Your Ultimate Guide to Sourcing Metal Dresser
Guide to Metal Dresser
- Introduction: Navigating the Global Market for metal dresser
- Understanding metal dresser Types and Variations
- Key Industrial Applications of metal dresser
- Strategic Material Selection Guide for metal dresser
- In-depth Look: Manufacturing Processes and Quality Assurance for metal dresser
- Comprehensive Cost and Pricing Analysis for metal dresser Sourcing
- Spotlight on Potential metal dresser Manufacturers and Suppliers
- Essential Technical Properties and Trade Terminology for metal dresser
- Navigating Market Dynamics, Sourcing Trends, and Sustainability in the metal dresser Sector
- Frequently Asked Questions (FAQs) for B2B Buyers of metal dresser
- Strategic Sourcing Conclusion and Outlook for metal dresser
Introduction: Navigating the Global Market for metal dresser
In today’s interconnected industrial landscape, sourcing the right metal dresser is pivotal for manufacturers, fabricators, and infrastructure developers aiming to maintain competitive advantage and operational excellence. From the burgeoning manufacturing hubs of Lagos and Buenos Aires to the advanced industrial corridors of Paris and Dubai, metal dressers serve as essential equipment for achieving precise surface finishing, shaping, and treatment of metal components. Their role transcends mere machinery; they are key enablers of quality, durability, and efficiency across sectors such as automotive, aerospace, construction, and heavy machinery.
For international B2B buyers, particularly those operating in Africa, South America, the Middle East, and Europe, navigating the complex global supply chain for metal dressers demands an informed, strategic approach. Market dynamics fluctuate with technological innovation, regional compliance standards, and evolving material requirements, making supplier selection and product specification critical challenges. This guide delivers an authoritative roadmap designed to empower procurement leaders and engineers with actionable insights tailored to diverse regional contexts.
Inside, you will find a thorough exploration of:
- Types and Variations: Understanding the different metal dresser models and their applications to match your project needs.
- Materials and Technical Specifications: Evaluating metal dresser components for longevity, performance, and maintenance.
- Manufacturing and Quality Control: Insights into fabrication methods, precision standards, and testing protocols.
- Supplier Identification and Evaluation: Frameworks for vetting global suppliers to ensure reliability, compliance, and cost-effectiveness.
- Cost Considerations and Market Trends: Analysis of pricing drivers, currency impacts, and emerging technologies.
- Frequently Asked Questions: Practical answers addressing common sourcing and operational challenges.
This comprehensive resource is crafted to help you make confident, future-proof purchasing decisions, ensuring your investment in metal dressers drives productivity and supports sustainable growth across your international operations.
Understanding metal dresser Types and Variations
Type Name | Key Distinguishing Features | Primary B2B Applications | Brief Pros & Cons for Buyers |
---|---|---|---|
Manual Metal Dresser | Hand-operated with replaceable dressing tools | Small-scale workshops, precision toolrooms | Pros: Cost-effective, precise control; Cons: Labor-intensive, slower for large volumes |
Hydraulic Metal Dresser | Uses hydraulic power for automated dressing | Heavy industry, mining, large-scale fabrication | Pros: High efficiency, consistent pressure; Cons: Higher upfront cost, maintenance needs |
Pneumatic Metal Dresser | Air-powered operation offering rapid dressing cycles | Automotive, aerospace, manufacturing plants | Pros: Fast operation, less operator fatigue; Cons: Requires compressed air system, noise levels |
Electric Metal Dresser | Electrically powered with variable speed and precision | Electronics manufacturing, metal fabrication | Pros: Versatile, adjustable settings; Cons: Energy consumption, complexity in repair |
Rotary Metal Dresser | Rotating dressing tool for continuous surface conditioning | Mining, grinding operations, heavy machinery | Pros: Continuous operation, long tool life; Cons: Complex setup, higher initial investment |
Manual Metal Dresser
Manual metal dressers are the most traditional type, relying on skilled operators to manually dress grinding wheels or metal surfaces using replaceable tools. These are ideal for precision tasks or small batch production where control and accuracy are paramount. For B2B buyers in regions with lower labor costs or specialized craftsmanship, manual dressers offer a cost-effective solution. However, the slower process and operator dependency may limit scalability for large industrial applications.
