Your Ultimate Guide to Sourcing Pink Slip Dress
Guide to Pink Slip Dress
- Introduction: Navigating the Global Market for pink slip dress
- Understanding pink slip dress Types and Variations
- Key Industrial Applications of pink slip dress
- Strategic Material Selection Guide for pink slip dress
- In-depth Look: Manufacturing Processes and Quality Assurance for pink slip dress
- Comprehensive Cost and Pricing Analysis for pink slip dress Sourcing
- Spotlight on Potential pink slip dress Manufacturers and Suppliers
- Essential Technical Properties and Trade Terminology for pink slip dress
- Navigating Market Dynamics, Sourcing Trends, and Sustainability in the pink slip dress Sector
- Frequently Asked Questions (FAQs) for B2B Buyers of pink slip dress
- Strategic Sourcing Conclusion and Outlook for pink slip dress
Introduction: Navigating the Global Market for pink slip dress
The global demand for pink slip dresses has surged as fashion markets increasingly embrace versatile, elegant, and comfortable apparel that appeals across diverse demographics. For international B2B buyers, particularly those operating in dynamic regions like Africa, South America, the Middle East, and Europe—including fashion hubs such as Indonesia and France—understanding the nuances of sourcing pink slip dresses is crucial to capturing market share and meeting consumer expectations.
This guide delivers a comprehensive roadmap to mastering the complexities of the pink slip dress supply chain. It covers the spectrum of product types, from minimalist satin slips to intricate lace-trimmed variations, and highlights key material considerations including fabric quality, sustainability, and regional preferences. Buyers will gain insights into manufacturing processes, quality control protocols, and best practices for supplier vetting—essential for minimizing risk and ensuring product excellence.
Additionally, the guide explores cost structures and pricing strategies relevant to international trade, helping buyers optimize margins without compromising quality. Market trends and consumer behavior analysis equip readers to anticipate shifts and adapt their sourcing strategies accordingly. An FAQ section addresses common challenges such as compliance, logistics, and customization options, providing actionable solutions tailored for diverse international contexts.
By integrating these critical components, this guide empowers B2B buyers to make informed, strategic sourcing decisions for pink slip dresses—enhancing competitiveness and driving sustainable growth in a rapidly evolving global fashion landscape.
Understanding pink slip dress Types and Variations
Type Name | Key Distinguishing Features | Primary B2B Applications | Brief Pros & Cons for Buyers |
---|---|---|---|
Classic Satin Slip | Smooth satin fabric, bias-cut for drape, spaghetti straps | Wholesale fashion retailers, boutiques | + Luxurious feel and appearance – Requires careful handling and storage to avoid snags |
Lace-Trimmed Slip | Satin or silk base with delicate lace edging | Premium lingerie and eveningwear suppliers | + Adds elegance and appeal – Higher production cost and delicate maintenance |
Floral Print Slip | Lightweight fabric with floral patterns | Fast fashion, seasonal collections | + Trend-driven, versatile for casual or semi-formal – Print quality consistency can vary |
Midi-Length Slip | Falls mid-calf, often in silk or satin | Department stores, upscale fashion brands | + Popular length for diverse markets – May require size customization for regional fit preferences |
Plus Size Slip | Extended sizing with supportive cuts | Inclusive fashion lines, specialty retailers | + Expands market reach – Sourcing quality plus size materials can be challenging |
Classic Satin Slip
The Classic Satin Slip dress is characterized by its smooth satin fabric and bias-cut design that ensures a flattering drape. Its minimalist spaghetti straps make it a versatile staple in many wardrobes. For B2B buyers, this type is ideal for retailers focusing on timeless and elegant apparel. However, satin requires delicate handling during manufacturing and shipping to avoid damage, which is a critical consideration when ordering in bulk for international markets like Europe and the Middle East.
Lace-Trimmed Slip
Incorporating lace trims on satin or silk bases, the Lace-Trimmed Slip adds sophistication suitable for premium lingerie and eveningwear markets. This variant appeals to buyers targeting niche luxury segments across regions such as France and upscale Middle Eastern markets. While it commands a higher price point, the craftsmanship involved and delicate maintenance requirements mean buyers must ensure suppliers maintain high quality and traceability standards to meet consumer expectations.
Floral Print Slip
Floral Print Slips use lightweight fabrics adorned with vibrant patterns, catering to fast fashion and seasonal collections. This type resonates well with younger demographics and markets in South America and Africa where bold prints are popular. Buyers should prioritize suppliers with reliable print consistency and colorfastness to avoid post-sale returns. Its versatility allows blending casual and semi-formal styles, increasing appeal for multi-channel retail strategies.
Midi-Length Slip
Midi-Length Slips, typically made from silk or satin, extend to mid-calf, offering a balance between elegance and practicality. This length is favored in European and Middle Eastern markets where modesty and style intersect. B2B buyers should consider regional sizing preferences and potential customization to optimize fit. This type suits department stores and upscale brands seeking to diversify their slip dress offerings.
Plus Size Slip
Designed with extended sizing and supportive cuts, Plus Size Slips address the growing demand for inclusive fashion lines. This segment is crucial for specialty retailers and brands focusing on body positivity, particularly in diverse markets like Africa and South America. Sourcing quality plus size materials and ensuring consistent fit standards are key challenges for buyers, requiring thorough supplier vetting and due diligence to maintain brand reputation and customer satisfaction.
