Your Ultimate Guide to Sourcing Formal Navy Blue Dress
Guide to Formal Navy Blue Dress
- Introduction: Navigating the Global Market for formal navy blue dress
- Understanding formal navy blue dress Types and Variations
- Key Industrial Applications of formal navy blue dress
- Strategic Material Selection Guide for formal navy blue dress
- In-depth Look: Manufacturing Processes and Quality Assurance for formal navy blue dress
- Comprehensive Cost and Pricing Analysis for formal navy blue dress Sourcing
- Spotlight on Potential formal navy blue dress Manufacturers and Suppliers
- Essential Technical Properties and Trade Terminology for formal navy blue dress
- Navigating Market Dynamics, Sourcing Trends, and Sustainability in the formal navy blue dress Sector
- Frequently Asked Questions (FAQs) for B2B Buyers of formal navy blue dress
- Strategic Sourcing Conclusion and Outlook for formal navy blue dress
Introduction: Navigating the Global Market for formal navy blue dress
The formal navy blue dress stands as a timeless staple in professional and ceremonial wardrobes worldwide. For international B2B buyers, especially from diverse markets such as Africa, South America, the Middle East, and Europe, sourcing this garment involves navigating a complex landscape of style preferences, quality standards, and supply chain dynamics. The versatility and universal appeal of navy blue formalwear make it a critical product category for wholesalers, retailers, and corporate buyers seeking to meet evolving customer demands.
This comprehensive guide delves into every aspect essential for confident procurement decisions. It covers the various types of formal navy blue dresses—from tailored suits to elegant evening gowns—highlighting the importance of fabric selection, sustainable materials, and craftsmanship quality. Insightful sections on manufacturing processes and quality control protocols provide transparency into production standards, enabling buyers to align with suppliers who meet their specific compliance and ethical requirements.
Additionally, the guide explores global supplier networks, cost considerations, and market trends that influence pricing and availability. Special emphasis is placed on regional market nuances and consumer expectations in key territories such as Saudi Arabia and Spain, offering actionable intelligence for tailored sourcing strategies. A detailed FAQ section addresses common challenges, from sizing standards to shipping logistics, ensuring buyers are equipped to mitigate risks and optimize their supply chains.
By integrating these insights, international buyers can streamline vendor selection, reduce lead times, and enhance product offerings with confidence. This guide empowers businesses to capitalize on the enduring appeal of the formal navy blue dress while navigating the complexities of the global apparel market with agility and precision.
Understanding formal navy blue dress Types and Variations
Type Name | Key Distinguishing Features | Primary B2B Applications | Brief Pros & Cons for Buyers |
---|---|---|---|
Classic Sheath Dress | Tailored, form-fitting silhouette, knee-length | Corporate events, formal meetings, conferences | Pros: Timeless style, versatile; Cons: Limited movement, sizing critical |
A-Line Navy Blue Dress | Flared skirt from waist, fitted bodice | Formal dinners, presentations, award ceremonies | Pros: Flattering for many body types, comfortable; Cons: More fabric cost |
Navy Blue Evening Gown | Floor-length, often with embellishments or luxe fabrics | Gala events, black-tie functions, luxury markets | Pros: High perceived value, elegant; Cons: Higher production cost, niche market |
Navy Blue Blazer Dress | Structured blazer-style top with dress skirt or integrated | Business formal, executive meetings, networking | Pros: Professional look, multi-use; Cons: Requires precise tailoring for fit |
Navy Blue Wrap Dress | Adjustable front wrap design, V-neckline | Versatile formal occasions, business casual | Pros: Adjustable fit, stylish; Cons: May require higher quality fabric for structure |
Classic Sheath Dress
This type is characterized by its sleek, form-fitting cut that typically ends at the knee, making it ideal for professional and formal business settings. It suits buyers targeting corporate clients or event organizers who need versatile, elegant attire. When sourcing, buyers should emphasize fabric quality and accurate sizing to avoid returns, as fit is critical for this style’s appeal.
A-Line Navy Blue Dress
Featuring a fitted bodice with a skirt that flares gently from the waist, the A-line dress offers comfort and flattering lines for a broad audience. It is well-suited for formal dinners and ceremonies where ease of movement is important. B2B buyers should consider the higher fabric consumption and potential cost implications but can leverage its broad market appeal.
Navy Blue Evening Gown
This luxurious, floor-length dress often incorporates premium materials and embellishments, catering to high-end events and luxury retailers. Buyers focusing on gala or black-tie markets must prioritize craftsmanship and fabric sourcing, as these factors significantly impact perceived value and price points. Production lead times and minimum order quantities should be carefully managed.
Navy Blue Blazer Dress
Combining the sharp tailoring of a blazer with the femininity of a dress, this style is popular in executive and networking environments. It demands precision in tailoring and quality materials to maintain a professional look. Buyers should assess supplier expertise in structured garments and consider the potential for multi-season use to maximize ROI.
Navy Blue Wrap Dress
Known for its adjustable front closure and flattering V-neckline, the wrap dress adapts well to various body shapes and formal occasions, including business casual settings. Buyers should focus on sourcing fabrics with good drape and durability to maintain structure. This style’s versatility can appeal to diverse markets, but quality control is essential to ensure consistency.
Related Video: Stylish Navy Blue Dress Outfit. How to Wear Navy Blue Dress and Outfit Inspirations?
