Master Sourcing High-Quality Fuschia Dresses for Global B2B
Guide to Fuschia Dress
- Introduction: Navigating the Global Market for fuschia dress
- Understanding fuschia dress Types and Variations
- Key Industrial Applications of fuschia dress
- Strategic Material Selection Guide for fuschia dress
- In-depth Look: Manufacturing Processes and Quality Assurance for fuschia dress
- Comprehensive Cost and Pricing Analysis for fuschia dress Sourcing
- Spotlight on Potential fuschia dress Manufacturers and Suppliers
- Essential Technical Properties and Trade Terminology for fuschia dress
- Navigating Market Dynamics, Sourcing Trends, and Sustainability in the fuschia dress Sector
- Frequently Asked Questions (FAQs) for B2B Buyers of fuschia dress
- Strategic Sourcing Conclusion and Outlook for fuschia dress
Introduction: Navigating the Global Market for fuschia dress
In today’s fast-evolving global fashion landscape, the fuschia dress stands out as a vibrant, versatile garment that commands attention across diverse markets. For international B2B buyers—especially those operating in dynamic regions such as Africa, South America, the Middle East, and Europe—understanding the intricacies of sourcing and supplying fuschia dresses is crucial to capturing consumer demand and staying competitive. This garment’s bold color and varied styles offer tremendous opportunities but also present unique challenges in terms of quality, material selection, and supply chain agility.
This comprehensive guide equips buyers with actionable insights to confidently navigate the global fuschia dress market. It delves into the full spectrum of considerations, including the diverse types and styles of fuschia dresses favored in different regions, the impact of fabric choices on cost and consumer appeal, and the critical manufacturing and quality control processes that ensure product excellence. Additionally, the guide highlights how to identify reliable suppliers, optimize cost structures, and leverage market trends to anticipate demand shifts.
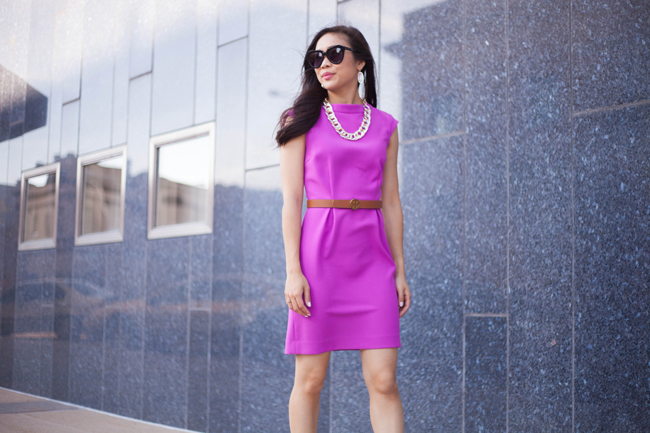
Illustrative Image (Source: Google Search)
By focusing on strategic sourcing tailored to markets like Nigeria, Saudi Arabia, Brazil, and key European hubs, this resource empowers buyers to make informed decisions that balance innovation, sustainability, and profitability. Whether negotiating minimum order quantities or assessing ethical compliance, readers will gain a clear roadmap to streamline procurement and build resilient partnerships. Ultimately, this guide is designed to help international buyers unlock the full potential of the fuschia dress category and thrive in a competitive, globalized fashion ecosystem.
Understanding fuschia dress Types and Variations
Type Name | Key Distinguishing Features | Primary B2B Applications | Brief Pros & Cons for Buyers |
---|---|---|---|
Evening Gown | Floor-length, elegant silhouette, often with embellishments | Luxury retail, formal event collections | High perceived value; requires careful sizing and quality control |
Casual Day Dress | Knee-length, relaxed fit, breathable fabrics | Mass market retail, seasonal casual wear lines | Versatile and high volume; lower margins, trend-sensitive |
Bodycon Dress | Tight-fitting, stretchy fabric, emphasizes silhouette | Clubwear, youth fashion segments | Popular in fast fashion; sizing precision critical |
Wrap Dress | Overlapping front panels, adjustable fit, versatile style | Multi-season collections, office wear | Flexible sizing; requires skilled pattern making |
Maxi Dress | Long flowing style, often lightweight materials | Resort wear, summer collections | Appeals to diverse markets; fabric sourcing impacts cost |
Evening Gown
Evening gowns in fuschia are characterized by their luxurious, floor-length designs often enhanced with embellishments like sequins or lace. These dresses target premium markets such as luxury boutiques and formal event retailers. For B2B buyers, quality control is paramount to maintain brand reputation, and precise sizing is essential given the tailored nature of these garments. Sourcing premium fabrics and skilled manufacturing partners ensures these gowns meet high-end consumer expectations.
Casual Day Dress
Casual day dresses in fuschia typically feature knee-length cuts and relaxed fits using breathable fabrics like cotton or viscose blends. These are well-suited for mass-market retailers focusing on seasonal casual wear. B2B buyers should emphasize scalability and supplier reliability to meet high volume demands. While margins may be thinner, versatility and trend adaptability make this type a staple in many regional markets including Africa and South America, where climate and comfort are key.
Bodycon Dress
The bodycon fuschia dress is a tight-fitting garment made from stretchy materials such as spandex blends, designed to accentuate body shape. This type is popular in youth and clubwear segments across urban markets in Europe and the Middle East. B2B buyers must focus on accurate sizing and fabric quality to prevent returns and ensure customer satisfaction. Fast fashion suppliers often favor this style due to its quick turnaround and trend-driven appeal.
Wrap Dress
Wrap dresses feature overlapping front panels that tie or button for an adjustable fit, making them highly versatile for multiple occasions. Their adaptability suits office wear and multi-season collections, appealing to professional markets in Europe and the Middle East. For B2B buyers, the challenge lies in ensuring pattern accuracy and skilled craftsmanship to deliver consistent fit and quality. This style supports moderate order volumes with good repeat purchase potential.