Related Video: Large Language Models (LLMs) – Everything You NEED To Know
Key Industrial Applications of pink slip dress
Industry/Sector | Specific Application of pink slip dress | Value/Benefit for the Business | Key Sourcing Considerations for this Application |
---|---|---|---|
Fashion Retail & Wholesale | Seasonal and trend-responsive product lines | Drives sales growth with trendy, versatile apparel | Fabric quality, colorfastness, sizing accuracy, ethical manufacturing |
Hospitality & Events | Uniforms and event staff attire | Enhances brand image with stylish, comfortable wear | Durability, comfort, ease of care, custom branding options |
E-commerce & Dropshipping | Fast-moving inventory for online fashion platforms | Enables quick turnaround and broad market appeal | Flexible MOQ, reliable supply chain, packaging, shipping logistics |
Boutique & Specialty Stores | Curated collections targeting niche markets | Differentiates product offerings with unique styles | Limited edition styles, material sourcing transparency, exclusivity |
Export & International Trade | Bulk supply for global fashion markets | Expands market reach with culturally adaptable designs | Compliance with international standards, tariff considerations, traceability |
Fashion Retail & Wholesale
In the fashion retail sector, pink slip dresses serve as essential seasonal staples that cater to evolving consumer preferences. Retailers in Africa, South America, the Middle East, and Europe benefit from sourcing high-quality pink slip dresses that align with current trends and local tastes. The dresses solve the problem of offering versatile, easy-to-style apparel that appeals to diverse demographics. Buyers must prioritize fabric durability, colorfastness, and sizing consistency to ensure customer satisfaction and reduce returns.
Hospitality & Events
Pink slip dresses are increasingly used as stylish yet practical uniforms for hospitality staff and event personnel. This application is particularly relevant in upscale hotels and event management companies across regions such as the Middle East and Europe, where brand image and employee comfort are critical. The dresses provide a balance of elegance and functionality, helping businesses maintain a professional appearance while ensuring staff mobility. Buyers should focus on sourcing dresses with durable fabrics, easy maintenance, and options for custom branding.
E-commerce & Dropshipping
For online fashion platforms targeting international markets, pink slip dresses are a popular fast-moving product due to their universal appeal and simplicity. Dropshipping businesses in Indonesia, France, and beyond benefit from reliable suppliers who can offer flexible minimum order quantities and quick fulfillment. This application addresses the challenge of maintaining inventory agility and meeting diverse customer demands. Key sourcing factors include consistent quality, efficient packaging, and compliance with shipping regulations to minimize delays.
Boutique & Specialty Stores
Boutiques in niche markets leverage pink slip dresses to create distinctive curated collections that stand out from mass-market offerings. This is especially valuable in regions like South America and Europe, where consumers seek unique styles and limited editions. The dresses help boutiques solve the issue of differentiation by offering exclusive designs that reflect local or seasonal aesthetics. Buyers should emphasize transparency in material sourcing, exclusivity agreements, and the ability to customize designs to maintain a competitive edge.
Export & International Trade
Exporters and importers dealing with pink slip dresses cater to a wide array of global fashion markets, adapting designs to meet cultural preferences and regulatory requirements. Businesses in Africa and Europe engaged in bulk trade benefit from sourcing dresses that comply with international quality and safety standards. This application addresses the complexity of cross-border trade, including tariff management and supply chain traceability. Buyers must ensure their suppliers provide full documentation, certifications, and flexible logistics solutions to optimize market entry.
Related Video: LABORATORY APPARATUS AND THEIR USES
Strategic Material Selection Guide for pink slip dress
When selecting materials for manufacturing pink slip dresses, international B2B buyers must carefully consider fabric properties, cost-efficiency, manufacturing complexity, and regional compliance standards. The choice of material directly impacts the dress’s aesthetic appeal, durability, comfort, and suitability for different climates and markets across Africa, South America, the Middle East, and Europe. Below is a detailed analysis of four common materials used in pink slip dresses: silk, satin (polyester-based), cotton blends, and rayon.
Silk
Key Properties:
Silk is a natural protein fiber known for its luxurious sheen, excellent drape, and breathability. It naturally regulates temperature, keeping wearers cool in warm climates and warm in cooler environments. Silk is lightweight but strong, with moderate elasticity.
Pros & Cons:
Silk offers premium quality and a high-end look, which appeals to luxury markets such as France and parts of Europe. It is biodegradable and sustainable when sourced responsibly. However, silk is costly, requires delicate handling during manufacturing, and can be prone to damage from perspiration and sunlight. Its care requirements may limit appeal in regions with high humidity or where easy maintenance is preferred.
Impact on Application:
Silk is ideal for premium pink slip dresses targeting upscale retailers and boutiques. It suits formal and evening wear due to its lustrous appearance but may not be optimal for everyday casual wear in hot or humid climates without proper finishing.
Regional Considerations:
Buyers in Europe and the Middle East often demand certifications related to sustainable sourcing (e.g., OEKO-TEX, GOTS for organic silk). In Africa and South America, where climate can be hotter, silk’s breathability is a plus, but cost and care may limit mass-market appeal. Compliance with ASTM or ISO textile standards is common across these regions.
Satin (Polyester-Based)
Key Properties:
Polyester satin is a synthetic fabric with a smooth, shiny surface and good wrinkle resistance. It is durable, resistant to stretching and shrinking, and maintains color vibrancy well.
Pros & Cons:
This fabric is cost-effective compared to silk and easier to manufacture at scale. It offers a similar glossy finish, making it a popular choice for affordable pink slip dresses. However, polyester satin is less breathable, which may cause discomfort in hot climates. It is also less environmentally friendly due to its synthetic nature.
Impact on Application:
Polyester satin is suitable for mass-market and fast-fashion pink slip dresses, especially where budget constraints exist. It performs well in controlled indoor environments but may be less favored in regions with high temperatures or where consumers prioritize natural fibers.
Regional Considerations:
Buyers from South America and Africa often prefer polyester satin for its affordability and ease of care. However, growing environmental regulations in Europe and the Middle East encourage sourcing recycled polyester or blends to meet sustainability standards like REACH or EU Ecolabel.
Cotton Blends
Key Properties:
Cotton blends combine natural cotton fibers with synthetic fibers like polyester or elastane, enhancing durability, stretch, and wrinkle resistance. Cotton provides breathability and moisture absorption.
Pros & Cons:
Cotton blends strike a balance between comfort, cost, and ease of care. They are more affordable than silk and have better breathability than pure synthetics. The blends improve fabric strength and reduce shrinkage but may lack the luxurious sheen of silk or satin.
Impact on Application:
Ideal for casual and everyday pink slip dresses, cotton blends are versatile across climates and consumer preferences. They can be tailored for stretch or softness, making them suitable for diverse markets from Indonesia to Europe.
