Your Ultimate Guide to Sourcing Navy Maxi Dress
Guide to Navy Maxi Dress
- Introduction: Navigating the Global Market for navy maxi dress
- Understanding navy maxi dress Types and Variations
- Key Industrial Applications of navy maxi dress
- Strategic Material Selection Guide for navy maxi dress
- In-depth Look: Manufacturing Processes and Quality Assurance for navy maxi dress
- Comprehensive Cost and Pricing Analysis for navy maxi dress Sourcing
- Spotlight on Potential navy maxi dress Manufacturers and Suppliers
- Essential Technical Properties and Trade Terminology for navy maxi dress
- Navigating Market Dynamics, Sourcing Trends, and Sustainability in the navy maxi dress Sector
- Frequently Asked Questions (FAQs) for B2B Buyers of navy maxi dress
- Strategic Sourcing Conclusion and Outlook for navy maxi dress
Introduction: Navigating the Global Market for navy maxi dress
The global demand for navy maxi dresses continues to surge, driven by their timeless appeal, versatility, and cross-cultural resonance. For international B2B buyers—especially those operating in dynamic markets across Africa, South America, the Middle East, and Europe—navigating this evolving landscape requires more than just identifying suppliers. It demands a strategic approach to sourcing that balances quality, cost-efficiency, compliance, and market trends.
This guide offers a comprehensive exploration of the navy maxi dress supply chain, tailored specifically for discerning buyers seeking to expand or optimize their product portfolios. From an in-depth analysis of fabric types and manufacturing processes to quality control benchmarks, supplier evaluation, and cost considerations, every aspect is covered with actionable insights. Additionally, the guide sheds light on regional sourcing advantages, tariff implications, and logistics challenges that directly impact international trade flows.
By engaging with this resource, buyers will gain clarity on how to:
- Select the right materials that align with durability and consumer preferences
- Partner with manufacturers who uphold ethical standards and deliver consistent quality
- Navigate complex global tariffs and trade regulations affecting sourcing choices
- Optimize inventory and supply chain resilience in a fast-changing market environment
Ultimately, this guide empowers international B2B buyers to make informed, strategic decisions that enhance competitiveness and profitability in the navy maxi dress segment. Whether sourcing for boutique retailers in Mexico, mass-market channels in South Africa, or fashion-forward outlets in Europe and the Middle East, the insights herein are designed to support sustainable growth and operational excellence.
Understanding navy maxi dress Types and Variations
Type Name | Key Distinguishing Features | Primary B2B Applications | Brief Pros & Cons for Buyers |
---|---|---|---|
Casual Navy Maxi Dress | Lightweight fabrics, simple cuts, often sleeveless or short-sleeved | Everyday wear, retail chains, casual boutiques | + High demand, versatile; – Seasonal sensitivity, lower price margins |
Formal Navy Maxi Dress | Luxurious materials (silk, satin), embellishments, structured fit | Event wear, luxury retailers, online premium stores | + High value, premium market; – Higher production cost, smaller volume |
Bohemian Navy Maxi Dress | Flowy, layered designs, ethnic prints or embroidery | Niche boutiques, ethnic fashion retailers | + Unique appeal, cultural resonance; – Limited mainstream demand |
Plus-Size Navy Maxi Dress | Tailored to plus-size fits, inclusive sizing, flattering cuts | Inclusive fashion brands, department stores | + Expands market reach, growing segment; – Requires precise fit knowledge |
Sustainable Navy Maxi Dress | Made from eco-friendly fabrics, organic dyes, ethical sourcing | Eco-conscious brands, export markets focused on sustainability | + Meets rising demand for green products; – Potentially higher costs, sourcing complexity |
Casual Navy Maxi Dress
This type features breathable, easy-care fabrics such as cotton or rayon, with designs favoring comfort and everyday wear. It suits mass-market retailers and volume-driven buyers targeting warm climates or casual consumer segments. B2B buyers should focus on fabric durability, cost efficiency, and trend adaptability. Inventory turnover is typically faster, but margins may be slimmer due to high competition.
Formal Navy Maxi Dress
Characterized by premium fabrics like silk or satin and often adorned with beads or lace, formal navy maxi dresses cater to luxury or event wear markets. B2B buyers should prioritize quality control, supplier reliability, and compliance with luxury standards. While production costs are higher, these dresses command premium pricing and appeal to discerning clientele, making them suitable for upscale retailers or e-commerce platforms.
Bohemian Navy Maxi Dress
These dresses emphasize artistic, flowy silhouettes with ethnic-inspired prints or embroidery, appealing to niche markets focused on cultural or artisanal fashion. B2B buyers benefit from sourcing from specialized manufacturers or regions known for craftsmanship. The challenge lies in balancing unique design authenticity with scalability and maintaining consistent quality for export markets.
Plus-Size Navy Maxi Dress
Designed with inclusive sizing and flattering fits, this category addresses a growing global demand for plus-size apparel. Buyers should ensure accurate size grading, fit testing, and diversity in style offerings. This segment helps brands expand their market share, especially in regions with increasing awareness of body positivity. However, sizing complexity requires close collaboration with manufacturers to minimize returns and optimize customer satisfaction.
Sustainable Navy Maxi Dress
Made from organic or recycled materials with ethical labor practices, sustainable navy maxi dresses appeal to environmentally conscious consumers across Europe, the Middle East, and parts of Africa. B2B buyers must vet suppliers for certifications and traceability. While initial costs may be higher, these products enhance brand reputation and meet regulatory or consumer demands for sustainability, offering long-term competitive advantages.
Related Video: Stylish Navy Blue Dress Outfit. How to Wear Navy Blue Dress and Outfit Inspirations?