Hydraulic Metal Dresser
Hydraulic metal dressers leverage hydraulic pressure to automate the dressing process, delivering uniform force and consistent results. They are well-suited for heavy industries such as mining and large-scale manufacturing where durability and throughput are critical. B2B buyers should consider the higher capital investment and the need for regular hydraulic system maintenance but will benefit from improved productivity and reduced manual labor.
Pneumatic Metal Dresser
Pneumatic metal dressers utilize compressed air to power rapid dressing cycles, making them a strong fit for sectors requiring speed and repeatability, like automotive and aerospace manufacturing. These systems reduce operator fatigue and increase throughput but require a reliable compressed air infrastructure. Buyers should evaluate the operational noise and energy infrastructure costs when integrating pneumatic dressers into their facilities.
Electric Metal Dresser
Electric metal dressers offer versatility with variable speed controls and precise operation, making them ideal for electronics manufacturing and detailed metal fabrication. Their adaptability allows fine-tuning for different materials and dressing requirements. While they consume more energy and can be complex to repair, their precision and ease of automation make them attractive for buyers seeking advanced process control and integration with existing electrical systems.
Rotary Metal Dresser
Rotary metal dressers feature a rotating tool that continuously conditions surfaces, providing long tool life and steady performance. Commonly used in mining and heavy machinery grinding, they enable continuous operation with minimal downtime. B2B buyers should note the complexity of setup and higher initial costs, which are offset by reduced maintenance frequency and increased operational efficiency in demanding environments.
Related Video: Large Language Models (LLMs) – Everything You NEED To Know
Key Industrial Applications of metal dresser
Industry/Sector | Specific Application of metal dresser | Value/Benefit for the Business | Key Sourcing Considerations for this Application |
---|---|---|---|
Automotive Manufacturing | Surface finishing of metal dies and molds | Enhances precision and durability of tooling, reduces downtime | Material hardness, wear resistance, supplier quality certifications |
Aerospace Engineering | Restoration and maintenance of turbine blades | Maintains aerodynamic efficiency and safety standards | Compliance with aerospace-grade material standards, traceability |
Heavy Machinery & Equipment | Dressing grinding wheels for metal fabrication | Ensures consistent surface quality and prolongs tool life | Compatibility with abrasive materials, durability, supplier support |
Construction & Infrastructure | Preparation of metal surfaces for coating and welding | Improves adhesion and corrosion resistance of metal structures | Corrosion resistance, environmental compliance, size/customization |
Electronics & Electrical | Metal surface conditioning in component manufacturing | Guarantees electrical conductivity and precise dimensions | Precision, contamination control, adherence to industry standards |
In the automotive manufacturing sector, metal dressers are crucial for the surface finishing of dies and molds used in stamping and forming metal parts. By maintaining the sharpness and surface quality of these tools, metal dressers help manufacturers in regions like South America and Europe reduce production defects and extend tool lifespan, leading to cost savings and improved throughput. Buyers should prioritize sourcing metal dressers with high hardness and wear resistance, ensuring suppliers provide quality certifications to meet stringent automotive standards.