Regional Considerations:
In Africa and South America, cotton blends are favored for their comfort and affordability. European buyers often seek blends certified under standards like OEKO-TEX or GOTS to ensure low chemical use and sustainability. Compliance with ASTM and ISO textile standards is also typical.
Rayon
Key Properties:
Rayon is a semi-synthetic fiber made from regenerated cellulose, known for its silk-like feel, excellent drape, and breathability. It absorbs moisture well but wrinkles easily.
Pros & Cons:
Rayon offers a luxurious texture at a mid-range price point, making it attractive for pink slip dresses that require elegance without the high cost of silk. However, it is less durable when wet and requires careful laundering. It can also be prone to shrinkage and color fading.
Impact on Application:
Rayon suits markets where a balance between affordability and luxury is desired. It performs well in moderate climates but may require fabric treatments to enhance durability and wrinkle resistance for hotter or more humid regions.
Regional Considerations:
Buyers in the Middle East and Europe appreciate rayon’s aesthetic and comfort but often request certifications for chemical safety and environmental impact (e.g., OEKO-TEX). In tropical climates like Indonesia and parts of South America, rayon’s breathability is advantageous, but suppliers must ensure proper finishing to withstand local conditions.
Material | Typical Use Case for pink slip dress | Key Advantage | Key Disadvantage/Limitation | Relative Cost (Low/Med/High) |
---|---|---|---|---|
Silk | Luxury, formal, and evening wear | Luxurious sheen, breathable, natural | High cost, delicate care, less durable | High |
Satin (Polyester) | Affordable, mass-market, fast fashion | Cost-effective, durable, wrinkle-resistant | Less breathable, environmental concerns | Low |
Cotton Blends | Casual, everyday wear across diverse climates | Comfortable, breathable, affordable | Less luxurious appearance, varies by blend | Medium |
Rayon | Mid-range luxury with silk-like feel | Soft drape, breathable, mid-cost | Prone to wrinkles, less durable when wet | Medium |
In-depth Look: Manufacturing Processes and Quality Assurance for pink slip dress
Manufacturing Processes for Pink Slip Dress
The production of a pink slip dress involves a series of well-defined stages, each critical to ensuring the final garment meets both aesthetic and functional standards. Understanding these stages helps B2B buyers evaluate suppliers’ capabilities and optimize their sourcing strategies.
1. Material Preparation
- Fabric Selection: The process begins with selecting the appropriate fabric, commonly silk, satin, or polyester blends that provide the characteristic smooth texture and drape of slip dresses. Buyers should specify fabric weight, weave type, and colorfastness requirements.
- Inspection & Testing: Incoming fabric undergoes rigorous inspection for defects such as weaving faults, color inconsistencies, or damage. Some suppliers perform fabric shrinkage tests and tensile strength measurements at this stage.
- Cutting Preparation: Fabric is laid out and marked using CAD software or manual templates to optimize material usage. Precision cutting tools, including automated cutters, are often employed to reduce waste and improve consistency.
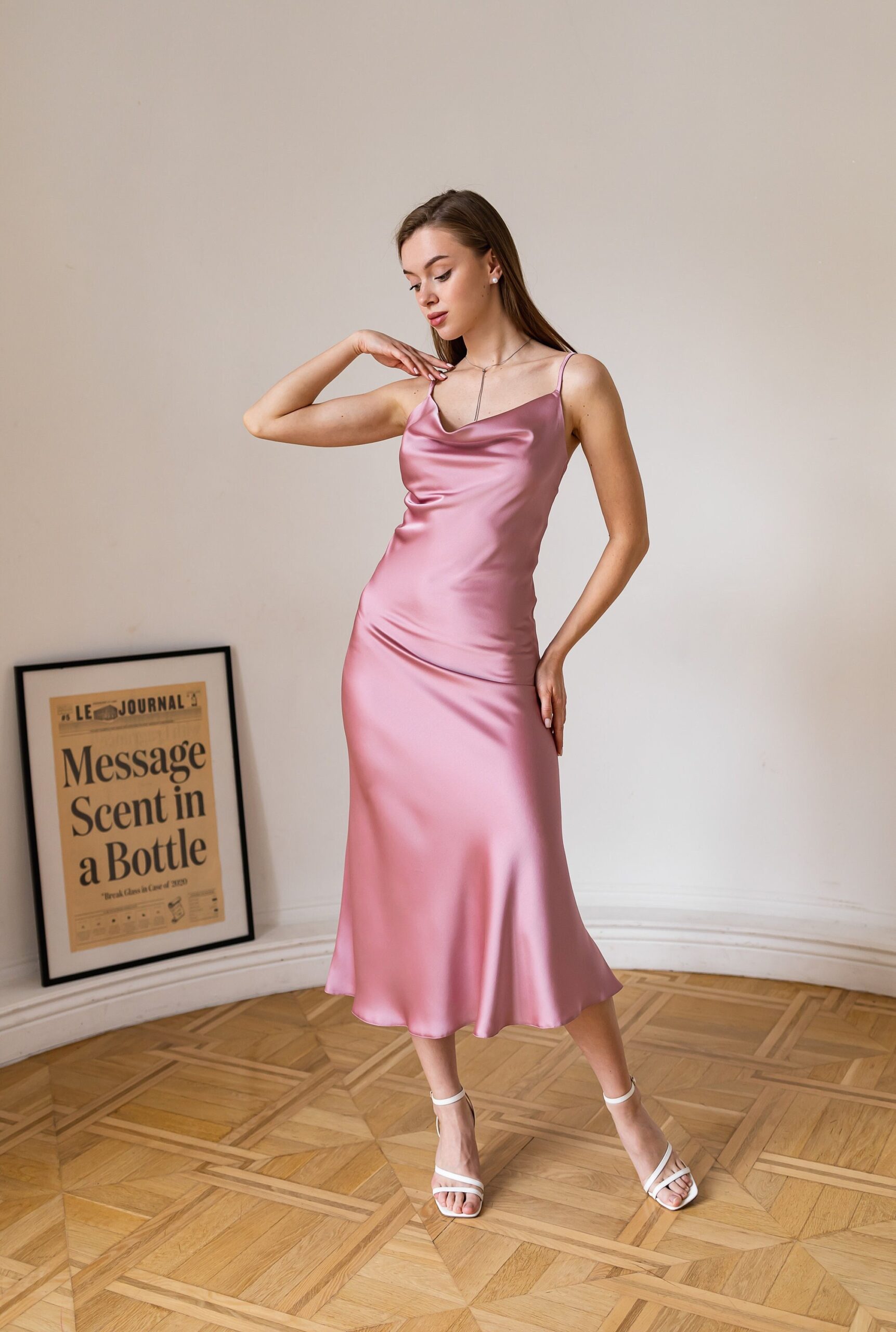
Illustrative Image (Source: Google Search)
2. Forming and Cutting
- Pattern Making: Detailed patterns are created based on the dress design, incorporating seam allowances and fitting ease. These patterns are either digitally generated or hand-crafted by skilled technicians.
