Master Sourcing Strategies for Plastic Dressing: A B2B
Introduction: Navigating the Global Market for plastic dressing
In today’s competitive landscape, plastic dressing has emerged as a vital component across various industries, from automotive and electronics to medical applications. Its significance lies not only in functionality but also in enhancing product aesthetics and durability. As international B2B buyers from regions such as Africa, South America, the Middle East, and Europe seek to optimize their procurement strategies, understanding the nuances of plastic dressing becomes paramount.
This comprehensive guide delves into the multifaceted world of plastic dressing, covering essential aspects such as types of plastic dressing, materials used, manufacturing processes, and quality control standards. Furthermore, it provides insights into sourcing strategies, supplier evaluations, and cost considerations, equipping buyers with the knowledge to make informed decisions. By addressing common queries and challenges faced by B2B buyers, this guide aims to demystify the sourcing process for plastic dressing.
Empowering your sourcing strategy with detailed market analysis and supplier insights, this guide is designed to help you navigate the complexities of the global market. Whether you are looking to enhance product performance or reduce costs, understanding the dynamics of plastic dressing will enable you to forge successful partnerships and drive innovation in your offerings. Leverage this resource to stay ahead in a rapidly evolving marketplace and ensure your procurement decisions align with your business objectives.
Understanding plastic dressing Types and Variations
Type Name | Key Distinguishing Features | Primary B2B Applications | Brief Pros & Cons for Buyers |
---|---|---|---|
Thermoplastic Dressing | Flexible, heat-sensitive, and can be reshaped with heat. | Medical, automotive, and consumer products. | Pros: Lightweight, easy to mold; Cons: Limited temperature resistance. |
Polyurethane Dressing | High durability, excellent abrasion resistance, and elasticity. | Industrial applications and medical devices. | Pros: Strong and resilient; Cons: Higher cost compared to other types. |
Polyvinyl Chloride (PVC) | Rigid or flexible, resistant to environmental degradation. | Construction, plumbing, and automotive parts. | Pros: Cost-effective, versatile; Cons: Environmental concerns due to production. |
Acrylic Dressing | High transparency and UV resistance, with good weatherability. | Signage, displays, and protective covers. | Pros: Aesthetic appeal; Cons: Brittle and can crack under stress. |
Composite Dressing | Combination of materials for enhanced properties. | Aerospace, automotive, and sports equipment. | Pros: Tailored properties; Cons: Complex manufacturing and higher costs. |
Thermoplastic Dressing
Thermoplastic dressings are characterized by their ability to be reshaped with heat, making them ideal for applications that require flexibility and custom fitting. They are commonly used in the medical field for wound care and in the automotive sector for lightweight components. Buyers should consider factors such as temperature resistance and the specific molding capabilities needed for their applications.
Polyurethane Dressing
Polyurethane dressings are known for their high durability and excellent abrasion resistance, making them suitable for industrial applications and medical devices. Their elasticity allows them to withstand mechanical stress, which is crucial in demanding environments. B2B buyers should evaluate the cost versus the longevity and performance benefits when considering polyurethane options.
Polyvinyl Chloride (PVC)
PVC dressings can be rigid or flexible and are widely recognized for their resistance to environmental degradation. Commonly utilized in construction and plumbing, PVC is a cost-effective choice for many applications. Buyers should be aware of the environmental concerns associated with PVC production and consider sustainability when sourcing materials.
Acrylic Dressing
Acrylic dressings offer high transparency and UV resistance, making them perfect for applications in signage and protective covers. Their aesthetic appeal is a significant advantage, particularly in consumer-facing products. However, buyers must consider the brittleness of acrylic, which can lead to cracking under stress, making it less suitable for high-impact applications.
Composite Dressing
Composite dressings combine various materials to enhance performance characteristics, making them ideal for specialized applications in aerospace, automotive, and sports equipment. They can be tailored to meet specific requirements, such as weight reduction or increased strength. Buyers should weigh the benefits of customized properties against the complexity and higher costs associated with composite manufacturing.
Related Video: Lecture 1 Two compartment models
Key Industrial Applications of plastic dressing
Industry/Sector | Specific Application of Plastic Dressing | Value/Benefit for the Business | Key Sourcing Considerations for this Application |
---|---|---|---|
Medical Devices | Protective covers for surgical instruments | Enhances hygiene and safety, reduces risk of contamination | Compliance with medical standards (ISO, FDA) |
Automotive | Cable management systems | Improves durability and organization, reduces maintenance costs | Material compatibility with automotive standards |
Electronics | Insulation for wires and components | Increases product reliability and performance | Thermal and electrical resistance properties |
Oil & Gas | Sealing and protective wraps for equipment | Prevents leaks and prolongs equipment lifespan | Resistance to harsh chemicals and environmental conditions |
Construction | Protective sheathing for wires and cables | Enhances safety and durability on job sites | Compliance with local building regulations |
Medical Devices
In the medical sector, plastic dressing is primarily used for protective covers for surgical instruments and devices. This application is crucial in maintaining hygiene standards and minimizing the risk of contamination during medical procedures. International buyers must ensure that their sourcing partners comply with stringent medical regulations, such as ISO and FDA standards, to guarantee product safety and effectiveness. Additionally, opting for materials that are biocompatible can further enhance patient safety.
