Definitive Guide to Sourcing Utility Dress for Durable,
Guide to Utility Dress
- Introduction: Navigating the Global Market for utility dress
- Understanding utility dress Types and Variations
- Key Industrial Applications of utility dress
- Strategic Material Selection Guide for utility dress
- In-depth Look: Manufacturing Processes and Quality Assurance for utility dress
- Comprehensive Cost and Pricing Analysis for utility dress Sourcing
- Spotlight on Potential utility dress Manufacturers and Suppliers
- Essential Technical Properties and Trade Terminology for utility dress
- Navigating Market Dynamics, Sourcing Trends, and Sustainability in the utility dress Sector
- Frequently Asked Questions (FAQs) for B2B Buyers of utility dress
- Strategic Sourcing Conclusion and Outlook for utility dress
Introduction: Navigating the Global Market for utility dress
In today’s fast-evolving global apparel landscape, the utility dress stands out as a versatile, functional garment that meets diverse market demands—from corporate uniforms to casual workwear. For international B2B buyers, particularly those operating in dynamic regions such as Africa, South America, the Middle East, and Europe, sourcing the right utility dress is not just about aesthetics but about durability, comfort, and cost-efficiency. These factors are pivotal to maintaining competitive advantage and fulfilling customer expectations in varied climatic and cultural contexts.
This comprehensive guide is designed to empower buyers with actionable insights across the entire sourcing journey. It covers essential topics including the diverse types of utility dresses, key material selections tailored for durability and climate adaptability, and critical manufacturing and quality control standards that ensure product consistency. Additionally, it offers detailed analysis of global supplier landscapes, cost structures, and market trends—equipping buyers with the knowledge to negotiate effectively and minimize risks.
By understanding these components, international buyers—from Kenya’s emerging markets to the UK’s established retail sectors—can make informed, strategic decisions that align with their business goals. Whether you seek to optimize supply chains, ensure sustainable sourcing, or respond swiftly to market demands, this guide provides the expert framework necessary to navigate the complex global market for utility dresses with confidence and success.
Understanding utility dress Types and Variations
Type Name | Key Distinguishing Features | Primary B2B Applications | Brief Pros & Cons for Buyers |
---|---|---|---|
Classic Workwear Dress | Durable fabrics, simple cuts, often with pockets and belts | Industrial workers, maintenance staff | Pros: High durability, practical; Cons: Limited style variety, heavier weight |
Protective Utility Dress | Integrated safety features like flame retardancy or high-visibility strips | Construction, oil & gas, electrical sectors | Pros: Enhances worker safety; Cons: Higher cost, may reduce comfort |
Multi-pocket Utility Dress | Numerous functional pockets and compartments | Field engineers, technicians, logistics | Pros: Excellent storage, convenience; Cons: Can appear bulky, complex design |
Lightweight Utility Dress | Breathable fabrics, ergonomic design for mobility | Retail, hospitality, healthcare | Pros: Comfort and flexibility; Cons: Less protective, may wear out faster |
Modular Utility Dress | Interchangeable components (e.g., detachable sleeves, adjustable length) | Military, emergency services | Pros: Versatile and adaptable; Cons: More expensive, complex maintenance |
Classic Workwear Dress
This type is characterized by its robust construction using heavy-duty fabrics such as canvas or denim, designed to withstand harsh working environments. It typically features straightforward cuts and practical elements like belts and reinforced seams. Ideal for industries such as manufacturing and maintenance, it emphasizes durability over style. B2B buyers should consider fabric quality and ease of repair to maximize lifecycle and reduce replacement costs.
Protective Utility Dress
Equipped with safety enhancements such as flame-resistant materials, reflective strips, or electrical hazard protection, these dresses serve critical roles in high-risk environments like construction sites or oil refineries. Buyers must prioritize compliance with international safety standards and certifications relevant to their industry, balancing protection with wearer comfort to ensure adoption and effectiveness.
Multi-pocket Utility Dress
Designed for professionals requiring quick access to tools and devices, this variant includes multiple pockets, loops, and compartments. It suits roles like field engineers or logistics coordinators who benefit from hands-free storage. When sourcing, buyers should evaluate pocket placement ergonomics and overall garment weight to avoid mobility impairment.
Lightweight Utility Dress
Made from breathable, moisture-wicking fabrics, these dresses focus on comfort and ease of movement, making them suitable for sectors such as hospitality or healthcare where long hours and agility are essential. Buyers should assess fabric performance under various conditions and consider the trade-off between comfort and durability for their specific operational context.
Modular Utility Dress
Featuring customizable components like detachable sleeves or adjustable lengths, modular dresses offer adaptability for varying climates and tasks, favored by military and emergency response teams. For B2B buyers, the complexity of maintenance and higher initial investment must be weighed against the versatility and potential cost savings from reduced uniform inventories.
Related Video: All Machine Learning Models Explained in 5 Minutes | Types of ML Models Basics
Key Industrial Applications of utility dress
Industry/Sector | Specific Application of utility dress | Value/Benefit for the Business | Key Sourcing Considerations for this Application |
---|---|---|---|
Manufacturing | Protective workwear for assembly line workers | Enhances worker safety, reduces downtime due to injuries | Durable fabrics, compliance with safety standards, breathability |
Construction | Heavy-duty utility garments for site laborers | Protection against hazards, weather resistance, durability | High abrasion resistance, weatherproofing, ergonomic design |
Healthcare | Sterile utility dress for medical personnel | Infection control, comfort during long shifts | Antimicrobial materials, ease of sterilization, comfort fit |
Oil & Gas | Flame-resistant utility clothing for field workers | Minimizes fire risk, complies with industry safety regulations | Flame retardant certification, chemical resistance, durability |
Logistics & Warehousing | High-visibility utility dress for warehouse staff | Improves visibility, reduces accidents, enhances workflow | Reflective materials, lightweight, durable, easy maintenance |
Manufacturing
In manufacturing environments, utility dress serves as essential protective workwear for assembly line operators and machine handlers. These garments must balance durability with comfort to prevent injuries from sharp objects, machinery, and repetitive tasks. For international B2B buyers, especially in regions like Kenya or the UK, sourcing utility dress with certified safety standards and breathable fabrics is critical. This ensures compliance with local labor laws and enhances productivity by reducing worker fatigue.