- Cutting: The fabric layers are cut according to the patterns. For pink slip dresses, precision is paramount to maintain the smooth silhouette; thus, laser cutting or die-cutting methods may be used in advanced factories.
- Edge Treatment: Depending on fabric type, edges may be heat-sealed or pre-finished to prevent fraying before assembly.
3. Assembly
- Sewing: Skilled operators sew the cut pieces together using specialized machines. For slip dresses, techniques like flatlock seams or French seams are common to enhance comfort and durability while maintaining a delicate appearance.
- Incorporation of Details: Straps, linings, and any embellishments such as lace trims or adjustable sliders are added at this stage. Attention to detail in stitching and attachment is critical to avoid defects.
- Quality Stitching Checks: Stitch density and tension are monitored closely to ensure seam strength without puckering.
4. Finishing
- Pressing and Shaping: The garment is carefully pressed to eliminate wrinkles and set the shape. For delicate fabrics, steam pressing with controlled temperature prevents damage.
- Final Trimming: Loose threads and excess fabric are trimmed. Labels, tags, and packaging inserts are attached as per buyer specifications.
- Packaging: Dresses are folded or hung according to buyer instructions, with protective covers or boxes to maintain garment integrity during transit.
Quality Assurance and Control (QA/QC) in Pink Slip Dress Production
Quality assurance in pink slip dress manufacturing is a multi-tiered process designed to minimize defects and ensure compliance with international standards. For B2B buyers, understanding these QC layers is essential for supplier evaluation and risk mitigation.
Relevant International and Industry Standards
- ISO 9001: This globally recognized quality management system standard ensures suppliers maintain consistent quality processes, traceability, and continuous improvement. Buyers should prioritize suppliers with ISO 9001 certification.
- OEKO-TEX Standard 100: Particularly relevant for textile products, this certification guarantees that fabrics are free from harmful substances, an increasingly important factor for health-conscious markets.
- REACH Compliance: For suppliers exporting to Europe, adherence to REACH regulations on chemical safety is crucial.
- Additional Regional Standards: Depending on the buyer’s location, certifications such as CE marking (Europe) or specific country import regulations must be verified.
Key Quality Control Checkpoints
- Incoming Quality Control (IQC): Raw materials, including fabrics and trims, are inspected upon arrival. IQC verifies compliance with agreed specifications before production begins, reducing the risk of downstream defects.
- In-Process Quality Control (IPQC): Continuous monitoring during sewing and assembly ensures defects like misaligned seams, incorrect stitching, or color mismatches are caught early. Random sampling and real-time inspections are common IPQC methods.
- Final Quality Control (FQC): Completed garments undergo thorough inspection for fit, finish, and functional aspects (e.g., strap adjustability, seam strength). This stage typically includes visual checks, measurement verification, and sometimes wear testing.
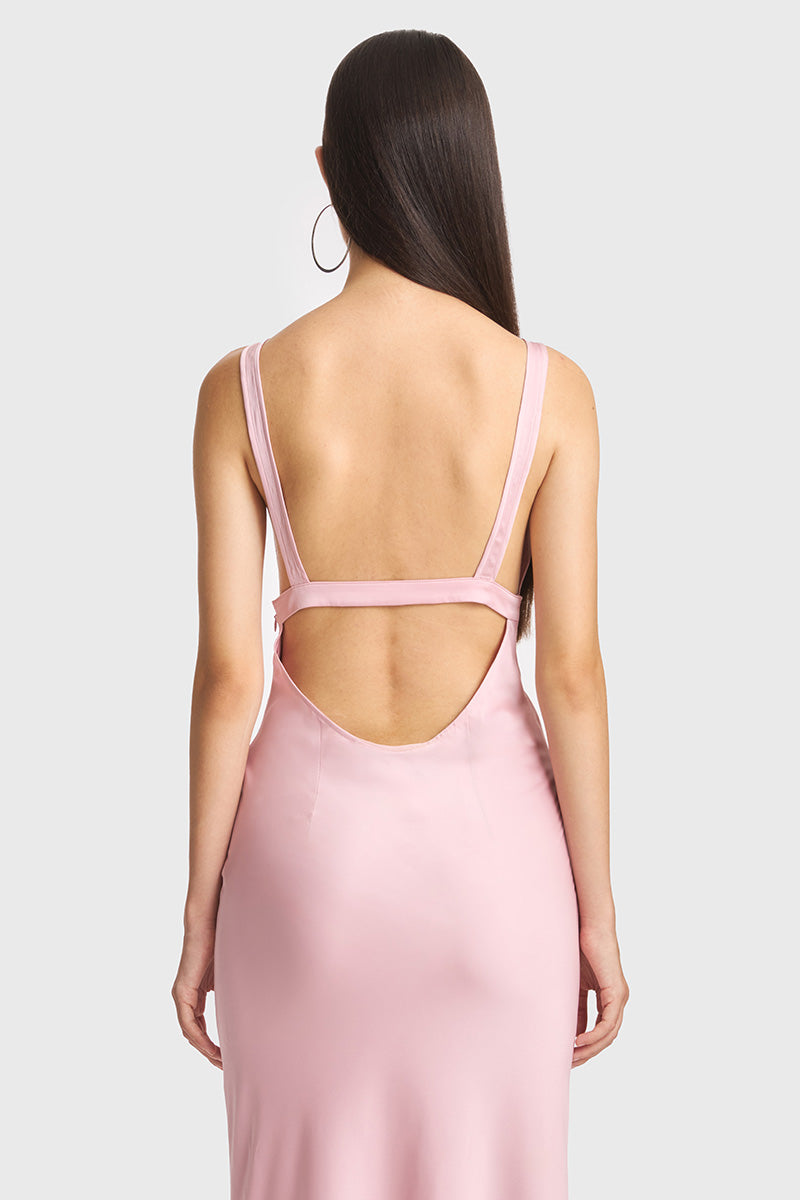
Illustrative Image (Source: Google Search)
Common Testing Methods
- Colorfastness Tests: Ensure the pink dye does not bleed or fade under washing, rubbing, or exposure to light.
