Your Ultimate Guide to Sourcing Fall Dresses Casual
Guide to Fall Dresses Casual
- Introduction: Navigating the Global Market for fall dresses casual
- Understanding fall dresses casual Types and Variations
- Key Industrial Applications of fall dresses casual
- Strategic Material Selection Guide for fall dresses casual
- In-depth Look: Manufacturing Processes and Quality Assurance for fall dresses casual
- Comprehensive Cost and Pricing Analysis for fall dresses casual Sourcing
- Spotlight on Potential fall dresses casual Manufacturers and Suppliers
- Essential Technical Properties and Trade Terminology for fall dresses casual
- Navigating Market Dynamics, Sourcing Trends, and Sustainability in the fall dresses casual Sector
- Frequently Asked Questions (FAQs) for B2B Buyers of fall dresses casual
- Strategic Sourcing Conclusion and Outlook for fall dresses casual
Introduction: Navigating the Global Market for fall dresses casual
In today’s dynamic fashion landscape, casual fall dresses have emerged as a pivotal category that blends comfort, style, and versatility—essential for retailers and distributors targeting diverse international markets. For B2B buyers across Africa, South America, the Middle East, and Europe, understanding the nuances of this segment is critical to capitalizing on seasonal demand while catering to evolving consumer preferences.
This guide offers a comprehensive roadmap for sourcing casual fall dresses, covering everything from trending dress types and fabric innovations to manufacturing best practices and quality control benchmarks. We delve into sourcing strategies tailored to varied regional tastes and climates, empowering buyers in markets like Italy and Kenya to select styles and materials that resonate locally yet maintain global appeal.
Key areas explored include:
– Diverse dress styles suitable for casual fall wear, emphasizing adaptability across different cultural contexts.
– Fabric selection, highlighting sustainable and climate-appropriate materials that balance quality with cost-efficiency.
– Manufacturing and quality assurance, detailing standards to ensure durability and customer satisfaction.
– Supplier evaluation, providing criteria to identify reliable partners capable of scalable production and timely delivery.
– Cost structures and pricing trends, enabling informed negotiation and margin optimization.
– Market insights and demand forecasts, helping buyers anticipate shifts and position their offerings competitively.
– FAQs addressing common sourcing challenges, from customs regulations to logistics considerations.
By synthesizing these critical dimensions, this guide equips international B2B buyers with actionable insights to make strategic, data-driven sourcing decisions—transforming casual fall dresses from mere inventory items into profitable, market-responsive assets.
Understanding fall dresses casual Types and Variations
Type Name | Key Distinguishing Features | Primary B2B Applications | Brief Pros & Cons for Buyers |
---|---|---|---|
Knit Sweater Dress | Soft knit fabric, often with ribbed texture | Casual retail, boutique stores, online platforms | Pros: Comfortable, versatile; Cons: Seasonal demand fluctuations, sizing variability |
Shirt Dress | Button-down front, collar, often cotton or flannel | Department stores, fashion chains, export markets | Pros: Classic style, easy to source; Cons: Fabric quality varies, requires size standardization |
Wrap Dress | Wrap-around design with adjustable tie closures | Specialty retailers, online boutiques | Pros: Adjustable fit, flattering for various body types; Cons: Higher production complexity, costlier |
Midi Dress | Mid-calf length, often with long sleeves | Mass market, fast fashion, export to diverse climates | Pros: Trendy, adaptable to layering; Cons: Fabric choice critical for fall season warmth |
Sweater Maxi Dress | Long length, knitted, often with turtleneck or cowl | Premium boutiques, colder climate markets | Pros: High perceived value, ideal for cold regions; Cons: Higher price point, niche market segment |
Knit Sweater Dress
Knit sweater dresses are a staple for fall casual wear, characterized by their soft, often ribbed knit fabric that provides warmth and comfort. These dresses appeal to buyers targeting markets with cooler fall climates, such as Europe and parts of the Middle East. For B2B buyers, sourcing consistent quality knit materials and managing seasonal inventory are key considerations. Their versatility allows retailers to market them across casual and semi-formal segments, enhancing product range appeal.
Shirt Dress
Shirt dresses offer a timeless look with button-down fronts and collars, frequently made from cotton or flannel blends suited for transitional fall weather. This type is widely accepted in department stores and fashion chains, making it a reliable product for bulk buyers. However, buyers must ensure fabric durability and maintain strict size standardization to meet diverse international market demands, especially in regions like South America and Africa where sizing preferences vary.
Wrap Dress
Wrap dresses stand out with their adjustable tie closures, providing a customizable fit attractive to a broad demographic. They are popular in specialty retail and online boutiques focused on flattering silhouettes. From a B2B perspective, the complexity of manufacturing wrap dresses requires careful supplier selection to ensure quality and cost efficiency. Their adaptable design also supports marketing strategies aimed at inclusivity and body positivity, which is a growing trend globally.
Midi Dress
Midi dresses, typically mid-calf length with long sleeves, blend style and practicality for fall. They are favored in mass market and fast fashion channels due to their on-trend appeal and suitability for layering. Buyers should prioritize fabric choices that balance breathability with warmth to cater to diverse climates, from the cooler zones of Europe to milder African markets. Efficient supply chain management is essential to capitalize on fast fashion cycles.
Sweater Maxi Dress
Sweater maxi dresses combine length and knit warmth, often featuring turtlenecks or cowls, making them ideal for premium and colder climate markets like Northern Europe and certain Middle Eastern regions. These dresses command a higher price point and cater to niche segments seeking luxury casual wear. B2B buyers should assess market readiness for premium pricing and focus on quality craftsmanship to justify costs, ensuring alignment with consumer expectations in targeted regions.