Construction
Construction workers require heavy-duty utility dress that offers protection from physical hazards such as sharp tools, debris, and exposure to adverse weather. Utility garments designed for this sector prioritize abrasion resistance, waterproofing, and ergonomic fit to support long hours on site. For buyers in the Middle East or South America, where climates can be extreme, sourcing utility dress with weatherproofing and UV protection is essential to maintain workforce safety and operational continuity.
Healthcare
In healthcare, utility dress is used as sterile uniforms or scrubs that protect both medical staff and patients by controlling infection. These garments must be easy to sterilize, antimicrobial, and comfortable for extended wear. International buyers in Europe and Africa should focus on sourcing utility dress that meets stringent hygiene standards and offers moisture-wicking properties to support demanding hospital environments while ensuring compliance with healthcare regulations.
Oil & Gas
The oil and gas industry demands flame-resistant utility dress to protect workers from fire and chemical hazards. These garments must meet rigorous safety certifications such as NFPA or EN standards, and offer resistance to chemicals and extreme conditions. Buyers from regions with growing oil sectors like the Middle East or South America should prioritize sourcing utility dress with proven flame retardant properties and durability to safeguard personnel and reduce liability risks.
Logistics & Warehousing
Utility dress in logistics and warehousing focuses on high-visibility clothing that enhances worker safety by reducing the risk of accidents in busy environments. Reflective strips and bright colors improve visibility in low-light conditions, while lightweight, durable fabrics ensure comfort and longevity. B2B buyers in Europe and Africa should consider sourcing utility dress that complies with occupational safety standards and supports efficient warehouse operations through ergonomic design and easy maintenance.
Related Video: Uses and Gratifications Theory
Strategic Material Selection Guide for utility dress
Material Analysis for Utility Dress Selection
1. Cotton Twill
Key Properties:
Cotton twill is a durable woven fabric known for its diagonal weave pattern, providing strength and resistance to wear. It offers good breathability and moderate moisture absorption, making it suitable for warm climates. Its temperature tolerance is moderate, generally comfortable up to 60°C in washing and usage.
Pros & Cons:
Cotton twill is highly durable and comfortable, making it ideal for utility dresses requiring frequent wear. It is cost-effective and widely available, simplifying sourcing. However, it wrinkles easily and can shrink if not pre-treated. Its natural fibers are prone to mildew in humid environments unless treated.
Impact on Application:
Cotton twill is well-suited for environments with moderate physical activity and where breathability is crucial, such as in Africa or South America. It performs less well in highly corrosive or chemical-laden environments due to fiber degradation.
International B2B Considerations:
Buyers in Europe and the UK often require compliance with OEKO-TEX or GOTS certifications for organic cotton to meet sustainability standards. In the Middle East and Africa, durability and ease of maintenance are prioritized, with a preference for pre-shrunk and treated cotton to avoid shrinkage and mildew. ASTM standards for fabric strength and colorfastness are commonly referenced.
2. Polyester-Cotton Blend (Poly-Cotton)
Key Properties:
This synthetic-natural blend combines the strength and wrinkle resistance of polyester with the comfort of cotton. It offers higher abrasion resistance and better moisture-wicking than pure cotton. It is resistant to shrinking and stretching, with good dimensional stability.
Pros & Cons:
Poly-cotton blends are cost-efficient and easier to maintain, with less ironing required. They dry faster and resist mildew better than pure cotton. However, polyester content can reduce breathability and may cause discomfort in hot, humid climates if used in high percentages.
Impact on Application:
Ideal for utility dresses used in environments requiring durability and moderate protection from environmental factors. Suitable for industrial or service sectors in Europe and the Middle East, where maintenance ease and longevity are critical.
International B2B Considerations:
Buyers should verify blend ratios to balance comfort and durability. Compliance with REACH and EU textile regulations is essential for European markets. In South America and Africa, local climatic conditions may favor lower polyester content to enhance breathability. Sourcing from suppliers with transparent supply chains is advantageous.
3. Ripstop Nylon
Key Properties:
Ripstop nylon is a lightweight synthetic fabric with a distinctive grid pattern that prevents tearing. It is highly resistant to abrasion, water, and chemicals, with excellent tensile strength and quick-drying properties. It tolerates a wide temperature range and resists UV degradation.
Pros & Cons:
Its durability and resistance to harsh conditions make it ideal for utility dresses used in outdoor or industrial settings. It is lightweight and easy to clean. However, ripstop nylon can be less breathable and may cause discomfort in hot climates unless ventilated.
Impact on Application:
Best suited for utility dresses in environments with exposure to moisture, chemicals, or rough handling—common in Middle Eastern industrial sectors or European outdoor workwear. Its water resistance is beneficial in humid or rainy regions like parts of South America.
International B2B Considerations:
Buyers should ensure compliance with international standards such as ISO for fabric strength and water resistance. Certifications related to flame retardancy or chemical resistance may be required depending on end-use. Consider environmental impact and recycling options, especially for European clients emphasizing sustainability.