- Dimensional Stability: Garments are tested for shrinkage after washing to guarantee size retention.
- Tensile and Seam Strength Testing: Ensures durability of seams and fabric under stress.
- Sensory Inspection: Evaluates hand feel, smoothness, and overall appearance to meet premium quality expectations.
How B2B Buyers Can Verify Supplier Quality Control
For international buyers, especially from diverse markets such as Africa, South America, the Middle East, and Europe, verifying supplier QC processes requires a strategic approach to mitigate risks and ensure product quality.
Supplier Audits
- Factory Audits: Conducting onsite audits helps verify compliance with ISO 9001 and other certifications, assess working conditions, and review QC documentation. Buyers can engage third-party audit firms specializing in textile and garment manufacturing.
- Process Audits: These focus on critical stages like cutting and sewing to ensure adherence to quality standards and efficiency benchmarks.
Quality Reports and Documentation
- QC Reports: Suppliers should provide detailed inspection reports at IQC, IPQC, and FQC stages, including defect rates and corrective actions taken.
- Material Certificates: Verification of fabric origin, chemical safety certificates, and compliance documents support traceability and regulatory adherence.
Third-Party Inspections
- Independent Testing Labs: Buyers can request third-party lab testing for colorfastness, fabric composition, and safety compliance, adding an objective layer of assurance.
- Pre-Shipment Inspections: These inspections verify the quality and quantity of finished goods before shipment, reducing the risk of receiving substandard products.
QC and Certification Nuances for International Buyers
International buyers must navigate varying regulatory landscapes and quality expectations, which influence the QC requirements and certification priorities.
- Africa and South America: Buyers often prioritize durability and cost-efficiency, so QC focuses on fabric strength and seam reliability. Certifications like OEKO-TEX are gaining importance as markets become more health and environment-conscious. Supplier proximity and logistical considerations also affect QC planning.
- Middle East: Compliance with chemical safety and modesty standards may be critical. Buyers here often require stringent documentation and certifications to meet local import regulations.
- Europe (e.g., France): Buyers demand high compliance with environmental and safety regulations (REACH, OEKO-TEX, ISO 9001). Traceability and sustainability certifications are increasingly required, reflecting consumer demand for ethically produced garments.
- Southeast Asia (e.g., Indonesia): Buyers benefit from suppliers with robust in-process controls and certifications that align with international export standards, ensuring smooth customs clearance and market acceptance.
Strategic Takeaways for B2B Buyers
- Specify Detailed Fabric and Construction Standards: Clear, detailed specifications for fabric type, colorfastness, and seam techniques reduce ambiguity and ensure quality alignment.
- Prioritize Certified Suppliers: Engage manufacturers with ISO 9001 and relevant textile certifications to ensure robust quality systems.
- Implement Multi-Stage QC Verification: Request IQC, IPQC, and FQC reports and leverage third-party inspections to mitigate quality risks.
- Conduct Due Diligence Tailored to Regional Needs: Understand local market regulations and buyer expectations to select suppliers who meet both compliance and performance requirements.
- Leverage Technology: Utilize digital tools for pattern making, cutting, and QC documentation to enhance transparency and efficiency.
By applying these insights, international B2B buyers can confidently navigate the complexities of pink slip dress manufacturing and quality assurance, securing reliable partnerships and delivering consistent product excellence to their markets.
Related Video: Garments Full Production Process | Order receive to Ex-Factory | Episode 2
Comprehensive Cost and Pricing Analysis for pink slip dress Sourcing
Understanding the cost and pricing structure for sourcing pink slip dresses is crucial for international B2B buyers aiming to optimize procurement strategies. This analysis breaks down key cost components, price influencers, and actionable tips tailored to buyers from Africa, South America, the Middle East, and Europe, including markets such as Indonesia and France.
Key Cost Components in Pink Slip Dress Production
-
Materials
The fabric choice (silk, satin, polyester blends) heavily impacts cost. Natural fibers like silk command higher prices, while synthetic alternatives may reduce costs but affect perceived quality. Trims, linings, and dyeing processes also contribute to material expenses. -
Labor
Labor costs vary significantly by manufacturing region. Countries with lower labor costs, such as parts of Southeast Asia or Africa, offer competitive pricing but require stringent quality oversight. Skilled labor for delicate stitching or embellishments may increase costs. -
Manufacturing Overhead
Includes factory utilities, equipment depreciation, and administrative expenses. Efficient production lines and economies of scale can reduce overhead per unit. -
Tooling and Setup Costs
Initial pattern making, sample development, and machinery setup are often fixed costs distributed over order volume. Custom designs or frequent style changes increase these expenses. -
Quality Control (QC)
QC ensures product consistency and compliance with buyer specifications. For international buyers, third-party inspections or in-house audits add to overall cost but mitigate risks of returns or reputational damage. -
Logistics and Shipping
Freight charges, customs duties, and tariffs must be factored in. Sourcing from Asia to Europe or Africa involves longer transit times and higher logistics costs compared to regional sourcing. -
Supplier Margin
Suppliers typically include a profit margin reflecting their operational risk and market positioning. Margins fluctuate based on supplier reputation, exclusivity, and order volume.
