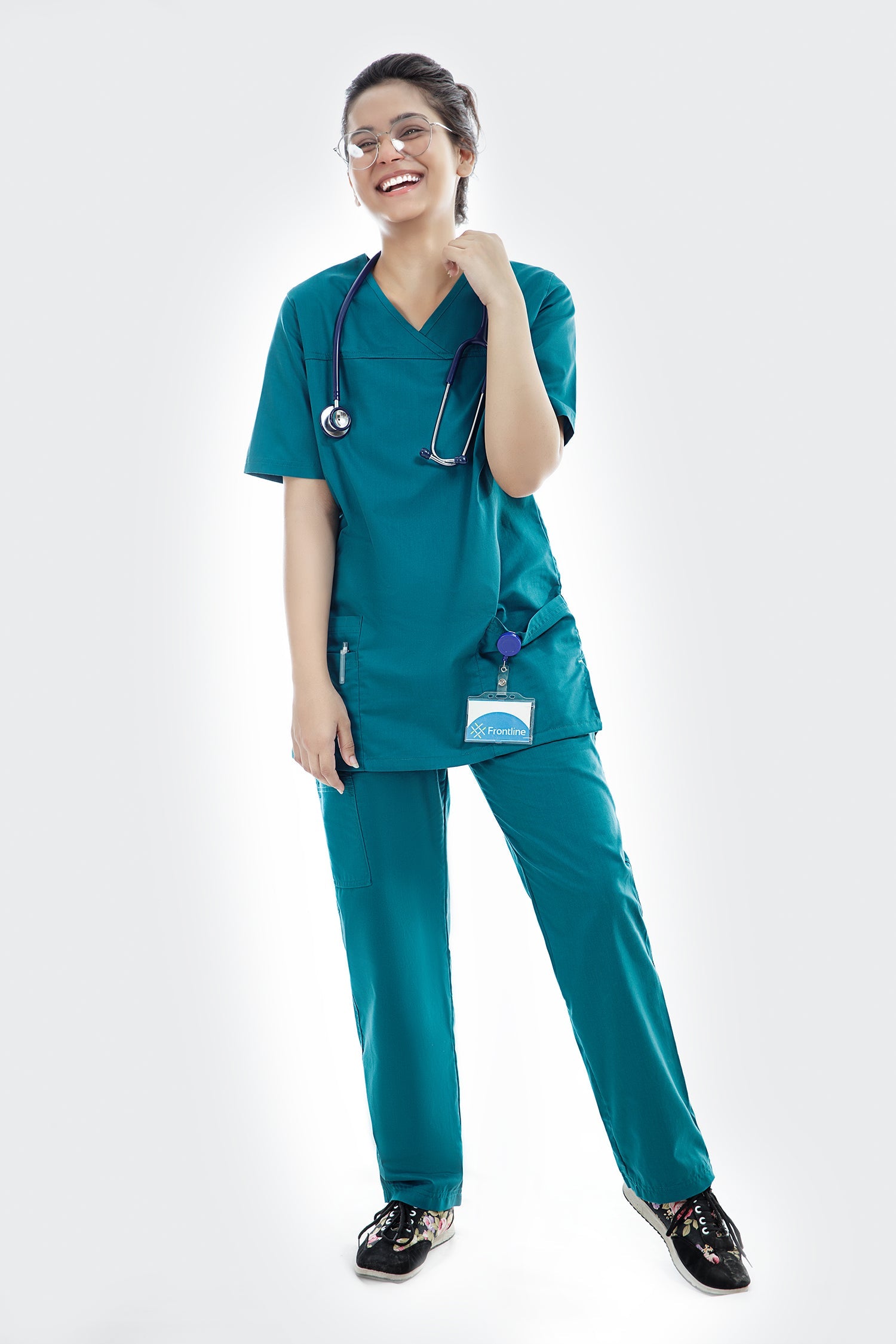
Illustrative Image (Source: Google Search)
Sustainability & Ethical Sourcing in B2B
Sustainability has emerged as a pivotal consideration in the scrub dress sector, reflecting broader healthcare and textile industry trends toward minimizing environmental impact. For international B2B buyers, incorporating sustainable procurement strategies not only meets growing client expectations but also mitigates risks linked to regulatory penalties and reputational damage.