Automotive
In the automotive industry, plastic dressing is utilized in cable management systems, which help organize and protect wiring from wear and environmental factors. This application not only improves the durability of components but also reduces maintenance costs associated with wiring issues. Buyers in this sector should consider sourcing materials that meet automotive industry standards for heat resistance and flexibility, ensuring long-term performance in various operating conditions.
Electronics
Plastic dressing serves as insulation for wires and components in the electronics industry. This application is vital for enhancing product reliability and performance by preventing short circuits and electrical failures. When sourcing materials, international buyers should prioritize thermal and electrical resistance properties to ensure that the plastic dressing can withstand the operational stresses of electronic devices, particularly in diverse climates found in Africa, South America, and the Middle East.
Oil & Gas
In the oil and gas sector, plastic dressing is used for sealing and protective wraps around equipment. This application is essential for preventing leaks and prolonging the lifespan of expensive machinery, ultimately leading to cost savings for businesses. Buyers should focus on sourcing materials that exhibit resistance to harsh chemicals and extreme environmental conditions, as these factors are prevalent in oil and gas operations.
Construction
Plastic dressing is commonly applied as protective sheathing for wires and cables in the construction industry. This application enhances safety on job sites by preventing electrical hazards and improving the durability of installations. When sourcing plastic dressing for construction, buyers should ensure compliance with local building regulations and standards, which can vary significantly across different regions in Europe, Africa, and the Middle East.
Related Video: 3M™ V.A.C.® Dressing Basic Application using 3M™ Dermatac™ Drape
Strategic Material Selection Guide for plastic dressing
When selecting materials for plastic dressing, international B2B buyers must consider various factors including the properties of the materials, their suitability for specific applications, and compliance with relevant standards. Below is an analysis of four common materials used in plastic dressing, focusing on their key properties, advantages and disadvantages, and specific considerations for buyers in regions such as Africa, South America, the Middle East, and Europe.
Polypropylene (PP)
Key Properties:
Polypropylene is known for its excellent chemical resistance, lightweight nature, and ability to withstand temperatures up to 100°C (212°F). It has a low moisture absorption rate, making it suitable for various applications.
Pros & Cons:
The main advantages of polypropylene include its durability, resistance to fatigue, and low cost. However, it has lower temperature resistance compared to other materials and can become brittle at low temperatures, which may limit its use in cold environments.
Impact on Application:
Polypropylene is compatible with many chemicals, making it ideal for applications involving corrosive substances. However, it may not be suitable for high-temperature applications.
Considerations for International Buyers:
Buyers should ensure that polypropylene products comply with ASTM and ISO standards. In regions like South Africa and Egypt, local regulations may require specific certifications for chemical resistance.
Polyvinyl Chloride (PVC)
Key Properties:
PVC is a versatile thermoplastic that offers good mechanical strength, chemical resistance, and can withstand temperatures up to 60°C (140°F). It is also flame retardant and has good electrical insulating properties.
Pros & Cons:
PVC is relatively inexpensive and easy to process, making it a popular choice for many applications. However, its rigidity can be a limitation in applications requiring flexibility, and it can release harmful chemicals when burned.
Impact on Application:
PVC is widely used in plumbing and electrical applications due to its excellent corrosion resistance. However, its temperature limitations may restrict its use in high-heat environments.
Considerations for International Buyers:
Buyers in the Middle East and Europe should be aware of the REACH regulations concerning the use of PVC, as compliance may vary by country. Understanding local standards is crucial for ensuring product acceptance.
Acrylonitrile Butadiene Styrene (ABS)
Key Properties:
ABS is known for its high impact resistance, toughness, and ability to withstand temperatures up to 80°C (176°F). It is also easy to paint and glue, enhancing its versatility.
Pros & Cons:
The key advantage of ABS is its strength and durability, making it suitable for demanding applications. However, it is more expensive than polypropylene and PVC, which may be a consideration for budget-conscious buyers.
Impact on Application:
ABS is commonly used in automotive and electronic applications due to its excellent impact resistance. However, it is less resistant to chemicals compared to PVC and polypropylene.
Considerations for International Buyers:
Buyers should check for compliance with automotive standards (like ISO/TS 16949) when sourcing ABS components. In regions like South America, understanding the local market’s acceptance of ABS can influence procurement strategies.