Related Video: Large Language Models (LLMs) – Everything You NEED To Know
Key Industrial Applications of fall dresses casual
Industry/Sector | Specific Application of fall dresses casual | Value/Benefit for the Business | Key Sourcing Considerations for this Application |
---|---|---|---|
Fashion Retail | Seasonal product lines for mid-range and premium brands | Drives seasonal sales, attracts diverse customer bases | Quality fabric sourcing, trend alignment, sustainable materials |
Hospitality & Tourism | Uniforms and casual wear for hotel staff and event hosts | Enhances brand image, comfort for employees | Durable fabrics, easy maintenance, culturally appropriate designs |
Corporate Gifting | Customized casual fall dresses for corporate gifts | Strengthens client relationships, brand promotion | Customization capabilities, timely delivery, ethical sourcing |
E-commerce Platforms | Curated fall casual dress collections for online sales | Expands market reach, personalized shopping experience | Reliable supplier partnerships, inventory flexibility, logistics efficiency |
Export & Wholesale | Bulk supply to boutiques and department stores | Economies of scale, consistent product availability | Compliance with international trade standards, cost-effective production |
Fall dresses casual play a pivotal role in fashion retail, especially for mid-range and premium brands targeting seasonal consumers. Retailers in Europe and South America benefit from sourcing high-quality fabrics that align with current fall trends, ensuring their collections meet customer expectations. For B2B buyers, prioritizing sustainable materials and trend responsiveness is crucial to maintaining competitive advantage and brand reputation.
In the hospitality and tourism sector, fall casual dresses are often used as staff uniforms, blending comfort with a professional yet approachable appearance. Hotels and event venues in regions like the Middle East and Africa value durable, easy-to-maintain fabrics that can withstand frequent use while respecting local cultural aesthetics. Buyers must focus on sourcing designs that balance style with practicality, ensuring employee comfort and brand consistency.
For corporate gifting, customized fall dresses offer a unique avenue for businesses to reinforce client relationships and promote their brand during autumn events. Companies in Europe and South America often look for suppliers capable of delivering bespoke designs with timely fulfillment. Ethical sourcing and customization flexibility are vital for buyers aiming to uphold corporate social responsibility while impressing recipients.
E-commerce platforms leverage curated collections of fall casual dresses to attract diverse international customers, enhancing personalized shopping experiences. Buyers, particularly from Africa and Europe, require dependable supplier partnerships that can adapt to fluctuating inventory demands and provide efficient logistics solutions. Ensuring a reliable supply chain is essential to meet consumer expectations and capitalize on seasonal demand spikes.
In export and wholesale, bulk purchasing of fall casual dresses enables boutiques and department stores to benefit from economies of scale and consistent product availability. International buyers from regions such as Kenya and Italy must ensure suppliers comply with trade regulations and offer cost-effective production without compromising quality. This balance supports sustainable growth and competitive pricing in their respective markets.
Related Video: LABORATORY APPARATUS AND THEIR USES
Strategic Material Selection Guide for fall dresses casual
Cotton: The Classic Choice for Casual Fall Dresses
Key Properties: Cotton is a natural fiber known for its breathability, moisture absorption, and moderate thermal insulation. It performs well in mild to cool temperatures typical of fall climates and offers good comfort against the skin. Cotton’s natural fibers provide flexibility and ease of dyeing, which is advantageous for diverse color palettes.
Pros & Cons: Cotton is highly durable with proper care, relatively cost-effective, and widely available globally. However, it wrinkles easily and can shrink if not pre-treated or blended with synthetic fibers. Manufacturing cotton garments is straightforward but requires attention to finishing processes to maintain softness and reduce pilling.
Impact on Application: Cotton’s moisture-wicking ability makes it suitable for fall dresses worn in transitional weather, especially in regions with fluctuating temperatures like parts of Europe and South America. It is compatible with various dyes and finishes, allowing for versatile design options.
International B2B Considerations: Buyers from Africa and the Middle East should verify cotton sourcing certifications (e.g., organic or fair trade) to meet growing consumer demand for sustainability. Compliance with standards such as OEKO-TEX and ASTM D123 is essential to ensure fabric safety and quality. Italian buyers often prefer premium combed or Egyptian cotton for higher-end casual wear, while Kenyan markets may prioritize durability and cost-efficiency.
Polyester: Durable and Cost-Effective Synthetic Option
Key Properties: Polyester is a synthetic fiber known for its high tensile strength, wrinkle resistance, and quick-drying properties. It maintains shape well under pressure and resists shrinking and stretching, making it suitable for mass production and long-lasting garments.
Pros & Cons: Polyester is generally less expensive than natural fibers and offers excellent durability and color retention. However, it has lower breathability and can feel less comfortable in warm or humid fall climates. Manufacturing complexity is moderate, with advanced knitting and weaving technologies required for quality finishes.
Impact on Application: Polyester blends are ideal for fall dresses intended for regions with variable humidity, such as parts of South America and the Middle East, where moisture management is critical. Its resistance to mildew and UV degradation also extends garment life in sunny climates.
International B2B Considerations: Buyers should ensure polyester fabrics comply with international standards like REACH (Europe) and ASTM for chemical safety. African markets might require blends to improve comfort, while European buyers, particularly in Italy, may demand higher-grade polyester blends with natural fibers for enhanced luxury appeal.
Wool Blends: Warmth with Style for Cooler Fall Days
Key Properties: Wool, especially merino or blended wool, offers superior insulation, moisture-wicking, and natural elasticity. It is highly resistant to wrinkles and maintains warmth even when damp, making it excellent for cooler fall climates.
Pros & Cons: Wool blends provide a premium feel and excellent thermal regulation but come at a higher cost and require more complex manufacturing processes, including careful handling to prevent shrinkage and felting. Durability depends on the blend ratio and finishing techniques.