Key Industrial Applications of navy maxi dress
Industry/Sector | Specific Application of navy maxi dress | Value/Benefit for the Business | Key Sourcing Considerations for this Application |
---|---|---|---|
Hospitality & Tourism | Uniforms and staff attire for luxury resorts | Enhances brand image with elegant, comfortable attire | Fabric durability, ease of care, consistent color fastness, supplier reliability |
Corporate & Events | Corporate gifting and event staff uniforms | Professional appearance, promotes brand identity | Customization options, quality control, timely delivery, ethical sourcing |
Retail & Fashion | Seasonal collection offerings for women’s apparel | Meets consumer demand for trendy, versatile dresses | Trend alignment, material sourcing flexibility, tariff impact awareness |
Export & Wholesale | Bulk supply for boutique retailers and markets | Economies of scale, broad market reach | Compliance with international trade regulations, packaging standards, cost efficiency |
Hospitality & Wellness | Uniforms for spa and wellness centers | Comfortable, breathable attire improving staff performance | Breathability, fabric sustainability, supplier certifications, regional climate adaptability |
Hospitality & Tourism
In luxury resorts and boutique hotels across Africa, the Middle East, and Europe, navy maxi dresses serve as elegant uniforms for female staff, particularly in guest services and hospitality roles. These dresses provide a sophisticated look while ensuring comfort during long shifts. For B2B buyers, sourcing durable fabrics that maintain color vibrancy despite frequent washing is critical. Additionally, suppliers offering consistent sizing and timely delivery support seamless operations in high-turnover environments.
Corporate & Events
Corporate gifting and event staffing often utilize navy maxi dresses for their classic appeal and professional tone. Companies in South America and Europe prefer these dresses to outfit event personnel or as branded gifts that reflect corporate identity. Buyers should prioritize suppliers who offer customization, such as embroidery or bespoke tailoring, while maintaining high quality standards. Ethical sourcing and fair labor practices are increasingly important to appeal to socially conscious clients and meet compliance requirements.
Retail & Fashion
For fashion retailers targeting women’s apparel markets in Mexico, Thailand, and Europe, navy maxi dresses are staple items in seasonal collections due to their versatility and timeless style. B2B buyers must navigate shifting fashion trends and tariff landscapes, especially with synthetic fabric blends subject to changing trade policies. Close collaboration with suppliers who can adapt fabric choices and design elements quickly ensures competitive advantage and responsiveness to consumer demand.
Export & Wholesale
Wholesale distributors and exporters supplying boutique stores across multiple regions benefit from navy maxi dresses’ broad market appeal. Bulk purchasing allows for cost savings and consistent product availability. Buyers should focus on suppliers with robust international trade knowledge, ensuring compliance with customs regulations and packaging standards. Efficient logistics and clear documentation reduce delays, critical for markets with complex import rules such as the Middle East and South America.
Hospitality & Wellness
Spas and wellness centers in diverse climates—ranging from Mediterranean Europe to tropical South America—require staff uniforms that combine style with comfort. Navy maxi dresses made from breathable, sustainable fabrics enhance staff performance and client perception. B2B buyers must assess fabric sustainability certifications and climate adaptability to ensure uniforms remain comfortable and durable under varying temperature and humidity conditions. Partnering with suppliers who emphasize eco-friendly production supports corporate social responsibility goals.
Related Video: LABORATORY APPARATUS AND THEIR USES
Strategic Material Selection Guide for navy maxi dress
When selecting materials for navy maxi dresses, international B2B buyers must carefully evaluate fabric properties, sourcing complexities, and regional compliance to meet diverse market demands. The choice of material directly influences the garment’s aesthetic appeal, durability, production feasibility, and cost-effectiveness, all critical factors for buyers from Africa, South America, the Middle East, and Europe.
Cotton
Key Properties: Cotton is a natural fiber known for its breathability, moisture absorption, and softness. It performs well in warm climates due to its excellent temperature regulation but lacks inherent stretch or wrinkle resistance.
Pros & Cons: Cotton is durable and comfortable, making it ideal for casual and semi-formal maxi dresses. It is widely available and cost-effective, but it tends to wrinkle easily and can shrink if not pre-treated. Manufacturing complexity is moderate, with established global supply chains.
Impact on Application: Cotton’s high breathability suits tropical and warm regions such as parts of Africa and South America, enhancing wearer comfort. However, it may absorb stains more readily and requires careful finishing to maintain color vibrancy, especially for deep navy hues.
International Considerations: Buyers should verify compliance with standards such as OEKO-TEX and GOTS for organic cotton, which are increasingly demanded in Europe and the Middle East. Cotton sourced from countries like Egypt or India may offer premium quality but could be subject to tariffs or import restrictions depending on trade agreements.
Polyester
Key Properties: Polyester is a synthetic fiber prized for its strength, wrinkle resistance, and color retention. It is hydrophobic, meaning it dries quickly and resists mildew but can retain heat, making it less breathable.
Pros & Cons: Polyester is cost-effective and easy to manufacture at scale, offering excellent durability and low maintenance. However, it may feel less comfortable in hot climates and is less environmentally friendly unless recycled variants are used.
Impact on Application: Polyester’s wrinkle resistance and colorfastness make it a popular choice for navy maxi dresses intended for travel or long wear. It suits buyers targeting markets in Europe and the Middle East, where garment longevity and appearance are prioritized.
International Considerations: Buyers should be aware of tariff implications when sourcing polyester fabrics from Asia, especially China, due to recent trade policy changes. Compliance with REACH (EU) and other chemical safety standards is essential for European markets. Recycled polyester options may appeal to sustainability-conscious buyers in all regions.
Rayon (Viscose)
Key Properties: Rayon is a semi-synthetic fiber derived from cellulose, offering a silk-like feel with good drape and breathability. It is less durable than polyester and cotton and prone to shrinking and wrinkling.
Pros & Cons: Rayon provides an elegant, flowy appearance ideal for maxi dresses, enhancing garment aesthetics. However, it requires delicate handling during manufacturing and care, increasing production complexity and cost. It is less suited for high-humidity environments due to moisture retention.
Impact on Application: Rayon’s luxurious hand and drape make it attractive for premium segments in South America and Europe. Its moisture sensitivity may pose challenges in tropical African or Middle Eastern climates unless blended with other fibers.