Maxi Dress
Maxi dresses in fuschia are long, flowing garments often crafted from lightweight fabrics such as chiffon or rayon, ideal for resort wear and summer collections. These dresses appeal to diverse international markets, especially in warm climates like Nigeria and Brazil. B2B buyers should consider fabric sourcing carefully, as material cost and availability significantly affect pricing. Additionally, supply chain agility is important to respond to seasonal demand peaks efficiently.
Related Video: Large Language Models (LLMs) – Everything You NEED To Know
Key Industrial Applications of fuschia dress
Industry/Sector | Specific Application of fuschia dress | Value/Benefit for the Business | Key Sourcing Considerations for this Application |
---|---|---|---|
Fashion Retail & Apparel | Seasonal and event-driven collections | Drives consumer engagement with vibrant, trendy colors | Quality of fabric dye, colorfastness, compliance with regional textile standards |
Hospitality & Events | Uniforms and staff attire for upscale venues | Enhances brand image and customer experience | Durable materials, ease of maintenance, cultural appropriateness |
Entertainment & Media | Costume design for performances and media shoots | Visual impact and audience engagement | Customization options, fabric comfort, rapid prototyping capability |
Luxury & Boutique Retail | Exclusive limited-edition dress lines | Creates exclusivity and appeals to high-end consumers | Fabric origin transparency, ethical sourcing, premium finishing |
Export & Wholesale | Bulk supply to international fashion markets | Cost-effective production with consistent quality | Reliable logistics, compliance with import/export regulations, MOQ flexibility |
Fashion Retail & Apparel
In the fast-paced fashion retail sector, fuschia dresses are often used in seasonal collections and event-specific lines to capture consumer attention with bold, vibrant colors. Retailers in regions like Europe and South America benefit from the color’s appeal during spring and summer seasons, driving sales and brand differentiation. B2B buyers must prioritize fabric dye quality and colorfastness to ensure garments maintain their vividness after multiple washes. Compliance with local textile standards, particularly in markets like the EU, is critical to avoid regulatory issues.
Hospitality & Events
Upscale hotels, restaurants, and event management companies frequently use fuschia dresses as uniforms or event staff attire to convey a sophisticated and energetic atmosphere. This application is particularly relevant in Middle Eastern and African luxury hospitality markets, where brand image and customer experience are paramount. Buyers should focus on sourcing durable, easy-to-maintain fabrics that withstand frequent use and laundering. Additionally, cultural sensitivity in design and color tone is essential to align with regional preferences and norms.
Entertainment & Media
Fuschia dresses play a key role in costume design for television, film, and live performances, providing striking visual appeal that enhances audience engagement. Production companies in Nigeria, Brazil, and Saudi Arabia often require rapid prototyping and customization to meet tight shooting schedules and creative demands. B2B buyers must ensure that manufacturers offer flexible design options, comfortable fabrics suitable for long wear, and efficient quality control to meet the high standards of media production.
Luxury & Boutique Retail
For luxury and boutique retailers, fuschia dresses are used in limited-edition collections that emphasize exclusivity and craftsmanship. High-end consumers in European and Middle Eastern markets seek garments made from premium fabrics with ethical sourcing credentials. B2B buyers should prioritize transparency in fabric origin, certifications such as GOTS for organic materials, and meticulous finishing techniques. These factors help build brand trust and justify premium pricing.
Export & Wholesale
Exporters and wholesalers rely on fuschia dresses as a popular SKU to supply diverse international markets, including Africa and South America. Bulk production must balance cost efficiency with consistent quality to meet the expectations of retailers across different regions. Key sourcing considerations include reliable logistics partners to navigate customs and import/export regulations, as well as flexible minimum order quantities to accommodate varying market demands. Ensuring product compliance with destination country standards reduces the risk of shipment delays or rejections.
Related Video: LABORATORY APPARATUS AND THEIR USES
Strategic Material Selection Guide for fuschia dress
When selecting materials for manufacturing fuschia dresses, international B2B buyers must carefully evaluate fabric options that balance aesthetics, durability, cost, and regional market preferences. This guide analyzes four common materials—Polyester, Cotton, Viscose, and Silk—providing actionable insights tailored for buyers from Africa, South America, the Middle East, and Europe.
Polyester
Key Properties:
Polyester is a synthetic fiber known for its high tensile strength, wrinkle resistance, and excellent color retention, making it ideal for vibrant hues like fuschia. It exhibits good resistance to shrinking and stretching, and it performs well under a wide range of temperatures, though it is less breathable than natural fibers.
Pros & Cons:
Polyester is highly durable and cost-effective, enabling mass production with relatively low manufacturing complexity. It resists mildew and abrasion, which is beneficial for humid climates. However, it can feel less comfortable in hot environments due to poor moisture absorption and may have lower perceived luxury compared to natural fabrics.
Impact on Application:
Polyester’s ability to hold bright colors without fading makes it suitable for fast fashion and high-volume retail markets. Its quick-drying nature supports easy care, a key selling point in regions with limited laundry infrastructure.
Considerations for International Buyers:
Buyers in hot climates such as Nigeria and Saudi Arabia should consider blends (e.g., polyester-cotton) to improve breathability. Compliance with standards like OEKO-TEX and REACH ensures chemical safety, which is increasingly demanded in European markets. Import duties and local textile regulations vary, so sourcing from suppliers with transparent certifications is critical.
Cotton
Key Properties:
Cotton is a natural fiber prized for its breathability, softness, and moisture-wicking properties. It is comfortable in warm climates and hypoallergenic, making it a preferred choice for everyday wear.