Impact on Application: Wool blends are particularly suitable for European markets like Italy, where fall temperatures drop significantly, and consumers seek both style and functionality. In African and Middle Eastern markets, lightweight wool blends may be preferred for cooler evenings without overheating.
International B2B Considerations: Compliance with wool-specific standards such as Woolmark certification and ASTM D3776 is crucial. Buyers should also consider the environmental impact and traceability of wool sourcing, which is increasingly important across all regions.
Rayon (Viscose): Softness and Drapability for Casual Elegance
Key Properties: Rayon is a semi-synthetic fiber made from regenerated cellulose, offering excellent softness, breathability, and drape. It mimics natural fibers like silk or cotton but with a smoother finish and enhanced color vibrancy.
Pros & Cons: Rayon is cost-effective and versatile but tends to wrinkle easily and may lose strength when wet. It requires careful manufacturing to avoid shrinkage and maintain fabric integrity. It is less durable than polyester or wool blends but offers superior comfort.
Impact on Application: Rayon is ideal for fall dresses designed for indoor or mild outdoor wear, especially in markets where softness and aesthetic appeal are prioritized, such as Europe and South America. It suits layered outfits typical of transitional fall fashion.
International B2B Considerations: Buyers should verify compliance with environmental standards like OEKO-TEX and ensure sustainable sourcing of cellulose materials. In African and Middle Eastern markets, rayon’s breathability is a key selling point, but durability concerns may necessitate blends with synthetic fibers.
Material | Typical Use Case for fall dresses casual | Key Advantage | Key Disadvantage/Limitation | Relative Cost (Low/Med/High) |
---|---|---|---|---|
Cotton | Everyday casual dresses for mild to cool fall days | Breathable, comfortable, widely accepted | Prone to wrinkles and shrinkage | Medium |
Polyester | Durable, wrinkle-resistant dresses for humid climates | Cost-effective, shape retention | Less breathable, can feel synthetic | Low |
Wool Blends | Warm, stylish dresses for cooler fall temperatures | Excellent insulation and wrinkle resistance | Higher cost, complex manufacturing | High |
Rayon (Viscose) | Soft, drapey dresses for indoor or mild outdoor use | Softness and elegant drape | Less durable, wrinkles easily | Medium |
In-depth Look: Manufacturing Processes and Quality Assurance for fall dresses casual
Manufacturing Processes for Casual Fall Dresses: Key Stages and Techniques
The manufacturing of casual fall dresses involves a series of carefully coordinated stages designed to ensure quality, consistency, and efficiency. Understanding these stages equips B2B buyers with the knowledge to evaluate supplier capabilities and negotiate effectively.
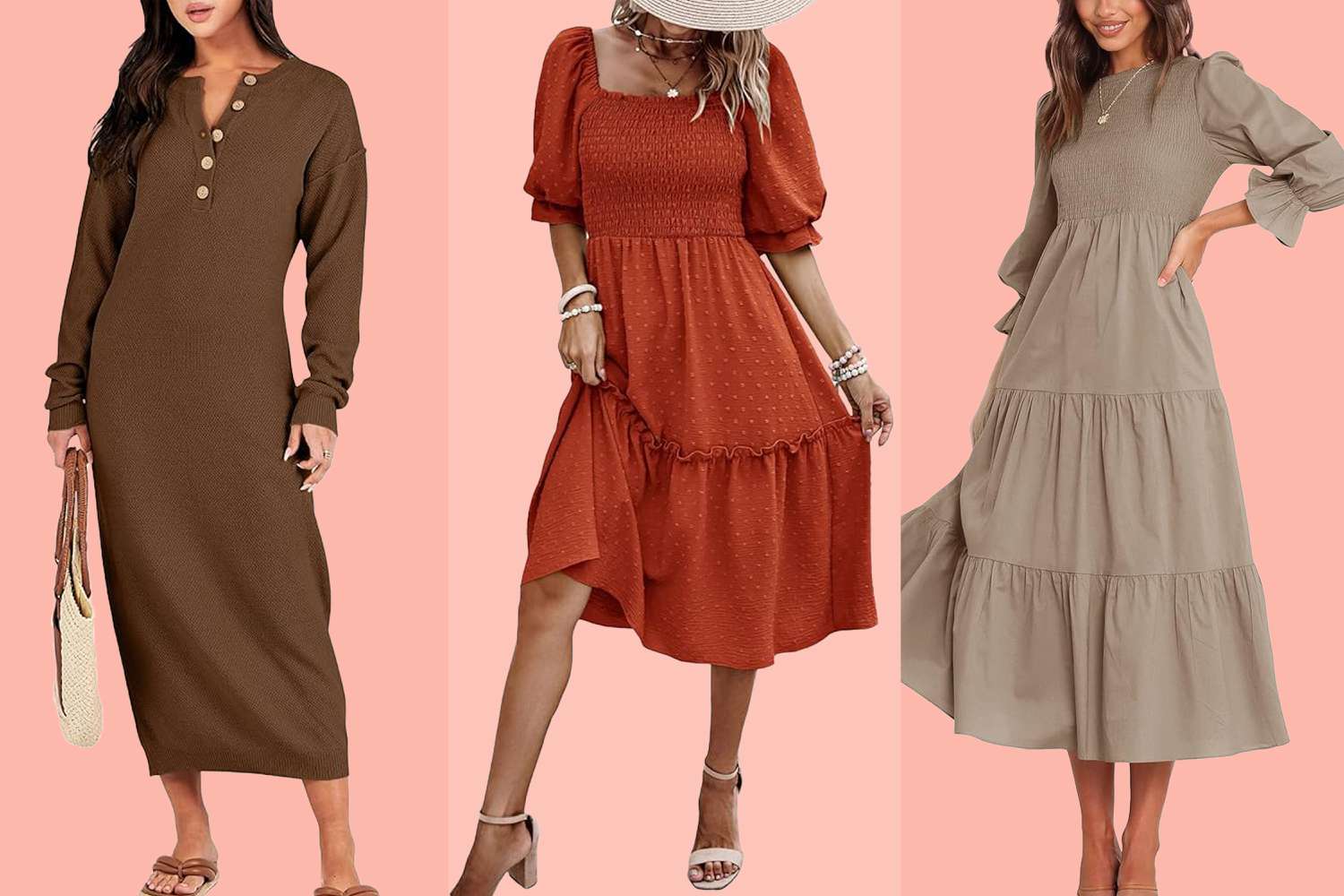
Illustrative Image (Source: Google Search)
1. Material Preparation
Material selection is critical, especially for fall dresses which typically use fabrics like cotton blends, wool knits, and synthetic fibers optimized for comfort and seasonal appropriateness. Material preparation includes:
- Fabric sourcing and inspection: Ensuring fabric meets specifications for weight, texture, and colorfastness.