4. Canvas (Heavyweight Cotton or Cotton Blend)
Key Properties:
Canvas is a heavy-duty fabric known for its ruggedness and resistance to wear and tear. It offers excellent durability and moderate breathability, with good resistance to physical abrasion and some chemical exposure. It can be treated for water and stain resistance.
Pros & Cons:
Canvas utility dresses provide superior protection and longevity, suitable for heavy industrial or manual labor environments. The fabric can be stiff and less comfortable without proper finishing. It is heavier and may retain heat, which could be a limitation in hot climates.
Impact on Application:
Ideal for utility dresses in sectors requiring robust protection, such as construction or agriculture in Africa and South America. Its weight and durability make it less suitable for hot, humid environments unless ventilated or blended with lighter fibers.
International B2B Considerations:
Buyers should request compliance with ASTM or DIN standards for fabric weight and tensile strength. In Europe and the UK, eco-friendly treatments and certifications are increasingly important. For Middle Eastern markets, water and stain resistance treatments enhance usability.
Summary Table of Utility Dress Materials
Material | Typical Use Case for utility dress | Key Advantage | Key Disadvantage/Limitation | Relative Cost (Low/Med/High) |
---|---|---|---|---|
Cotton Twill | General-purpose utility wear in moderate climates | Comfortable, breathable, cost-effective | Prone to shrinkage and mildew | Low |
Polyester-Cotton Blend | Industrial and service sectors requiring durability | Durable, wrinkle-resistant, easy care | Reduced breathability, may be less comfy | Medium |
Ripstop Nylon | Outdoor, chemical-exposed, or wet environments | Tear-resistant, water and chemical resistant | Less breathable, potential heat retention | Medium to High |
Canvas (Heavyweight Cotton or Blend) | Heavy-duty industrial and manual labor applications | Extremely durable and protective | Heavy, less comfortable in hot climates | Medium |
In-depth Look: Manufacturing Processes and Quality Assurance for utility dress
Manufacturing Processes for Utility Dress: Key Stages and Techniques
The production of utility dresses, designed primarily for functionality, durability, and cost-efficiency, involves a structured manufacturing process that ensures consistent quality and performance. Understanding these stages helps B2B buyers from diverse international markets make informed sourcing decisions.
1. Material Preparation
This initial phase focuses on selecting and preparing raw materials, which typically include durable fabrics such as cotton blends, polyester, or technical textiles depending on the utility requirements. Fabric inspection for defects, pre-shrinking, and color consistency verification are critical here. For buyers in regions like Africa and South America, sourcing suppliers that offer materials compliant with regional climate and wear conditions is crucial.
2. Cutting and Forming
Accurate cutting of fabric components using manual or automated cutting machines (e.g., CAD/CAM systems) ensures minimal waste and precision in garment size. Forming may involve pleating, folding, or shaping fabric panels to meet design specifications. Advanced laser cutting or die-cutting techniques can enhance precision for bulk orders, which is beneficial for buyers requiring large, consistent batches.
3. Assembly and Stitching
Assembly involves stitching cut components into the final garment. For utility dresses, reinforced stitching techniques such as double stitching, bartacking at stress points, and seam sealing are employed to enhance durability. Automated sewing machines and skilled labor are combined to maintain quality and efficiency. Buyers in the Middle East and Europe often prioritize suppliers who demonstrate consistent workmanship and compliance with ergonomic sewing standards.
4. Finishing Processes
Finishing includes attaching buttons, zippers, labels, and applying treatments such as anti-wrinkle, water resistance, or fire retardancy, depending on the dress’s intended use. Quality finishing elevates the product’s functionality and market appeal. Final pressing and packaging are also critical to preserve garment integrity during shipment.
Quality Assurance Frameworks and Checkpoints
Robust quality assurance (QA) is fundamental for utility dresses, especially when catering to international markets with stringent standards.
International and Industry Standards
– ISO 9001: This is the global benchmark for quality management systems. Suppliers certified under ISO 9001 demonstrate systematic control over production processes and continuous improvement practices.
– Industry-Specific Certifications: Depending on the utility dress application, additional certifications such as OEKO-TEX® Standard 100 (for harmful substances), CE marking (for PPE-related garments in Europe), or regional standards (e.g., South African SANS standards) may apply. Buyers should verify these based on their target market and end-use requirements.
Quality Control Checkpoints
– Incoming Quality Control (IQC): Inspection of raw materials and components upon arrival to ensure conformity with specified standards before production begins. This step prevents defective inputs from progressing further.
– In-Process Quality Control (IPQC): Continuous monitoring during manufacturing to detect defects early, including stitch density, seam strength, and component alignment. This is critical for maintaining batch consistency.
– Final Quality Control (FQC): Comprehensive inspection of finished dresses, including visual appearance, measurements, functionality tests (e.g., zipper operation, button security), and packaging integrity.
Common Testing Methods
– Dimensional Measurement: Verifying garment sizes against technical specifications using tools like measuring tapes and digital scanners.
– Colorfastness Testing: Assessing fabric resistance to washing, rubbing, and light exposure, essential for utility garments exposed to harsh conditions.
– Tensile and Tear Strength Tests: Ensuring fabric and seams can withstand operational stresses.
– Chemical Testing: For treatments and finishes, confirming compliance with safety and environmental standards.
How B2B Buyers Can Verify Supplier Quality Assurance
Ensuring supplier reliability and product quality is paramount, especially for buyers operating across different continents with varying regulatory environments.
1. Factory Audits and Certifications Review
Conduct or commission comprehensive factory audits focusing on manufacturing capabilities, quality control systems, labor conditions, and environmental compliance. Review valid certificates such as ISO 9001, OEKO-TEX®, and any relevant local certifications to confirm authenticity.