Pros & Cons:
Cotton offers excellent comfort and dye uptake, resulting in vibrant fuschia shades. It is biodegradable and aligns with sustainability trends. However, it wrinkles easily, may shrink if not pre-treated, and generally costs more than synthetic fibers. Manufacturing complexity increases with organic or premium cotton grades.
Impact on Application:
Cotton dresses are favored in markets prioritizing comfort and sustainability, such as Europe and parts of South America. Its natural feel appeals to consumers in warmer African regions, though care instructions must be clear to avoid shrinkage.
Considerations for International Buyers:
Buyers should verify certifications like GOTS (Global Organic Textile Standard) for organic cotton and ensure compliance with ASTM or ISO standards for fabric quality. Cotton sourcing from countries with reliable supply chains (e.g., India, Egypt) can reduce lead times. Import tariffs and seasonal demand fluctuations must be factored into procurement planning.
Viscose (Rayon)
Key Properties:
Viscose is a semi-synthetic fiber made from regenerated cellulose. It drapes well, has a silky appearance, and absorbs dyes effectively, producing rich fuschia tones. It is breathable but less durable than polyester or cotton.
Pros & Cons:
Viscose offers a luxurious feel at a moderate cost, bridging synthetic and natural fiber advantages. However, it wrinkles easily, can shrink, and may lose strength when wet. Manufacturing requires careful handling to maintain fabric integrity, increasing production complexity.
Impact on Application:
Viscose is well-suited for mid-range fashion segments where aesthetic appeal and comfort are priorities. Its softness makes it attractive in European and Middle Eastern markets, but durability concerns may limit its use in high-wear environments.
Considerations for International Buyers:
Buyers should assess supplier adherence to environmental standards due to viscose’s chemical-intensive production. Certifications like FSC (Forest Stewardship Council) for raw materials and compliance with REACH regulations are important for European importers. In tropical climates, viscose’s moisture sensitivity requires clear consumer care guidelines.
Silk
Key Properties:
Silk is a natural protein fiber renowned for its sheen, softness, and excellent drape. It maintains vibrant colors and has natural temperature-regulating properties, keeping wearers cool in heat and warm in cold.
Pros & Cons:
Silk conveys luxury and exclusivity, justifying higher price points. It is lightweight and hypoallergenic but delicate, requiring specialized manufacturing and care. Production complexity is high, and costs are significantly greater than other fibers.
Impact on Application:
Ideal for premium fuschia dress collections targeting affluent markets in Europe and the Middle East. Its natural elegance supports brand differentiation but limits scalability due to cost and care requirements.
Considerations for International Buyers:
Buyers must ensure silk sourcing complies with ethical standards, including fair labor practices and animal welfare. Certifications like Silk Mark or Oeko-Tex Standard 100 add credibility. Import regulations and tariffs vary widely; partnering with experienced suppliers can mitigate risks related to quality and delivery timelines.
Material | Typical Use Case for fuschia dress | Key Advantage | Key Disadvantage/Limitation | Relative Cost (Low/Med/High) |
---|---|---|---|---|
Polyester | Mass-market, fast fashion, vibrant color retention | Durable, cost-effective, colorfast | Less breathable, lower comfort in heat | Low |
Cotton | Everyday wear, sustainable fashion, warm climates | Comfortable, breathable, sustainable | Wrinkles, potential shrinkage | Medium |
Viscose | Mid-range fashion, drape-focused, soft hand feel | Luxurious feel, good dye uptake | Wrinkles, less durable, moisture sensitive | Medium |
Silk | Premium collections, luxury market, elegant drape | Natural sheen, temperature regulating | High cost, delicate, complex care | High |
In-depth Look: Manufacturing Processes and Quality Assurance for fuschia dress
The manufacturing and quality assurance of a fuschia dress involve a series of meticulously planned and executed stages, each critical to delivering a product that meets international standards and buyer expectations. For B2B buyers across Africa, South America, the Middle East, and Europe, understanding these processes provides a foundation for selecting reliable suppliers and ensuring consistent product quality.
Manufacturing Process for Fuschia Dress
The production of a fuschia dress typically follows four main stages: material preparation, forming, assembly, and finishing. Each phase incorporates specific techniques and considerations tailored to the garment’s style, fabric, and target market.
1. Material Preparation
Material preparation is the cornerstone of quality garment production. For a fuschia dress, the choice of fabric—often cotton blends, silk, polyester, or sustainable alternatives like Tencel—affects the entire manufacturing cycle.
- Fabric inspection and testing: Incoming fabrics undergo checks for colorfastness, shrinkage, and tensile strength. This step ensures that the vibrant fuschia color is consistent and durable.
- Cutting preparation: Fabrics are spread in multiple layers to optimize yield and reduce waste. Digital cutting machines or traditional hand-cutting methods may be used depending on order size.
- Trims and accessories sourcing: Zippers, buttons, linings, and labels are sourced and verified for color matching and durability.
2. Forming
Forming involves shaping fabric pieces into the components of the dress.
- Cutting: Precision cutting is crucial for maintaining pattern alignment and fabric grain, especially with bold colors like fuschia where imperfections are noticeable.
- Dyeing (if applicable): Some manufacturers dye fabric post-cutting to achieve specific shades or effects. However, pre-dyed fabric is preferred for color consistency.
- Embroidery or embellishments: If the design includes decorative elements, these are added at this stage using automated or hand techniques.
3. Assembly
The assembly stage transforms cut components into a finished garment.
- Sewing: Skilled operators use industrial sewing machines to join panels, attach sleeves, collars, and hems. Overlock stitching is common for seam durability.
- Fusing and pressing: Interlinings and facings are fused for structure. Pressing ensures crisp seams and professional appearance.
- In-line inspection: Operators or supervisors conduct visual and tactile checks during assembly to detect defects early.
4. Finishing
Finishing elevates the dress to retail-ready status.