The production of scrub dresses traditionally relies on cotton and polyester blends, with polyester’s synthetic origins contributing to microplastic pollution and high carbon footprints. Consequently, there is a marked shift toward eco-friendly materials such as GOTS-certified organic cotton, Tencel (lyocell), and recycled polyester fibers, which offer reduced water usage, lower chemical inputs, and biodegradability advantages. Utilizing low-impact dyes and waterless dyeing technologies further enhances the environmental profile of scrub garments.
Ethical sourcing extends beyond materials to encompass fair labor practices and supply chain transparency. Buyers should seek suppliers that adhere to internationally recognized standards like SA8000 or WRAP, ensuring safe working conditions and fair wages. Traceability tools and blockchain-enabled platforms are increasingly used to verify compliance, helping buyers demonstrate accountability to stakeholders.
Green certifications such as OEKO-TEX Standard 100, Bluesign, and Cradle to Cradle provide assurance that scrub dresses meet stringent environmental and health criteria, making them attractive for healthcare institutions prioritizing sustainability. By integrating these certifications and partnering with responsible manufacturers, buyers can support circular economy initiatives, reduce waste through garment recycling programs, and align with global sustainability goals.
Evolution and Historical Context
Scrub dresses originated as simple, utilitarian garments designed to maintain hygiene and minimize contamination in medical environments. Historically, they were basic cotton or polyester uniforms with little variation. Over time, the sector has evolved significantly, influenced by advances in textile technology, infection control protocols, and healthcare worker needs.
In the latter half of the 20th century, scrubs became standardized hospital attire, reflecting professional identity and improving workplace safety. The rise of global healthcare networks and outsourcing in the early 2000s led to increased mass production and cost competition, primarily centered in Asia.
Today, the scrub dress sector is a sophisticated market blending functionality, comfort, and sustainability. Buyers now demand innovative fabrics with antimicrobial properties, ergonomic designs, and environmental responsibility. This evolution underscores the importance of strategic sourcing partnerships that can deliver quality, compliance, and agility in an increasingly complex global landscape.
Related Video: International Trade Explained
Frequently Asked Questions (FAQs) for B2B Buyers of scrub dress
-
How can I effectively vet suppliers of scrub dresses to ensure reliability and quality?
To vet suppliers, start by requesting detailed company profiles, certifications, and client references. Verify their manufacturing capabilities, compliance with international labor and environmental standards, and quality control processes. For buyers in Africa, South America, the Middle East, and Europe, consider suppliers with experience exporting to your region to ensure familiarity with local regulations and logistics. Conduct factory audits, either personally or via third-party inspection agencies, to assess working conditions and production quality. Digital tools like virtual factory tours and sample orders can also help gauge responsiveness and product standards before committing to large orders. -
What customization options are typically available for scrub dresses in B2B orders?
Most manufacturers offer customization on fabric type, color, design features (pockets, closures, collars), and sizing to match buyer specifications. Advanced options may include embroidery for logos or branding, antimicrobial fabric treatments, and sustainable material choices like organic cotton or recycled blends. When negotiating, clarify the minimum order quantities (MOQs) required for customized items and the impact on lead times and pricing. For international buyers, ensure that customization aligns with your market’s regulatory requirements and customer preferences to maximize product appeal and compliance. -
What are the standard minimum order quantities (MOQs) and lead times for scrub dress production?
MOQs vary widely depending on the supplier’s scale and production methods but typically range from 100 to 1,000 pieces per style or color. Lead times generally span 30 to 90 days from order confirmation, influenced by factors such as fabric availability, customization complexity, and current factory workload. International buyers should factor in additional time for shipping and customs clearance. To optimize supply chain efficiency, discuss flexible MOQs and expedited production options upfront, especially if you require multiple styles or frequent replenishments. -
What payment terms are common in international B2B transactions for scrub dresses?