Polyethylene (PE)
Key Properties:
Polyethylene is characterized by its flexibility, low density, and high resistance to moisture and chemicals. It can withstand temperatures ranging from -60°C to 80°C (-76°F to 176°F).
Pros & Cons:
Polyethylene is lightweight and cost-effective, making it suitable for various applications. However, it has lower tensile strength compared to other plastics, which may limit its use in high-stress applications.
Impact on Application:
PE is widely used in packaging and containers due to its moisture resistance. However, its lower strength may not be suitable for applications requiring high structural integrity.
Considerations for International Buyers:
When sourcing polyethylene, buyers should ensure that products meet the relevant food safety standards (like FDA regulations) if used in food packaging. In Europe, compliance with EU regulations is also essential.
Material | Typical Use Case for plastic dressing | Key Advantage | Key Disadvantage/Limitation | Relative Cost (Low/Med/High) |
---|---|---|---|---|
Polypropylene | Chemical containers | Excellent chemical resistance | Brittle at low temperatures | Low |
Polyvinyl Chloride | Electrical conduits | Cost-effective and versatile | Releases harmful chemicals when burned | Low |
Acrylonitrile Butadiene Styrene | Automotive parts | High impact resistance | More expensive than other plastics | Medium |
Polyethylene | Packaging materials | Lightweight and moisture resistant | Lower tensile strength | Low |
This guide provides a comprehensive overview of the materials commonly used in plastic dressing, helping international B2B buyers make informed decisions based on performance, cost, and compliance with regional standards.
In-depth Look: Manufacturing Processes and Quality Assurance for plastic dressing
Manufacturing Processes for Plastic Dressing
Manufacturing plastic dressing involves several key stages, each critical to ensuring the final product meets industry standards and customer specifications. Understanding these processes is essential for B2B buyers, particularly those sourcing from regions like Africa, South America, the Middle East, and Europe.
1. Material Preparation
The manufacturing process begins with material selection. Thermoplastics, such as polyethylene (PE), polypropylene (PP), and polyvinyl chloride (PVC), are commonly used due to their flexibility and durability.
- Material Sourcing: Buyers should verify the quality of raw materials by checking supplier certifications and sourcing practices, as the quality of plastic directly impacts the final product.
- Pre-processing: This includes drying the materials to remove moisture, which is crucial to prevent defects during the molding process.
2. Forming
The forming stage is where the selected plastic is transformed into the desired shape. The primary techniques include:
- Injection Molding: This process involves injecting molten plastic into a mold. It is highly efficient for producing large quantities of uniform products.
- Blow Molding: Used for hollow products, this technique involves inflating hot plastic within a mold.
- Extrusion: This is ideal for producing continuous shapes, such as sheets or tubes, by forcing melted plastic through a die.
Each method has its advantages and is selected based on the product requirements and production volume.
3. Assembly
After forming, components may require assembly. This can involve:
- Mechanical Assembly: Using screws, clips, or other fasteners to join parts.
- Adhesive Bonding: This method uses glues or adhesives to bond components, which is often used when mechanical fastening is impractical.
Buyers should ensure that assembly techniques align with their product specifications and end-use requirements.
4. Finishing
Finishing processes enhance the aesthetic and functional properties of the plastic dressing. Common techniques include:
- Surface Treatment: Processes like sanding, polishing, or painting improve appearance and provide additional protection.
- Printing: Custom branding or labeling can be applied using pad printing or screen printing techniques.
Quality in this stage is vital, as the finishing affects both the product’s marketability and performance.
Quality Assurance in Manufacturing
Quality assurance (QA) is a critical aspect of the manufacturing process for plastic dressing. Implementing robust QA practices ensures that products meet both international standards and customer expectations.
International Standards
B2B buyers should prioritize suppliers who adhere to recognized quality standards such as:
- ISO 9001: This standard outlines requirements for a quality management system (QMS), ensuring consistent quality in products and services.
- ISO 13485: Specifically applicable to medical devices, this standard emphasizes the importance of a QMS that meets regulatory requirements.
- CE Marking: Essential for products sold within the European Economic Area, indicating compliance with health, safety, and environmental protection standards.
Quality Control Checkpoints
Effective quality control (QC) involves several checkpoints throughout the manufacturing process:
- Incoming Quality Control (IQC): Ensures raw materials meet specified standards before production begins.
- In-Process Quality Control (IPQC): Conducted during manufacturing to monitor and control the process, helping to identify issues early.
- Final Quality Control (FQC): The final inspection before products are packaged and shipped, verifying that they meet all specifications.
Common Testing Methods
Testing methods used in quality assurance include:
- Dimensional Inspection: Verifying that the product dimensions match specifications using tools like calipers and micrometers.
- Mechanical Testing: Assessing properties such as tensile strength and impact resistance.
- Environmental Testing: Evaluating how products perform under various environmental conditions (e.g., temperature extremes, humidity).
