Your Ultimate Guide to Sourcing Army Mess Dress
Guide to Army Mess Dress
- Introduction: Navigating the Global Market for army mess dress
- Understanding army mess dress Types and Variations
- Key Industrial Applications of army mess dress
- Strategic Material Selection Guide for army mess dress
- In-depth Look: Manufacturing Processes and Quality Assurance for army mess dress
- Comprehensive Cost and Pricing Analysis for army mess dress Sourcing
- Spotlight on Potential army mess dress Manufacturers and Suppliers
- Essential Technical Properties and Trade Terminology for army mess dress
- Navigating Market Dynamics, Sourcing Trends, and Sustainability in the army mess dress Sector
- Frequently Asked Questions (FAQs) for B2B Buyers of army mess dress
- Strategic Sourcing Conclusion and Outlook for army mess dress
Introduction: Navigating the Global Market for army mess dress
The global demand for army mess dress uniforms reflects their enduring significance in military tradition and formal ceremonial occasions worldwide. For B2B buyers engaged in defense supply chains, procuring authentic, high-quality mess dress uniforms is crucial—not only to meet stringent military specifications but also to uphold the dignity and professionalism of armed forces personnel. Whether outfitting officers in the UK, Brazil, or emerging military markets in Africa, South America, and the Middle East, understanding the nuances of these uniforms is key to successful sourcing.
This guide offers a comprehensive roadmap to navigating the complex international market for army mess dress. It covers a broad spectrum of essential topics: from detailed classifications of mess dress types and the premium materials used, to manufacturing standards and rigorous quality control processes. Buyers will gain insights into identifying reputable suppliers, analyzing cost structures, and understanding regional market dynamics that influence pricing and availability.
Additionally, the guide addresses common questions and challenges faced by international purchasers, providing practical solutions to mitigate risks such as counterfeit products, sizing inconsistencies, and compliance with military regulations. By equipping buyers with this knowledge, the guide empowers procurement professionals to make informed, strategic decisions that ensure value, authenticity, and timely delivery.
For defense contractors and uniform distributors operating across Africa, South America, the Middle East, and Europe, this resource is an indispensable tool to streamline sourcing, enhance supplier negotiations, and maintain the highest standards of military attire excellence on a global scale.
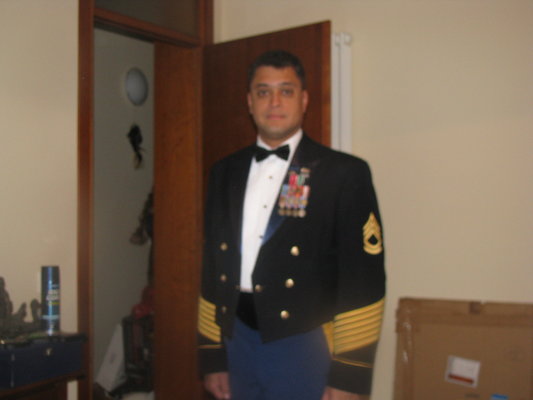
Illustrative Image (Source: Google Search)
Understanding army mess dress Types and Variations
Type Name | Key Distinguishing Features | Primary B2B Applications | Brief Pros & Cons for Buyers |
---|---|---|---|
Army Blue Mess Dress | Dark blue coat, black cummerbund or white vest, black oxford shoes, optional cape for officers | Formal military dinners, ceremonial events | Pros: Classic, recognizable; Cons: Limited to formal events, sizing complexity |
Army Evening Mess Dress | Similar to Army Blue but with white vest, white gloves, and formal shirt with studs | Black-tie military occasions, evening receptions | Pros: High formality, elegant; Cons: Higher cost, seasonal wear constraints |
Cold-Weather Mess Dress | Includes black all-weather coat, black leather gloves, AG 489 cold-weather cap | Outdoor formal events in cold climates | Pros: Functional for cold climates; Cons: Bulkier, less versatile indoors |
Officer’s Cape Variation | Army blue cape replacing coat for officers only, exclusive design and wear policy | Officer formal events, after-duty social events | Pros: Distinguished look, exclusive; Cons: Not for enlisted, higher price |
Semi-Formal Mess Dress | Blue service cap optional, white dress shirts (soft bosom), black cummerbund | Less formal military gatherings, semi-formal dinners | Pros: Versatile, cost-effective; Cons: Less prestigious, limited ceremonial use |
The Army Blue Mess Dress is the standard formal uniform featuring a dark blue coat paired with a black cummerbund or white vest, complemented by black oxford shoes. It is widely used in formal military dinners and ceremonial events. For B2B buyers, sourcing this uniform requires attention to high-quality fabric and precise tailoring to maintain the traditional look, ensuring durability and comfort for prolonged wear.
The Army Evening Mess Dress elevates formality by incorporating a white vest, white gloves, and a formal dress shirt with studs. It suits black-tie military occasions and evening receptions. Buyers should consider the higher production costs and seasonal demand, as these uniforms are typically reserved for special events, necessitating premium materials and accessories.
For colder climates, the Cold-Weather Mess Dress variation includes a black all-weather coat, black leather gloves, and the AG 489 cold-weather cap. This type is essential for formal outdoor events in regions with harsh weather, making it particularly relevant for buyers in colder parts of Europe and the Middle East. Bulk and layering considerations affect supply chain logistics and inventory management.