- Pre-treatment: Processes such as washing, dyeing, or coating to enhance fabric performance and durability.
- Cutting: Using automated cutting machines or manual cutting tables to shape fabric pieces according to patterns.
2. Forming and Shaping
This stage involves converting flat fabric pieces into three-dimensional dress components.
- Pattern making: Precision in pattern design ensures fit and style consistency. Digital pattern-making tools are increasingly common for accuracy.
- Cutting and layering: Multiple layers are cut simultaneously to increase efficiency while maintaining precision.
- Shaping techniques: Includes pleating, gathering, and darts which define the dress silhouette.
3. Assembly
Assembly is the core production phase where components are stitched together.
- Sewing: High-quality stitching (lockstitch, overlock) is essential for durability and appearance.
- Incorporation of trims and details: Buttons, zippers, labels, and decorative elements are added here.
- Use of automated sewing machines: For consistent seam quality and faster throughput.
4. Finishing
Final touches enhance garment aesthetics and functionality.
- Pressing and steaming: Removes wrinkles and sets seams for a polished look.
- Quality checks: Preliminary inspections for defects such as loose threads or uneven stitching.
- Packaging: Includes tagging, folding, and protective wrapping tailored for international shipping standards.
Quality Assurance Frameworks and Checkpoints
Robust quality assurance (QA) is vital for maintaining product standards and building buyer confidence, especially in international markets where compliance varies.
International and Industry Standards
- ISO 9001: The globally recognized standard for quality management systems, emphasizing process control and continuous improvement. Buyers should verify suppliers’ ISO 9001 certification as a baseline quality assurance indicator.
- OEKO-TEX Standard 100: Relevant for textile safety, ensuring fabrics are free from harmful substances—important for markets with strict chemical regulations like the EU.
- Additional certifications: Depending on the target market, certifications like GOTS (organic textiles), WRAP (ethical manufacturing), and CE marking (for compliance in European markets) may be relevant.
Quality Control Checkpoints
- Incoming Quality Control (IQC): Inspection of raw materials (fabrics, trims) to ensure compliance with specifications before production starts. This reduces risks of defects downstream.
- In-Process Quality Control (IPQC): Ongoing monitoring during production stages, including stitch quality, seam strength, and dimensional accuracy. IPQC helps catch defects early and reduce rework costs.
- Final Quality Control (FQC): Comprehensive inspection of finished dresses, including visual checks for defects, measurement verification, and functional testing of closures and trims.
Common Testing Methods
- Dimensional and fit testing: Verifying that dress measurements align with size charts and fit standards.
- Colorfastness testing: Ensures colors do not bleed or fade under washing or exposure to sunlight.
- Tensile strength and seam durability tests: Measure the garment’s ability to withstand wear and tear.
- Pilling and abrasion resistance: Particularly important for knit fabrics used in fall dresses.
- Chemical testing: Confirms compliance with safety standards regarding dyes and finishes.
Practical Guidance for International B2B Buyers: Verifying Supplier Quality Control
For buyers from Africa, South America, the Middle East, and Europe, understanding how to validate a supplier’s QA processes is essential to mitigate risks and secure reliable partnerships.
1. Conduct On-Site Audits
Audits allow buyers to verify manufacturing capabilities, QC procedures, and working conditions firsthand. Focus areas include:
- Verification of ISO and other quality certifications.
- Observation of IQC, IPQC, and FQC checkpoints in action.
- Review of process documentation and traceability records.
2. Request Detailed QC Reports
Suppliers should provide transparent QC documentation, including:
- Fabric inspection reports with lab test results (e.g., colorfastness, chemical safety).
- In-process inspection logs showing defect rates and corrective actions.
- Final inspection reports with defect classification and batch acceptance criteria.
3. Utilize Third-Party Inspections
Independent inspection agencies provide unbiased verification of quality and compliance, offering services such as:
- Pre-shipment inspections to confirm order specifications before export.
- Random sample testing by accredited labs to validate fabric and garment properties.
- Social compliance audits ensuring ethical production practices.
4. Understand Regional QC Nuances
- Africa & South America: Suppliers may vary widely in QC maturity. Buyers should prioritize partners with international certifications and consider third-party audits to offset potential risks.
- Middle East: Buyers often demand adherence to strict chemical safety and modesty standards; ensure suppliers understand regional compliance and cultural requirements.
- Europe (e.g., Italy): High expectations for fit, finish, and sustainability certifications. Buyers should look for suppliers that integrate advanced quality management systems and eco-friendly practices.