Verifying Supplier Quality Control
B2B buyers can take several steps to verify the quality control practices of potential suppliers:
- Conduct Audits: Regular audits of suppliers can provide insights into their manufacturing processes and adherence to quality standards.
- Request Quality Reports: Suppliers should provide documentation of their quality assurance processes, including test results and compliance certifications.
- Engage Third-Party Inspectors: Utilizing independent inspectors can offer an unbiased assessment of a supplier’s quality assurance practices.
Quality Control Nuances for International Buyers
International buyers, especially from diverse regions like Africa, South America, and the Middle East, should be aware of specific nuances in quality control:
- Regulatory Compliance: Different regions may have varying regulatory requirements that affect product standards. Understanding these is crucial for compliance and market entry.
- Cultural Differences: Communication styles and business practices can vary significantly. Establishing clear expectations and maintaining open lines of communication can mitigate misunderstandings.
- Supply Chain Logistics: Consideration of logistics, such as shipping times and costs, can impact product quality. Ensure suppliers have robust logistics strategies to minimize delays and damage.
In summary, a thorough understanding of manufacturing processes and quality assurance practices is vital for B2B buyers in the plastic dressing industry. By focusing on material quality, production techniques, and stringent quality control measures, buyers can ensure they receive high-quality products that meet their specific needs.
Related Video: Amazing factories | Manufacturing method and top 4 processes | Mass production process
Comprehensive Cost and Pricing Analysis for plastic dressing Sourcing
To effectively navigate the sourcing of plastic dressing, international B2B buyers must understand the intricate cost structure and pricing dynamics involved. This analysis focuses on the primary cost components, the factors influencing prices, and offers strategic tips for buyers in regions such as Africa, South America, the Middle East, and Europe.
Cost Components
-
Materials: The cost of raw materials significantly influences the overall pricing of plastic dressing. Common materials include various grades of plastics (e.g., polyethylene, polypropylene) and additives. Buyers should monitor market trends and price fluctuations in these materials to optimize procurement strategies.
-
Labor: Labor costs can vary greatly depending on the manufacturing location. Regions with lower labor costs may offer competitive pricing, but this can sometimes compromise quality. Evaluating the skill level and training of the workforce is essential for quality assurance.
-
Manufacturing Overhead: This includes costs associated with utilities, equipment maintenance, and administrative expenses. Efficient manufacturing processes can help reduce overhead, which can be a point of negotiation in pricing discussions.
-
Tooling: Tooling costs are critical, especially for custom designs. These costs can be amortized over larger production runs, making it essential to consider order volumes when assessing tooling expenses.
-
Quality Control (QC): Implementing robust QC measures ensures that the final product meets industry standards. While this may add to the initial cost, it ultimately reduces the risk of defects and returns.
-
Logistics: Shipping and handling costs can vary based on distance, mode of transport, and the complexity of the supply chain. Incoterms play a crucial role in determining who bears these costs, impacting the overall pricing.
-
Margin: Suppliers typically include a profit margin in their pricing. Understanding the average margin in the industry can aid buyers in negotiating better terms.
Price Influencers
Several factors can influence the pricing of plastic dressing:
-
Volume/MOQ: Larger order quantities often lead to lower per-unit costs. Buyers should assess their demand accurately to negotiate minimum order quantities (MOQs) that align with their needs.
-
Specifications/Customization: Custom designs or specific performance criteria can increase costs. Buyers should balance their need for customization with budget constraints.
-
Materials Quality/Certifications: Higher quality materials or those with specific certifications (e.g., ISO, FDA) can command premium prices. Buyers in regulated industries must weigh the benefits of certification against costs.
-
Supplier Factors: The reputation and reliability of suppliers can affect pricing. Established suppliers may charge more due to their proven track record, while new entrants might offer lower prices to gain market share.
-
Incoterms: Understanding Incoterms is vital for managing logistics costs. Buyers should negotiate terms that minimize their risk and exposure to unexpected costs.
Buyer Tips
-
Negotiation: Engage suppliers in discussions about pricing flexibility, especially for larger orders or long-term contracts. Building a relationship can lead to better terms.
-
Cost-Efficiency: Analyze the Total Cost of Ownership (TCO), which includes not only the purchase price but also logistics, maintenance, and potential disposal costs.
-
Market Research: Stay informed about material costs, labor rates, and industry trends. This knowledge can empower buyers during negotiations and help them identify the best sourcing strategies.
-
Pricing Nuances: Be aware that prices can fluctuate based on global supply chain dynamics, tariffs, and local economic conditions. Consider these factors when planning purchases.
-
Supplier Diversity: Explore multiple suppliers to mitigate risks associated with supply chain disruptions. This can also foster competition, potentially leading to better pricing.