The Officer’s Cape Variation offers a unique, exclusive alternative to the standard coat, reserved for officers only. The army blue cape provides a distinguished appearance for after-duty social events and formal officer functions. B2B buyers must factor in exclusivity, higher costs, and strict wear policies when sourcing this variation, ensuring compliance with military regulations.
Lastly, the Semi-Formal Mess Dress is a more versatile option featuring optional blue service caps, softer dress shirts, and the black cummerbund. It fits semi-formal dinners and less rigid military gatherings, ideal for buyers seeking cost-effective solutions with moderate formality. However, it lacks the prestige of full mess dress uniforms, limiting its use in highly ceremonial settings.
Related Video: Large Language Models (LLMs) – Everything You NEED To Know
Key Industrial Applications of army mess dress
Industry/Sector | Specific Application of army mess dress | Value/Benefit for the Business | Key Sourcing Considerations for this Application |
---|---|---|---|
Defense & Military Supply | Formal military ceremonies and official functions | Enhances military professionalism and tradition; supports morale | Compliance with military dress codes; quality of fabric and tailoring; durability for repeated use |
Event Management & Hospitality | High-end military and governmental formal events | Projects prestige and protocol adherence; ensures uniformity in appearance | Customization options; timely delivery; adherence to formal specifications and insignia placement |
Uniform Manufacturing & Textile | Production of specialized ceremonial military attire | Expands product portfolio; meets niche demand for ceremonial uniforms | Access to approved patterns; sourcing premium materials like silk and satin; quality control standards |
Government & Protocol Services | Diplomatic receptions and state dinners | Upholds national image and ceremonial decorum; facilitates protocol compliance | Accurate rank insignia and accessories; cultural sensitivity in design; reliable supply chain |
International Military Training & Exchange Programs | Uniform provision for visiting officers and delegations | Promotes interoperability and respect among allied forces; supports formal engagements | Standardized sizing; cross-national design compatibility; ease of customization for different ranks |
The Defense & Military Supply sector relies heavily on army mess dress uniforms for formal ceremonies, parades, and official functions. These uniforms are essential in maintaining the dignity and tradition of armed forces, boosting troop morale, and projecting a professional image. International B2B buyers from regions such as Africa, South America, the Middle East, and Europe must ensure suppliers can meet strict military dress codes and deliver durable, high-quality materials capable of withstanding frequent wear and cleaning.
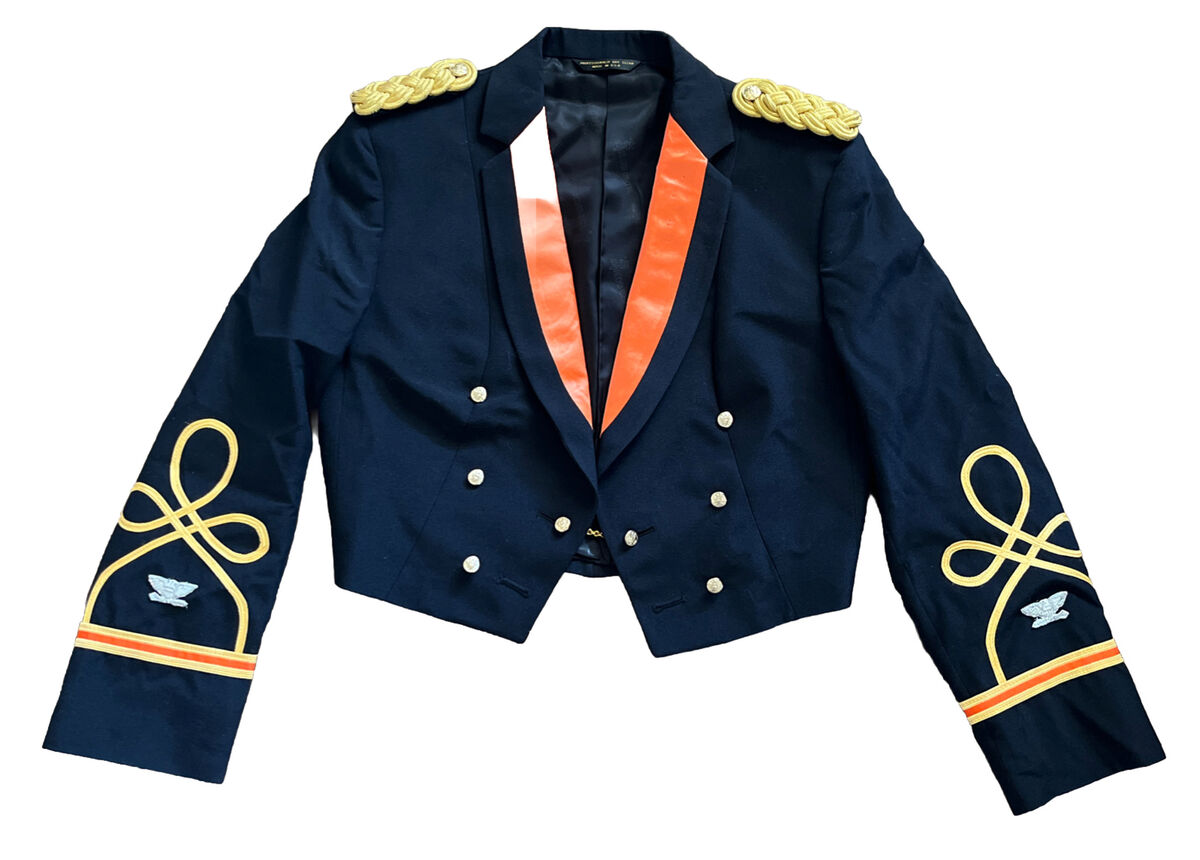
Illustrative Image (Source: Google Search)
In Event Management & Hospitality, army mess dress uniforms are critical for organizing and managing high-profile military and governmental events. These uniforms provide a standardized and prestigious look that reinforces protocol and ceremony. Buyers should prioritize suppliers who offer customization options, can guarantee punctual delivery, and strictly adhere to official specifications, including the correct placement of insignia and accessories, which is particularly important for events in culturally diverse regions.