Summary: Maximizing Value Through Manufacturing and Quality Assurance Insight
For international B2B buyers sourcing casual fall dresses, a deep understanding of manufacturing stages and quality assurance frameworks enables informed decision-making. Prioritizing suppliers with certified quality systems, transparent QC processes, and willingness to accommodate audits or third-party inspections reduces risk and ensures product consistency. Tailoring QC verification approaches to regional market requirements further strengthens supply chain reliability and buyer confidence.
Related Video: Amazing Garment Manufacturing Process from Fabric to Finished Product Inside the Factory
Comprehensive Cost and Pricing Analysis for fall dresses casual Sourcing
Breakdown of Cost Components in Casual Fall Dress Sourcing
When sourcing casual fall dresses for B2B transactions, understanding the cost structure is crucial for effective negotiation and budgeting. The primary cost components include:
- Materials: Fabric choice (e.g., cotton blends, knits, wool blends), trims, buttons, zippers, and labels significantly impact the base cost. Natural fibers or sustainable materials generally carry a premium.
- Labor: Wages vary widely by region; for example, manufacturing in parts of South Asia or Africa might offer lower labor costs compared to Europe. However, quality and compliance standards can affect labor expenses.
- Manufacturing Overhead: This includes factory utilities, equipment depreciation, and indirect labor. Efficient factories with modern machinery can reduce overhead per unit.
- Tooling: Initial setup costs such as pattern making, sample development, and cutting dies are typically amortized over production volume.
- Quality Control (QC): Inspections during and post-production ensure defect rates are minimized, which may involve third-party audits, especially for buyers requiring certifications.
- Logistics: Freight charges, customs duties, and inland transportation costs vary significantly depending on sourcing location and delivery terms.
- Margin: Suppliers incorporate their profit margin, influenced by market demand, competition, and order size.
Key Pricing Influencers for Fall Dress Orders
Several factors shape the final price offered by manufacturers and suppliers:
- Order Volume / Minimum Order Quantity (MOQ): Larger orders usually yield better per-unit pricing due to economies of scale. Buyers from smaller markets like Kenya or niche retailers in Europe might face higher per-unit costs due to lower volumes.
- Specifications and Customization: Complex designs, embroidery, prints, or additional embellishments increase production time and material costs.
- Material Quality and Certifications: Dresses made with organic or certified sustainable fabrics command higher prices but appeal to eco-conscious markets.
- Supplier Capabilities: Established suppliers with advanced manufacturing capabilities and certifications (e.g., ISO, SA8000) often charge premiums but reduce risk.
- Incoterms: The chosen delivery terms (FOB, CIF, DDP) significantly affect logistics costs and risk allocation, impacting landed cost calculations.
Practical Tips for International B2B Buyers
For buyers in Africa, South America, the Middle East, and Europe, strategic sourcing and cost management are key to maximizing profitability:
- Negotiate Based on Total Cost of Ownership: Look beyond unit price. Factor in shipping, customs, inventory holding, and potential rework costs. For instance, sourcing from Asia might have low unit costs but higher logistics and lead times.
- Leverage Volume Commitments: Pooling orders with other buyers or committing to higher volumes can unlock discounts. Regional buying groups or trade associations may facilitate this.
- Assess Supplier Reliability and Compliance: Prioritize suppliers with consistent quality and adherence to labor and environmental standards, reducing risk of costly returns or reputational damage.
- Understand Pricing Nuances by Region: For example, European buyers (Italy) often prioritize quality and compliance, accepting higher prices, while buyers in Kenya or Brazil might focus on balancing cost with acceptable quality.
- Clarify Incoterms Early: Define responsibilities clearly to avoid unexpected customs fees or delays. DDP terms reduce buyer hassle but come at a premium.
- Request Detailed Cost Breakdowns: Transparent pricing helps identify negotiation levers, such as material substitutions or production efficiencies.
Disclaimer on Pricing
Prices for casual fall dresses vary widely depending on design complexity, sourcing region, order volume, and market conditions. The cost insights provided serve as indicative guidance to assist B2B buyers in making informed sourcing decisions. Actual quotes should be obtained directly from suppliers and verified through sampling and due diligence.
Spotlight on Potential fall dresses casual Manufacturers and Suppliers
This section offers a look at a few manufacturers active in the ‘fall dresses casual’ market. This is a representative sample for illustrative purposes; B2B buyers must conduct their own extensive due diligence before any engagement. Information is synthesized from public sources and general industry knowledge.
Essential Technical Properties and Trade Terminology for fall dresses casual
Key Technical Properties for Fall Casual Dresses
Understanding the technical properties of fall casual dresses is crucial for international B2B buyers to ensure product quality, consistency, and customer satisfaction across diverse markets such as Africa, South America, the Middle East, and Europe.