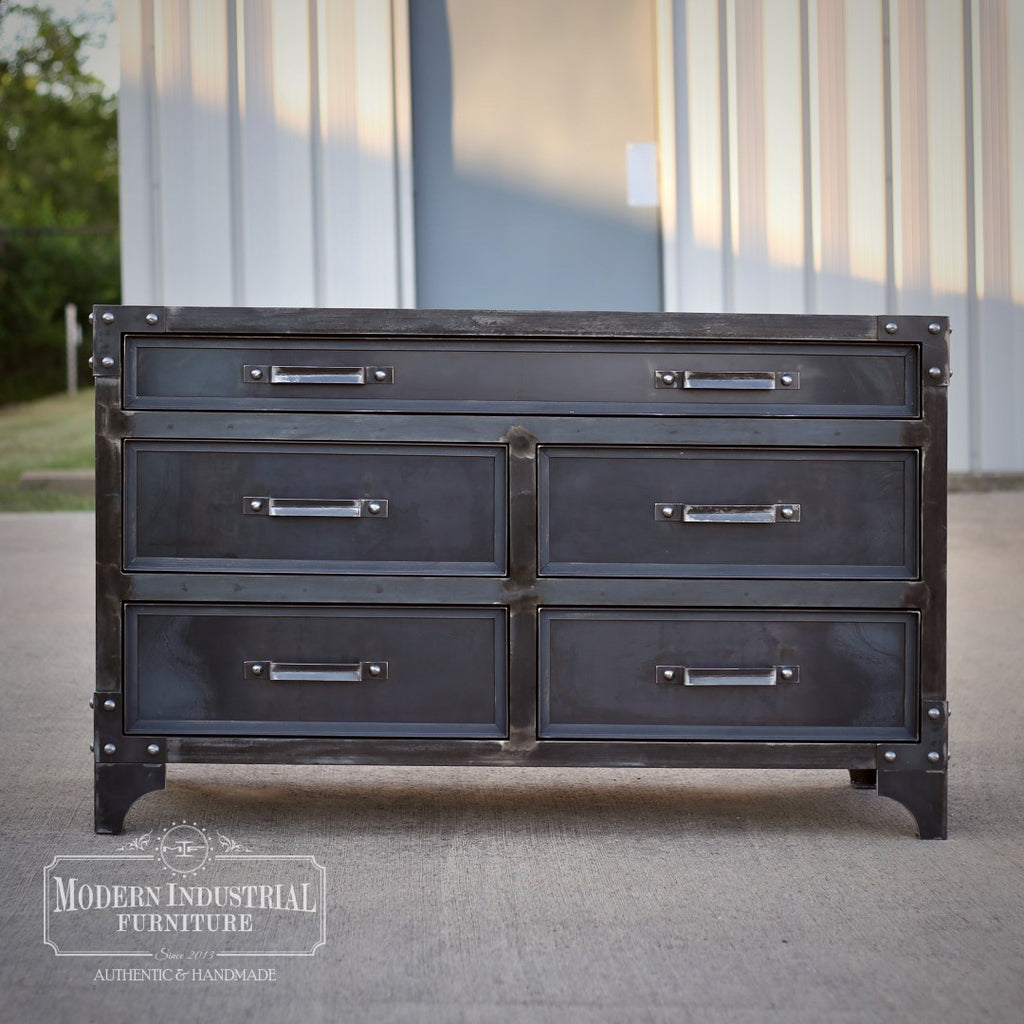
Illustrative Image (Source: Google Search)
Within aerospace engineering, metal dressers play a vital role in the restoration and maintenance of turbine blades and other critical components. These applications require precision and strict adherence to safety standards, especially in markets such as the Middle East and France, where aerospace industries demand reliable performance. International buyers must seek metal dressers compliant with aerospace-grade materials and with full traceability documentation to guarantee component integrity and regulatory compliance.
For heavy machinery and equipment manufacturers, metal dressers are used to dress grinding wheels that shape and finish metal components. This ensures consistent surface quality and extends the operational life of abrasive tools, which is essential in large-scale manufacturing hubs across Africa and Europe. Buyers should focus on compatibility with various abrasive materials, durability under heavy use, and supplier technical support to optimize tool performance.
In the construction and infrastructure sector, metal dressers prepare metal surfaces before coating or welding, significantly improving adhesion and corrosion resistance. This application is especially relevant in regions like Nigeria, Argentina, and the UAE, where harsh environmental conditions demand robust metal protection solutions. Sourcing considerations include the corrosion resistance of the dresser material, adherence to environmental regulations, and options for size or customization to fit diverse structural components.
Finally, in the electronics and electrical industries, metal dressers are employed for surface conditioning of metal components to ensure precise dimensions and optimal electrical conductivity. This is critical for manufacturers in Europe and South America producing high-precision electronic parts. Buyers should prioritize dressers that offer high precision, minimize contamination, and comply with industry standards to maintain product quality and reliability.