For companies in Uniform Manufacturing & Textile, producing army mess dress uniforms opens access to a specialized market segment requiring precision tailoring and premium materials such as silk or satin for cummerbunds and bow ties. B2B buyers from emerging markets and established economies alike must focus on sourcing from manufacturers who follow approved patterns and maintain rigorous quality control to ensure consistency and authenticity in ceremonial attire.
Government & Protocol Services utilize army mess dress uniforms extensively during diplomatic receptions, state dinners, and formal protocol occasions. These uniforms help uphold national image and ensure adherence to formal decorum. Buyers should seek suppliers capable of providing accurate rank insignia, culturally sensitive design options, and a reliable supply chain to meet the demands of international diplomatic events, especially in regions with diverse protocol traditions.
Lastly, International Military Training & Exchange Programs require army mess dress uniforms for visiting officers and delegations to foster mutual respect and interoperability during formal engagements. Procurement professionals should ensure standardized sizing and design compatibility across different national forces, while also allowing for customization according to rank and country-specific requirements. This is vital for smooth integration during multinational exercises or diplomatic visits in Africa, South America, the Middle East, and Europe.
Related Video: U.S Army Reintroduces Army Green Service Uniforms
Strategic Material Selection Guide for army mess dress
Wool
Key Properties: Wool is a natural fiber known for its excellent insulation, breathability, and moisture-wicking capabilities. It maintains warmth in cold climates while allowing ventilation in warmer environments. Wool also exhibits good resilience and wrinkle resistance, making it suitable for formal military attire.
Pros & Cons: Wool offers superior durability and a prestigious appearance, which is essential for ceremonial army mess dress. It is naturally flame-resistant and biodegradable, appealing to eco-conscious buyers. However, wool can be costly and requires specialized manufacturing processes like careful weaving and finishing. It may also be less comfortable in hot, humid climates without proper ventilation.
Impact on Application: Wool’s insulating properties make it ideal for mess dress uniforms used in temperate to cold regions, such as Europe and parts of the Middle East during winter. Its natural breathability suits varied climates but may require blending with synthetic fibers for enhanced durability and moisture management in tropical zones like parts of Africa and South America.
International B2B Considerations: Buyers from Europe and the UK often prefer high-grade wool complying with standards like ASTM D6193 or EN 12127 for fiber content and performance. In Africa and South America, sourcing wool blends that balance cost and climate adaptability is common. Compliance with international textile certifications (e.g., OEKO-TEX) can be a decisive factor for buyers focusing on sustainability and quality assurance.
Polyester
Key Properties: Polyester is a synthetic fiber known for its strength, wrinkle resistance, and color retention. It has excellent dimensional stability and dries quickly, making it resistant to shrinking and stretching. Polyester is also resistant to mildew and abrasion.
Pros & Cons: Polyester is cost-effective and easier to manufacture at scale, which benefits large uniform orders. It is lightweight and durable, suitable for warmer climates. However, polyester lacks the natural breathability of wool and can trap heat, potentially reducing comfort in hot environments. It also has lower flame resistance compared to natural fibers.
Impact on Application: Polyester is widely used in mess dress uniforms for regions with hot and humid climates, such as parts of Africa and South America, where moisture management and durability are critical. It is often blended with wool or cotton to improve comfort and appearance while maintaining affordability.
International B2B Considerations: Polyester fabrics must meet international standards such as ISO 105 for colorfastness and ASTM D5034 for tensile strength. Buyers from the Middle East and Europe require certifications ensuring UV resistance and flame retardancy, especially for ceremonial uniforms. Suppliers offering customized blends with wool or cotton have a competitive advantage in these markets.
Silk (for accessories like cummerbunds and bow ties)
Key Properties: Silk is a natural protein fiber prized for its lustrous appearance, smooth texture, and lightweight feel. It offers moderate thermal regulation and excellent drape, making it ideal for formal accessories.
Pros & Cons: Silk adds a high-end, luxurious touch to mess dress components such as cummerbunds and bow ties, enhancing the overall aesthetic. It is breathable and comfortable but delicate, requiring careful handling and higher manufacturing costs. Silk is susceptible to damage from moisture and sunlight.