International Considerations: Buyers must ensure compliance with environmental regulations regarding viscose production, especially in Europe. Sourcing from suppliers with certifications like FSC or PEFC for sustainable wood pulp is increasingly important. Tariff exposure varies by origin and must be factored into cost models.
Linen
Key Properties: Linen, made from flax fibers, is highly breathable, strong, and has a natural luster. It excels in moisture-wicking and is well-suited for hot climates but wrinkles easily and can feel coarse if not finely processed.
Pros & Cons: Linen maxi dresses offer a premium, natural look with excellent comfort in warm regions such as Africa and the Middle East. However, the fabric’s tendency to wrinkle and higher production costs due to labor-intensive processing can be drawbacks.
Impact on Application: Linen’s natural texture and breathability make it ideal for resort wear and summer collections. It aligns well with sustainability trends favored in Europe and South America but may require blending or finishing treatments to enhance softness and reduce wrinkling.
International Considerations: Linen sourcing is often regional; European buyers may prefer European flax for quality and compliance with EU textile regulations. African and Middle Eastern buyers should consider import duties and local consumer preferences for fabric feel and durability.
Material | Typical Use Case for navy maxi dress | Key Advantage | Key Disadvantage/Limitation | Relative Cost (Low/Med/High) |
---|---|---|---|---|
Cotton | Casual and semi-formal maxi dresses for warm climates | Breathable, comfortable, widely available | Prone to wrinkling and shrinking without treatment | Low |
Polyester | Travel-friendly, wrinkle-resistant maxi dresses | Durable, colorfast, low maintenance | Less breathable, environmental concerns unless recycled | Low to Medium |
Rayon (Viscose) | Elegant, flowy maxi dresses for premium markets | Luxurious drape and feel | Less durable, moisture sensitive, higher production complexity | Medium |
Linen | Resort wear and summer maxi dresses in hot climates | Highly breathable, natural texture | Wrinkles easily, higher production cost, coarse feel if untreated | Medium to High |
In-depth Look: Manufacturing Processes and Quality Assurance for navy maxi dress
Manufacturing Processes for Navy Maxi Dress
The production of a navy maxi dress involves a sequence of carefully managed stages to ensure the final garment meets design specifications, quality expectations, and delivery timelines. For international B2B buyers, understanding these manufacturing steps is crucial to selecting reliable suppliers and optimizing supply chain efficiency.
1. Material Preparation
Material preparation begins with sourcing high-quality fabrics, trims, and accessories. For navy maxi dresses, common fabric choices include cotton blends, rayon, chiffon, or polyester, depending on desired drape and durability. The fabric undergoes pre-treatment processes such as:
- Inspection: Visual and tactile checks for defects, color consistency, and fabric weight.
- Pre-shrinking: Washing or heat-setting to reduce future shrinkage.
- Cutting: Using manual or automated cutting machines, fabric is cut into pattern pieces based on technical design specifications.
Fabric sourcing must consider tariff implications and sustainability credentials, especially for buyers in Africa, South America, the Middle East, and Europe, where trade agreements and import duties vary significantly.
2. Forming and Assembly
The forming stage involves shaping the cut fabric pieces into garment components:
- Sewing: Skilled operators or automated sewing machines join pieces through stitching techniques like straight stitch, overlock, or flatlock, ensuring seam strength and appearance.
- Dyeing and Finishing: Although navy fabric is often pre-dyed, additional processes such as washing, softening, or applying anti-wrinkle finishes may be conducted post-assembly.
- Embroidery or Embellishment (if applicable): Decorative elements are added with precision.
Assembly integrates components such as bodices, sleeves, skirts, and linings. Quality in this phase depends on operator skill, machine calibration, and adherence to tech packs.
3. Finishing Processes
The finishing stage polishes the garment to retail-ready standards:
- Trimming: Excess threads are clipped, and loose ends tidied.
- Pressing: Garments are ironed or steamed to enhance shape and remove creases.
- Labeling and Packaging: Brand labels, care tags, and size markers are attached. Packaging is optimized for protection during transit and compliance with buyer specifications.
Finishing must ensure the navy maxi dress retains color vibrancy and fabric integrity, especially under diverse climatic conditions encountered across global markets.
Quality Assurance and Control Framework
For B2B buyers, rigorous quality assurance (QA) and quality control (QC) are essential to mitigate risks such as returns, reputational damage, and compliance failures. Understanding international and industry-specific standards, QC checkpoints, and verification methods empowers buyers to maintain high product quality.