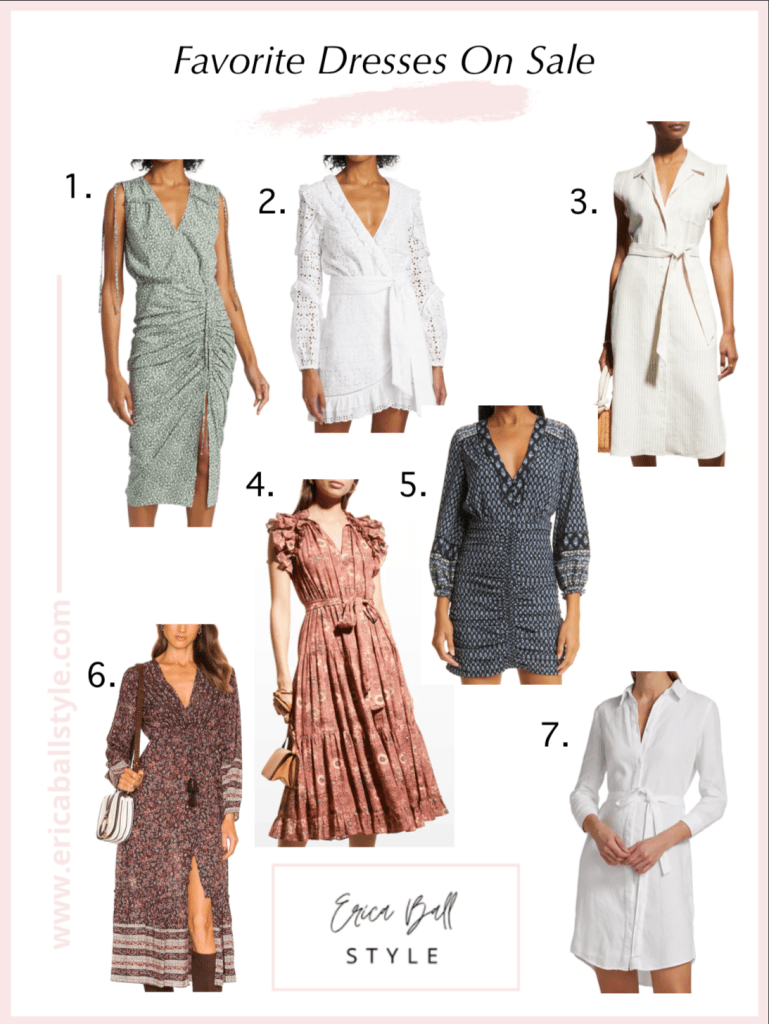
Illustrative Image (Source: Google Search)
1. Fabric Composition and Grade
The fabric blend (e.g., cotton-polyester mix, viscose, wool blends) directly impacts comfort, durability, and seasonal suitability. High-grade fabrics ensure better color retention and resistance to pilling, essential for fall wear which demands warmth and softness. Buyers should verify fabric certifications and request fabric swatches to assess quality before bulk orders.
2. Colorfastness
Colorfastness measures the fabric’s resistance to fading or bleeding during washing and exposure to sunlight. For fall dresses, rich, deep colors are popular, so ensuring strong colorfastness ratings prevents customer returns and maintains brand reputation. Specify minimum colorfastness grades (often rated 1-5) in contracts.
3. Size Tolerance and Fit Consistency
Tolerance refers to the acceptable variation in garment measurements (e.g., length, bust, waist) from the specified size chart. For casual dresses, tight tolerance (±1-2 cm) is vital to meet customer expectations globally, where sizing standards may differ. Clear size grading rules reduce returns and improve buyer confidence.
4. Stitching and Seam Strength
Robust stitching with reinforced seams is critical for durability, especially in casual wear subjected to frequent use. Buyers should request information on stitch type (e.g., lockstitch, overlock) and thread quality. Seam strength tests can be requested to ensure the garment withstands wear and washing cycles.
5. Fabric Weight and Thickness
Fabric weight (measured in grams per square meter, GSM) affects the dress’s warmth and drape. Fall dresses typically require medium-weight fabrics (150-250 GSM) to balance comfort and insulation. Buyers should specify GSM ranges to suppliers to align with local climate preferences.
6. Care Instructions Compatibility
Understanding the recommended care (machine wash, dry clean, hand wash) is important as it influences customer satisfaction and resale potential. Durable, easy-care fabrics are preferred in many markets to reduce returns and enhance convenience.
Essential Trade Terminology for Fall Casual Dresses
Navigating international apparel sourcing requires familiarity with common industry terms. Below are key trade terms every B2B buyer should know:
1. OEM (Original Equipment Manufacturer)
OEM refers to suppliers who produce garments based on the buyer’s design specifications and branding. This allows buyers to create unique fall dress collections tailored to their target markets, enhancing competitiveness.
2. MOQ (Minimum Order Quantity)
MOQ is the smallest order volume a supplier is willing to produce. Understanding MOQ helps buyers plan inventory and manage costs effectively. Some suppliers offer flexible MOQs for new designs or smaller markets, which can be advantageous for testing demand.
3. RFQ (Request for Quotation)
An RFQ is a formal document sent to suppliers to obtain pricing, lead times, and terms for a specific product. Well-prepared RFQs with detailed technical specifications minimize misunderstandings and expedite sourcing decisions.
4. Incoterms (International Commercial Terms)
Incoterms define the responsibilities of buyers and sellers regarding shipping, insurance, and customs clearance. Common terms include FOB (Free on Board) and CIF (Cost, Insurance, Freight). Knowing Incoterms helps buyers manage logistics costs and risks efficiently.
5. Lead Time
Lead time is the duration from order confirmation to product delivery. For fall dresses, aligning lead times with seasonal demand cycles is crucial to avoid stockouts or overstocking. Buyers should negotiate clear lead times and penalties for delays.
6. Sampling
Sampling involves producing a prototype garment before mass production. This step allows buyers to verify quality, fit, and design accuracy, reducing costly errors in large orders.
By mastering these technical properties and trade terms, international B2B buyers can make informed decisions, optimize sourcing strategies, and build reliable supplier partnerships for fall casual dresses. This knowledge is particularly valuable when catering to diverse markets with varying climate and consumer preferences.
Navigating Market Dynamics, Sourcing Trends, and Sustainability in the fall dresses casual Sector
Market Overview & Key Trends
The global market for casual fall dresses is experiencing robust growth, driven by evolving consumer preferences for versatile, comfortable, yet stylish apparel. Key markets such as Europe (notably Italy), the Middle East, Africa (with emerging hubs like Kenya), and South America are witnessing increased demand for seasonal wardrobe staples that balance fashion with functionality. This trend is propelled by urbanization, rising disposable incomes, and a growing middle class eager to adopt global fashion trends adapted for local climates.