Impact on Application: Silk is predominantly used for decorative elements rather than the main uniform fabric. Its elegance aligns with ceremonial use, especially in European and Middle Eastern markets where tradition and presentation are paramount. For tropical climates, silk accessories may require protective storage or blending with synthetic fibers.
International B2B Considerations: Buyers in Brazil and Europe often look for silk complying with standards like ISO 105 for colorfastness and responsible sourcing certifications (e.g., GOTS for organic silk). The ability to provide custom dyeing and finishing services tailored to military insignia and color schemes is highly valued.
Cotton
Key Properties: Cotton is a natural cellulose fiber known for its softness, breathability, and moisture absorbency. It is comfortable for extended wear and hypoallergenic. Cotton fabrics vary widely in weave and weight, affecting durability and appearance.
Pros & Cons: Cotton is affordable and easy to manufacture, making it a popular choice for mess dress shirts and lining materials. It offers good comfort in warm climates but wrinkles easily and has lower durability compared to wool or polyester blends. Cotton also has limited flame resistance.
Impact on Application: Cotton is ideal for dress shirts worn under mess coats, especially in hot and humid regions like Africa and South America. It can be blended with polyester to improve wrinkle resistance and durability while maintaining comfort.
International B2B Considerations: Compliance with standards such as ASTM D3775 (fabric count) and ISO 6330 (washing procedures) is critical for buyers in Europe and the Middle East. Cotton sourced from Brazil and African countries often appeals due to local availability and cost advantages. Buyers emphasize certifications related to pesticide use and organic farming practices.
Material | Typical Use Case for army mess dress | Key Advantage | Key Disadvantage/Limitation | Relative Cost (Low/Med/High) |
---|---|---|---|---|
Wool | Main fabric for mess dress coats and trousers | Excellent insulation, durability, and prestigious appearance | Higher cost and less comfortable in hot climates without blends | High |
Polyester | Blended fabrics for mess dress uniforms and linings | Cost-effective, durable, wrinkle-resistant | Less breathable, lower flame resistance | Low |
Silk | Accessories like cummerbunds and bow ties | Luxurious appearance and smooth texture | Delicate, requires careful handling | High |
Cotton | Dress shirts and lining materials | Comfortable, breathable, and affordable | Prone to wrinkling and less durable | Low |
In-depth Look: Manufacturing Processes and Quality Assurance for army mess dress
Manufacturing army mess dress uniforms demands a combination of traditional tailoring craftsmanship and modern quality control protocols to meet stringent military standards. For international B2B buyers, especially from regions such as Africa, South America, the Middle East, and Europe, understanding these manufacturing stages and quality assurance measures is critical for selecting reliable suppliers and ensuring product compliance.
Key Manufacturing Stages for Army Mess Dress
-
Material Preparation
– Fabric Selection: Premium wool blends, high-quality silk, satin, and cotton fabrics are commonly sourced to match military specifications. Material properties like durability, colorfastness, and wrinkle resistance are prioritized.
– Inspection: Incoming raw materials undergo initial quality checks for defects, color consistency, and compliance with contract specifications.
– Cutting: Using precision cutting tools and sometimes automated cutters, fabric pieces are cut according to approved patterns to minimize waste and ensure uniformity. -
Forming and Tailoring
– Pattern Making: Detailed patterns based on military designs are created or approved by defense authorities. These include precise measurements for coats, trousers, vests, and accessories such as cummerbunds.
– Sewing and Assembly: Skilled tailors assemble the cut pieces using industrial sewing machines. Techniques include reinforced stitching on stress points and precise alignment of insignias, lapels, and trims.
– Detailing: Incorporation of decorative elements such as gold or white cufflinks, buttons, epaulets, and branch insignias. These are often hand-sewn or attached with specialized machinery to ensure durability and aesthetic accuracy. -
Finishing Processes
– Pressing and Shaping: Uniforms undergo professional pressing to achieve sharp creases and the distinctive silhouette required by military dress codes.
– Accessory Integration: Gloves, hats, and other approved accessories are matched and packaged with the uniform.
– Packaging: Uniforms are carefully folded or hung in protective packaging to prevent damage during transport.
Quality Assurance and Control Checkpoints
Quality control (QC) is integrated at multiple stages to ensure uniformity, compliance, and durability:
- Incoming Quality Control (IQC): Verification of raw materials’ compliance with military-grade fabric specifications, color standards, and accessory authenticity.
- In-Process Quality Control (IPQC): Ongoing inspections during cutting, sewing, and assembly phases to detect defects early, including stitching integrity, pattern accuracy, and accessory placement.
- Final Quality Control (FQC): Comprehensive evaluation of finished uniforms for overall appearance, dimensional accuracy, and functional tests such as button strength and fabric resilience.
Relevant International and Industry Standards
- ISO 9001: The globally recognized quality management system standard is often the baseline for textile and uniform manufacturers, ensuring consistent production processes and continuous improvement.
- Military Specifications (Mil-Specs): Many army mess dress uniforms must adhere to strict military standards that dictate fabric type, color shades, insignia placement, and accessory specifications.
- CE Marking & API Standards: While CE marking is primarily for products sold within the European Economic Area, certain uniform components or materials may require compliance with regional safety or material standards. API standards are less common but may apply if uniforms incorporate specialized protective features.