Key Industrial Applications of formal navy blue dress
Industry/Sector | Specific Application of formal navy blue dress | Value/Benefit for the Business | Key Sourcing Considerations for this Application |
---|---|---|---|
Corporate & Financial Services | Employee uniforms and client-facing attire | Enhances professional image, fosters brand consistency, and improves client trust | Quality fabric for comfort in long wear, compliance with corporate dress codes, availability of customization options |
Hospitality & Luxury Hotels | Staff uniforms for reception, concierge, and management | Creates a sophisticated and welcoming atmosphere, reinforces brand identity | Durable materials for frequent use, stain resistance, culturally appropriate design variations for diverse regions |
Aviation & Airlines | Cabin crew and ground staff uniforms | Promotes a polished, unified look that reassures passengers and supports brand prestige | Breathable and wrinkle-resistant fabrics, ease of maintenance, adherence to international uniform standards |
Government & Public Sector | Official formal events and daily office wear | Projects authority and professionalism, ensures uniformity across departments | Compliance with government regulations, availability in multiple sizes, regional climate adaptability |
Education & Private Institutions | Staff and faculty formal wear | Supports a respectful and professional learning environment, enhances institutional branding | Comfortable and modest designs, fabric durability, options for seasonal variations |
Corporate & Financial Services
In the corporate and financial sectors, formal navy blue dresses serve as standard uniforms for employees in client-facing roles such as bankers, consultants, and executives. The dress color symbolizes trust, stability, and professionalism—key attributes for these industries. For international buyers, particularly from regions like Europe and the Middle East, sourcing must focus on high-quality fabrics that maintain comfort during long working hours and allow for customization to meet specific corporate branding guidelines and dress codes.
Hospitality & Luxury Hotels
Luxury hotels and upscale hospitality businesses rely on formal navy blue dresses for staff uniforms in roles including receptionists, concierge, and management teams. This application enhances the overall guest experience by projecting sophistication and consistency. B2B buyers from Africa and South America should prioritize sourcing fabrics that are durable and stain-resistant due to the high-traffic environment, while also considering culturally appropriate tailoring and design modifications to suit regional preferences and climate conditions.
Aviation & Airlines
Airlines use formal navy blue dresses as part of the cabin crew and ground staff uniforms to maintain a polished, cohesive brand image that instills confidence in passengers. The dresses must be breathable, wrinkle-resistant, and easy to maintain given the demanding schedules and travel conditions. International procurement professionals, especially from Europe and the Middle East, should ensure that suppliers comply with global airline uniform standards and provide options that balance aesthetics with functional performance.
Government & Public Sector
Government agencies and public sector organizations often adopt formal navy blue dresses for official events and daily office attire to convey professionalism and uniformity. Buyers from diverse regions such as Saudi Arabia and Spain must consider compliance with local government regulations regarding uniforms, as well as the availability of a broad size range and climate-adapted fabrics to accommodate different working environments and cultural norms.
Education & Private Institutions
Private educational institutions and universities utilize formal navy blue dresses for staff and faculty to foster a respectful and professional atmosphere. The dress code supports institutional branding and creates a cohesive identity. For B2B buyers in Africa and South America, sourcing should focus on durable, comfortable fabrics with modest design options and seasonal adaptability to ensure year-round wearability while maintaining a polished appearance.
Related Video: LABORATORY APPARATUS AND THEIR USES
Strategic Material Selection Guide for formal navy blue dress
When selecting materials for formal navy blue dresses in an international B2B context, understanding the properties, advantages, and limitations of common fabrics is essential to meet diverse market demands. The choice of material directly influences the garment’s durability, comfort, appearance, and suitability for different climates and cultural preferences. Below is an analysis of four prevalent materials used in formal navy blue dresses, with actionable insights for buyers from Africa, South America, the Middle East, and Europe.
Wool
Key Properties: Wool is a natural fiber known for excellent insulation, moisture-wicking, and breathability. It maintains warmth in cooler climates and adapts well to temperature fluctuations. Wool fibers have natural elasticity and resist wrinkles, making it ideal for formal wear.
Pros & Cons: Wool offers durability and a luxurious finish but can be costly and requires careful handling during manufacturing to avoid shrinkage and felting. It is heavier than synthetic fabrics, which may affect comfort in hot climates. Wool blends can mitigate some of these issues.
Impact on Application: Wool is highly suitable for formal navy blue dresses intended for cooler or temperate regions such as Europe (Spain) and parts of South America with mild winters. Its moisture management and insulation make it less ideal for hot, humid climates typical of much of Africa and the Middle East unless blended or lightweight wool variants are used.
International Considerations: Compliance with standards like ASTM D3776 (mass per unit area) and European EN ISO 3758 (care labeling) is important. Buyers in the Middle East and Africa should consider wool blends or lightweight wool to accommodate warmer climates. Wool sourcing should also align with sustainability and ethical standards increasingly demanded in European markets.
Polyester
Key Properties: Polyester is a synthetic fiber known for high tensile strength, wrinkle resistance, and color retention. It is hydrophobic, drying quickly but less breathable than natural fibers.
Pros & Cons: Polyester is cost-effective, easy to manufacture, and offers excellent colorfastness, which is critical for maintaining the deep navy blue shade. However, it can trap heat and moisture, making it less comfortable in hot climates. It is also less environmentally friendly unless recycled polyester is used.
Impact on Application: Polyester suits markets requiring affordable, durable formal dresses with minimal maintenance. It performs well in humid regions such as the Middle East and parts of Africa where wrinkle resistance and quick drying are valued. However, it may be less preferred in Europe and South America where natural fibers are favored for comfort and sustainability.
International Considerations: Buyers should verify compliance with international standards such as ISO 105 (colorfastness) and Oeko-Tex certification for chemical safety. Offering recycled polyester options can appeal to environmentally conscious buyers in Europe and South America.