For international B2B buyers, understanding regional nuances is critical. In Europe, particularly Italy, there is strong emphasis on craftsmanship, fabric quality, and trend-forward designs that blend classic autumnal palettes with contemporary cuts. Meanwhile, African markets favor breathable, easy-to-maintain fabrics suitable for transitional weather, often incorporating vibrant patterns that resonate culturally. South American buyers increasingly seek sustainable and ethically produced lines, aligning with rising environmental awareness, while Middle Eastern buyers prioritize modest yet fashionable options, often requiring longer hemlines and sleeves.
Technological advancements are reshaping sourcing and supply chain management in this sector. Digital platforms enable buyers to connect directly with manufacturers offering quick turnaround times and customizable designs. AI-driven trend forecasting tools help suppliers anticipate seasonal demands, reducing overstock and waste. Additionally, nearshoring and diversified supplier bases are emerging as strategies to mitigate geopolitical risks and shipping delays, which have been exacerbated by recent global disruptions.
In terms of sourcing, there is a growing preference for suppliers who can provide end-to-end transparency, from raw material procurement to finished product delivery. This is especially relevant for buyers focused on sustainability and ethical compliance, which are becoming non-negotiable criteria in supplier selection.
Sustainability & Ethical Sourcing in B2B
Sustainability has become a pivotal factor in the sourcing of casual fall dresses, with B2B buyers increasingly demanding environmentally responsible practices. The textile and apparel industry is one of the largest contributors to pollution and water consumption, making the adoption of green materials and sustainable manufacturing processes essential. Eco-friendly fibers such as organic cotton, Tencel, and recycled polyester are gaining traction for their reduced environmental footprint.
Ethical sourcing extends beyond materials to encompass fair labor practices and transparent supply chains. Buyers from regions like Europe and South America are particularly vigilant about certifications that validate these claims, such as GOTS (Global Organic Textile Standard), OEKO-TEX, and Fair Trade. These certifications assure compliance with environmental and social standards, which is crucial for maintaining brand reputation and meeting regulatory requirements.
For B2B buyers in Africa and the Middle East, integrating sustainability can also mean supporting local textile industries that promote circular economy principles and reduce carbon footprints by minimizing long-distance shipping. Collaborative partnerships with suppliers who invest in renewable energy, water-saving technologies, and waste reduction initiatives are increasingly preferred.
Furthermore, sustainability in packaging and logistics is gaining importance, with buyers seeking suppliers who use biodegradable or recyclable packaging materials and optimize shipping routes to reduce emissions. This holistic approach to sustainability not only addresses environmental concerns but also aligns with the values of end consumers, ultimately driving market competitiveness.
Brief Evolution of Casual Fall Dresses in B2B Context
The casual fall dress segment has evolved from simple, functional garments into a dynamic category reflecting broader fashion and societal shifts. Historically, fall dresses were primarily wool or heavy fabrics designed for warmth, with limited style variation. However, globalization and advances in textile technology have expanded fabric options and design innovations, enabling lightweight, layered, and multifunctional dresses suitable for diverse climates.
From a B2B perspective, the evolution is marked by the integration of trend responsiveness and sustainability. Early sourcing models focused on volume and cost-efficiency, often at the expense of quality and ethical considerations. Today, international buyers demand agility from suppliers to quickly adapt to seasonal trends while adhering to stringent sustainability standards. This has driven investments in supply chain digitization, ethical certifications, and eco-friendly materials, reflecting a mature market that balances commercial viability with corporate responsibility.
This historical progression underscores the importance for B2B buyers to partner with suppliers who not only understand fashion cycles but also prioritize transparency and sustainability to meet the complex demands of the modern global marketplace.
Related Video: Fall 2024 Fashion Trends NEW THIS SEASON
Frequently Asked Questions (FAQs) for B2B Buyers of fall dresses casual
-
How can I effectively vet suppliers of casual fall dresses for international markets?
Begin by verifying the supplier’s business licenses, certifications, and export history, especially their experience with markets like Africa, South America, the Middle East, and Europe. Request samples to assess fabric quality and craftsmanship. Use third-party inspection services to audit factories for compliance with labor and environmental standards. Check references from other international buyers and review online feedback. Prioritize suppliers who demonstrate transparency, responsiveness, and flexibility to local market preferences, ensuring reliable long-term partnerships. -
What customization options are typically available for casual fall dresses when ordering in bulk?
Most manufacturers offer customization including fabric choice, color palettes, sizing adjustments, label branding, and packaging. Some suppliers also accommodate design modifications such as sleeve length or neckline styles to suit regional preferences. It’s essential to discuss your target market’s climatic and cultural needs upfront. Confirm minimum order quantities (MOQs) for custom designs and prototype lead times. Collaborating early with your supplier on tech packs and samples ensures the final product aligns with your brand and customer expectations. -
What are the standard minimum order quantities (MOQs) and lead times for fall dress bulk orders?
MOQs vary widely but typically range from 100 to 500 pieces per style, depending on the supplier’s scale and customization level. Lead times usually span 30 to 60 days, factoring in design finalization, production, and quality checks. International buyers should plan for additional time due to shipping and customs clearance. Negotiate MOQs by consolidating multiple SKUs or colors to optimize costs. Early communication about delivery schedules helps mitigate delays and supports seasonal inventory planning. -
Which payment terms are most secure and practical for international B2B transactions in fall dress sourcing?
Common payment methods include letters of credit (LC), telegraphic transfers (T/T), and escrow services. Letters of credit provide strong security by involving banks to guarantee payment upon meeting agreed conditions, suitable for new supplier relationships. Established buyers may negotiate partial upfront deposits with balance upon shipment. Always clarify currency, payment milestones, and penalties for late payment in contracts. Utilizing reputable payment platforms with buyer protection mechanisms reduces financial risks in cross-border deals. -
What quality assurance certifications should I look for in casual fall dress suppliers?