Common Testing Methods in Quality Assurance
- Colorfastness Testing: Ensures the uniform colors do not fade or bleed under washing or exposure to sunlight.
- Tensile and Tear Strength: Fabric and accessory durability are tested under stress to guarantee longevity.
- Dimensional Stability: Uniform pieces are tested for shrinkage and deformation after laundering.
- Accessory Durability: Buttons, cufflinks, and insignias undergo pull and abrasion tests.
- Visual Inspections: Detailed audits to check for defects such as loose threads, uneven stitching, or incorrect insignia placement.
How B2B Buyers Can Verify Supplier Quality Control
- Factory Audits: Conduct or commission on-site inspections to assess manufacturing facilities, machinery, worker expertise, and QC processes.
- Review of Quality Reports: Request detailed inspection reports, including IQC, IPQC, and FQC documentation, along with certificates of compliance to relevant standards.
- Third-Party Inspections: Engage independent inspection agencies to perform random sampling and testing of products before shipment.
- Sample Evaluations: Obtain and evaluate physical samples to verify craftsmanship, materials, and adherence to specifications prior to bulk orders.
- Supplier Certifications: Confirm supplier certifications such as ISO 9001, and adherence to military or regional standards relevant to the buyer’s country.
QC and Certification Nuances for International Buyers
- Africa and South America: Buyers should emphasize supplier compliance with both international standards and any regional textile or import regulations. Local climatic conditions may also affect fabric choices and require suppliers to demonstrate durability under heat and humidity.
- Middle East: Given the preference for high-quality, formal military attire, buyers often require rigorous adherence to fabric quality and accessory detail. Suppliers experienced with regional military dress codes and cultural considerations are preferred.
- Europe (UK, Brazil, etc.): European buyers usually demand strict compliance with ISO standards and may require CE marking on certain components. They also tend to expect transparent QC documentation and traceability throughout the supply chain.
- Cross-border Logistics: Quality assurance should include packaging standards to prevent damage during long-distance shipping and customs inspections.
Strategic Recommendations for B2B Buyers
- Establish clear technical specifications and quality benchmarks upfront with suppliers.
- Invest in supplier development programs or joint quality improvement initiatives to tailor manufacturing processes to specific market needs.
- Utilize digital tools for remote factory audits and real-time quality monitoring when physical visits are constrained.
- Negotiate contracts that include penalties or corrective actions for non-compliance with QC standards.
By comprehensively understanding manufacturing workflows and quality assurance protocols, international B2B buyers can confidently source army mess dress uniforms that meet exacting military standards while aligning with regional regulatory and cultural requirements.
Related Video: Top 10 Most Incredible Manufacturing And Mass Production Process Videos
Comprehensive Cost and Pricing Analysis for army mess dress Sourcing
Breakdown of Cost Components in Army Mess Dress Production
When sourcing army mess dress uniforms, understanding the detailed cost components is crucial for effective budgeting and negotiation. The primary cost drivers include:
- Materials: High-quality fabrics such as wool blends, silk (for accessories like cummerbunds), and durable trims contribute significantly to cost. Specialized materials meeting military specifications or certifications (e.g., fire retardant, moisture-wicking) may increase raw material expenses.
- Labor: Skilled tailoring and embroidery, often required for rank insignia, badges, and precise fitting, represent a substantial portion of labor costs. Labor rates vary widely by region, affecting overall pricing.
- Manufacturing Overhead: This includes factory utilities, equipment depreciation, and indirect labor. Factories with advanced machinery or automated processes may have higher overhead but can achieve efficiency gains.
- Tooling and Equipment: Custom molds or patterns for buttons, badges, and specific uniform cuts require upfront investment, especially for bespoke designs or limited production runs.
- Quality Control (QC): Rigorous inspection processes to ensure adherence to military standards, including fabric quality, stitching, and accessory authenticity, add to operational costs but are critical for compliance.
- Logistics and Shipping: Depending on the buyer’s location, transportation, customs duties, and insurance fees can substantially influence landed cost. Sourcing from overseas suppliers introduces complexities such as tariffs and longer lead times.
- Profit Margin: Suppliers factor in margins based on brand reputation, exclusivity, and service levels. Bulk orders may attract lower margins due to volume discounts.
Key Price Influencers Affecting Army Mess Dress Cost
Several factors beyond basic cost components impact the final pricing of army mess dress uniforms:
- Order Volume and Minimum Order Quantities (MOQ): Larger orders typically benefit from economies of scale. Small or customized orders may incur premium pricing due to setup costs.
- Specifications and Customization: Uniforms tailored to specific military branches or ranks, incorporating unique insignia, embroidery, or authorized accessories (e.g., black cummerbund, shoulder boards), increase complexity and cost.
- Material Quality and Certifications: Compliance with military-grade fabric standards or certifications can drive prices higher but ensures durability and authenticity.
- Supplier Capabilities and Location: Established suppliers with military contracts or certifications often command premium pricing but provide reliability. Regional supplier location affects labor costs and shipping expenses.
- Incoterms and Payment Terms: The choice of Incoterms (e.g., FOB, CIF, DDP) determines responsibility for shipping, customs clearance, and insurance, influencing total landed cost. Favorable payment terms can also improve cash flow and reduce financial risk.