Influencing Factors on Final Pricing
-
Order Volume and Minimum Order Quantity (MOQ)
Larger orders generally reduce per-unit cost due to fixed cost amortization. Buyers should negotiate MOQs aligned with market demand to avoid inventory surpluses. -
Product Specifications and Customization
Complex designs, bespoke sizing, embroidery, or unique prints increase costs. Standardized styles yield better pricing but may limit market differentiation. -
Material Quality and Certifications
Organic or certified sustainable fabrics command premiums but appeal to eco-conscious consumers in Europe and the Middle East. Certifications (e.g., OEKO-TEX, GOTS) add verification costs. -
Supplier Factors
Established suppliers with proven compliance and reliability may charge higher prices but reduce supply chain risks. New or smaller manufacturers might offer aggressive pricing but require thorough due diligence. -
Incoterms and Payment Terms
The choice of Incoterms (FOB, CIF, DDP) affects who bears transportation and customs risks/costs. Favorable payment terms (e.g., letters of credit, net 30) can improve cash flow but may influence price negotiations.
Strategic Tips for International B2B Buyers
-
Engage in Transparent Negotiations
Understand supplier cost drivers and seek volume discounts or bundled service offerings. Highlight long-term partnership potential to secure better pricing. -
Consider Total Cost of Ownership (TCO)
Beyond unit price, factor in logistics, tariffs, inventory holding, and potential quality failure costs. Sometimes a higher unit price with reliable quality and faster delivery reduces overall expenses. -
Leverage Regional Sourcing Opportunities
Buyers in Africa and South America may benefit from sourcing within or near their regions to reduce shipping times and costs. European buyers, including France, should balance quality expectations with competitive Asian supply chains. -
Prioritize Due Diligence and Compliance
Verify supplier certifications and conduct regular audits. This is especially important for buyers targeting markets with strict import regulations like the EU or Gulf Cooperation Council countries. -
Monitor Currency Fluctuations and Tariff Changes
Exchange rate volatility can impact landed costs. Stay informed on trade agreements and tariff updates to anticipate cost shifts.
Indicative Pricing Disclaimer
Pricing for pink slip dresses varies widely based on material choice, order volume, and customization level. As a rough benchmark, basic polyester slip dresses may start at $8–$12 per unit FOB Asia, while premium silk versions with intricate detailing can exceed $25 per unit. Buyers should request detailed quotations inclusive of all cost components and verify terms to avoid hidden expenses.
By dissecting these cost and pricing elements, international B2B buyers can make informed decisions, optimize sourcing strategies, and strengthen supplier relationships for pink slip dress procurement across diverse global markets.
Spotlight on Potential pink slip dress Manufacturers and Suppliers
This section offers a look at a few manufacturers active in the ‘pink slip dress’ market. This is a representative sample for illustrative purposes; B2B buyers must conduct their own extensive due diligence before any engagement. Information is synthesized from public sources and general industry knowledge.
Essential Technical Properties and Trade Terminology for pink slip dress
Critical Technical Properties for Pink Slip Dresses
When sourcing pink slip dresses for international B2B trade, understanding key technical properties ensures product quality, consistency, and compliance with market expectations. Here are the essential specifications to consider:
-
Fabric Composition and Grade
Typically made from silk, satin, polyester, or blends, the fabric composition affects drape, sheen, comfort, and care requirements. B2B buyers should specify fabric grade (e.g., mulberry silk vs. synthetic satin) to align with target market preferences and price points. Higher-grade materials command premium pricing but yield better customer satisfaction and reduced returns. -
Color Fastness and Shade Consistency
Pink slip dresses require uniform and stable dyeing to maintain color vibrancy under washing and wear. Color fastness ratings (e.g., ISO 105 standards) and Pantone color matching are crucial to ensure consistent pink shades across production batches, especially for multi-country distribution where consumer expectations vary. -
Size Tolerance and Fit Specifications
Clear definition of size charts and allowable dimensional tolerances (typically ±1 cm) is critical. Accurate fit reduces returns and increases brand reputation. Buyers should request tech packs with detailed garment measurements (bust, length, strap length) to verify supplier compliance. -
Seam and Stitch Quality
The durability and aesthetics of seams impact garment longevity and appearance. For slip dresses, flat seams or French seams are preferred to minimize irritation and enhance elegance. Specify stitch density (e.g., 10-12 stitches per inch) and thread type to ensure durability. -
Accessory and Trim Standards
Elements such as adjustable straps, lace trims, or embellishments should meet defined quality standards. Buyers must confirm supplier compliance with safety regulations (e.g., lead-free components) and durability tests to avoid trade disruptions or recalls. -
Packaging and Labeling Requirements
Proper packaging protects delicate fabrics during shipment. Buyers should specify fold methods, polybag types, and labeling (including care instructions, country of origin, and size tags) to meet retail and regulatory standards in target markets.
Key Trade Terminology for B2B Pink Slip Dress Transactions
Understanding common industry terms facilitates clearer communication and smoother negotiations with manufacturers and suppliers:
-
OEM (Original Equipment Manufacturer)
Refers to manufacturers producing pink slip dresses according to the buyer’s design specifications and branding. OEM partnerships allow for customization but may require higher minimum order quantities (MOQs). -
MOQ (Minimum Order Quantity)
The smallest number of units a supplier is willing to produce per order. MOQs affect inventory planning and cash flow, especially for buyers in emerging markets like Africa and South America where market demand might be smaller or seasonal. -
RFQ (Request for Quotation)
A formal document buyers send to suppliers to obtain detailed pricing, lead times, and terms for pink slip dress orders. A well-prepared RFQ includes material specs, sizes, packaging, and delivery requirements to get accurate and comparable quotes. -
Incoterms (International Commercial Terms)
Standardized trade terms defining responsibilities between buyers and sellers regarding shipping, insurance, and customs. Common Incoterms include FOB (Free on Board), CIF (Cost, Insurance, and Freight), and DDP (Delivered Duty Paid). Choosing appropriate Incoterms is vital to control costs and risks in international logistics. -
Tech Pack (Technical Package)
A comprehensive document including design sketches, fabric details, measurements, trims, and construction notes. Tech packs ensure suppliers produce pink slip dresses exactly as intended, minimizing costly errors. -
Lead Time
The total time from order placement to product delivery. Knowing realistic lead times allows buyers to plan inventory, marketing, and sales activities effectively, especially important when sourcing from distant manufacturing hubs.