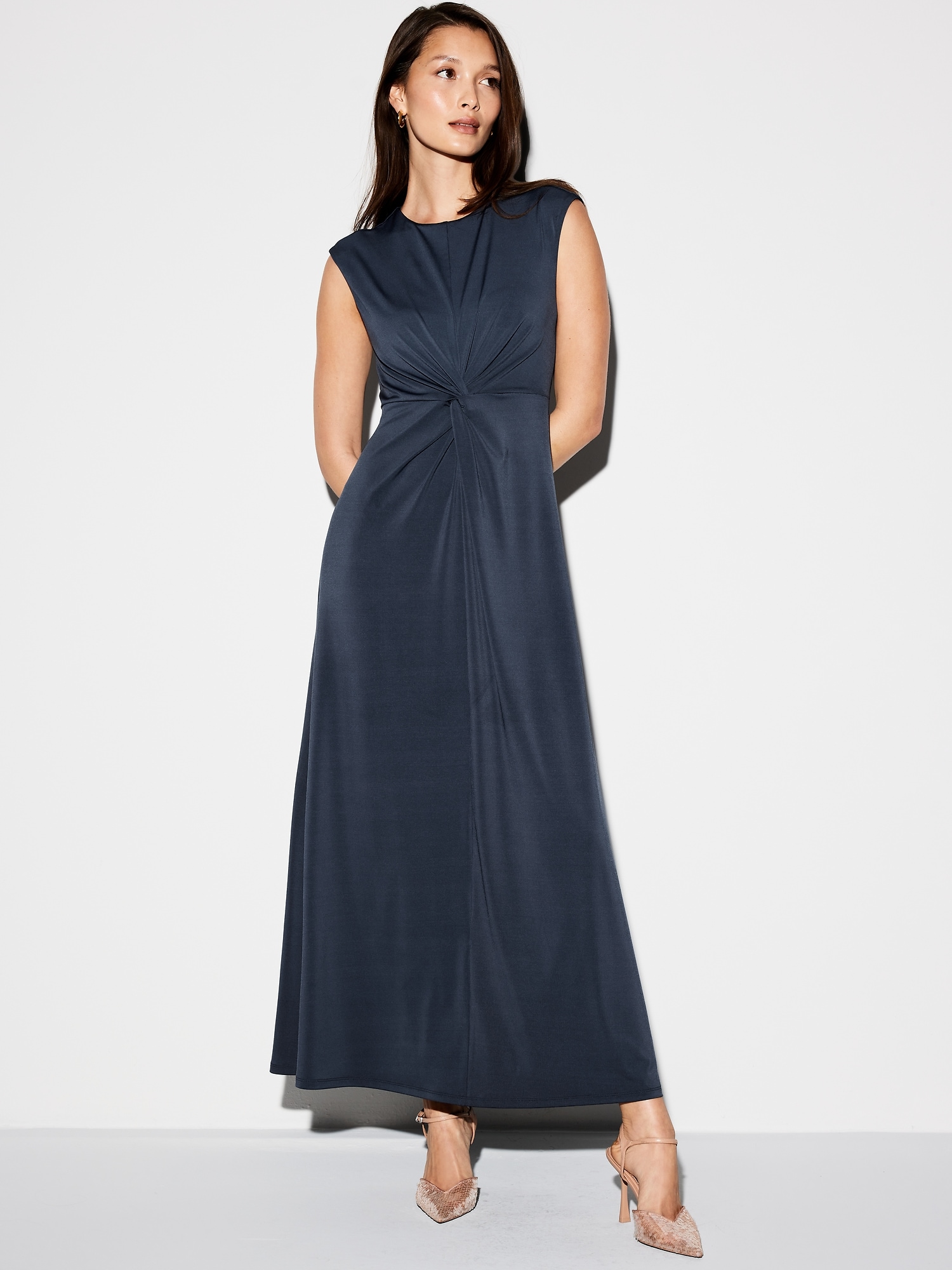
Illustrative Image (Source: Google Search)
Relevant International and Industry Standards
- ISO 9001: This globally recognized standard governs quality management systems (QMS). Suppliers certified with ISO 9001 demonstrate consistent process control, continuous improvement, and customer satisfaction focus.
- OEKO-TEX Standard 100: Particularly relevant for textiles, ensuring fabrics are free from harmful substances—a key consideration for health-conscious markets.
- REACH Compliance (EU): Ensures chemical safety in textiles, crucial for buyers in Europe and regions with EU trade ties.
- ASTM and AATCC Standards: These define testing methods for colorfastness, fabric strength, and durability.
- Country-specific certifications: For example, CE marking is generally not required for apparel but may be relevant if garments incorporate protective elements.
Buyers should verify the supplier’s adherence to these standards as part of their due diligence.
QC Checkpoints in Production
Quality control operates at multiple stages to catch defects early and maintain production consistency:
- Incoming Quality Control (IQC): Inspection of raw materials and components upon arrival. Fabric rolls are tested for color uniformity, weight, and defects.
- In-Process Quality Control (IPQC): Continuous monitoring during cutting, sewing, and assembly. Sample inspections ensure seam integrity, measurements, and adherence to tech packs.
- Final Quality Control (FQC): Comprehensive evaluation of finished dresses before shipment. This includes visual inspection, measurement verification, and functional tests (e.g., zipper operation, button strength).
Implementing these checkpoints reduces the likelihood of costly rework and returns.
Common Testing Methods
- Colorfastness Testing: Evaluates resistance to washing, rubbing, and light exposure to maintain the navy hue.
- Dimensional Stability Testing: Assesses shrinkage or distortion after laundering.
- Seam Strength and Stitch Density Testing: Ensures durability under wear conditions.
- Fabric Weight and Thickness Measurement: Confirms consistency with specification sheets.
B2B buyers should request test reports or certificates from accredited labs to validate these parameters.
Verifying Supplier Quality Control: Practical Strategies for B2B Buyers
International buyers face unique challenges in verifying supplier QC due to geographic distance, varying regulatory environments, and cultural differences. Effective verification strategies include:
- Factory Audits: Conduct or commission third-party audits to assess production capabilities, compliance with ISO 9001/QMS, worker conditions, and process controls. Audits tailored to regional contexts (e.g., compliance with local labor laws in Mexico or Thailand) ensure holistic evaluation.
- Sample Inspections: Request pre-production and pre-shipment samples for detailed assessment. Third-party inspection agencies can perform on-site inspections using AQL (Acceptable Quality Level) standards.
- Review of QC Documentation: Suppliers should provide detailed inspection reports, test certificates, and corrective action records. Buyers must scrutinize these for consistency and authenticity.
- Ongoing Supplier Development: Establish collaborative quality improvement programs, sharing best practices and providing training to elevate supplier QC capabilities.
QC and Compliance Nuances for Buyers in Africa, South America, Middle East, and Europe
- Tariff and Trade Policy Awareness: Buyers must factor in tariff exposure affecting material sourcing and manufacturing locations. For instance, sourcing fabrics from countries under high tariffs may increase costs or delay shipments.
- Sustainability and Ethical Sourcing: Regions like Europe and parts of Africa increasingly demand transparency on environmental impact and labor practices. Buyers should prioritize suppliers with certifications such as Fair Trade or GOTS (Global Organic Textile Standard).
- Cultural and Regulatory Differences: Understanding local labor laws, safety standards, and import regulations in supplier countries (e.g., Thailand, Mexico) helps buyers anticipate compliance risks.