Actionable Buyer Tips for International B2B Procurement
For buyers in Africa, South America, the Middle East, and Europe, navigating army mess dress sourcing requires strategic considerations:
- Negotiate Volume Discounts and Flexible MOQs: Engage suppliers early to discuss volume-based pricing tiers. For smaller orders, explore shared production runs or consolidated shipments to reduce unit costs.
- Prioritize Total Cost of Ownership (TCO): Assess beyond unit price by factoring in logistics, customs duties, lead times, and after-sales service. Delays or quality issues can increase overall expenditure.
- Validate Supplier Certifications and Compliance: Ensure suppliers meet relevant military standards and certifications to avoid costly rejections or non-compliance penalties.
- Leverage Incoterms Wisely: Opt for Incoterms that align with your import capabilities and risk tolerance. For example, DDP (Delivered Duty Paid) reduces import complexity but may carry a premium.
- Account for Regional Pricing Nuances: Currency fluctuations, import tariffs, and local regulations impact pricing. Work with local trade advisors or customs brokers to optimize cost structures.
- Request Detailed Cost Breakdowns: Transparency from suppliers on cost elements helps identify savings opportunities, such as alternative materials or simplified accessory options.
- Plan for Long-Term Relationships: Establishing consistent supplier partnerships can unlock better pricing, priority production slots, and tailored service for recurring orders.
Disclaimer on Pricing
Prices for army mess dress uniforms can vary widely based on supplier, customization level, and order specifics. The information provided herein serves as a general guideline to assist buyers in making informed decisions. Prospective purchasers should conduct direct supplier engagement and obtain quotations tailored to their unique requirements.
Spotlight on Potential army mess dress Manufacturers and Suppliers
This section offers a look at a few manufacturers active in the ‘army mess dress’ market. This is a representative sample for illustrative purposes; B2B buyers must conduct their own extensive due diligence before any engagement. Information is synthesized from public sources and general industry knowledge.
Essential Technical Properties and Trade Terminology for army mess dress
Critical Technical Properties for Army Mess Dress
When sourcing army mess dress uniforms, understanding key technical specifications is essential for ensuring product quality, uniformity, and compliance with military standards. Below are the most critical properties international B2B buyers should prioritize:
-
Material Grade and Composition
High-quality fabrics such as wool blends or premium polyester are standard for durability, comfort, and appearance. Material grade directly impacts the uniform’s longevity and wearer comfort in various climates, a crucial consideration for buyers in Africa, South America, the Middle East, and Europe. Confirm certifications or test reports verifying fiber content and fabric weight (typically measured in grams per square meter). -
Color Fastness and Shade Consistency
Uniform colors, particularly the distinctive army blue or black, must meet strict colorfastness standards to prevent fading and ensure consistency across batches. This property affects the professional appearance of the uniform and is vital for maintaining brand and military identity integrity. Request color matching standards and sample approvals before bulk orders. -
Precision Tailoring and Size Tolerances
Mess dress uniforms require precise tailoring with strict adherence to size charts and fit specifications. Tolerances in garment dimensions (e.g., sleeve length, waist size) should be minimal to maintain uniformity across personnel. Buyers should specify acceptable tolerance ranges to suppliers to guarantee consistent fit and comfort. -
Accessory Integration and Compatibility
Components such as cummerbunds, vests, gloves, and headgear must be compatible in style and materials with the main uniform. The technical property here involves accessory design standards and material compatibility to ensure cohesive appearance and functional wearability. -
Durability and Maintenance Requirements
Military mess dress must withstand repeated use and cleaning without losing structural integrity or appearance. Properties such as stain resistance, wrinkle resistance, and ease of dry cleaning are important for long-term cost-effectiveness. Buyers should inquire about maintenance instructions and fabric treatments applied. -
Ornamentation and Embellishment Standards
Buttons, insignia, and rank badges must conform to military specifications regarding material, finish (e.g., gold or silver plating), and attachment methods. These technical details affect both the uniform’s aesthetics and durability during wear.
Key Industry and Trade Terms for B2B Buyers
Navigating international procurement of army mess dress uniforms involves familiarity with common trade terms and industry jargon that streamline communication and transactions:
-
OEM (Original Equipment Manufacturer)
Refers to a manufacturer that produces uniforms based on specific military designs or standards provided by the buyer. OEM partnerships ensure authenticity and compliance but may require minimum order quantities and longer lead times. -
MOQ (Minimum Order Quantity)
The smallest number of units a supplier is willing to produce or sell in one order. Understanding MOQ is critical for budget planning and inventory management, especially when ordering for smaller military units or multinational forces. -
RFQ (Request for Quotation)
A formal process where buyers solicit detailed price quotes from suppliers for specific uniform specifications and quantities. RFQs enable price comparison and help define contract terms clearly before commitment. -
Incoterms (International Commercial Terms)
Standardized trade terms defining responsibilities, costs, and risks between buyers and sellers during shipping. Common terms include FOB (Free on Board), CIF (Cost, Insurance, Freight), and DDP (Delivered Duty Paid). Knowing Incoterms helps buyers control logistics costs and customs clearance processes effectively. -
Lead Time
The total time from placing an order to receiving the finished uniforms. Lead time affects project scheduling and deployment readiness; buyers should negotiate realistic lead times based on supplier capacity and production complexity. -
Quality Assurance (QA) and Quality Control (QC)
QA refers to systematic processes ensuring uniforms meet design and performance standards throughout production, while QC involves inspection and testing of finished products. Buyers should request supplier QA/QC protocols to mitigate risks of receiving substandard goods.