2. Quality Reports and Sample Inspections
Request detailed quality inspection reports including IQC, IPQC, and FQC data. Obtain pre-shipment samples for independent lab testing or on-site inspection to validate claims. For buyers in Europe and the Middle East, third-party testing labs accredited by bodies such as SGS or Intertek are preferred.
3. Third-Party Inspections and Continuous Monitoring
Engage third-party quality inspection agencies to perform random batch inspections and factory surveillance during production. This reduces risks of quality lapses and ensures ongoing compliance, especially critical for buyers in emerging markets like Kenya or Brazil where local oversight may be limited.
4. Leverage Technology for Transparency
Utilize supply chain management software and digital platforms that provide real-time tracking of production stages and QC results. Blockchain-enabled traceability solutions are emerging to guarantee transparency and authenticity, appealing to buyers committed to ethical sourcing.
Quality Assurance Considerations for International B2B Buyers
Regional Nuances and Compliance
– Africa (e.g., Kenya): Buyers should prioritize suppliers familiar with local textile regulations and durability requirements suited for tropical climates. Certifications such as SANS or compliance with African Continental Free Trade Area (AfCFTA) standards can facilitate smoother market entry.
– South America: Emphasis on sustainable sourcing and compliance with regional standards like INMETRO (Brazil) or IRAM (Argentina) is critical. Environmental and social governance (ESG) factors are gaining importance here.
– Middle East: Suppliers must align with GCC (Gulf Cooperation Council) standards and often require compliance with fire retardancy and modesty-related garment standards. Buyers should verify adherence to these niche requirements.
– Europe (e.g., UK): Strict adherence to EU regulations, including REACH for chemical safety and CE marking for protective clothing, is mandatory. Post-Brexit, UK buyers must also consider UKCA marking and local standards.
Customizing Quality Expectations
Utility dresses serve diverse industries—from healthcare to industrial labor—so buyers must communicate precise quality requirements and testing protocols upfront. This includes specifying fabric performance, durability, and safety features tailored to end-use.
Building Long-Term Supplier Relationships
Establishing trust through transparent communication, shared quality objectives, and regular performance reviews ensures sustained product excellence and supply chain resilience across international borders.
By thoroughly understanding the manufacturing stages and quality assurance mechanisms specific to utility dresses, international B2B buyers can effectively mitigate risks, ensure compliance, and secure durable, high-performance products tailored to their regional market needs.
Related Video: BMW Car Factory – ROBOTS Fast PRODUCTION Manufacturing
Comprehensive Cost and Pricing Analysis for utility dress Sourcing
Understanding the full cost structure behind sourcing utility dresses is critical for international B2B buyers aiming to optimize budgets without compromising on quality. The pricing of utility dresses involves multiple components, each impacting the final cost and offering negotiation leverage for savvy purchasers.
Key Cost Components in Utility Dress Sourcing
-
Materials: Fabric type (e.g., cotton, polyester blends), trims, and accessories significantly influence raw material costs. Sustainable or certified materials often command premium pricing but can add brand value and compliance advantages, especially for buyers in regions with strict import regulations.
-
Labor: Wages vary widely by manufacturing location. Countries in Asia, Eastern Europe, and select African regions may offer competitive labor costs. However, labor quality and compliance with labor laws (e.g., fair wages, working conditions) can affect both price and brand reputation.
-
Manufacturing Overhead: This includes factory utilities, maintenance, and administrative expenses. Efficient factories with modern equipment tend to have optimized overheads, potentially lowering per-unit costs.
-
Tooling and Setup: Initial costs for pattern making, sample development, and machinery setup are often amortized over the production run. Higher customization or complex designs increase these upfront costs.
-
Quality Control (QC): Rigorous inspection procedures, including fabric testing and garment durability checks, add to costs but reduce risks of returns and brand damage. Buyers should factor in third-party or in-house QC expenses.
-
Logistics and Shipping: Freight costs, customs duties, insurance, and warehousing impact landed cost. International buyers, especially from Africa, South America, the Middle East, and Europe, must consider varying port fees and transit times.
-
Supplier Margin: Manufacturers and suppliers include profit margins that reflect their market positioning, production efficiency, and demand levels.
Influential Pricing Factors for Buyers
-
Order Volume and Minimum Order Quantities (MOQ): Larger orders generally benefit from economies of scale, lowering per-unit prices. However, buyers with smaller markets (e.g., boutique buyers in Kenya or niche European retailers) may negotiate MOQs or explore consolidated sourcing to reduce costs.
-
Specifications and Customization: Additional features such as reinforced stitching, pockets, or branding elements increase cost. Clear specification documents help avoid costly revisions.
-
Material Quality and Certifications: Certifications like OEKO-TEX or GOTS for organic textiles add assurance but also cost. Buyers targeting eco-conscious markets should weigh these premiums against potential market advantages.
-
Supplier Reputation and Capacity: Established suppliers with strong track records may charge more but offer reliability and compliance assurances. New or smaller suppliers might offer competitive pricing but require thorough vetting.
-
Incoterms: The chosen international commercial terms (e.g., FOB, CIF, DDP) dictate which party bears shipping, insurance, and customs risks, influencing total landed cost and cash flow.
Strategic Buyer Tips for Cost Efficiency
-
Negotiate Based on Total Cost of Ownership (TCO): Beyond unit price, consider quality-related costs such as returns, reworks, and long-term supplier reliability. Investing in slightly higher-priced suppliers with robust QC can reduce unforeseen expenses.
-
Leverage Volume Consolidation: Buyers from emerging markets like South America or Africa can collaborate with regional partners to aggregate orders, achieving better pricing and logistics efficiencies.