- Final quality checks: Wrinkles, loose threads, color consistency, and fit are evaluated.
- Labeling and tagging: Care labels and branding tags are affixed as per buyer specifications.
- Packaging: Garments are folded or hung, then packed with protective materials to prevent damage during transit.
Quality Assurance (QA) and Control (QC) Protocols
Quality assurance in fuschia dress manufacturing is governed by a combination of international standards and industry-specific requirements. Effective QC protocols help mitigate risks, reduce returns, and enhance brand reputation.
Relevant International and Industry Standards
- ISO 9001: The globally recognized quality management standard emphasizes process control, continual improvement, and customer satisfaction. Suppliers certified to ISO 9001 demonstrate robust quality systems.
- OEKO-TEX Standard 100: Ensures textiles are free from harmful substances, increasingly important for international buyers focused on consumer safety.
- REACH Compliance: Pertinent for European buyers, this regulation restricts hazardous chemicals in textiles.
- Country-specific certifications: Buyers from regions like the Middle East or Africa should verify compliance with local import regulations and textile standards, such as SASO in Saudi Arabia or SONCAP in Nigeria.
Key QC Checkpoints
Quality control is typically segmented into three critical checkpoints to maintain consistency throughout production:
- Incoming Quality Control (IQC): Inspection of raw materials and trims before entering production. IQC verifies fabric quality, color accuracy (especially vital for fuschia hues), and accessory compliance.
- In-Process Quality Control (IPQC): Continuous monitoring during sewing and assembly phases. IPQC detects stitching defects, seam strength issues, and color mismatches early to avoid compounding errors.
- Final Quality Control (FQC): A comprehensive evaluation of finished garments, including visual inspection, measurements, and functional testing (e.g., zipper operation, button security).
Common Testing Methods
B2B buyers should expect suppliers to conduct or provide documentation on the following tests:
- Colorfastness Tests: Assess resistance to washing, rubbing, and light exposure to ensure the fuschia color remains vibrant.
- Dimensional Stability: Measures shrinkage after laundering, crucial for maintaining dress fit.
- Tensile and Seam Strength: Ensures durability during wear.
- Chemical Tests: Confirm absence of harmful dyes or substances per OEKO-TEX or REACH.
Verifying Supplier Quality Control: Best Practices for B2B Buyers
For international buyers, particularly from emerging and established markets, verifying a supplier’s QC capabilities is essential to mitigate risks and build long-term partnerships.
- Factory Audits: Conduct or commission third-party audits to assess production capabilities, QC procedures, and compliance with labor and environmental standards.
- Quality Reports and Certifications: Request detailed inspection reports, test certificates, and ISO/OEKO-TEX certificates as evidence of quality adherence.
- Third-Party Inspections: Engage independent inspection agencies to perform random checks during production and pre-shipment, providing unbiased verification.
- Sample Approvals: Insist on pre-production and pre-shipment sample approvals to confirm color accuracy, fit, and finish.
- Digital Traceability: Leverage suppliers using digital tools for real-time quality monitoring and supply chain transparency.
QC and Certification Nuances for International Buyers
- Africa (e.g., Nigeria): Regulatory frameworks like SONCAP require conformity assessments. Buyers should ensure suppliers can provide necessary documentation for customs clearance. Local testing labs may be limited; hence, reliance on internationally accredited labs and third-party inspections is common.
- Middle East (e.g., Saudi Arabia): SASO certification and GSO standards emphasize product safety and labeling. Buyers should verify that suppliers understand regional compliance and can manage certification logistics.
- South America: Importers often demand compliance with both international and local standards. Sustainability credentials and chemical safety are increasingly scrutinized.
- Europe: Stringent REACH and GDPR-related data handling standards necessitate suppliers with advanced compliance systems. Buyers may prioritize suppliers with transparent supply chains and certifications like ISO 14001 (environmental management).
Conclusion
For B2B buyers sourcing fuschia dresses internationally, a deep understanding of manufacturing processes and quality assurance is paramount. From precise material preparation to rigorous final inspections, each stage influences the garment’s market success. Verifying supplier quality through audits, certifications, and independent inspections safeguards investments and ensures product excellence. Tailoring QC expectations to regional regulatory landscapes further empowers buyers to navigate complexities and build resilient, compliant supply chains.
Related Video: Garments Full Production Process | Order receive to Ex-Factory | Episode 2
Comprehensive Cost and Pricing Analysis for fuschia dress Sourcing
Understanding the cost and pricing landscape for sourcing fuschia dresses is crucial for international B2B buyers seeking to optimize procurement strategies while ensuring quality and timely delivery. The pricing structure is influenced by multiple cost components and market variables that vary depending on sourcing regions and buyer requirements.
Key Cost Components in Fuschia Dress Sourcing
-
Materials: Fabric choice is the largest cost driver. Premium materials such as organic cotton, viscose blends, or sustainable fabrics often come with higher unit costs but appeal to conscious consumers. The vibrancy and dyeing process of fuschia fabric, especially if using eco-friendly dyes, can also add to material expenses.
-
Labor: Labor costs fluctuate widely by manufacturing location. Countries like India, Bangladesh, and some parts of Southeast Asia offer competitive labor rates, whereas Europe and the Middle East may incur higher wages. Labor-intensive processes such as intricate stitching or embellishments increase the labor component.
-
Manufacturing Overhead: This includes factory utilities, machinery depreciation, and indirect labor. Efficient factories with advanced automation reduce overhead per unit. Overhead costs also cover compliance with ethical labor standards and environmental regulations, which have become integral to modern sourcing.
-
Tooling and Setup: Initial costs to create molds, patterns, and production setups impact the per-unit price, especially for new designs or smaller orders. These fixed costs dilute as order volumes increase.