Related Video: Forming Sheet Metal & Metal Forming Tools – Uses Explained By Gene Winfield at SEMA
Strategic Material Selection Guide for metal dresser
Material Selection for Metal Dressers: Key Considerations for International B2B Buyers
Selecting the right material for a metal dresser is critical to ensure durability, performance, and cost-efficiency in various industrial applications. For international B2B buyers, especially those operating in Africa, South America, the Middle East, and Europe, understanding the properties, advantages, and limitations of common materials is essential to optimize procurement strategies and meet regional compliance standards.
Carbon Steel
Key Properties:
Carbon steel is known for its excellent strength and toughness, making it suitable for metal dressers subjected to mechanical stress and moderate temperatures (typically up to 400°C). It has moderate corrosion resistance but generally requires protective coatings or treatments to prevent rust, especially in humid or corrosive environments.
Pros & Cons:
– Pros: Cost-effective, widely available, and easy to machine and weld. Its robustness makes it ideal for structural components in metal dressers.
– Cons: Susceptible to corrosion without protective coatings, which can increase maintenance costs. Not suitable for highly corrosive or marine environments without additional treatment.
Impact on Application:
Carbon steel metal dressers are best suited for dry or controlled environments where corrosion is minimal. They perform well in general industrial applications but are less ideal for chemical or outdoor exposure unless galvanized or painted.
International Buyer Considerations:
Buyers from regions like South America (e.g., Argentina) and Africa should consider local climate effects on corrosion and opt for coated variants. Compliance with ASTM A216 Grade WCB or equivalent EN standards (e.g., EN 10213) is common in Europe and the Middle East. Supply chain reliability and cost fluctuations in steel markets should be monitored closely.
Stainless Steel (e.g., 304, 316 Grades)
Key Properties:
Stainless steel offers superior corrosion resistance due to chromium content, excellent strength, and good temperature tolerance (up to 870°C for 304 and higher for 316). It resists oxidation, chemical attack, and is hygienic, making it suitable for demanding environments.
Pros & Cons:
– Pros: Excellent corrosion resistance, low maintenance, and high durability. Suitable for aggressive environments and hygienic applications.
– Cons: Higher initial cost and more challenging to machine compared to carbon steel. Weight can be a consideration in some designs.
Impact on Application:
Ideal for metal dressers used in corrosive environments such as chemical processing, food manufacturing, and coastal regions. Stainless steel dressers maintain integrity under exposure to moisture, acids, and high temperatures.
International Buyer Considerations:
European buyers (e.g., France) often require compliance with EN 10088 or ASTM A240 standards. Middle Eastern and African buyers should verify material certification and traceability due to regional regulatory demands. Price volatility due to nickel and chromium markets can affect procurement budgets.
Aluminum Alloys (e.g., 5052, 6061)
Key Properties:
Aluminum alloys are lightweight, corrosion-resistant, and exhibit good thermal and electrical conductivity. They have moderate strength and are suitable for applications where weight reduction is critical. Temperature tolerance is generally lower than steel, typically up to 150-200°C.
Pros & Cons:
– Pros: Lightweight, excellent corrosion resistance without coatings, easy to fabricate and form.
– Cons: Lower mechanical strength compared to steel, more expensive than carbon steel, and can be prone to surface scratches.
Impact on Application:
Aluminum metal dressers are preferred in applications requiring weight savings, such as mobile or transportable equipment. They are also suitable in humid or marine environments due to natural oxide layer protection.
International Buyer Considerations:
Buyers in coastal regions of Africa and South America benefit from aluminum’s corrosion resistance. Compliance with ASTM B209 or EN 485 standards is typical. Considerations include local availability of specific alloys and potential import tariffs affecting cost.
Brass
Key Properties:
Brass, an alloy of copper and zinc, is valued for its machinability, corrosion resistance, and attractive finish. It has moderate strength and good resistance to dezincification in certain environments. Temperature resistance is moderate, generally up to 200°C.