Cotton
Key Properties: Cotton is a natural fiber prized for breathability, softness, and moisture absorption. It is comfortable for extended wear and hypoallergenic.
Pros & Cons: Cotton is easy to dye, making it suitable for rich navy blue hues, and is generally affordable. However, it wrinkles easily and can shrink if not pre-treated. Cotton’s durability is moderate, and it may require blends or finishes to improve wrinkle resistance and longevity.
Impact on Application: Cotton is ideal for formal dresses in warmer climates such as much of Africa and South America due to its breathability. For formal wear, mercerized or combed cotton can enhance sheen and durability. However, pure cotton may be less suitable for humid Middle Eastern climates without performance finishes.
International Considerations: Compliance with standards like ASTM D3776 and ISO 6330 (washing and care) is crucial. Organic cotton or sustainably sourced cotton can be a strong selling point in European markets. Buyers should consider blends with synthetic fibers to improve wrinkle resistance for markets demanding low-maintenance garments.
Silk
Key Properties: Silk is a natural protein fiber known for its smooth texture, sheen, and excellent drape. It is lightweight and breathable but delicate.
Pros & Cons: Silk provides a luxurious appearance and excellent comfort, making it ideal for high-end formal dresses. However, it is expensive, requires delicate manufacturing processes, and has lower durability compared to wool or polyester. Silk is prone to water spots and UV degradation.
Impact on Application: Silk is favored in markets where luxury and elegance are paramount, such as Europe and affluent segments in the Middle East. It is less practical for everyday use in hot or humid climates without special finishes. Silk blends can improve durability and reduce cost.
International Considerations: Buyers should ensure compliance with standards such as ISO 105-B02 (colorfastness to washing) and ISO 13934 (tensile properties). Silk sourcing should consider ethical and sustainability certifications, which are increasingly important in European and South American markets.
Material | Typical Use Case for formal navy blue dress | Key Advantage | Key Disadvantage/Limitation | Relative Cost (Low/Med/High) |
---|---|---|---|---|
Wool | Formal dresses for cooler or temperate climates, business or evening wear | Excellent insulation, wrinkle resistance, luxurious feel | Heavier, costly, less suitable for hot climates | High |
Polyester | Affordable, durable formal dresses requiring low maintenance | Cost-effective, wrinkle-resistant, colorfast | Poor breathability, less comfortable in heat, environmental concerns | Low |
Cotton | Breathable formal dresses for warm climates, casual formal events | Soft, breathable, hypoallergenic | Wrinkles easily, moderate durability, may shrink | Medium |
Silk | High-end luxury formal dresses, elegant occasions | Luxurious sheen, excellent drape, lightweight | Expensive, delicate, less durable | High |
In-depth Look: Manufacturing Processes and Quality Assurance for formal navy blue dress
Manufacturing Processes for Formal Navy Blue Dresses
The production of formal navy blue dresses involves a series of meticulously planned stages to ensure high-quality output suitable for international B2B markets. These stages include material preparation, forming, assembly, and finishing — each critical to achieving the desired aesthetic, durability, and comfort expected from formal wear.
1. Material Preparation
Material selection and preparation form the foundation of quality manufacturing. For formal navy blue dresses, premium fabrics such as wool blends, high-grade polyester, silk blends, or fine cotton are commonly used. Fabric inspection is performed to detect flaws like color inconsistencies, weaving defects, or contamination. Cutting is typically executed with precision automated machines or skilled manual cutters, ensuring minimal waste and exact pattern conformity.
Key techniques:
– Fabric inspection and grading: Identifies defects to segregate usable material.
– Marker making and cutting: Optimizes fabric usage and ensures pattern accuracy.
– Pre-treatment: Includes processes like washing, steaming, or chemical treatments to stabilize fabric.
2. Forming
This stage involves shaping fabric pieces into garment components. Techniques such as pleating, darting, and interfacing are applied to create the structural elements of the dress. For formal attire, interfacing materials are often used to reinforce collars, cuffs, and lapels, ensuring crisp lines and professional finishes.
Key techniques:
– Interfacing and lining attachment: Enhances garment structure.
– Precision stitching: Uses industrial sewing machines with specialized needles suitable for delicate or dense fabrics.
– Embroidery or embellishment (if applicable): Often done with automated machines for consistency.
3. Assembly
Assembly integrates all garment components. This includes sewing panels, attaching zippers or buttons, and inserting linings. Seam strength and alignment are crucial at this stage, especially for formal dresses which require flawless silhouettes.
Key techniques:
– Seam sealing and reinforcing: Prevents fraying and increases garment durability.
– Tailoring and fitting adjustments: May be done manually for premium orders.
– Use of automated sewing lines: For volume production with consistent quality.
4. Finishing
The finishing process ensures the garment meets aesthetic and functional standards before packaging. This includes pressing, trimming loose threads, quality checks, and final packaging.
Key techniques:
– Heat pressing and steaming: Removes wrinkles and sets shape.
– Buttonhole and zipper quality verification: Ensures smooth operation.
– Packaging: Uses protective materials to prevent damage during shipping.
Quality Assurance (QA) and Quality Control (QC) Practices
Robust QA/QC systems are essential to maintain consistency, compliance, and customer satisfaction in the formal dress manufacturing sector. International B2B buyers must understand key standards and checkpoints to confidently evaluate suppliers.