-
Quality Control (QC): Rigorous QC protocols—covering fabric inspection, stitching, color fastness, and fit—add to costs but reduce returns and bolster brand reputation. International buyers should prioritize suppliers with documented QC procedures.
-
Logistics and Duties: Freight charges, customs duties, and local taxes significantly affect landed costs. Air freight is faster but costlier than sea freight. Duty rates vary by country and trade agreements; understanding Incoterms is essential to clarify cost responsibilities.
-
Supplier Margin: Suppliers price to cover costs and earn profit margins, typically ranging from 10% to 30%, depending on market positioning and volume.
Influencing Factors on Pricing
-
Order Volume and Minimum Order Quantities (MOQs): Larger volumes typically secure lower unit prices due to economies of scale and amortized tooling costs. Buyers from emerging markets should negotiate MOQs aligned with their sales forecasts to avoid excess inventory.
-
Product Specifications and Customization: Unique design elements, fabric blends, or special finishes increase costs. Customized packaging or private labeling also adds to pricing.
-
Material Quality and Certifications: Certifications such as GOTS organic or OEKO-TEX increase raw material costs but enhance marketability in regions with growing demand for sustainable fashion, including Europe and parts of the Middle East.
-
Supplier Reliability and Capacity: Established suppliers with proven track records may charge premiums for reliability and on-time delivery. Startups or less experienced manufacturers may offer lower prices but pose risks.
-
Incoterms Selection: Terms like FOB (Free on Board), CIF (Cost, Insurance, Freight), or DDP (Delivered Duty Paid) affect how costs and risks are split between buyer and seller. Buyers in Africa, South America, or the Middle East should clarify Incoterms to avoid unexpected charges.
Actionable Tips for International B2B Buyers
-
Negotiate Beyond Price: Engage suppliers on lead times, payment terms, and quality guarantees. Volume discounts and long-term contracts can unlock better pricing.
-
Calculate Total Cost of Ownership (TCO): Include logistics, customs, warehousing, and potential returns in your budgeting. A lower unit price may result in higher overall costs if quality issues or delays occur.
-
Leverage Technology and Transparency: Request digital samples, production tracking, and real-time inventory updates to minimize risks and improve decision-making.
-
Consider Local Regulations and Import Duties: For buyers in Nigeria, Saudi Arabia, or Brazil, understanding local import taxes and compliance requirements is vital to avoid penalties and delays.
-
Balance Cost and Sustainability: Increasingly, buyers in Europe and the Middle East prioritize ethical sourcing. Investing in certified sustainable materials may command premium prices but support brand differentiation and customer loyalty.
-
Assess MOQ Flexibility: Work with suppliers who offer scalable MOQs to match fluctuating demand, reducing inventory holding costs.
Indicative Pricing Disclaimer
Pricing for fuschia dresses varies widely depending on fabric selection, production complexity, order volume, and shipping method. For example, a basic cotton fuschia dress sourced from South Asia might start around $8–$12 per unit at large volumes, while a premium organic cotton or custom design with sustainable certification could range from $15–$25 or more. Logistics, duties, and customization will further influence final landed costs. Buyers should request detailed quotations and conduct due diligence to obtain accurate pricing reflective of their unique sourcing requirements.
By carefully analyzing these cost elements and pricing influencers, international B2B buyers from Africa, South America, the Middle East, and Europe can make informed decisions that optimize procurement efficiency, reduce risk, and enhance profitability in the competitive fuschia dress market.
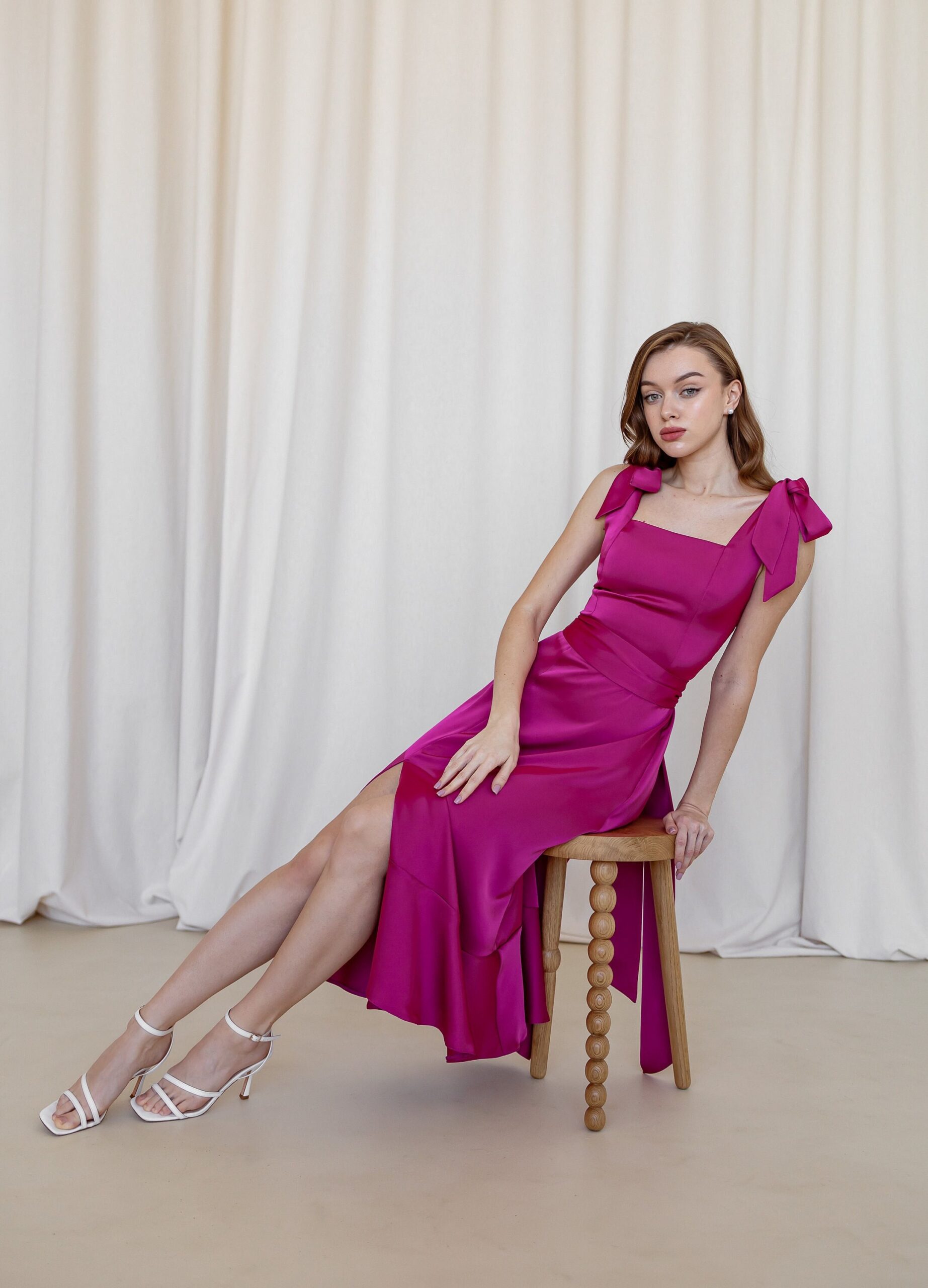
Illustrative Image (Source: Google Search)
Spotlight on Potential fuschia dress Manufacturers and Suppliers
This section offers a look at a few manufacturers active in the ‘fuschia dress’ market. This is a representative sample for illustrative purposes; B2B buyers must conduct their own extensive due diligence before any engagement. Information is synthesized from public sources and general industry knowledge.