In conclusion, by comprehensively understanding the cost structure and pricing dynamics of plastic dressing, B2B buyers can make informed decisions that align with their strategic goals. It is essential to continuously evaluate and adapt sourcing strategies to maintain competitiveness in the global market.
Spotlight on Potential plastic dressing Manufacturers and Suppliers
This section looks at several manufacturers active in the ‘plastic dressing’ market. This is a representative sample for illustrative purposes; B2B buyers must conduct extensive due diligence before any transaction. Information is synthesized from public sources and general industry knowledge.
Essential Technical Properties and Trade Terminology for plastic dressing
Key Technical Properties of Plastic Dressing
Understanding the critical specifications of plastic dressing is essential for B2B buyers to make informed purchasing decisions. Here are some of the most important technical properties to consider:
-
Material Grade
– The material grade refers to the specific type of plastic used in manufacturing the dressing, such as polyethylene (PE), polypropylene (PP), or polyvinyl chloride (PVC). Each material has unique characteristics, including durability, flexibility, and resistance to chemicals. Selecting the right material grade is crucial for ensuring that the plastic dressing meets the application requirements and regulatory standards. -
Tolerance
– Tolerance denotes the permissible limits of variation in the dimensions of the plastic dressing. It is vital for ensuring that components fit together correctly during assembly. Inaccurate tolerances can lead to functional issues or increased manufacturing costs. Understanding tolerance requirements helps buyers avoid costly adjustments or reworks in the production process. -
Thickness
– The thickness of the plastic dressing influences its strength, flexibility, and overall performance. Thicker materials generally offer better durability and resistance to wear, while thinner options may be more lightweight and flexible. Buyers must assess the application’s demands to choose the appropriate thickness for optimal performance. -
Impact Resistance
– This property measures the material’s ability to withstand sudden shocks or impacts without breaking or deforming. High-impact resistance is crucial in applications subject to rough handling or extreme conditions. For B2B buyers, selecting materials with adequate impact resistance can enhance product longevity and reduce replacement costs. -
UV Resistance
– UV resistance is essential for plastic dressings used in outdoor applications, as prolonged exposure to sunlight can degrade the material. Buyers should look for plastics that have been treated or formulated to resist UV degradation to ensure product durability and maintain aesthetic appeal over time.
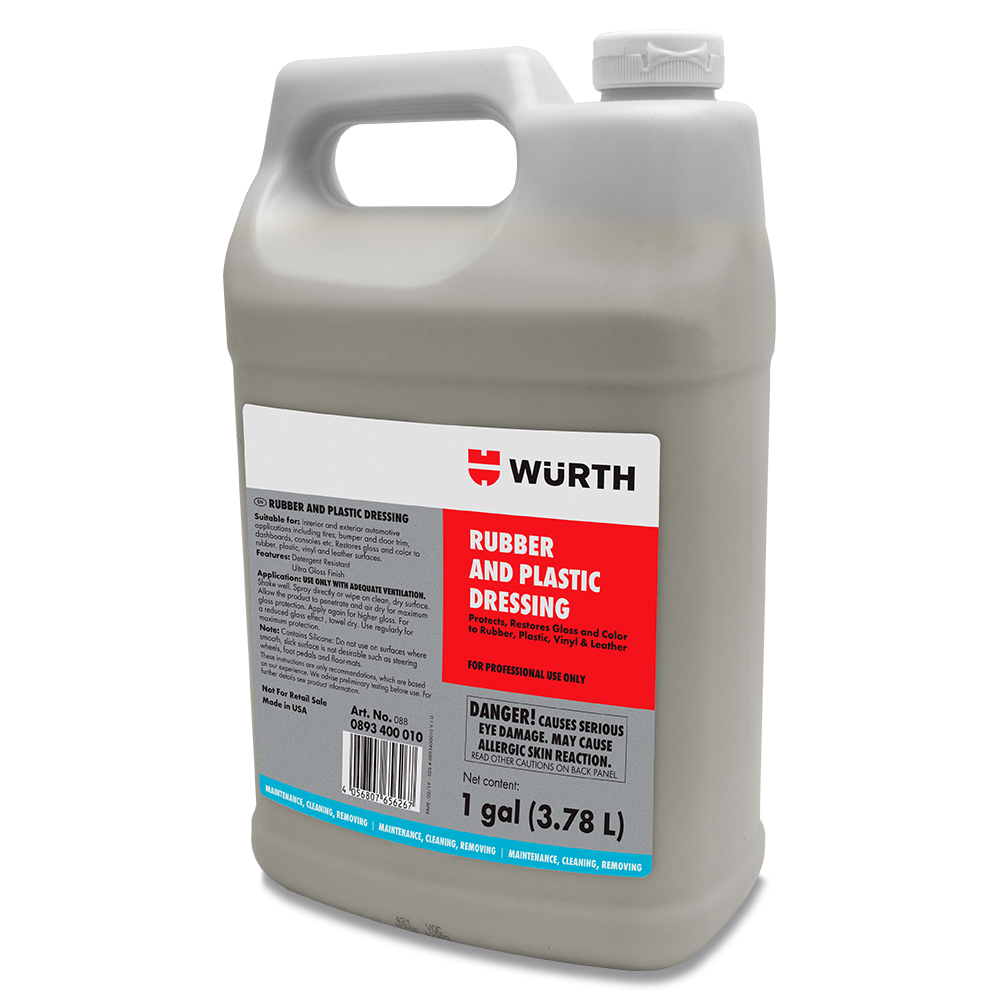
Illustrative Image (Source: Google Search)
Common Trade Terminology
Familiarity with industry jargon is equally important for effective communication and negotiation in the B2B landscape. Here are several key terms to know:
-
OEM (Original Equipment Manufacturer)
– An OEM is a company that manufactures products or components that are used in another company’s end products. Understanding OEM relationships helps buyers identify reliable suppliers who can provide high-quality plastic dressings tailored to specific requirements. -
MOQ (Minimum Order Quantity)
– MOQ refers to the smallest quantity of a product that a supplier is willing to sell. This term is critical for buyers to understand as it impacts inventory management and cash flow. Negotiating favorable MOQs can help businesses maintain optimal stock levels without overcommitting financially. -
RFQ (Request for Quotation)
– An RFQ is a formal document used by buyers to solicit price quotes from suppliers for specific products or services. Providing detailed specifications in an RFQ can lead to more accurate pricing and help buyers compare options effectively. -
Incoterms (International Commercial Terms)