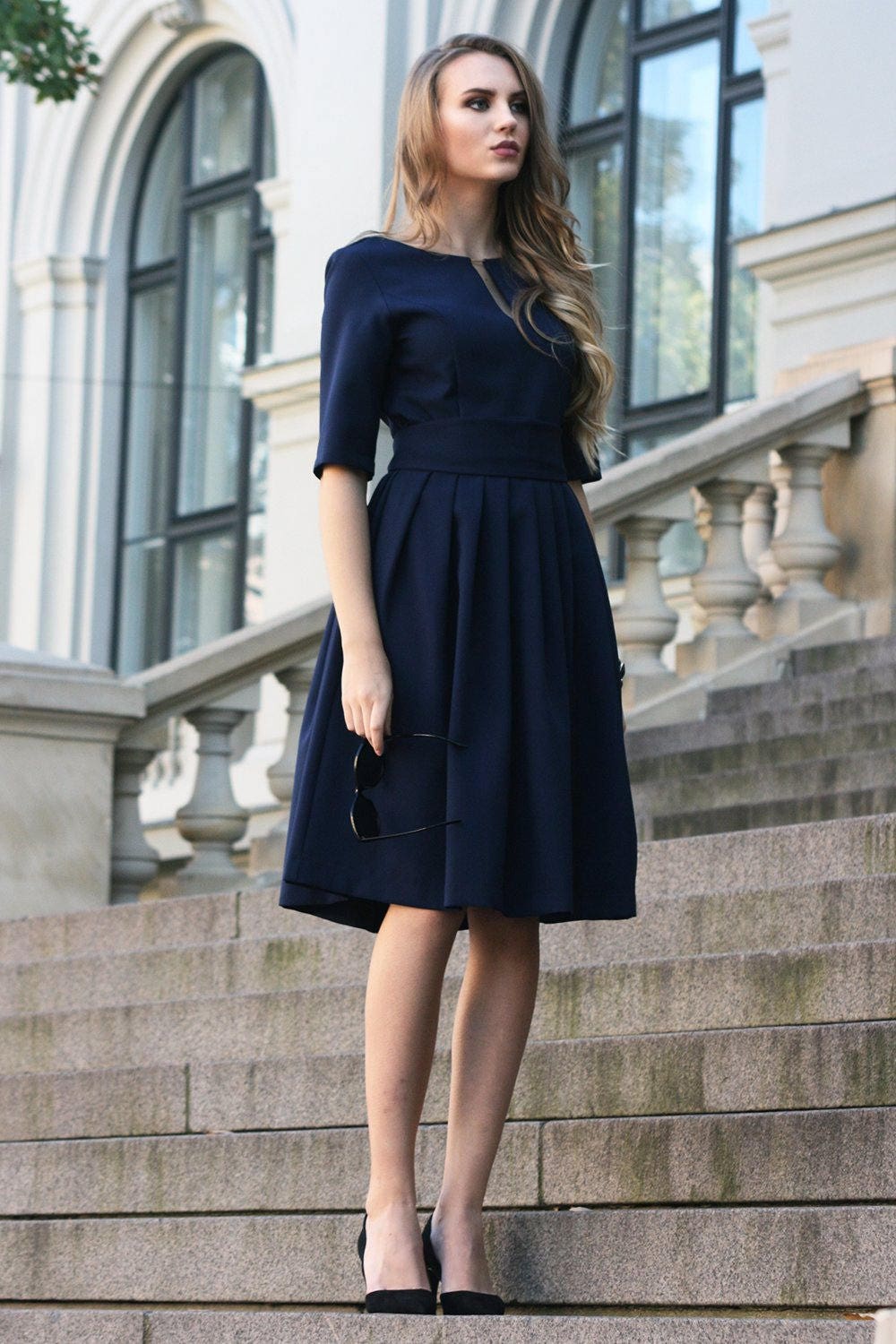
Illustrative Image (Source: Google Search)
Relevant International and Industry Standards
- ISO 9001: The global benchmark for quality management systems (QMS), ensuring suppliers have structured processes for continuous improvement and defect reduction.
- OEKO-TEX Standard 100: Certifies textiles free from harmful substances, crucial for health-conscious markets.
- REACH Compliance: Important for European buyers, ensuring chemical safety in textiles.
- GOTS (Global Organic Textile Standard): Relevant for organic fabric sourcing.
- Local certifications: For example, SASO certification in Saudi Arabia or INMETRO in Brazil may be required for import compliance.
QC Checkpoints Throughout Manufacturing
- Incoming Quality Control (IQC): Inspection of raw materials and components before production begins. This includes fabric quality, colorfastness tests, and accessory verification.
- In-Process Quality Control (IPQC): Continuous monitoring during production stages to detect and correct defects early. Key focus areas include seam integrity, stitching density, and adherence to design specifications.
- Final Quality Control (FQC): Comprehensive inspection of finished dresses. This stage covers dimensional accuracy, color uniformity, functional checks (zippers, buttons), and aesthetic inspection (wrinkles, stains).
Common Testing Methods
- Colorfastness testing: Ensures the navy blue dye resists fading or bleeding.
- Tensile and seam strength tests: Verify garment durability under stress.
- Dimensional stability tests: Assess shrinkage or deformation after washing.
- Visual inspection: Detects surface defects, irregularities, or finishing flaws.
- Chemical residue tests: Confirm compliance with safety standards.
How B2B Buyers Can Verify Supplier QC Capabilities
International buyers should take proactive steps to validate supplier quality management systems and production reliability:
- Factory Audits: Conduct on-site or virtual audits focusing on process controls, equipment, worker skill levels, and hygiene practices. Third-party audit firms provide impartial assessments.