Essential Technical Properties and Trade Terminology for fuschia dress
Key Technical Properties of a Fuschia Dress for B2B Buyers
When sourcing fuschia dresses for international markets, understanding the critical technical specifications ensures product quality, compliance, and customer satisfaction. Below are essential properties that buyers should prioritize:
-
Fabric Composition and Grade
The fabric type (e.g., 100% cotton, polyester blend, viscose) directly influences the dress’s appearance, durability, and comfort. Grade refers to fabric quality standards, such as GSM (grams per square meter), indicating thickness and weight. High-grade fabrics with consistent color fastness are vital for premium appeal and longevity, particularly in climates like those in Africa and the Middle East where durability and breathability matter. -
Color Fastness and Shade Consistency
Fuschia is a bright, eye-catching hue that must maintain vibrancy through washing and exposure to sunlight. Color fastness ratings (e.g., ISO 105 standards) measure resistance to fading. Consistent shade matching across batches is critical for brand uniformity, especially when ordering large quantities or repeat shipments. -
Sizing Tolerance and Fit Specifications
Precise garment measurements with clear tolerance levels (e.g., ±1 cm) ensure consistency and reduce return rates. Standardized sizing charts adapted to target regions (e.g., European vs. African sizing norms) help meet end-consumer expectations and minimize fit-related complaints. -
Stitching and Seam Strength
The durability of seams is measured by stitch density and thread quality. High stitch per inch (SPI) counts and reinforced seams are important for dresses that undergo frequent wear. This technical property directly impacts product lifespan and brand reputation. -
Finish and Embellishment Details
Surface finishes such as anti-wrinkle treatment, water repellency, or softeners enhance garment functionality. Embellishments (like sequins or lace) require clear specification on attachment methods to ensure durability and safety during transit. -
Compliance with Safety and Environmental Standards
Certifications such as OEKO-TEX Standard 100 or GOTS organic certification indicate non-toxic, environmentally responsible production. These credentials are increasingly important for buyers in Europe and South America who prioritize sustainable sourcing.
Common Trade Terminology for International Fashion Sourcing
Understanding key trade terms empowers buyers to negotiate effectively and manage supply chains with confidence:
-
OEM (Original Equipment Manufacturer)
Refers to manufacturers who produce garments designed and branded by the buyer. OEM partnerships allow customization and control over design, quality, and branding, essential for private labels seeking unique fuschia dresses. -
MOQ (Minimum Order Quantity)
The smallest number of units a supplier is willing to produce in a single order. Buyers must balance MOQs with inventory capacity and market demand. Lower MOQs offer flexibility for emerging markets, while larger MOQs may reduce unit costs. -
RFQ (Request for Quotation)
A formal inquiry sent to suppliers asking for detailed pricing, production timelines, and terms. A well-prepared RFQ enables buyers to compare offers transparently and select the best manufacturing partner. -
Incoterms (International Commercial Terms)
Standardized trade terms that define responsibilities between buyers and sellers for shipping, insurance, and customs clearance. Common terms include FOB (Free on Board) and CIF (Cost, Insurance, Freight). Knowing Incoterms helps buyers from regions like Nigeria or Saudi Arabia manage costs and logistics effectively. -
Lead Time
The total time from order placement to product delivery. Fast lead times are crucial in fashion to capitalize on trends and seasonal demand. Buyers should confirm lead times upfront to align supply with market windows. -
Tech Pack
A detailed document containing technical drawings, measurements, materials, and construction instructions. Supplying an accurate tech pack reduces errors and speeds up production, ensuring the fuschia dress meets exact specifications.
By mastering these technical properties and trade terms, international B2B buyers can optimize procurement strategies, ensure product quality, and build reliable supplier relationships tailored to their regional markets.