Understanding these technical properties and trade terms empowers international B2B buyers to make informed procurement decisions, ensuring the acquisition of high-quality, compliant army mess dress uniforms tailored to their specific operational and cultural environments.
Navigating Market Dynamics, Sourcing Trends, and Sustainability in the army mess dress Sector
Market Overview & Key Trends
The global market for army mess dress uniforms is shaped by a combination of tradition, stringent military standards, and evolving sourcing strategies. For international B2B buyers in Africa, South America, the Middle East, and Europe, understanding regional demand and supply chain complexities is critical. The demand is driven by official military procurement cycles, ceremonial functions, and the need for high-quality, durable garments that comply with strict dress codes. Countries such as the UK and Brazil emphasize authenticity and adherence to detailed uniform specifications, while emerging markets in Africa and the Middle East are increasingly investing in modernized military apparel to bolster formal representation.
Technological advancements are influencing sourcing trends, with digital textile printing and precision tailoring enabling customization at scale. Buyers should note a growing preference for suppliers that integrate advanced fabric technologies—such as moisture-wicking, wrinkle resistance, and cold-weather adaptability—without compromising the traditional aesthetic. Additionally, modular procurement models that allow for component upgrades (e.g., detachable capes, specialized gloves, or alternative headgear) are gaining traction, providing flexibility and cost-efficiency.
Market dynamics also reflect a shift toward regional manufacturing hubs to reduce lead times and logistics costs. For example, European suppliers often serve as quality benchmarks, while manufacturers in Brazil and South Africa are increasingly competitive in price and delivery. Buyers must evaluate vendor capabilities in meeting compliance standards such as detailed insignia placement, authorized materials (silk, satin for cummerbunds), and precise tailoring patterns that align with official military regulations.
Sustainability & Ethical Sourcing in B2B
Environmental considerations are becoming paramount in the army mess dress sector, where traditional materials like silk and wool dominate. B2B buyers are encouraged to engage suppliers who prioritize sustainable sourcing practices, such as using organic cotton blends, recycled polyester, and low-impact dyeing techniques to reduce water and chemical usage. Ethical supply chains are critical, ensuring fair labor practices and transparency, especially when sourcing from regions with varied regulatory oversight like parts of Africa and South America.
Green certifications—such as OEKO-TEX Standard 100 for textile safety, GOTS (Global Organic Textile Standard), and bluesign®—are increasingly requested by institutional buyers to verify environmental compliance. Furthermore, suppliers adopting circular economy principles, including garment recycling and biodegradable packaging, offer added value. These practices not only align with global military sustainability mandates but also enhance brand reputation and meet the growing expectations of governments and defense departments to reduce their carbon footprint.
In practical terms, buyers should seek partnerships with manufacturers who demonstrate commitment to sustainability through traceable supply chains, eco-friendly materials, and innovations like waterless dyeing or biodegradable garment components. This focus not only mitigates environmental impact but also reduces risks related to regulatory compliance and supply chain disruptions.
Brief Evolution & Historical Context
Army mess dress uniforms have a rich heritage, originating from 19th-century European military traditions where formal evening attire was essential for officers’ social and ceremonial functions. Initially influenced by royal court fashion, mess dress evolved to emphasize elegance combined with symbolic military insignia and regimental colors. Over time, this attire has maintained a balance between ceremonial prestige and functional design, incorporating elements like high-waisted trousers, cummerbunds, and specific glove and headgear regulations.
For B2B buyers, understanding this historical context is important as it underscores the non-negotiable nature of uniform authenticity and adherence to prescribed patterns and materials. This legacy drives demand for specialized craftsmanship and often limits sourcing flexibility, making it essential to partner with suppliers who are well-versed in military dress codes and capable of delivering consistent quality that honors tradition while meeting contemporary operational needs.
Related Video: International Trade 101 | Economics Explained
Frequently Asked Questions (FAQs) for B2B Buyers of army mess dress
-
How can I effectively vet suppliers of army mess dress uniforms for international procurement?
To ensure reliability, conduct thorough due diligence including verifying business licenses, certifications (ISO, military-grade compliance), and references from previous B2B clients. Request detailed product samples to assess material quality and craftsmanship. Engage with suppliers who specialize in military uniforms and have experience exporting to your region (Africa, South America, Middle East, Europe). Utilize third-party audit services or local agents to validate manufacturing facilities and ethical labor practices. Transparent communication and clear contractual terms on quality and delivery also mitigate risks. -
Is customization available for army mess dress orders, and what are typical options?
Most reputable suppliers offer customization to meet national military regulations or specific unit requirements. Customization options commonly include insignia placement, branch-specific ornamentation, rank badges, fabric choice, sizing variations, and accessory integration (e.g., cummerbunds, gloves, headgear). When sourcing internationally, clarify design specifications early and provide official military uniform standards documents. Customization may affect lead times and costs, so confirm these details upfront to align with your operational needs. -
What are the usual minimum order quantities (MOQs) and lead times for army mess dress uniforms?