- Review of QC Documentation: Request detailed quality inspection reports, test certificates, and compliance documentation to verify adherence to standards.
- Sample Testing: Order pre-production and production samples for independent lab testing to confirm material and workmanship quality.
- Third-Party Inspections: Employ trusted inspection agencies to perform IQC, IPQC, and FQC checks, providing unbiased verification.
- Supplier Certifications: Evaluate certifications like ISO 9001, OEKO-TEX, and local regulatory approvals as indicators of quality commitment.
QC and Certification Nuances for International Buyers in Africa, South America, the Middle East, and Europe
Africa and South America
Buyers in these regions often face challenges with inconsistent supply chain traceability and variable regulatory enforcement. Prioritize suppliers with:
– Transparent QC documentation.
– Certifications recognized internationally (ISO, OEKO-TEX).
– Experience exporting to regulated markets (EU, Middle East).
Local regulatory standards may be emerging; hence, international standards often serve as the benchmark.
Middle East (e.g., Saudi Arabia)
Strict import regulations and quality expectations necessitate:
– Compliance with SASO and Gulf Cooperation Council (GCC) standards.
– Suppliers capable of providing Halal certifications if required.
– Attention to cultural preferences in dress style and modesty, impacting design and finishing.
Robust QC systems aligned with both international and regional standards are critical.
Europe (e.g., Spain)
European buyers demand high compliance with:
– REACH and EU textile labeling regulations.
– Sustainability certifications (GOTS, OEKO-TEX).
– Ethical manufacturing practices, including labor standards audits.
Quality expectations are high, with emphasis on traceability, sustainability, and transparency.
Summary Recommendations for B2B Buyers
- Select suppliers with integrated manufacturing processes that emphasize precision cutting, expert assembly, and professional finishing tailored to formal navy blue dresses.
- Insist on documented quality management systems aligned with ISO 9001 and relevant textile standards.
- Engage in comprehensive QC verification through audits, sample testing, and third-party inspections.
- Understand regional certification requirements and ensure suppliers can meet or exceed these to avoid compliance issues.
- Prioritize sustainability and ethical practices increasingly demanded in Europe and gaining traction in other regions.
By focusing on these manufacturing and quality assurance pillars, international B2B buyers can confidently source formal navy blue dresses that meet stringent quality, compliance, and market expectations across Africa, South America, the Middle East, and Europe.
Related Video: Garments Full Production Process | Order receive to Ex-Factory | Episode 2
Comprehensive Cost and Pricing Analysis for formal navy blue dress Sourcing
Breakdown of Cost Components in Formal Navy Blue Dress Sourcing
When sourcing formal navy blue dresses, understanding the core cost components is essential for international B2B buyers aiming to optimize procurement and pricing strategies. The main cost elements include:
- Materials: Fabric quality (e.g., premium wool blends, high-grade polyester, or silk), linings, buttons, zippers, and thread. Material costs fluctuate based on fiber origin, fabric weight, and certification (e.g., OEKO-TEX, GOTS for sustainability).
- Labor: Skilled tailoring and stitching labor costs vary significantly by manufacturing country. Regions like South Asia and parts of Europe have higher labor rates compared to Southeast Asia but may offer superior craftsmanship.
- Manufacturing Overhead: Includes factory utilities, machinery depreciation, and indirect labor such as supervisors and maintenance staff. Efficient production lines with automation can reduce overhead.
- Tooling and Setup: One-time costs for pattern making, sample development, and cutting dies. These upfront investments are amortized over production volumes.
- Quality Control (QC): Inspection costs to ensure fabric color consistency, stitching accuracy, and compliance with buyer specifications. QC may be internal or outsourced.
- Logistics and Freight: International shipping, customs duties, insurance, and inland transportation. Costs depend on Incoterms, shipment mode (air/sea), and destination port efficiency.
- Margin: Supplier profit margin, which can range widely depending on supplier scale, exclusivity, and demand conditions.
Key Pricing Influencers for Formal Navy Blue Dresses
Several factors influence the final quoted price and should be carefully evaluated:
- Order Volume and Minimum Order Quantity (MOQ): Larger volumes typically command lower per-unit costs due to economies of scale. MOQ requirements can vary from 100 to 1000+ units depending on the manufacturer.
- Product Specifications and Customization: Complex designs, special trims, embroidery, or bespoke tailoring increase costs. Custom sizing or private label branding also adds to expenses.
- Material Selection and Quality Certifications: High-end fabrics with certifications for sustainability or performance will increase cost but add value for discerning markets.
- Supplier Reliability and Location: Established suppliers with strong compliance records may price higher but reduce risks. Proximity to shipping hubs can lower logistics costs.
- Incoterms: Terms such as FOB, CIF, or DDP affect who bears logistics and customs costs, impacting landed cost and cash flow management.
- Quality Standards and Certifications: Compliance with international standards (ISO, SA8000) or specific buyer requirements (e.g., ethical sourcing) can influence price.
Strategic Buyer Tips for International B2B Procurement
For buyers from Africa, South America, the Middle East, and Europe, navigating the cost and pricing landscape requires a nuanced approach:
- Negotiate Beyond Price: Engage suppliers on payment terms, lead times, and bundled services like packaging or drop shipping to optimize overall cost.
- Evaluate Total Cost of Ownership (TCO): Factor in shipping delays, customs clearance, warehousing, and potential rework costs rather than focusing solely on unit price.
- Leverage Volume and Long-Term Contracts: Committing to multi-order agreements can unlock better pricing tiers and priority production slots.