-
Clarify Specifications Early: Detailed tech packs and samples reduce costly last-minute changes and rejections.
-
Understand Pricing Nuances: Currency fluctuations, tariffs, and local regulations vary by region. For instance, UK buyers should monitor Brexit-related trade changes, while Middle Eastern buyers must factor in regional customs policies.
-
Utilize Technology and Analytics: Employ supply chain management tools or sourcing platforms to compare quotes, track costs, and forecast trends, enabling proactive purchasing decisions.
-
Consider Sustainable and Ethical Factors: While sustainability might increase upfront costs, it opens access to premium markets and aligns with growing regulatory standards in Europe and other regions.
Indicative Pricing Disclaimer
Prices for utility dresses fluctuate based on material quality, order size, supplier location, and market conditions. Buyers should treat any quoted prices as indicative and conduct thorough due diligence, including requesting samples, verifying certifications, and negotiating terms tailored to their specific sourcing needs.
By understanding these detailed cost components and price influencers, international B2B buyers can make informed sourcing decisions, balancing quality, cost, and supply chain resilience to meet their market demands effectively.
Spotlight on Potential utility dress Manufacturers and Suppliers
This section offers a look at a few manufacturers active in the ‘utility dress’ market. This is a representative sample for illustrative purposes; B2B buyers must conduct their own extensive due diligence before any engagement. Information is synthesized from public sources and general industry knowledge.
Essential Technical Properties and Trade Terminology for utility dress
Key Technical Properties of Utility Dress
Understanding the technical specifications of utility dresses is crucial for international B2B buyers to ensure product quality, durability, and suitability for end-use. Here are the critical properties to consider:
-
Material Grade and Composition
Utility dresses are typically made from durable fabrics such as cotton twill, polyester blends, or canvas. The material grade indicates fabric strength, weave density, and fiber quality. Higher-grade materials offer better abrasion resistance and longevity, essential for workwear in demanding environments. Buyers should specify fiber content and fabric weight (e.g., grams per square meter, GSM) to match performance needs. -
Colorfastness
This property measures how well the fabric retains color after exposure to washing, sunlight, and wear. For utility dresses used in industrial or outdoor settings, high colorfastness ensures a professional appearance over time. Buyers should request colorfastness ratings (usually on a scale of 1-5) and test reports to avoid premature fading. -
Dimensional Stability (Tolerance)
Dimensional stability refers to the fabric’s resistance to shrinkage or distortion after washing or use. Maintaining consistent garment dimensions is vital to fit and comfort. Buyers often require tolerance specifications, such as ±2% shrinkage, to ensure uniformity across production batches. -
Seam Strength and Stitch Density
Seam strength defines the durability of stitched joints, critical for utility dresses subjected to frequent movement and stress. Stitch density (stitches per inch) affects seam integrity; higher density generally means stronger seams. Buyers should confirm minimum seam strength values and stitch counts, especially for safety and industrial apparel. -
Breathability and Moisture Management
Utility dresses worn in hot or physically demanding environments must allow air circulation and wick moisture away from the skin. Fabric breathability is measured by air permeability tests, while moisture management relates to how quickly sweat evaporates. These properties impact wearer comfort and productivity. -
Flame Resistance (if applicable)
For certain industrial sectors, flame-resistant (FR) utility dresses are mandatory. The fabric must comply with international safety standards (e.g., NFPA, EN ISO 11612). Buyers should verify certifications and test results when sourcing FR utility dresses.
Common Trade Terminology for Utility Dress Sourcing
Navigating international B2B transactions requires familiarity with key industry terms that streamline communication and procurement processes:
-
OEM (Original Equipment Manufacturer)
Refers to suppliers who manufacture utility dresses based on the buyer’s designs and specifications. OEM partnerships allow buyers to customize products while leveraging the manufacturer’s production expertise. -
MOQ (Minimum Order Quantity)
The smallest quantity of units a supplier is willing to produce in one order. Understanding MOQ helps buyers plan inventory and manage costs effectively. For small markets or startups, negotiating MOQs can be critical. -
RFQ (Request for Quotation)
A formal inquiry sent by buyers to suppliers to obtain price quotes and terms for specified quantities and product details. An RFQ is the first step in the procurement cycle and helps compare offers objectively. -
Incoterms (International Commercial Terms)
Standardized trade terms published by the International Chamber of Commerce that define responsibilities for shipping, insurance, and tariffs between buyers and sellers. Common Incoterms include FOB (Free On Board), CIF (Cost, Insurance, and Freight), and DDP (Delivered Duty Paid). Knowing Incoterms ensures clarity on who bears costs and risks during transport. -
Lead Time
The total time from placing an order to receiving the goods. Lead time affects inventory planning and market responsiveness. Buyers should confirm lead times upfront, especially when sourcing from overseas suppliers. -
Compliance Certifications
Documents verifying that utility dresses meet regulatory standards related to safety, environment, or labor practices (e.g., OEKO-TEX, ISO certifications). Compliance is increasingly important for buyers targeting markets with strict import regulations or sustainability commitments.
For B2B buyers across Africa, South America, the Middle East, and Europe, mastering these technical properties and trade terms is essential for making informed sourcing decisions. This knowledge helps mitigate risks, optimize supply chains, and secure products that meet both quality standards and market expectations.
Navigating Market Dynamics, Sourcing Trends, and Sustainability in the utility dress Sector
Market Overview & Key Trends
The utility dress sector, characterized by durable, functional, and versatile apparel, is experiencing robust growth driven by evolving global demands. International B2B buyers from regions such as Africa, South America, the Middle East, and Europe are increasingly focusing on sourcing utility dresses that balance practicality with modern aesthetics. Key market drivers include rising urbanization, expanding workforce participation (especially among women), and growing demand for multi-purpose clothing in industries like healthcare, hospitality, and manufacturing.