Navigating Market Dynamics, Sourcing Trends, and Sustainability in the fuschia dress Sector
Market Overview & Key Trends in the Fuschia Dress Sector
The global market for fuschia dresses is shaped by vibrant consumer demand for bold, statement-making apparel that blends cultural influences with contemporary fashion. This demand is particularly strong in regions such as Africa, South America, the Middle East, and Europe, where fuschia is often associated with celebration, luxury, and modern femininity. For B2B buyers in countries like Nigeria and Saudi Arabia, sourcing fuschia dresses means tapping into a growing appetite for vivid color palettes that cater to festive occasions, professional wardrobes, and everyday fashion.
Key market drivers include:
- Cultural and Seasonal Demand: Festivals, weddings, and cultural events in target regions fuel cyclical spikes in demand for colorful dresses, with fuschia standing out due to its eye-catching appeal.
- Fast Fashion and Agile Supply Chains: Buyers increasingly prefer suppliers who can rapidly respond to trend shifts with flexible production runs and quick turnaround times.
- Digital Integration: Supply chain visibility tools, AI-driven demand forecasting, and e-commerce platforms are vital for managing inventory and reaching diverse markets efficiently.
- Customization and Niche Segmentation: There is growing interest in personalized designs and fabric blends that cater to regional climates and style preferences.
- Emerging Material Innovations: Sustainable and performance fabrics, such as organic cotton blends and moisture-wicking textiles, are gaining traction among buyers aiming to differentiate their offerings.
For B2B buyers, understanding these dynamics is crucial to selecting partners who combine trend sensitivity with operational excellence. Suppliers located in Asia and Europe often offer competitive pricing and advanced manufacturing capabilities, while African and Middle Eastern markets emphasize authenticity and cultural resonance in design.
Sustainability & Ethical Sourcing in B2B for Fuschia Dresses
Sustainability is no longer optional in fashion sourcing; it is a strategic imperative. The production of fuschia dresses, like other apparel, impacts water usage, chemical consumption, and carbon emissions. Buyers focusing on sustainability can leverage several approaches to minimize environmental footprints while meeting consumer expectations.
Environmental considerations include:
- Eco-friendly Fabrics: Organic cotton, Tencel, hemp, and recycled polyester reduce water usage and pollution. For fuschia dresses, sourcing GOTS-certified organic cotton or low-impact dyed fabrics ensures vibrant colors without harsh chemicals.
- Dyeing and Finishing: The fuschia shade requires careful dye selection. Low-impact, azo-free dyes and digital printing technologies reduce toxic runoff and energy consumption.
- Circularity and Waste Reduction: Partnering with manufacturers employing zero-waste pattern making or 3D knitting can significantly cut fabric waste during production.
Ethical sourcing factors critical to B2B buyers:
- Fair Labor Practices: Transparent supply chains that uphold worker rights, fair wages, and safe working conditions are essential for brand reputation and compliance with global standards.
- Certifications: Buyers should prioritize suppliers with certifications such as Fair Trade, OEKO-TEX Standard 100, and the Global Organic Textile Standard (GOTS) to validate ethical and sustainable claims.
- Traceability: Technologies like blockchain or supply chain management platforms provide end-to-end visibility, allowing buyers to verify the provenance of materials and production processes.
By integrating sustainability and ethical sourcing into their procurement strategies, B2B buyers not only mitigate risks but also align with increasingly conscious end consumers across their markets.
Brief Evolution of the Fuschia Dress in B2B Context
The prominence of the fuschia dress in global fashion reflects a broader evolution of color trends and fabric technology. Historically, fuschia, named after the 19th-century botanist Fuchsia, gained popularity in the mid-20th century as synthetic dyes became more accessible, enabling vibrant, long-lasting hues. Initially a niche choice, the color has surged in mainstream fashion thanks to its versatility and boldness.
In the B2B landscape, the fuschia dress has transitioned from a seasonal novelty to a staple in collections targeting diverse markets. This shift has been supported by advances in textile manufacturing, including improved dye fastness and sustainable fabric alternatives. Today, sourcing fuschia dresses involves balancing aesthetic appeal with supply chain agility and environmental responsibility, making it a compelling category for forward-thinking international buyers.
Related Video: International Trade Explained
Frequently Asked Questions (FAQs) for B2B Buyers of fuschia dress
-
How can I effectively vet suppliers of fuschia dresses to ensure reliability and quality?
To vet suppliers, start by verifying their business licenses and certifications related to ethical sourcing and quality management (e.g., ISO, GOTS for organic fabrics). Request detailed product samples to assess fabric quality, colorfastness, and workmanship. Check references or reviews from other international buyers, especially those in similar markets like Africa or the Middle East. Evaluate their communication responsiveness and transparency about production capabilities and lead times. Finally, consider visiting manufacturing sites or using third-party inspection services to confirm compliance with labor and environmental standards. -
Is it possible to customize fuschia dresses for different markets, and how should I approach this?
Yes, customization is feasible and often essential to cater to diverse regional preferences in Africa, South America, the Middle East, and Europe. Discuss options for fabric types, dress styles, sizes, and embellishments with your supplier upfront. Confirm their minimum order quantities (MOQs) for custom designs and request prototypes or samples before mass production. Leveraging 3D design tools or digital prototyping can speed up approvals and reduce errors. Always ensure that customization aligns with local cultural norms and consumer trends to maximize market acceptance. -
What are typical MOQs and lead times for ordering fuschia dresses from international manufacturers?
MOQs vary widely depending on the supplier and production method, but for fuschia dresses, expect minimum orders typically between 200 to 1000 units per style or size. Lead times generally range from 30 to 90 days, influenced by factors such as fabric sourcing, production complexity, and shipment logistics. Fast fashion suppliers may offer shorter lead times but at higher costs. To manage inventory risks, negotiate flexible MOQs or phased deliveries and confirm production schedules and shipping timelines to align with your market launch plans. -
What payment terms are common in international B2B transactions for fuschia dresses, especially with buyers from Africa and the Middle East?