- Understand Regional Pricing Nuances: For example, Middle Eastern buyers might prioritize certifications related to halal compliance, while European buyers often emphasize sustainability credentials.
- Incorporate Currency Risk Management: Exchange rate fluctuations can affect landed costs; consider contracts in stable currencies or use hedging tools.
- Verify Incoterm Implications: Ensure clarity on cost responsibilities and risk transfer points to prevent unexpected charges.
- Request Detailed Cost Breakdowns: Transparency helps identify cost-saving opportunities, such as alternative materials or simplified designs without compromising quality.
- Consider Supplier Technology Adoption: Suppliers utilizing advanced PLM (Product Lifecycle Management) or AI-driven sourcing tools often offer better cost control and faster response times.
Disclaimer on Pricing
Prices for formal navy blue dresses vary widely based on material quality, production scale, supplier location, and customization level. The figures and strategies discussed are indicative and should be validated through direct supplier engagement and market research tailored to your specific sourcing region and business needs.
Spotlight on Potential formal navy blue dress Manufacturers and Suppliers
This section offers a look at a few manufacturers active in the ‘formal navy blue dress’ market. This is a representative sample for illustrative purposes; B2B buyers must conduct their own extensive due diligence before any engagement. Information is synthesized from public sources and general industry knowledge.
Essential Technical Properties and Trade Terminology for formal navy blue dress
Critical Technical Properties for Formal Navy Blue Dresses
When sourcing formal navy blue dresses, understanding key technical specifications ensures product quality, consistency, and compliance with buyer expectations across diverse markets such as Africa, South America, the Middle East, and Europe.
-
Material Grade and Composition
The fabric quality, commonly wool blends, polyester, or high-grade cotton, determines durability, comfort, and appearance. Premium grades offer enhanced wrinkle resistance and color retention—critical for formal wear. Buyers should specify fiber content percentages to meet climate and cultural preferences. -
Color Fastness and Shade Consistency
Navy blue must maintain uniformity across batches to avoid mismatched inventory. Color fastness ratings (to washing, light, and rubbing) are essential to prevent fading, especially in regions with intense sunlight or humidity. Insist on standardized color codes (e.g., Pantone references) for precise replication. -
Tolerance in Sizing and Fit
Formal dresses require strict adherence to measurement tolerances (usually ±0.5 cm) to ensure consistent fit across production runs. This precision supports brand reputation and reduces return rates. Detailed size charts aligned with international standards are vital for cross-border trade. -
Fabric Weight and Weave Density
The weight (grams per square meter, gsm) and weave tightness affect the dress’s drape and structure. Heavier fabrics suit cooler climates, while lighter weaves provide breathability for warmer regions. Verify supplier specifications to match target market needs. -
Stitching Quality and Seam Strength
Durable stitching using industry-standard thread counts and seam types (e.g., double-needle stitching) enhances garment longevity. Seam strength tests and inspection reports help prevent defects and customer dissatisfaction, especially important in formal apparel. -
Compliance with Safety and Environmental Standards
Certifications such as OEKO-TEX Standard 100 or REACH compliance indicate the absence of harmful substances. These are increasingly required by European and Middle Eastern markets, reflecting growing consumer and regulatory demands for sustainable, safe textiles.
Essential Trade Terminology in Apparel Sourcing
Understanding common trade terms empowers B2B buyers to navigate negotiations, contracts, and logistics effectively.
-
OEM (Original Equipment Manufacturer)
Refers to suppliers producing garments based on the buyer’s design and specifications. OEM partnerships allow for customization and brand exclusivity, vital for formal dress collections aiming at distinct market segments. -
MOQ (Minimum Order Quantity)
The smallest order volume a supplier accepts. MOQs affect pricing, inventory management, and cash flow. Buyers from smaller markets or startups should negotiate MOQs aligned with their sales forecasts and storage capacity. -
RFQ (Request for Quotation)
A formal inquiry sent to suppliers detailing product specifications and quantities to obtain pricing and lead times. Precise RFQs reduce misunderstandings and expedite the procurement process, especially when dealing with international vendors. -
Incoterms (International Commercial Terms)
Standardized trade terms defining responsibilities for shipping, insurance, and customs between buyer and seller (e.g., FOB, CIF, DDP). Selecting appropriate Incoterms clarifies cost allocation and risk management in cross-border transactions. -
Lead Time
The total time from order placement to delivery. Critical for planning inventory and meeting market demand cycles. Buyers should factor in production, quality control, and shipping durations, particularly for seasonal formalwear. -
Bill of Materials (BOM)
A detailed list of all components (fabric, trims, buttons) used in manufacturing the dress. A comprehensive BOM helps control costs, ensures quality consistency, and facilitates supplier communication.
By mastering these technical properties and trade terms, international B2B buyers can optimize sourcing strategies, ensure product quality, and streamline operations for formal navy blue dress procurement tailored to diverse global markets.
Navigating Market Dynamics, Sourcing Trends, and Sustainability in the formal navy blue dress Sector
Market Overview & Key Trends
The global formal navy blue dress market is shaped by evolving consumer preferences, technological advancements, and shifting sourcing dynamics. For international B2B buyers from regions such as Africa, South America, the Middle East, and Europe—including key markets like Saudi Arabia and Spain—understanding these factors is critical for strategic sourcing and supply chain optimization.
Global Drivers:
The demand for formal navy blue dresses is fueled by the universal appeal of navy blue as a versatile, professional, and culturally neutral color suitable for diverse formal occasions. Economic growth in emerging markets, rising urbanization, and increasing participation of women in the workforce are expanding the formal wear segment. Additionally, the influence of digital fashion trends and social media has accelerated demand for stylish yet classic formal attire.