Emerging B2B sourcing trends emphasize agility and responsiveness. Buyers are prioritizing suppliers capable of quick turnarounds and flexible order volumes to adapt to fluctuating market needs. Digital sourcing platforms and supply chain management tools are becoming indispensable, enabling real-time inventory visibility and streamlined procurement processes. For example, buyers in Kenya and the UK are leveraging predictive analytics to forecast seasonal demand and optimize stock levels, reducing waste and improving profitability.
The sector also sees a shift toward regional diversification of supply chains. While Asian manufacturers remain dominant due to cost advantages, European and Middle Eastern producers are gaining traction by offering faster delivery and higher compliance with stringent quality and labor standards. African sourcing hubs, particularly in Kenya and South Africa, are emerging as promising alternatives, supported by improving infrastructure and trade agreements, which appeal to buyers aiming to shorten lead times and reduce carbon footprints.
Furthermore, material innovation and customization are critical trends. Utility dresses now often incorporate performance fabrics with moisture-wicking, antimicrobial, and wrinkle-resistant properties, meeting the demands of dynamic work environments. Buyers are increasingly seeking partners who offer bespoke designs and small-batch production to cater to niche markets and corporate branding requirements.
Sustainability & Ethical Sourcing in B2B
Sustainability is no longer optional in the utility dress sector; it is a strategic imperative. The environmental footprint of textile production—water usage, chemical discharge, and carbon emissions—poses significant challenges. B2B buyers from Africa to Europe are placing higher value on suppliers who demonstrate transparent, verifiable commitments to reducing environmental impact.
Ethical sourcing encompasses fair labor practices, safe working conditions, and community development. Buyers increasingly require certifications such as OEKO-TEX Standard 100, Global Organic Textile Standard (GOTS), and Fair Trade, which assure compliance with environmental and social benchmarks. These certifications are critical for mitigating reputational risks and aligning with global buyers’ corporate social responsibility (CSR) objectives.
Eco-friendly materials are gaining prominence in utility dress manufacturing. Organic cotton, recycled polyester, and innovative bio-based fabrics not only reduce reliance on virgin resources but also enhance product appeal to end consumers mindful of sustainability. For B2B buyers, sourcing from suppliers who integrate circular economy principles—such as take-back programs and upcycling—can unlock long-term value and regulatory advantages, especially in the European Union’s increasingly stringent environmental frameworks.
Moreover, digital traceability tools like blockchain enable buyers to verify the provenance of raw materials and monitor supply chain conditions in real time. This level of transparency is becoming a decisive factor when selecting partners, particularly for buyers in regions with growing regulatory oversight and consumer activism.
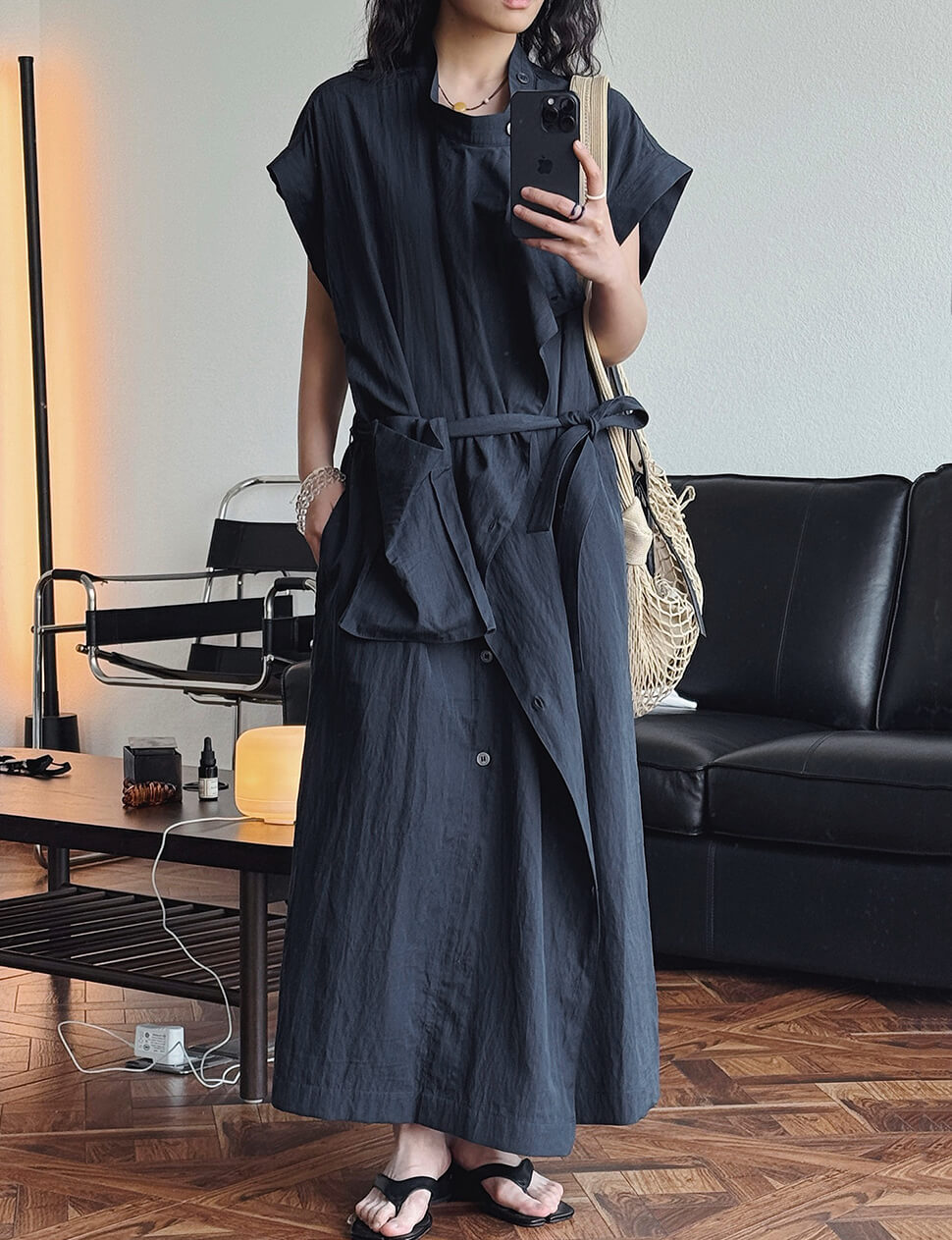
Illustrative Image (Source: Google Search)
Brief Evolution and Historical Context
Utility dresses have their roots in early 20th-century workwear, designed primarily for functionality, durability, and affordability. Initially adopted by laborers and service workers, the utility dress evolved during wartime economies, particularly in Europe, where rationing and resource constraints necessitated simple, multipurpose garments. Over decades, this workwear foundation transformed, integrating modern materials and design innovations to meet the complex needs of today’s workforce.