- Logistics and Lead Time Considerations: QC processes should integrate with supply chain management to accommodate longer transit times common in intercontinental shipments, ensuring quality is maintained until delivery.
Conclusion
For international B2B buyers sourcing navy maxi dresses, a detailed grasp of manufacturing processes combined with rigorous quality assurance frameworks is non-negotiable. By engaging suppliers who implement structured material preparation, precise assembly, and meticulous finishing, paired with adherence to international standards like ISO 9001 and robust QC checkpoints (IQC, IPQC, FQC), buyers can secure consistent product quality.
Moreover, leveraging audits, independent inspections, and transparent documentation enhances supplier accountability. Buyers must also navigate tariff landscapes, regional compliance nuances, and sustainability demands to optimize sourcing strategies. This comprehensive approach ultimately drives product excellence, customer satisfaction, and profitable long-term partnerships in the competitive global apparel market.
Related Video: Amazing Garment Manufacturing Process from Fabric to Finished Product Inside the Factory
Comprehensive Cost and Pricing Analysis for navy maxi dress Sourcing
Breakdown of Cost Components in Navy Maxi Dress Sourcing
Understanding the detailed cost structure behind a navy maxi dress is crucial for international B2B buyers aiming to optimize procurement strategies. The primary cost components typically include:
- Materials: The fabric (commonly cotton blends, polyester, rayon, or silk), dyes, trims, and accessories form the largest portion of the cost. High-quality or certified sustainable materials command premium prices. Synthetic blends may be affected by tariff shifts, especially if sourced from regions with evolving trade policies.
- Labor: This includes cutting, sewing, finishing, and packaging. Labor costs vary significantly across sourcing regions — with countries like Thailand offering competitive rates compared to Europe, while African and South American countries may present emerging opportunities with cost advantages and skilled workforces.
- Manufacturing Overhead: Facility costs, utilities, machinery depreciation, and indirect labor contribute here. Efficient factories with modern equipment can reduce overhead per unit.
- Tooling and Setup: Initial costs for pattern making, sample development, and machine setup can be amortized over order volumes but impact smaller batch pricing disproportionately.
- Quality Control (QC): Inspections, testing for colorfastness, stitching durability, and compliance with international standards add to costs but minimize returns and build buyer confidence.
- Logistics and Freight: Transportation from factory to port, customs clearance, and last-mile delivery vary widely depending on Incoterms, freight mode (sea, air), and distance to the buyer’s location. Emerging sourcing countries closer to African, Middle Eastern, or European markets can offer savings here.
- Supplier Margin: The manufacturer’s profit margin is influenced by market demand, supplier reputation, and negotiation dynamics.
Key Price Influencers in Navy Maxi Dress Procurement
Several factors influence the final quoted price for navy maxi dresses:
- Order Volume and MOQ: Larger orders reduce per-unit costs by spreading fixed costs and increasing supplier leverage. Buyers from smaller markets should consider consolidating orders or partnering with other buyers to meet MOQs.
- Product Specifications and Customization: Complex designs, special trims, embroidery, or unique dyeing processes increase costs. Buyers should balance design aspirations with cost implications.
- Material Selection: Premium, organic, or certified sustainable fabrics command higher prices but can open access to niche markets. Conversely, synthetic or blended materials may offer cost savings but face tariff volatility.
- Quality Certifications: Compliance with certifications such as OEKO-TEX, GOTS, or Fair Trade often entails higher costs but strengthens brand positioning, especially in Europe and the Middle East.
- Supplier Reliability and Capacity: Established suppliers with robust supply chains may charge a premium but reduce risks of delays and defects.
- Incoterms and Payment Terms: Terms like FOB, CIF, or DDP shift cost and risk responsibilities. Buyers should understand how these impact landed cost and negotiate accordingly.
Practical Tips for International B2B Buyers
- Negotiate with Total Cost of Ownership in Mind: Focus not just on unit price but on the entire procurement lifecycle—including shipping, customs duties, inventory holding, and returns handling.
- Leverage Local and Regional Trade Agreements: African buyers can benefit from AfCFTA provisions, South American buyers from Mercosur agreements, and Middle Eastern or European buyers from various bilateral treaties to reduce tariffs and improve cost efficiency.
- Diversify Sourcing to Mitigate Tariff Risks: Given the current global tariff volatility, especially affecting synthetic materials and China-origin components, diversify suppliers across Asia, Africa, and Latin America to maintain agility.
- Validate Supplier Compliance and Quality Early: Invest in pre-shipment inspections and factory audits to avoid costly quality issues, which can erode margins and delay time-to-market.
- Consider Lead Times and Inventory Costs: Faster shipping options reduce inventory holding but increase logistics expenses. Balance speed with cost-effectiveness based on market demand in your region.
- Understand Pricing Nuances by Region: For example, buyers in Mexico and Thailand may find competitive pricing in Asia-Pacific, whereas European buyers might prioritize suppliers closer to reduce freight time and complexity.
Disclaimer on Pricing
All pricing insights provided are indicative and subject to variation based on supplier negotiations, market conditions, seasonal demand, and geopolitical factors. Buyers should conduct thorough due diligence, request detailed quotes, and factor in dynamic trade policies and logistics costs to achieve accurate landed cost calculations.
By breaking down the cost structure and understanding influencing factors, international B2B buyers can make informed sourcing decisions for navy maxi dresses that balance quality, cost, and supply chain resilience across diverse global markets.
Spotlight on Potential navy maxi dress Manufacturers and Suppliers
This section offers a look at a few manufacturers active in the ‘navy maxi dress’ market. This is a representative sample for illustrative purposes; B2B buyers must conduct their own extensive due diligence before any engagement. Information is synthesized from public sources and general industry knowledge.