– Incoterms are a set of internationally recognized rules that define the responsibilities of buyers and sellers in international transactions. Understanding these terms, such as FOB (Free on Board) or CIF (Cost, Insurance, and Freight), is essential for managing shipping costs and risks associated with global procurement. -
Lead Time
– Lead time is the period from placing an order to receiving the goods. This term is crucial for inventory planning and meeting customer demands. Buyers should consider lead times when selecting suppliers to ensure timely delivery and avoid disruptions in production.
By grasping these essential technical properties and trade terminologies, international B2B buyers can navigate the complexities of sourcing plastic dressing more effectively, ultimately leading to better procurement decisions and successful partnerships.
Navigating Market Dynamics, Sourcing Trends, and Sustainability in the plastic dressing Sector
Market Overview & Key Trends
The plastic dressing sector is witnessing transformative shifts driven by global market dynamics. Key factors include increasing demand for medical applications, advancements in manufacturing technology, and a heightened focus on supply chain resilience. In regions like Africa, South America, the Middle East, and Europe, the rising prevalence of chronic diseases is boosting the need for high-quality plastic dressings, particularly in healthcare settings. This trend is further complemented by the push for innovation in product design, where custom plastic injection molding and advanced manufacturing techniques are becoming increasingly prevalent.
Emerging B2B technology trends, such as digital supply chain management and vendor-managed inventory, are enhancing operational efficiency. Companies are leveraging data analytics to optimize procurement processes and reduce lead times. The integration of IoT devices in manufacturing is also improving quality control and traceability, ensuring that products meet rigorous standards. For international buyers, particularly those from regions with fluctuating supply chains, these advancements offer a strategic advantage in sourcing reliable and timely products.
Moreover, the market is experiencing a shift towards localized sourcing. Companies are reshoring operations to mitigate risks associated with long lead times and geopolitical uncertainties. This trend allows businesses to enhance their responsiveness to market changes, ensuring that they can meet customer demands effectively.
Sustainability & Ethical Sourcing in B2B
Sustainability has become a cornerstone of the plastic dressing sector, driven by increasing regulatory pressures and consumer demand for environmentally responsible products. The environmental impact of plastic waste is prompting companies to reevaluate their sourcing strategies. Buyers are encouraged to prioritize suppliers who demonstrate a commitment to sustainability through the use of recycled materials and eco-friendly production processes.
Ethical supply chains are gaining prominence as businesses strive to uphold corporate social responsibility. This encompasses ensuring fair labor practices and transparency throughout the supply chain. Certifications such as ISO 14001 for environmental management and Global Recycle Standard (GRS) for recycled materials are becoming essential for companies aiming to build trust with their clients.
The introduction of bio-based plastics and other sustainable materials in the production of plastic dressings further supports this movement. These innovations not only reduce reliance on fossil fuels but also help companies meet sustainability targets, appealing to environmentally conscious consumers and regulatory bodies alike.
Brief Evolution/History
The evolution of plastic dressing can be traced back to the mid-20th century when synthetic materials began to replace traditional bandaging methods. Initially, products were simple and utilitarian, but as technology advanced, so did the functionality and design of plastic dressings. Over the decades, innovations such as hydrocolloid and polyurethane films have improved wound healing and patient comfort.