Sourcing Trends:
Buyers are increasingly prioritizing agility and speed-to-market. Technologies such as AI-driven trend forecasting and digital product lifecycle management (PLM) solutions help brands and suppliers rapidly adapt collections to shifting customer tastes. Cloud-based platforms enable real-time collaboration with global suppliers, improving transparency and reducing lead times. For formal navy blue dresses, this means quicker iterations on design details like fabric selection and fit customization, ensuring alignment with market demand.
Market Dynamics:
Supply chain complexities, including geopolitical tensions and raw material price volatility, compel buyers to diversify sourcing bases. Regions like South America and Africa are emerging as attractive sourcing hubs due to competitive labor costs and growing manufacturing capabilities. Meanwhile, buyers in Europe and the Middle East are focusing on multi-channel distribution strategies that blend wholesale, retail, and e-commerce channels to maximize reach and efficiency.
Actionable Insight:
B2B buyers should leverage integrated sourcing technologies and maintain flexible supplier networks to mitigate risks. Prioritize suppliers who demonstrate responsiveness and innovation in fabric technology, such as wrinkle-resistant or breathable textiles, which enhance the appeal of formal navy blue dresses in varied climates and cultural contexts.
Sustainability & Ethical Sourcing in B2B
Sustainability has become a decisive factor in the formal navy blue dress sector, driven by regulatory pressures and increasing consumer demand for ethical products. For B2B buyers, embedding sustainability into sourcing strategies is both a compliance necessity and a competitive differentiator.
Environmental Impact:
Traditional textile manufacturing is resource-intensive, consuming large amounts of water and energy, and generating chemical waste. Selecting suppliers committed to reducing carbon footprints through energy-efficient production, water recycling, and low-impact dyeing processes is essential. Navy blue dyes, traditionally reliant on synthetic chemicals, are increasingly being replaced with eco-friendly alternatives such as natural indigo or low-impact reactive dyes.
Ethical Supply Chains:
Ensuring fair labor practices and safe working conditions throughout the supply chain is paramount. B2B buyers should require transparency via certifications like Fair Trade, WRAP (Worldwide Responsible Accredited Production), or SA8000. These certifications provide assurance that the formal navy blue dresses are produced without exploitation and align with international labor standards.
Green Certifications & Materials:
Sourcing formal navy blue dresses made from organic cotton, recycled polyester, or sustainable blends can significantly reduce environmental impact. Certifications such as GOTS (Global Organic Textile Standard) and OEKO-TEX Standard 100 guarantee that fabrics meet stringent environmental and safety criteria. Additionally, lifecycle assessments (LCA) can help buyers evaluate the overall sustainability footprint of products and select suppliers who demonstrate continuous improvement.
Actionable Insight:
International buyers should integrate sustainability criteria into supplier evaluation frameworks and leverage digital tools for supply chain traceability. Engaging suppliers in sustainability initiatives not only mitigates risks but also enhances brand reputation in increasingly eco-conscious global markets.
Evolution and Historical Context
The formal navy blue dress has long been a staple in professional and formal wardrobes, evolving from traditional military and naval uniforms that influenced fashion’s adoption of navy blue as a symbol of authority and elegance. Over decades, this color has transcended its origins to become a global formal wear standard, favored for its sophistication and versatility.
From the mid-20th century onwards, formal navy blue dresses gained prominence in business and evening wear, adapting to cultural nuances across continents. Today, the sector reflects a fusion of classic tailoring with modern fabric innovations, catering to diverse markets from European corporate settings to Middle Eastern formal events.
For B2B buyers, understanding this evolution aids in selecting designs and suppliers that balance timeless appeal with contemporary demands, ensuring relevance across different international markets.
Related Video: International Trade 101 | Economics Explained
Frequently Asked Questions (FAQs) for B2B Buyers of formal navy blue dress
-
How can I effectively vet suppliers of formal navy blue dresses from different regions like Africa, the Middle East, or Europe?
Begin by verifying the supplier’s business licenses and certifications relevant to textile and apparel manufacturing. Request product samples to assess quality and compliance with your market standards. Utilize third-party audit services to inspect factory conditions and ethical practices, especially in regions with varying labor laws. Check references and reviews from other international buyers, and confirm their ability to meet your order size and delivery timelines. Establish clear communication channels early to evaluate responsiveness and transparency. -
What customization options are typically available for formal navy blue dresses in B2B sourcing?
Customization can include fabric choice, dress design details (such as collar style, sleeve length, and cut), sizing specifications, branding elements like labels or embroidery, and packaging preferences. Many manufacturers offer bespoke services to accommodate cultural preferences or regional dress codes, which is crucial for buyers from diverse markets like Saudi Arabia or Spain. Ensure your supplier can handle tech packs or detailed design sheets and confirm lead times for customized orders, as these may be longer than standard production runs. -
What are the common minimum order quantities (MOQs) and lead times for formal navy blue dress suppliers catering to international buyers?
MOQs typically range from 100 to 500 pieces per style or design, but this varies based on the supplier’s scale and production capabilities. Lead times can range from 30 to 90 days depending on complexity, customization, and raw material availability. Buyers from Africa and South America should factor in additional time for shipping and customs clearance. Negotiate MOQs upfront to balance inventory risks and cost efficiency. Some suppliers may offer sample orders or smaller MOQs for initial testing. -
Which payment terms are most secure and common for international B2B transactions involving formal dresses?