Essential Technical Properties and Trade Terminology for navy maxi dress
Key Technical Properties of Navy Maxi Dress for B2B Buyers
When sourcing navy maxi dresses at scale, understanding critical technical specifications ensures product quality, consistency, and cost-effectiveness. Below are essential properties to evaluate with your suppliers:
-
Fabric Composition and Grade
Navy maxi dresses typically use blends such as cotton-polyester, viscose, or rayon. The fabric composition affects drape, breathability, durability, and dye absorption. For B2B buyers, confirming the material grade ensures consistency in texture and colorfastness, which is vital for maintaining brand reputation and meeting consumer expectations across markets like Africa and Europe. -
Color Fastness and Shade Consistency
The deep navy color must remain consistent across production batches. Color fastness refers to the fabric’s resistance to fading from washing, sunlight, and abrasion. For international buyers, particularly those dealing with varied climates, a high standard of color fastness minimizes returns and dissatisfaction. -
Measurement Tolerances
Standardized sizing and measurement tolerances (e.g., ±1 cm for length or bust) guarantee that garments fit as expected. This is crucial for bulk orders where minor deviations can lead to large-scale quality issues, affecting inventory turnover and customer satisfaction in diverse markets. -
Stitching Quality and Seam Strength
Durable stitching (e.g., double-needle or reinforced seams) is essential to withstand wear and tear, especially in maxi dresses that experience frequent movement. Buyers should specify stitch density and thread type to ensure longevity and reduce returns due to garment failure. -
Finish and Treatment
Treatments like anti-wrinkle, anti-pilling, or water resistance can add value depending on target markets. For example, buyers in humid regions may prefer wrinkle-resistant finishes to appeal to consumers seeking low-maintenance apparel. -
Packaging and Labeling Compliance
Packaging must protect the garment during transit and meet import regulations. Proper labeling (size, care instructions, country of origin) is critical for customs clearance and local market compliance, especially in regions with strict labeling laws like the EU.
Common Trade Terminology Relevant to Navy Maxi Dress Sourcing
Understanding industry jargon helps international buyers communicate clearly and negotiate effectively with suppliers:
-
OEM (Original Equipment Manufacturer)
Refers to manufacturers who produce garments based on the buyer’s design and specifications. OEM partnerships allow buyers to maintain brand identity while leveraging supplier expertise and capacity. -
MOQ (Minimum Order Quantity)
The smallest number of units a supplier is willing to produce in one order. MOQs impact inventory planning and cash flow, particularly for buyers entering new markets or testing product lines. -
RFQ (Request for Quotation)
A formal inquiry sent to suppliers asking for pricing, lead times, and terms based on detailed product specifications. RFQs are the foundation for cost comparison and supplier selection. -
Incoterms (International Commercial Terms)
Standardized trade terms that define responsibilities for shipping, insurance, and tariffs between buyer and seller. Common terms include FOB (Free on Board) and CIF (Cost, Insurance, Freight). Knowing Incoterms helps buyers manage logistics costs and risks effectively. -
Lead Time
The total time from order placement to delivery. Managing lead times is critical in fashion to align inventory with seasonal trends and avoid stockouts or overstock. -
Substantial Transformation
A customs term defining where a product’s origin is determined based on where it undergoes significant manufacturing changes. This affects tariff rates and eligibility for trade agreements, influencing sourcing decisions especially under evolving global trade policies.
For international B2B buyers, especially those operating across Africa, South America, the Middle East, and Europe, mastering these technical properties and trade terms is essential. They not only ensure product quality and compliance but also enable strategic sourcing decisions that reduce costs, mitigate risks, and enhance competitiveness in diverse markets.
Navigating Market Dynamics, Sourcing Trends, and Sustainability in the navy maxi dress Sector
Market Overview & Key Trends
The navy maxi dress segment remains a staple in global apparel markets, buoyed by its versatile appeal across seasons and cultures. For B2B buyers in Africa, South America, the Middle East, and Europe, this category reflects both traditional elegance and evolving consumer preferences. The demand is increasingly shaped by a blend of classic design appeal and contemporary styling, catering to diverse markets from formal events in Europe to casual wear in tropical regions like Mexico and Thailand.
Global drivers influencing this sector include rising urbanization, increasing online retail penetration, and the growing middle class in emerging economies. These factors stimulate demand for accessible yet quality maxi dresses in staple colors like navy, which is favored for its adaptability and timelessness. Additionally, the shift towards e-commerce and omni-channel retail strategies necessitates agile supply chains capable of rapid response to trend fluctuations.
Key sourcing trends reflect a pivot towards diversified manufacturing bases to mitigate geopolitical risks and tariff impacts, especially in light of recent trade policy changes affecting Asia. Countries in Africa and South America are gaining prominence as competitive sourcing hubs due to favorable trade agreements and lower labor costs, making them attractive alternatives for navy maxi dress production. Meanwhile, suppliers in Europe and the Middle East focus on premium quality and sustainable fabric sourcing to serve discerning markets.
Technological advancements such as AI-driven demand forecasting, inventory optimization, and blockchain-enabled supply chain transparency are becoming essential tools for B2B buyers. These innovations reduce overstock risks, enhance fulfillment accuracy, and ensure compliance with ethical sourcing standards — critical factors in maintaining competitiveness across regions.