By mastering these technical properties and trade terms, B2B buyers from Africa, South America, the Middle East, and Europe can make informed sourcing decisions, build stronger supplier relationships, and optimize their supply chains for pink slip dresses. Clear communication on specifications and contractual terms reduces risks and supports successful international trade partnerships.
Navigating Market Dynamics, Sourcing Trends, and Sustainability in the pink slip dress Sector
Market Overview & Key Trends
The global pink slip dress market is witnessing dynamic shifts driven by evolving consumer preferences, technological advancements, and regional fashion influences. For international B2B buyers from regions such as Africa, South America, the Middle East, and Europe, understanding these market nuances is critical to capitalizing on growth opportunities.
Global Drivers: The resurgence of minimalist and versatile fashion staples has propelled the pink slip dress into mainstream wardrobes. Its adaptability across climates—from warm tropical zones in Indonesia and Brazil to cooler European markets like France and Germany—makes it a strategic product for diverse geographies. Additionally, the rise of digital fashion platforms and influencer marketing amplifies demand, encouraging retailers to stock contemporary variations that reflect regional tastes.
Sourcing Trends: Increasingly, buyers prioritize suppliers offering flexible production runs and rapid turnaround times. This agility allows adaptation to fast-changing trends and mitigates inventory risks. Digital integration tools such as AI-driven trend forecasting and virtual sampling are transforming sourcing strategies, enabling buyers to preview styles and fabrics remotely, which is especially beneficial for cross-continental transactions. Countries with established garment manufacturing hubs, including Turkey, Morocco, and Indonesia, offer competitive pricing with improved lead times, appealing to buyers targeting African and Middle Eastern markets.
Market Dynamics: The pink slip dress sector is marked by heightened competition, with brands emphasizing differentiation through fabric innovation and design customization. B2B buyers should note the growing preference for mid-to-high-end quality finishes that balance affordability and durability. Additionally, partnerships with suppliers who can provide comprehensive services—from design assistance to logistics support—enhance supply chain resilience amid global disruptions.
Sustainability & Ethical Sourcing in B2B
Sustainability is no longer optional but a strategic imperative in the pink slip dress supply chain. Environmental impact concerns—from water-intensive cotton cultivation to chemical dyeing processes—are driving buyers to demand transparent and ethical sourcing.
Environmental Impact: The conventional production of slip dresses often involves cotton, which can be resource-heavy. Buyers sourcing for African and South American markets, where water scarcity can be an issue, should prioritize organic or recycled cotton variants. Similarly, the use of low-impact dyes and waterless finishing technologies can significantly reduce the environmental footprint.
Ethical Supply Chains: Due diligence in supplier vetting is essential. B2B buyers must ensure compliance with labor standards, fair wages, and safe working conditions, especially when sourcing from emerging economies. Certifications such as GOTS (Global Organic Textile Standard), OEKO-TEX, and Fair Trade offer credible assurance of responsible practices. Integrating traceability technologies enables buyers to verify origin and production methods, mitigating risks associated with greenwashing or supply chain opacity.
Green Certifications & Materials: Embracing alternative sustainable materials like Tencel, bamboo fibers, and recycled polyester can differentiate product offerings while meeting consumer demand for eco-friendly fashion. Collaboration with suppliers invested in circular economy principles—such as take-back programs or biodegradable packaging—further strengthens brand positioning and satisfies regulatory requirements in Europe and other markets with stringent sustainability laws.
Evolution of the Pink Slip Dress in B2B Context
Originating as an intimate undergarment in the early 20th century, the pink slip dress has evolved into a versatile outerwear piece embodying simplicity and elegance. Its transformation reflects broader shifts in women’s fashion toward minimalism and comfort, making it a perennial favorite across global markets.
For B2B buyers, this evolution underscores the importance of balancing heritage aesthetics with modern design innovations. The dress’s adaptability allows for diverse fabrications and embellishments, enabling suppliers to cater to region-specific preferences—whether lightweight silk blends for tropical climates or layered satin for European winters. Understanding this historical context aids buyers in positioning their collections to appeal to both traditional and contemporary consumers, maximizing market reach.
Related Video: Global trade will never be the same again, says Christine Lagarde | Power & Politics
Frequently Asked Questions (FAQs) for B2B Buyers of pink slip dress
-
How can I effectively vet suppliers of pink slip dresses to ensure reliability and quality?
To vet suppliers, start by verifying their business licenses and certifications relevant to textile and garment manufacturing. Request samples to assess fabric quality, stitching, and finishing. Check their production capacity and lead times to match your order volumes. Use third-party audits or factory visits where possible, especially for suppliers in unfamiliar regions. Additionally, review their compliance with international labor and environmental standards to mitigate reputational risks. Engaging with suppliers who offer traceability or due diligence reports can further assure supply chain transparency and product authenticity. -
What customization options are typically available for pink slip dresses in B2B orders?
Most manufacturers offer various customization options including fabric choice (e.g., satin, silk blends), color shades, dress length (mini, midi, maxi), strap styles, and embellishments like lace or embroidery. Buyers can often request private labeling or hang tags to strengthen brand identity. It’s essential to communicate detailed tech packs or design specifications upfront to avoid misunderstandings. For international buyers, confirm if the supplier supports custom packaging or sizing adjustments to cater to regional market preferences, ensuring your product resonates with target consumers. -
What are typical minimum order quantities (MOQs) and lead times for pink slip dress orders?
MOQs vary widely depending on the supplier and customization level but commonly range from 100 to 500 units per design or color. Lead times generally span 30 to 60 days, factoring in sample approval, production, and shipping. Buyers should negotiate MOQs based on their budget and market demand, especially when entering new regions like Africa or South America. Planning orders well in advance is critical to accommodate longer shipping times and customs clearance, particularly when sourcing from Asia or Europe. Discussing flexible MOQs and expedited production options can help meet urgent demands. -
Which payment terms are standard in international B2B transactions for pink slip dresses?