Common payment terms include a 30% deposit upfront with the balance paid before shipment or against documents via Letter of Credit (LC) to mitigate risk. For trusted suppliers, net 30 or net 60 days terms might be negotiated. Use escrow services or trade finance platforms where possible. Ensure payment terms align with your cash flow and protect against supplier default. Always clarify currency, bank charges, and confirm all payment methods accepted by the supplier.

Illustrative Image (Source: Google Search)
-
What quality assurance certifications and standards should I look for when sourcing formal navy blue dresses internationally?
Look for ISO 9001 certification for quality management systems and OEKO-TEX Standard 100 certification ensuring textiles are free from harmful substances. Compliance with local regulations such as REACH in Europe or GOTS for organic textiles can be critical. Certifications related to ethical labor practices (e.g., SA8000) enhance supplier credibility. Request detailed inspection reports and consider engaging third-party quality control agencies to verify garment standards before shipment. -
How should I manage logistics and shipping challenges when importing formal navy blue dresses from diverse regions?
Choose suppliers experienced with international shipping and capable of providing detailed documentation including commercial invoices, packing lists, and certificates of origin. Opt for freight forwarders familiar with your target markets to navigate customs efficiently. Consider Incoterms carefully; FOB (Free On Board) or CIF (Cost, Insurance, Freight) are common but clarify responsibilities for shipping and insurance. Plan for potential delays due to customs inspections, especially in regions with complex import regulations. -
What strategies can help resolve disputes related to product quality or delivery delays in international formal dress sourcing?
Establish clear contracts specifying quality benchmarks, delivery schedules, and penalties for non-compliance. Use third-party inspection services to verify product quality pre-shipment and document any discrepancies immediately. Maintain open communication and involve legal counsel familiar with international trade laws if disputes escalate. Leveraging platforms that offer dispute resolution or mediation can reduce risks. Build relationships with suppliers that prioritize transparency and responsiveness to minimize conflicts. -
How can I ensure sustainability and ethical compliance when sourcing formal navy blue dresses internationally?
Request detailed information on the supplier’s sustainability policies, including material sourcing, waste management, and labor practices. Verify certifications like GOTS or Fair Trade, which indicate environmentally and socially responsible production. Incorporate sustainability criteria into your supplier evaluation and audits. Buyers in Europe and the Middle East increasingly prioritize these factors due to regulatory and consumer pressures, so aligning with compliant suppliers can enhance brand reputation and market access.
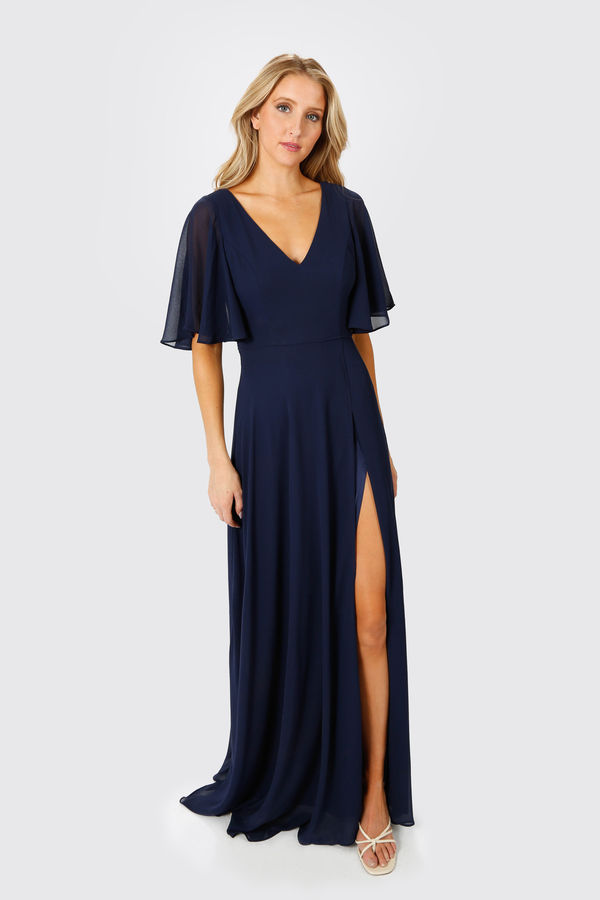
Illustrative Image (Source: Google Search)
Strategic Sourcing Conclusion and Outlook for formal navy blue dress
Strategic sourcing of formal navy blue dresses demands a comprehensive approach that balances quality, cost-efficiency, and supply chain agility. For international B2B buyers from Africa, South America, the Middle East, and Europe, prioritizing suppliers with strong compliance to sustainability and ethical manufacturing standards is increasingly critical. Leveraging advanced sourcing platforms and technology-driven solutions can help streamline procurement processes, reduce lead times, and improve inventory accuracy.
Key takeaways include the importance of:
– Supplier vetting and collaboration to ensure consistent quality and timely delivery.
– Customization capabilities that meet diverse market preferences and regional dress codes.
– Integration of digital tools such as AI-powered demand forecasting and supply chain visibility to mitigate risks and adapt swiftly to market shifts.
Looking ahead, the formal navy blue dress market will continue evolving alongside global fashion trends and regulatory demands. Buyers who embrace innovation, foster transparent supplier relationships, and align sourcing strategies with sustainability goals will unlock competitive advantages. Now is the time for international buyers to deepen partnerships, invest in technology-enabled sourcing, and confidently expand their product offerings to meet growing demand across their regions.
Seize this opportunity to elevate your sourcing strategy and secure a resilient, future-ready supply chain for formal navy blue dresses.