Pros & Cons:
– Pros: Excellent machinability, corrosion-resistant in water and atmospheric conditions, aesthetically appealing for decorative metal dressers.
– Cons: Higher cost than steel and aluminum, softer material prone to deformation under heavy loads.
Impact on Application:
Brass dressers are typically used in decorative or low-load applications where appearance and corrosion resistance are important, such as in architectural metal furniture or specialty industrial equipment.
International Buyer Considerations:
European and Middle Eastern buyers often require compliance with EN 12165 or ASTM B16 standards. Brass’s cost and softness may limit its use in heavy-duty industrial contexts but offers value in niche markets.
Summary Table of Material Selection for Metal Dressers
Material | Typical Use Case for metal dresser | Key Advantage | Key Disadvantage/Limitation | Relative Cost (Low/Med/High) |
---|---|---|---|---|
Carbon Steel (e.g., A216 WCB) | General service, non-corrosive fluids for valve bodies | Cost-effective, good strength | Susceptible to corrosion if not protected | Low |
Stainless Steel (304/316) | Corrosive environments, hygienic and chemical applications | Superior corrosion resistance, durable | Higher cost, heavier, machining complexity | High |
Aluminum Alloys (5052/6061) | Lightweight, corrosion-resistant applications | Lightweight, natural corrosion resistance | Lower strength, costlier than carbon steel | Medium |
Brass | Decorative, low-load industrial applications | Excellent machinability and corrosion resistance | Softer, higher cost, prone to deformation | High |
This guide provides international B2B buyers with a clear framework to evaluate metal dresser materials based on application requirements, environmental conditions, and regional compliance. By aligning material choice with operational demands and sourcing realities, buyers can optimize performance, cost, and supply chain resilience.
In-depth Look: Manufacturing Processes and Quality Assurance for metal dresser
Manufacturing a metal dresser involves a series of precise and controlled processes designed to ensure durability, aesthetic appeal, and functional integrity. For international B2B buyers, especially from regions such as Africa, South America, the Middle East, and Europe, understanding these manufacturing stages and the embedded quality assurance mechanisms is crucial to secure reliable supply and consistent product performance.
Manufacturing Processes for Metal Dressers
1. Material Preparation
The process begins with selecting and preparing raw materials, primarily sheet metals such as stainless steel, carbon steel, or aluminum alloys. Material preparation includes cutting the metal sheets to size, deburring edges, and sometimes pre-treating surfaces to enhance adhesion for subsequent coatings or finishes. Precision at this stage ensures minimal waste and forms the foundation for high-quality output.
2. Forming and Shaping
Forming is a critical step where the flat metal sheets are transformed into the various structural components of the dresser. Key techniques include:
– Stamping and Pressing: Used to create consistent shapes and features like drawer faces and frame panels. High-tonnage presses apply exact force to mold the metal.
– Bending: CNC-controlled bending machines produce accurate angles for structural elements, ensuring proper assembly fit.
– Laser Cutting or CNC Punching: These methods provide precise cutouts for handles, ventilation, or decorative features, supporting both functional and aesthetic requirements.
3. Assembly
Once components are formed, the assembly stage integrates these parts into a cohesive unit. Welding (MIG or TIG) is common for joining metal parts, offering strength and durability. Mechanical fastening methods such as rivets or screws may be used where disassembly or modularity is desired. Robotic or semi-automated assembly lines enhance consistency and reduce human error, which is critical for large production runs.
4. Surface Treatment and Finishing
Finishing processes protect the metal dresser from corrosion, wear, and environmental exposure while also providing an attractive appearance. Common finishing techniques include:
– Powder Coating: Offers a durable, uniform finish with excellent resistance to scratching and fading.
– Electroplating or Anodizing: Used mainly for aluminum and steel to improve corrosion resistance and surface hardness.
– Polishing and Buffing: Applied to stainless steel dressers to achieve a smooth, reflective surface.
– Painting: Custom colors and textures can be applied based on client specifications.