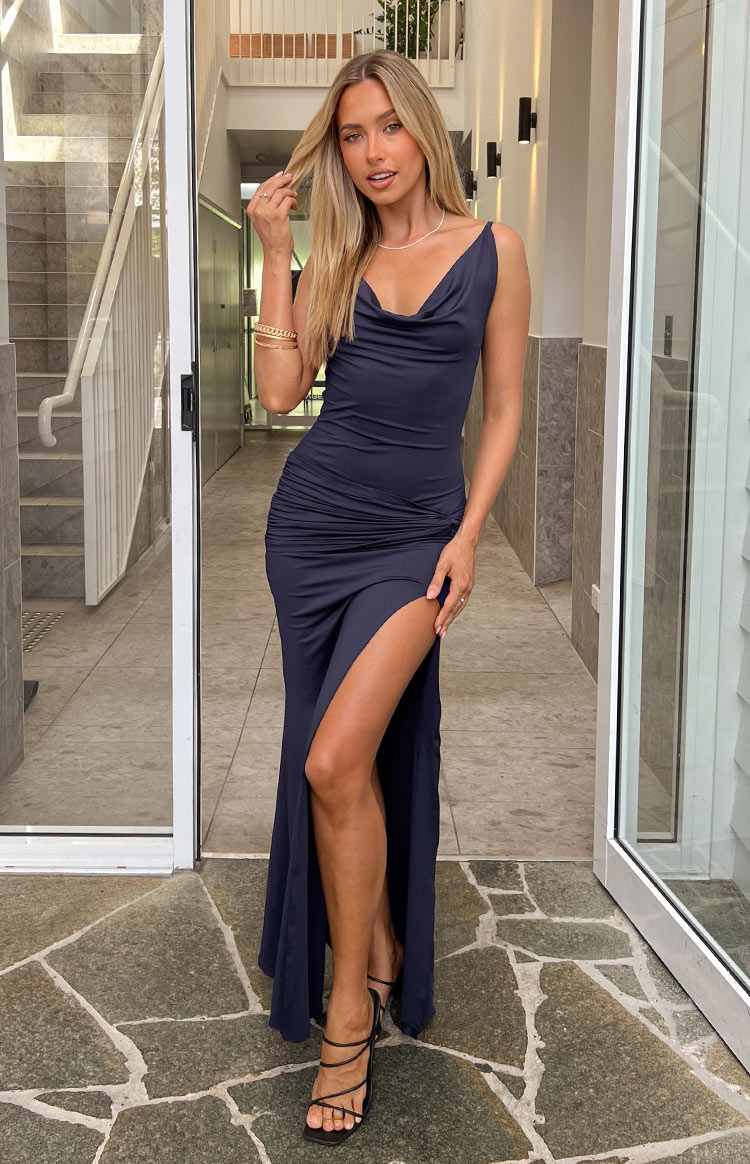
Illustrative Image (Source: Google Search)
Sustainability & Ethical Sourcing in B2B
Sustainability has evolved from a niche concern to a core strategic imperative in the navy maxi dress sector. The environmental footprint of apparel production — particularly water-intensive dyeing processes and synthetic fabric reliance — demands that B2B buyers prioritize eco-friendly materials and manufacturing practices. Navy dresses, often requiring deep indigo or navy dye, pose specific challenges related to chemical usage and wastewater management.
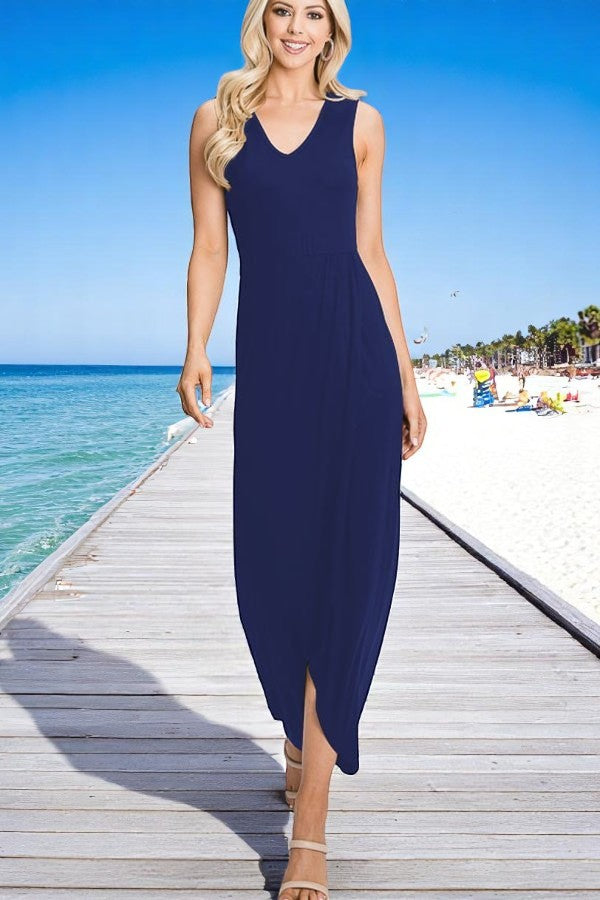
Illustrative Image (Source: Google Search)
Ethical supply chains are no longer optional; they are vital for brand reputation and regulatory compliance, especially for buyers sourcing from regions with varied labor standards. Certifications such as OEKO-TEX Standard 100, Global Organic Textile Standard (GOTS), and Bluesign provide assurance that fabrics and dyes meet stringent environmental and social criteria. Incorporating organic cotton, Tencel, or recycled polyester blends in navy maxi dresses helps reduce carbon footprints and appeals to sustainability-conscious retailers and consumers.
For international buyers, transparency tools like blockchain and supplier audits ensure traceability from raw material sourcing to finished garment, minimizing risks related to forced labor or unethical practices. Moreover, adopting circular economy principles — including recyclable packaging and take-back programs — can enhance long-term value and align with global sustainability goals.
Brief Evolution and Historical Context
The navy maxi dress, rooted in the maxi skirt trends of the late 1960s and early 1970s, has transcended decades to become a wardrobe essential worldwide. Originally symbolizing freedom and casual elegance during the bohemian fashion wave, it has since been adapted by designers into versatile silhouettes suitable for both casual and formal occasions.
From a B2B perspective, understanding this evolution is key to anticipating shifts in consumer demand — from loose, flowing cuts to more structured, tailored styles that meet modern tastes. The navy color, historically associated with authority and sophistication, continues to resonate globally, offering a reliable base for seasonal collections.
Today, the navy maxi dress represents a fusion of heritage and innovation, where traditional craftsmanship meets modern supply chain efficiencies and sustainability imperatives. This balance offers international buyers opportunities to cater to diverse markets while navigating dynamic sourcing landscapes.
Related Video: US-China trade war hits Chinese factories and businesses hard
Frequently Asked Questions (FAQs) for B2B Buyers of navy maxi dress
-
How can I effectively vet suppliers of navy maxi dresses to ensure reliability and quality?