Common payment terms include a 30-50% upfront deposit with the balance paid before shipment or upon delivery. Letters of credit (LC) and escrow services offer added security for large orders or new supplier relationships. For buyers in regions like the Middle East or Europe, negotiating net 30 or net 60 terms may be possible with established suppliers. It’s advisable to use secure payment platforms and clearly outline terms in contracts to minimize disputes. Always confirm currency exchange considerations and any additional banking fees that could impact overall cost. -
How can I ensure consistent quality assurance (QA) for pink slip dresses sourced internationally?
Implement a multi-step QA process starting with pre-production sample approvals and fabric tests. Insist on in-line inspections during manufacturing and final inspections before shipment to catch defects early. Partnering with third-party quality control firms or using local agents in supplier countries can enhance oversight. Request certifications such as OEKO-TEX or GOTS for fabric safety, and compliance with international standards (ISO, SA8000) to guarantee ethical production. Clear quality benchmarks and communication protocols with suppliers reduce the risk of receiving substandard goods. -
What certifications or compliance documents should I request from pink slip dress suppliers?
Request certificates that prove compliance with international textile and labor standards, such as OEKO-TEX Standard 100 for harmful substances, GOTS for organic textiles, and WRAP or BSCI for ethical labor practices. For European buyers, compliance with REACH regulations and CE markings might be relevant. Additionally, ask for country of origin declarations and supply chain traceability reports to ensure transparency. These documents not only help meet regulatory requirements but also enhance brand reputation in markets sensitive to sustainability and ethical sourcing. -
What are the best practices for managing logistics and shipping of pink slip dress orders internationally?
Coordinate with suppliers to select the most efficient shipping methods—sea freight for cost-effectiveness on large orders, air freight for urgent deliveries. Understand import regulations and duties in your target markets, including any tariffs or restrictions specific to textiles. Use freight forwarders experienced in fashion goods to handle documentation and customs clearance smoothly. Incorporate buffer times in your schedule for potential delays. Tracking shipments digitally and maintaining open communication with logistics partners ensures timely updates and proactive problem-solving. -
How should I handle disputes or quality issues with pink slip dress suppliers?
Establish clear contractual terms outlining quality standards, inspection rights, and dispute resolution mechanisms before placing orders. If issues arise, document defects with photos and detailed reports promptly. Engage in direct negotiation with suppliers for resolution—this may include replacements, refunds, or discounts. Utilize third-party mediation or arbitration if necessary, especially for high-value contracts. Maintaining professional and transparent communication helps preserve long-term supplier relationships while protecting your business interests. Always have contingency plans and diversified supplier bases to mitigate supply disruptions.
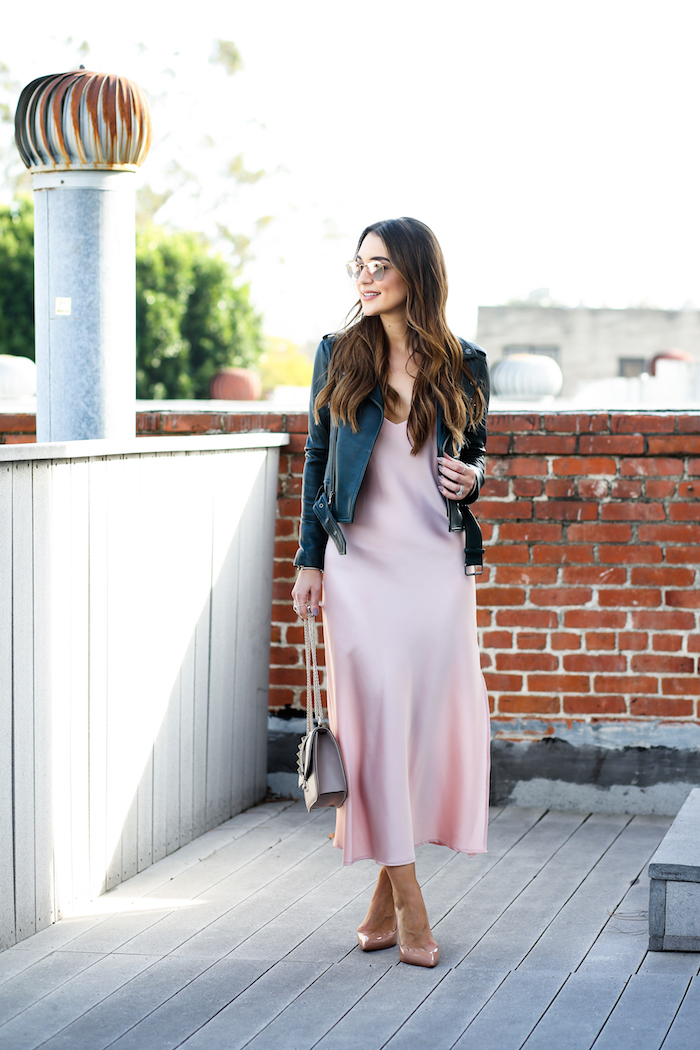
Illustrative Image (Source: Google Search)
Strategic Sourcing Conclusion and Outlook for pink slip dress
Strategic sourcing of pink slip dresses presents a compelling opportunity for international B2B buyers seeking to balance trend responsiveness, quality, and supply chain transparency. Key takeaways underscore the importance of partnering with manufacturers who offer customization capabilities, sustainable practices, and reliable lead times. Buyers from Africa, South America, the Middle East, and Europe must prioritize due diligence in supplier vetting, ensuring compliance with regional regulations and sustainability standards to mitigate risks and enhance brand reputation.
Leveraging strategic sourcing not only secures competitive pricing but also enables agility in responding to evolving consumer preferences, particularly as the pink slip dress continues to gain global fashion traction. Emphasizing traceability and ethical manufacturing further differentiates your offerings in increasingly conscientious markets.
Looking ahead, embracing advanced sourcing strategies—such as integrating digital supply chain verification and fostering long-term supplier relationships—will be critical to sustaining growth and resilience. International buyers are encouraged to proactively engage with innovative manufacturers, invest in supply chain transparency, and align sourcing decisions with emerging market demands to capitalize on the pink slip dress trend effectively. This forward-thinking approach will position your business at the forefront of fashion retail across diverse global regions.