In recent years, the sector has undergone a significant transformation, with a focus on patient-centric design and advanced materials. The rise of e-commerce and digital procurement platforms has also changed how international buyers source plastic dressings, allowing for greater access to global suppliers and enhanced product variety. This evolution underscores the importance of staying informed about market trends and technological advancements for effective B2B sourcing strategies.
Related Video: Specialization and Trade: Crash Course Economics #2
Frequently Asked Questions (FAQs) for B2B Buyers of plastic dressing
-
What should I consider when vetting suppliers for plastic dressing?
When vetting suppliers, prioritize their experience and reputation in the industry. Look for certifications such as ISO 9001 or ISO 13485, which indicate adherence to quality management standards. Assess their production capabilities, including machinery and technology used, and their ability to meet your specific requirements. Request references from other clients and investigate their track record for timely delivery and customer service. Additionally, consider the supplier’s geographical location and how it impacts logistics, especially for international shipping. -
Can I customize plastic dressing products to suit my specific needs?
Most reputable suppliers offer customization options for plastic dressing products. Discuss your specific requirements, including dimensions, material types, and functional features. Be prepared to provide detailed specifications and prototypes if available. Customization may also influence pricing and lead times, so ensure that you clarify these aspects upfront. Engaging in collaborative design discussions can lead to innovative solutions that meet your unique needs while maintaining product integrity. -
What are the typical minimum order quantities (MOQs) and lead times for plastic dressing?
Minimum order quantities can vary significantly by supplier and product type. Generally, MOQs range from 500 to 5,000 units for standard products, while custom designs may have higher MOQs due to tooling costs. Lead times also depend on the complexity of the order; standard items might take 4-6 weeks, while custom orders can take 8-12 weeks or longer. Always confirm these details during the initial negotiation phase to ensure they align with your project timelines. -
What payment terms are common in international B2B transactions for plastic dressing?
Payment terms can vary based on the supplier’s policies and your negotiation. Common options include payment in advance, letters of credit, or net 30/60 days post-delivery. For international transactions, consider the risks associated with currency fluctuations and potential tariffs. Establish clear payment schedules and ensure both parties agree to the terms in writing to avoid misunderstandings. Using secure payment methods can also provide additional protection for both buyer and seller. -
How can I ensure quality assurance and compliance with certifications for plastic dressing?
To ensure quality assurance, request a copy of the supplier’s quality management system documentation and relevant certifications. Conduct audits or request third-party inspections if necessary. It’s also prudent to specify quality standards in your contract, including the use of approved materials and compliance with local regulations. Establish a routine for quality checks during production and upon delivery to mitigate risks and ensure that the products meet your specifications. -
What logistics considerations should I keep in mind when sourcing plastic dressing internationally?
Logistics play a crucial role in the timely delivery of your products. Evaluate shipping options, including air freight for faster delivery versus sea freight for cost savings. Understand the implications of customs duties and taxes in your country, as these can significantly affect your overall costs. Ensure that your supplier has experience with international shipping and can provide necessary documentation such as bills of lading and certificates of origin to facilitate smooth customs clearance. -
How should I handle disputes with my supplier regarding plastic dressing orders?
To manage disputes effectively, establish clear communication channels and document all agreements, including specifications, delivery dates, and payment terms. If a dispute arises, address it promptly by discussing the issue directly with your supplier. Many suppliers have dispute resolution processes in place. If needed, consider mediation or arbitration as alternatives to litigation. Always keep a record of all communications and agreements to support your case should it escalate. -
What trends are currently influencing the plastic dressing market that I should be aware of?
Key trends include the growing demand for sustainable materials and eco-friendly production processes, driven by global environmental concerns. Additionally, advancements in manufacturing technologies, such as 3D printing and automation, are enhancing customization capabilities and reducing lead times. Buyers should also be aware of the increasing regulatory scrutiny regarding plastic use and waste, which may influence sourcing decisions. Staying informed about these trends can help you align your procurement strategies with market demands.
Important Disclaimer & Terms of Use
⚠️ Important Disclaimer
The information provided in this guide, including content regarding manufacturers, technical specifications, and market analysis, is for informational and educational purposes only. It does not constitute professional procurement advice, financial advice, or legal advice.
While we have made every effort to ensure the accuracy and timeliness of the information, we are not responsible for any errors, omissions, or outdated information. Market conditions, company details, and technical standards are subject to change.
B2B buyers must conduct their own independent and thorough due diligence before making any purchasing decisions. This includes contacting suppliers directly, verifying certifications, requesting samples, and seeking professional consultation. The risk of relying on any information in this guide is borne solely by the reader.