Common payment terms include a 30-50% upfront deposit with the balance paid upon shipment or delivery. Letters of credit (LC) or escrow services offer secure transaction methods, reducing risks for both parties. For buyers in Africa and the Middle East, working with suppliers that accept multiple payment methods (wire transfers, PayPal, or trade finance instruments) helps ease currency and banking restrictions. Always negotiate clear payment schedules and penalties for late payments, and confirm that payment terms comply with both countries’ trade regulations. -
How can I ensure quality assurance and obtain necessary certifications for fuschia dresses?
Quality assurance begins with clear product specifications and standards agreed upon before production. Request detailed quality control (QC) plans from your supplier, including fabric testing, color matching, stitching, and safety compliance. Use third-party inspection agencies to conduct pre-shipment audits, especially for large orders. Certifications such as OEKO-TEX, GOTS (for organic fabrics), and fair labor compliance are valuable for market trust and regulatory compliance in Europe and other regions. Insist on documentation for all certifications and test reports to validate product claims.
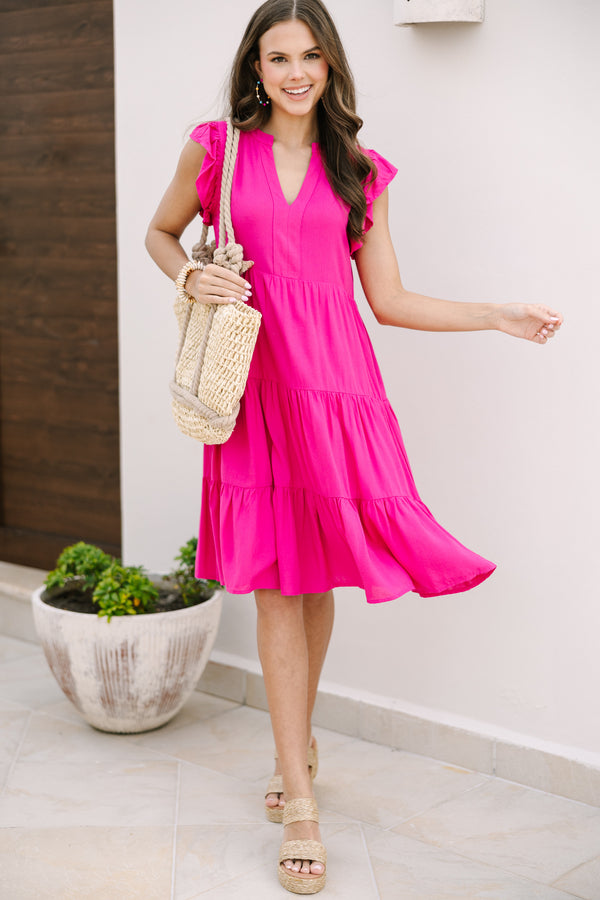
Illustrative Image (Source: Google Search)
-
What logistics considerations should I keep in mind when importing fuschia dresses internationally?
Plan logistics by assessing the most cost-effective and reliable shipping routes to your region, balancing speed and cost. Sea freight is economical for large shipments but requires longer lead times, while air freight offers speed at a premium. Confirm that your supplier can provide proper packaging to protect the vibrant fuschia color from fading or damage. Be aware of import duties, taxes, and customs clearance procedures specific to your country. Partner with experienced freight forwarders familiar with your market to navigate documentation, compliance, and last-mile delivery efficiently. -
How should I handle disputes or quality issues with overseas suppliers of fuschia dresses?
Establish clear contract terms covering product specifications, delivery timelines, and dispute resolution mechanisms before ordering. In case of quality issues, document problems with photos and reports, then communicate promptly with the supplier for resolution options such as replacements, discounts, or refunds. Use third-party mediation or arbitration if direct negotiation fails. Maintain open, professional communication to preserve relationships. To minimize disputes, implement regular quality checks during production and engage inspection services at critical milestones. -
Are there specific trade regulations or compliance issues I should be aware of when importing fuschia dresses?
Yes, regulations vary by region but often include import tariffs, labeling requirements, and product safety standards. For example, the European Union enforces strict chemical and textile labeling laws (REACH compliance), while Middle Eastern countries may require halal certification or specific modesty standards. Africa’s regional trade agreements, like the AfCFTA, can affect tariffs and customs duties. Work with customs brokers and legal experts to ensure compliance with local regulations, and request that suppliers provide all necessary certificates and declarations to avoid shipment delays or penalties.
Strategic Sourcing Conclusion and Outlook for fuschia dress
In the dynamic market for fuschia dresses, strategic sourcing remains the cornerstone of competitive advantage. International buyers from regions such as Africa, South America, the Middle East, and Europe must prioritize partnerships with suppliers who demonstrate reliability, ethical standards, and agility in adapting to fashion trends. Leveraging suppliers who integrate sustainable materials and innovative production methods can not only enhance product appeal but also align with growing consumer demand for responsible fashion.
Key takeaways for B2B buyers include the importance of end-to-end supply chain visibility, enabling timely decision-making and minimizing risks associated with delays or quality lapses. Embracing digital tools and predictive analytics will further optimize inventory management and streamline order fulfillment, crucial for maintaining responsiveness in fast-changing markets. Additionally, understanding regional trade regulations and logistics complexities will help mitigate costs and ensure smooth cross-border operations.
Looking ahead, the fuschia dress segment is poised for growth fueled by rising demand for vibrant, versatile apparel. Buyers are encouraged to cultivate long-term supplier relationships grounded in transparency and innovation to future-proof their sourcing strategies. By doing so, businesses can confidently meet evolving market needs while driving sustainable profitability across diverse international markets. Now is the time to act decisively—partner strategically and embrace supply chain excellence to capture emerging opportunities in this vibrant fashion category.