Suppliers usually request a deposit upfront (30-50%) with the balance paid before shipment or upon delivery. Common payment methods include wire transfer (T/T), Letter of Credit (L/C), and increasingly, secure online payment platforms. For buyers in emerging markets, negotiating payment terms that mitigate currency risk and provide some credit period can be beneficial. Always verify supplier bank details and use escrow services if available to reduce fraud risk. Clear payment schedules aligned with production milestones help maintain trust and smooth order fulfillment. -
How can I ensure quality control and compliance with international standards for scrub dresses?
Implementing a multi-stage quality assurance (QA) process is essential. This includes fabric inspection, in-line production checks, and final product audits. Request certifications such as ISO 9001 for quality management, OEKO-TEX for fabric safety, or specific healthcare garment standards relevant to your market. Collaborate with suppliers on pre-shipment inspections by third-party agencies to detect defects early. Buyers should also confirm compliance with local regulations on materials and labeling, particularly for markets with strict healthcare apparel requirements like the EU or Middle East.
-
What certifications should I look for when sourcing scrub dresses internationally?
Look for certifications that demonstrate product safety, environmental responsibility, and ethical manufacturing. Key certifications include GOTS (Global Organic Textile Standard) for organic materials, OEKO-TEX Standard 100 for chemical safety, and WRAP (Worldwide Responsible Accredited Production) for social compliance. Additionally, certifications specific to medical textiles or protective clothing may be required depending on your market. Verifying these certifications through official registries helps ensure your supplier adheres to global best practices, reducing risk and enhancing your brand credibility. -
What are the best practices for managing logistics and shipping of bulk scrub dress orders internationally?
Plan logistics early, coordinating with suppliers on packaging standards that protect garments during transit. Choose shipping methods balancing cost and speed—sea freight is economical for large volumes but slower, while air freight offers faster delivery at higher cost. Understand import regulations, tariffs, and customs documentation requirements in your country to avoid delays. Engage experienced freight forwarders familiar with your region (Africa, South America, Middle East, Europe) to handle clearance and compliance. Regular communication with suppliers and logistics partners ensures transparency and timely updates on shipment status. -
How should disputes or quality issues be handled in international scrub dress sourcing contracts?
Include clear dispute resolution clauses in contracts, specifying governing law, arbitration venues, and timelines for issue resolution. Establish agreed-upon quality standards and inspection protocols documented in purchase agreements. If defects or non-compliance arise, promptly notify the supplier with evidence and request corrective actions such as rework, replacements, or refunds. Utilizing third-party inspection and certification reports can support your claims. Maintaining open communication and building long-term relationships with suppliers encourages cooperative problem-solving and reduces the likelihood of recurring issues.
Strategic Sourcing Conclusion and Outlook for scrub dress
Strategic sourcing of scrub dresses demands a nuanced understanding of global supply dynamics, material innovation, and regulatory environments. For international B2B buyers, especially those operating in Africa, South America, the Middle East, and Europe, prioritizing supplier reliability, compliance with evolving tariff regimes, and sustainability credentials is essential. Balancing cost efficiency with quality and ethical manufacturing practices will differentiate your procurement strategy in a competitive healthcare apparel market.
Key takeaways include:
- Diversify sourcing regions to mitigate risks associated with tariffs and geopolitical shifts, leveraging emerging manufacturing hubs beyond traditional centers.
- Engage suppliers offering sustainable fabrics and transparent production processes to meet growing demand for eco-conscious medical apparel.
- Invest in partnerships that provide agility and scalability, enabling rapid response to fluctuating healthcare demands and regulatory changes.
- Leverage technology-enabled sampling and prototyping to accelerate product development cycles and reduce time-to-market.
Looking ahead, the scrub dress market will increasingly reward buyers who adopt a forward-thinking sourcing approach—one that integrates compliance, innovation, and resilience. International buyers are encouraged to actively collaborate with manufacturers who demonstrate adaptability and a commitment to sustainability, ensuring your supply chain is not only cost-effective but also future-proofed against ongoing global trade uncertainties. Embrace strategic sourcing as a catalyst for competitive advantage and long-term growth in the healthcare apparel sector.