Strategic Sourcing Conclusion and Outlook for plastic dressing
In conclusion, the strategic sourcing of plastic dressing presents a vital opportunity for international B2B buyers seeking to enhance their supply chain resilience and operational efficiency. Key takeaways include the importance of selecting reliable suppliers who can provide quality products with shorter lead times and lower shipping risks. Emphasizing local partnerships can mitigate the vulnerabilities exposed by global disruptions, ensuring a more stable supply chain.
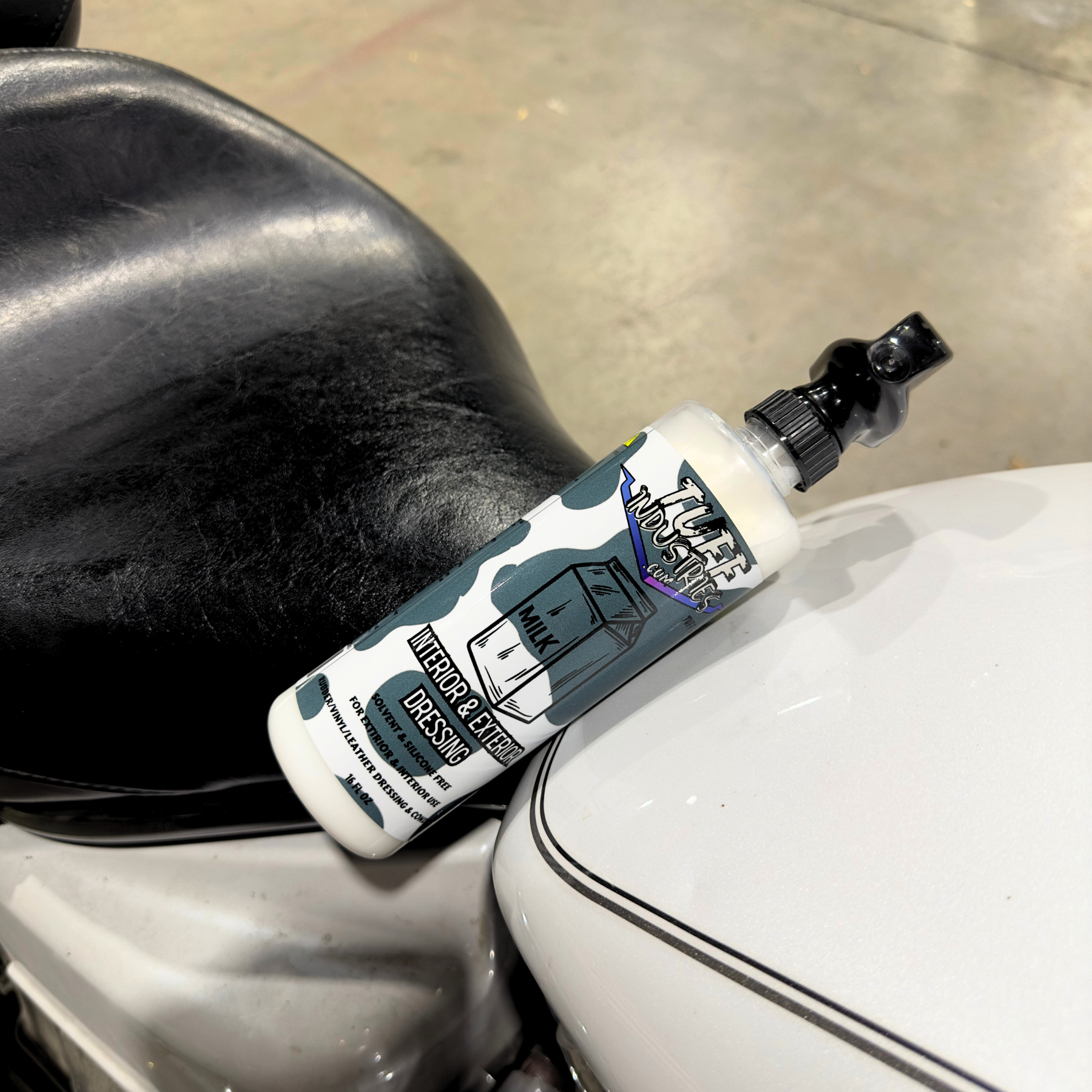
Illustrative Image (Source: Google Search)
Furthermore, as labor and production costs rise in traditional manufacturing hubs, buyers should explore sourcing options in emerging markets across Africa and South America, where competitive advantages can still be realized. Embracing innovative manufacturing techniques, such as automation and lean practices, can also contribute to cost savings and improved quality.
Looking ahead, international B2B buyers are encouraged to proactively engage with suppliers and invest in strategic relationships that align with their business goals. The landscape of plastic dressing is evolving; thus, staying informed and adaptable will be crucial for sustaining a competitive edge. By prioritizing strategic sourcing, buyers can not only optimize their procurement processes but also contribute to a more resilient global supply chain.