MOQs typically range from 50 to 200 units depending on supplier capacity and customization complexity. Lead times average between 8 to 16 weeks, factoring design finalization, production, quality assurance, and shipping. Bulk orders may benefit from reduced per-unit pricing but require careful demand forecasting to avoid overstock. For urgent requirements, discuss expedited production options, though these usually come at a premium. Establishing long-term contracts can improve lead time predictability and supplier prioritization. -
Which payment terms are standard in international B2B deals for army mess dress procurement?
Common payment terms include a 30-50% upfront deposit with the balance paid upon inspection or delivery. Letters of Credit (L/C) and Escrow services provide added security for both parties, especially when dealing with new suppliers. Wire transfers (T/T) are widely accepted, but buyers should verify banking details carefully to avoid fraud. Negotiating net payment terms (e.g., Net 30) is possible for established relationships. Always ensure contracts clearly specify payment milestones linked to production and shipment stages. -
What quality assurance measures and certifications should I expect from suppliers of army mess dress?
Suppliers should adhere to military textile standards such as durability, colorfastness, and fabric composition aligned with official regulations. Certifications like ISO 9001 for quality management and compliance with international military uniform standards add credibility. Ask for inspection reports, material test certificates, and third-party lab results. Pre-shipment quality audits and sample approvals are crucial to prevent discrepancies. Insist on documented traceability for raw materials and manufacturing processes to ensure consistent product quality.
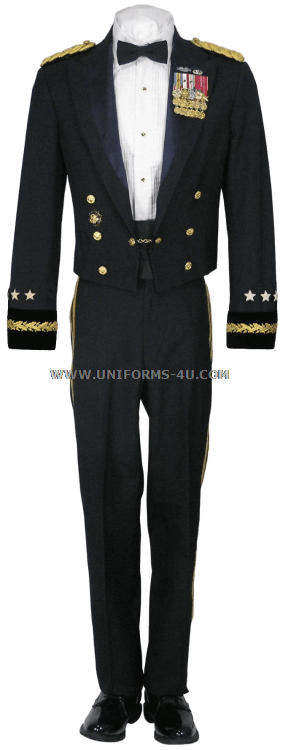
Illustrative Image (Source: Google Search)
-
How do logistics and shipping work for international orders of army mess dress uniforms?
Suppliers typically offer FOB (Free On Board) or CIF (Cost, Insurance, and Freight) shipping terms. Choose logistics partners experienced in handling military-grade apparel to ensure secure and timely delivery. Customs clearance requires accurate HS codes and import documentation reflecting military uniform classification. Consider air freight for urgent deliveries and sea freight for cost efficiency on large orders. Coordinate with freight forwarders familiar with your destination country’s import regulations to avoid delays or additional duties. -
What strategies can help resolve disputes or quality issues post-delivery in international army mess dress transactions?
Establish clear contract clauses covering inspection rights, return policies, and dispute resolution mechanisms (e.g., arbitration or mediation). Maintain detailed documentation of all communications, specifications, and quality checks. In case of defects, promptly notify the supplier with evidence such as photos and inspection reports. Negotiate remedies such as replacements, repairs, or partial refunds. Building long-term partnerships encourages suppliers to address issues cooperatively. Consider third-party quality inspections upon arrival to objectively assess compliance. -
Are there regional considerations when sourcing army mess dress for markets in Africa, South America, the Middle East, and Europe?
Yes, regional climate, cultural preferences, and military dress codes influence fabric choices and uniform design. For example, lighter, breathable materials may be preferred in tropical African or Middle Eastern climates, while European orders might emphasize formal cuts and winter accessories. Import regulations and tariffs vary widely; thus, understanding local trade agreements and customs procedures is critical. Language barriers and time zone differences also necessitate clear communication protocols and flexibility in scheduling. Partnering with regional agents or distributors can ease market entry and after-sales support.
Strategic Sourcing Conclusion and Outlook for army mess dress
Strategic sourcing of army mess dress uniforms demands a nuanced approach that balances quality, compliance, and cultural relevance. For B2B buyers across Africa, South America, the Middle East, and Europe, understanding precise uniform specifications—such as authorized materials, design patterns, and accessory standards—is critical. Prioritizing suppliers who adhere to military-grade manufacturing standards ensures durability and authenticity, which are essential for formal military occasions.
Key takeaways for successful procurement include:
- Compliance Assurance: Verify that suppliers meet exact military dress code requirements, including fabric types, colors, and authorized accessories.
- Customization Capability: Opt for vendors capable of tailoring uniforms to regional and rank-specific variations while maintaining global standards.
- Supplier Reliability: Choose partners with proven track records in delivering on time and providing after-sales support, especially for complex orders involving multiple uniform components.
- Cost Efficiency: Leverage bulk purchasing and long-term contracts to optimize costs without compromising quality.
Looking ahead, the army mess dress market is evolving with increasing demand for sustainable materials and enhanced comfort features. International buyers are encouraged to engage proactively with manufacturers who invest in innovation and uphold strict quality controls. Embracing strategic sourcing not only secures superior uniforms but also fosters partnerships that support military professionalism and ceremonial excellence worldwide.