For B2B buyers, understanding this evolution highlights the sector’s resilience and adaptability. The utility dress’s heritage of practicality combined with contemporary advancements positions it as a vital category within corporate uniforming, industrial apparel, and institutional wear. This historical perspective underscores the importance of sourcing partners who appreciate both the garment’s legacy and the need for ongoing innovation in materials, sustainability, and supply chain agility.
Related Video: International Trade 101 | Economics Explained
Frequently Asked Questions (FAQs) for B2B Buyers of utility dress
-
How can I effectively vet suppliers of utility dresses to ensure reliability and quality?
To vet suppliers, start with verifying their business credentials, certifications (ISO, OEKO-TEX), and industry reputation via trade platforms or local chambers of commerce. Request detailed product samples and inquire about their quality control processes. For international suppliers, especially in regions like Asia or Eastern Europe, consider factory audits or third-party inspections. Checking references from other B2B buyers and reviewing their compliance with labor and environmental standards is critical. Building direct communication channels with suppliers helps clarify capabilities and fosters trust, reducing risks in sourcing utility dresses. -
What customization options are typically available when sourcing utility dresses in bulk?
Most manufacturers offer customization on fabric types, colors, sizing, and design features such as pockets, closures, and stitching patterns. Buyers can also request branding elements like logos or labels. Advanced customization may include fabric treatments (e.g., water resistance), ergonomic tailoring, or compliance with specific industry uniforms. Discussing your requirements early helps suppliers assess feasibility and cost implications. For buyers in diverse markets such as Africa or Europe, customization can address regional preferences and climate needs, making your product more competitive. -
What are the typical minimum order quantities (MOQs) and lead times for utility dress orders?
MOQs for utility dresses vary widely, often ranging from 100 to 1,000 units depending on the supplier’s production scale and customization level. Lead times typically range from 30 to 90 days, influenced by order complexity, material availability, and factory workload. For first-time or smaller orders, some suppliers may offer trial batches or flexible MOQs at a premium. Planning well in advance and clear communication about deadlines help manage expectations. Buyers from regions like South America or the Middle East should factor in additional shipping and customs clearance time. -
What payment terms are common, and how can I protect my transaction when sourcing internationally?
Common payment terms include a 30-50% advance deposit with the balance paid upon shipment or after inspection. Letters of Credit (LC) and escrow services provide extra security by ensuring funds are released only after contractual conditions are met. Using reputable payment platforms and verifying supplier bank details reduces fraud risk. It’s advisable to start with smaller orders to build trust before scaling. For buyers in emerging markets, negotiating flexible payment schedules or using trade finance solutions can ease cash flow pressures. -
How can I ensure quality assurance and compliance for utility dresses sourced internationally?
Request detailed quality assurance protocols and certifications such as ISO 9001 or specific textile standards like OEKO-TEX. Insist on pre-shipment inspections by third-party agencies to verify material quality, stitching, and compliance with agreed specifications. Sample approval before bulk production is essential to avoid costly mistakes. For markets with strict regulatory requirements, ensure the supplier adheres to local labor laws and environmental standards. Regular audits and building long-term supplier relationships promote consistent quality and reliability. -
What certifications should I look for to verify ethical and sustainable sourcing of utility dresses?
Look for certifications such as Global Organic Textile Standard (GOTS), Fair Trade, WRAP (Worldwide Responsible Accredited Production), and OEKO-TEX Standard 100. These indicate compliance with environmental, social, and chemical safety standards. For buyers prioritizing sustainability, suppliers offering recycled or organic fabrics and transparent supply chains are preferable. Certifications reassure end customers and align with increasing regulatory demands in Europe and other markets. Request documentation and verify through certifying bodies to confirm authenticity.
-
What are the best logistics practices for shipping utility dresses internationally?
Choose suppliers familiar with export regulations and experienced in international freight options including sea, air, or courier services. Consolidate shipments when possible to reduce costs and use reliable freight forwarders who provide tracking and customs clearance support. Understand Incoterms (e.g., FOB, CIF) to clarify responsibility for shipping costs and risks. For buyers in Africa and South America, consider potential delays due to customs or port congestion and plan buffer times. Effective communication with logistics partners ensures timely and cost-efficient delivery. -
How should disputes or quality issues be handled with overseas utility dress suppliers?