Seek suppliers with certifications such as ISO 9001 for quality management, OEKO-TEX Standard 100 for textile safety, and WRAP or SA8000 for ethical manufacturing practices. These certifications ensure compliance with international standards and reassure buyers about product safety, sustainability, and labor conditions. For European markets, compliance with REACH regulations on chemical use is critical. Request third-party lab test reports for fabric durability and colorfastness to prevent post-import quality issues. -
How can I optimize logistics and shipping when importing casual fall dresses internationally?
Choose suppliers experienced with your target region’s import regulations and preferred shipping methods (sea freight, air freight, or express courier). Consolidate shipments to reduce costs but balance with inventory turnover needs. Clarify Incoterms (e.g., FOB, CIF) to understand responsibilities and risks during transit. Partnering with freight forwarders familiar with customs clearance in Africa, South America, the Middle East, and Europe can streamline processes. Plan for potential delays during peak seasons and allocate buffer time in your supply chain. -
What steps should I take if there is a dispute or product quality issue with a supplier?
Immediately document the issue with photos and detailed descriptions. Refer to your contract’s terms regarding quality standards, dispute resolution, and warranties. Engage in prompt communication with the supplier to negotiate remedies such as replacements, discounts, or refunds. If unresolved, consider mediation or arbitration clauses stipulated in your agreement. Maintaining professional and clear records throughout the process strengthens your position. Building strong relationships and clear contracts upfront reduces the likelihood of disputes. -
How can I stay competitive in my local market when sourcing casual fall dresses internationally?
Focus on identifying unique design elements and fabric innovations that resonate with your regional consumers. Leverage supplier flexibility to create localized styles or limited editions. Optimize pricing by negotiating MOQs and payment terms, and streamline logistics to reduce lead times. Invest in quality assurance to maintain brand reputation and minimize returns. Additionally, stay informed on market trends and competitor offerings in your region to adapt quickly. Strong supplier collaboration and market insights are key to sustained competitiveness.
Strategic Sourcing Conclusion and Outlook for fall dresses casual
Strategic sourcing in the casual fall dress segment offers international B2B buyers a unique opportunity to balance quality, cost-efficiency, and market responsiveness. Key takeaways emphasize the importance of partnering with suppliers who demonstrate flexibility in design adaptation, sustainable production practices, and reliable delivery timelines. Buyers from regions such as Africa, South America, the Middle East, and Europe must prioritize sourcing strategies that align with evolving consumer preferences and regional market dynamics.
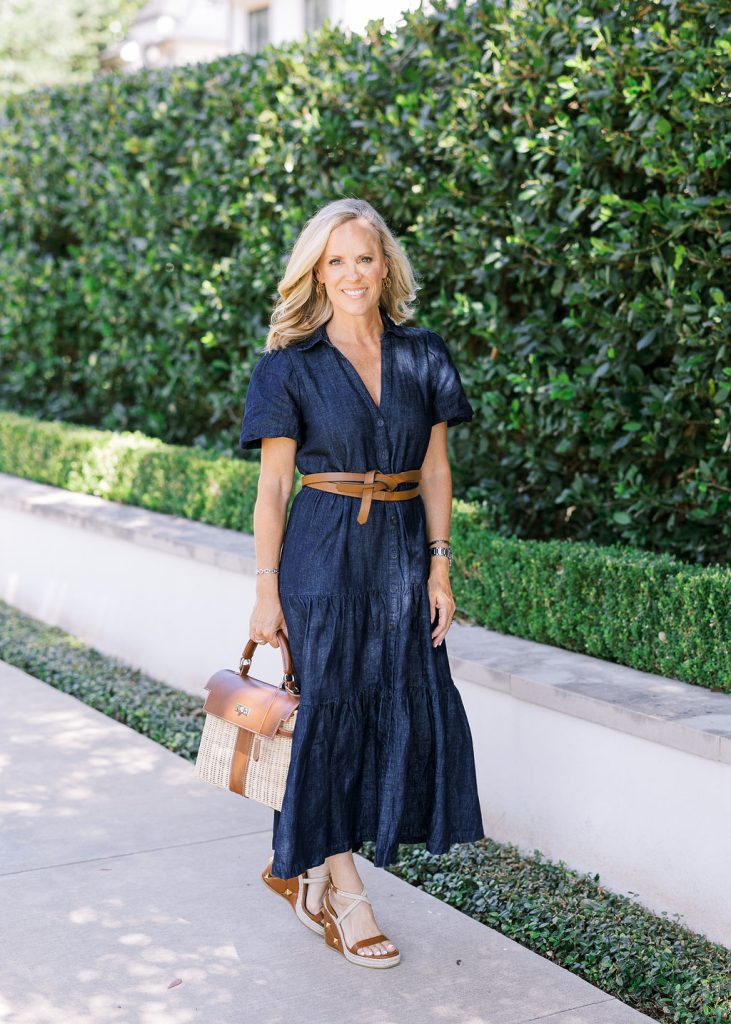
Illustrative Image (Source: Google Search)
Key considerations include:
– Supplier diversity: Engaging with manufacturers across multiple geographies to mitigate risks and leverage local expertise.
– Material innovation: Focusing on eco-friendly and durable fabrics that appeal to conscious consumers while ensuring product longevity.
– Supply chain transparency: Establishing clear communication channels and traceability to enhance trust and compliance.
Looking ahead, the casual fall dress market will continue to evolve with an emphasis on sustainability and digital integration. International buyers are encouraged to adopt a proactive sourcing approach—investing in collaborative supplier relationships and leveraging data-driven insights to anticipate trends. By doing so, businesses in Italy, Kenya, and beyond can secure competitive advantages and respond agilely to market shifts, driving growth and long-term success in the global fashion landscape.