To vet suppliers, start by requesting detailed company profiles, including years in business, production capacity, and compliance certifications (e.g., ISO, SA8000). Verify references from other international buyers, especially within your region. Conduct virtual or in-person factory audits focusing on manufacturing processes, labor conditions, and quality control measures. Utilize third-party inspection services for unbiased quality assessments. Additionally, request samples to evaluate fabric quality, stitching, and color consistency. Prioritize suppliers demonstrating transparent communication, proven compliance with ethical sourcing, and flexibility in meeting your customization and volume needs. -
What customization options are typically available for navy maxi dresses in B2B sourcing, and how do they impact cost and lead time?
Customization can include fabric type, color shades, embellishments, sizing adjustments, and packaging. Some suppliers offer private labeling and design modifications to align with your brand identity. However, custom orders usually require minimum order quantities (MOQs) higher than standard stock and longer lead times due to sample approvals and production adjustments. Costs increase with complexity—unique fabrics, embroidery, or special finishes add to expenses. To optimize, clearly define customization needs upfront and negotiate with suppliers for batch production efficiencies or tiered pricing based on volume. -
What are common minimum order quantities (MOQs), typical lead times, and payment terms for navy maxi dresses when sourcing internationally?
MOQs vary widely but generally range from 100 to 500 pieces per style or color, depending on supplier scale and customization. Lead times typically span 30 to 90 days, factoring in design finalization, production, and quality checks. Payment terms often require a 30-50% deposit upfront, with the balance payable upon shipment or after inspection. Some suppliers may accept letters of credit or escrow services for added security. Negotiate terms that balance your cash flow constraints with supplier requirements, and consider phased orders to reduce inventory risk. -
How can B2B buyers ensure quality assurance (QA) and compliance certifications when importing navy maxi dresses?
Request suppliers’ quality assurance protocols and certifications such as OEKO-TEX Standard 100, Global Organic Textile Standard (GOTS), or WRAP for social compliance. Insist on detailed product specifications and pre-shipment inspection reports. Employ independent third-party inspectors to conduct in-line and final inspections to verify fabric quality, construction, and color fastness. Establish clear defect tolerance levels and return policies in your contract. For buyers in regions with strict import regulations, ensure compliance with local textile and safety standards to avoid customs delays or rejections. -
What logistics considerations should international B2B buyers keep in mind when importing navy maxi dresses?
Plan for multimodal logistics involving sea freight for cost efficiency or air freight for urgent shipments. Factor in customs clearance times, tariffs, and duties which vary by country and trade agreements—especially critical given recent tariff shifts affecting apparel imports. Coordinate with freight forwarders experienced in textile shipments to manage packaging requirements and avoid damage. Use supply chain visibility tools to track shipments in real-time. For buyers in Africa, South America, and the Middle East, consider port infrastructure and inland transport reliability to minimize delays. -
How can B2B buyers mitigate risks related to disputes or delays in navy maxi dress orders?
Mitigate risks by drafting comprehensive purchase agreements outlining product specifications, delivery timelines, payment terms, and dispute resolution mechanisms. Include clauses for penalties or compensation in case of late delivery or quality issues. Use escrow or staged payments linked to milestones. Maintain open communication channels and conduct regular progress checks during production. In case of disputes, explore mediation or arbitration before litigation, especially in cross-border contexts. Partnering with suppliers who have proven track records and transparent operations reduces the likelihood of conflicts. -
Are there region-specific trade regulations or tariffs that B2B buyers should be aware of when sourcing navy maxi dresses?
Yes, trade policies differ significantly by region. For example, buyers in the US and Europe face increased tariffs on apparel imports from certain countries due to recent trade enforcement measures. African and Middle Eastern buyers should verify if preferential trade agreements (e.g., AGOA, COMESA, GCC agreements) apply to reduce duties. South American countries may benefit from Mercosur agreements. Stay updated on tariff schedules and origin rules, especially around “substantial transformation” criteria that affect duty classification. Engaging customs brokers knowledgeable in your region can optimize cost and compliance. -
What payment and financing options are recommended for international B2B buyers purchasing navy maxi dresses?
Common payment methods include telegraphic transfers (T/T), letters of credit (L/C), and open account terms for established relationships. Letters of credit offer security by involving banks as intermediaries, reducing payment risk. For new suppliers, upfront deposits combined with escrow services can protect buyers. Buyers can also explore trade financing solutions like supply chain finance or factoring to improve cash flow. Negotiate payment schedules aligned with production milestones to balance risk. Always confirm that payment methods comply with your country’s foreign exchange regulations and banking norms.
Strategic Sourcing Conclusion and Outlook for navy maxi dress
Strategic sourcing of navy maxi dresses offers international B2B buyers a critical competitive advantage in today’s complex and dynamic apparel market. Key takeaways include the necessity of embracing supply chain visibility, diversifying supplier bases to mitigate tariff risks, and prioritizing ethical and sustainable sourcing practices. Buyers from Africa, South America, the Middle East, and Europe must carefully evaluate raw material origins, manufacturing locations, and logistics partners to optimize cost, quality, and delivery timelines.
In a landscape reshaped by evolving trade policies and consumer demand for transparency, strategic sourcing is no longer just a cost exercise but a driver of resilience and brand reputation. Leveraging technology for inventory management and predictive analytics enhances decision-making, while flexible supply chains enable rapid responses to market shifts and tariff changes. Collaborations with suppliers who adhere to fair labor and environmental standards will increasingly resonate with global consumers.
Looking ahead, B2B buyers are encouraged to adopt an agile sourcing approach—balancing nearshoring opportunities, free trade zones, and innovative materials—to future-proof their navy maxi dress offerings. Engage proactively with suppliers, invest in supply chain intelligence, and cultivate partnerships that align with your strategic goals. This forward-thinking mindset will position your business to thrive amid ongoing global trade complexities and evolving fashion trends.