Establish clear contractual terms covering product specifications, delivery timelines, and dispute resolution mechanisms before placing orders. In case of quality issues, document discrepancies with photos and inspection reports, and communicate promptly with the supplier for remediation or replacement. Utilizing third-party mediation or arbitration clauses can help resolve conflicts without lengthy legal processes. Building a collaborative relationship rather than adversarial can facilitate quicker resolutions. For buyers in regions with less developed legal frameworks, working with suppliers who have international certifications and a good reputation reduces dispute risks.
Strategic Sourcing Conclusion and Outlook for utility dress
Strategic sourcing for utility dresses is pivotal in navigating today’s complex global apparel market. For international B2B buyers, especially those in Africa, South America, the Middle East, and Europe, adopting a well-crafted sourcing strategy ensures access to quality materials, reliable manufacturing, and competitive pricing. Key takeaways include the importance of aligning sourcing decisions with market trends, emphasizing supplier partnerships that prioritize transparency and sustainability, and leveraging technology to enhance supply chain agility.
Value-driven sourcing enables buyers to balance cost-efficiency with quality assurance, mitigating risks related to fluctuating demand and supply disruptions. Proactive engagement with suppliers, including those in emerging textile hubs, can unlock innovative materials and ethical production practices—critical factors as consumer expectations shift towards sustainability and social responsibility.
Looking ahead, the utility dress market is poised for growth fueled by evolving workwear needs and a rising emphasis on functional yet stylish apparel. Buyers are encouraged to deepen their strategic sourcing capabilities by investing in data-driven market insights, fostering collaborative supplier relationships, and prioritizing sustainable practices. By doing so, international B2B buyers can secure competitive advantage, meet diverse regional demands, and contribute positively to the global apparel ecosystem.
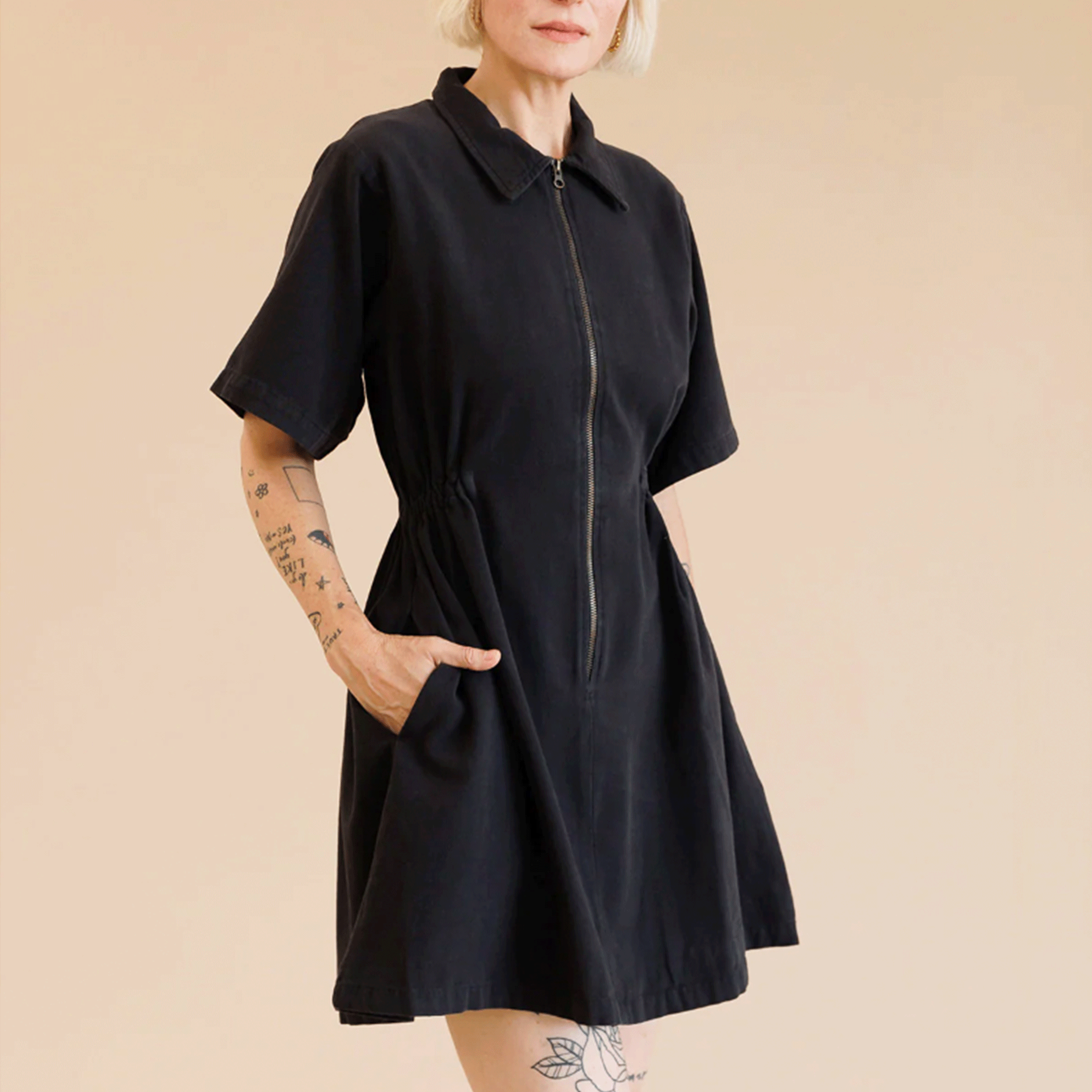
Illustrative Image (Source: Google Search)