Quality Assurance (QA) and Quality Control (QC) Framework
For B2B buyers, rigorous QA and QC protocols are non-negotiable to guarantee product reliability and regulatory compliance, especially when sourcing from global suppliers.
Relevant International and Industry Standards
– ISO 9001: The global benchmark for quality management systems, ensuring suppliers maintain consistent processes and continuous improvement practices.
– CE Marking: Essential for metal dressers sold within the European Economic Area, indicating conformity with health, safety, and environmental protection standards.
– API Standards (where applicable): For dressers used in industrial sectors such as oil and gas, adherence to American Petroleum Institute standards may be required.
– Other Regional Certifications: Buyers from regions like South America or the Middle East should verify compliance with local standards or import regulations, such as INMETRO in Brazil or SASO in Saudi Arabia.
Key QC Checkpoints
– Incoming Quality Control (IQC): Inspection of raw materials to verify chemical composition, mechanical properties, and surface conditions before production begins. This often involves material certificates and sample testing.
– In-Process Quality Control (IPQC): Continuous monitoring during forming, welding, and assembly stages to detect defects early. Techniques include dimensional checks, weld integrity inspections, and surface finish verification.
– Final Quality Control (FQC): Comprehensive inspection of finished dressers covering structural integrity, finishing quality, and functionality tests (e.g., drawer operation, load-bearing capacity).
Common Testing Methods
– Non-Destructive Testing (NDT): Ultrasonic or dye penetrant testing is applied to welds and critical joints to detect cracks or flaws without damaging the product.
– Corrosion Resistance Testing: Salt spray chambers simulate harsh environments to assess coating durability and metal resistance.
– Load and Stability Tests: Ensures the dresser can withstand expected operational stresses without deformation or failure.
– Dimensional Accuracy: Calipers, coordinate measuring machines (CMM), or laser scanners verify adherence to design specifications.
How B2B Buyers Can Verify Supplier QC Practices
Supplier Audits:
Performing on-site audits or virtual factory tours enables buyers to evaluate the supplier’s manufacturing environment, machinery, workforce skills, and adherence to documented procedures. Audits should cover process flows, equipment calibration, and personnel training records.
Review of Quality Documentation:
Requesting and analyzing quality manuals, ISO certifications, inspection reports, and test certificates provides transparency into the supplier’s quality system. Buyers should ensure traceability of materials and components through batch numbers and inspection logs.
Third-Party Inspections:
Engaging independent inspection agencies offers an unbiased assessment of product quality before shipment. These inspections can be tailored to check specific parameters or conduct full-scale acceptance tests, mitigating risks associated with international procurement.
QC and Certification Nuances for International Buyers
- Regional Compliance Requirements: Buyers from Africa, South America, the Middle East, and Europe must consider local import regulations and certification requirements. For example, a metal dresser destined for France requires CE marking, while buyers in Argentina should ensure compliance with INMETRO or IRAM standards.
- Language and Documentation: Ensure quality certificates, test reports, and manuals are provided in a language accessible to your procurement and technical teams, or include certified translations.
- Cultural and Logistical Considerations: Understanding supplier business practices and logistical challenges in your region can influence QC effectiveness. For instance, long transit times in African or Middle Eastern supply chains may necessitate more robust packaging and post-delivery inspection protocols.
- Custom Specification Alignment: Clearly communicate your functional and regulatory requirements upfront. Customizing QA/QC checklists and acceptance criteria with your supplier reduces ambiguity and supports smoother cross-border transactions.
By grasping the detailed manufacturing steps and embedded quality assurance mechanisms, international B2B buyers can confidently select metal dresser suppliers that deliver consistent, compliant, and high-performing products tailored to diverse market demands. This knowledge empowers procurement teams to negotiate effectively, mitigate risks, and foster long-term supplier partnerships across Africa, South America, the Middle East, and Europe.
Related Video: China’s Top 5 Manufacturing and Mass Production Videos | by @miracleprocess
Comprehensive Cost and Pricing Analysis for metal dresser Sourcing
Breakdown of Cost Components in Metal Dresser Sourcing
Understanding the detailed cost structure behind metal dresser procurement is essential for international B2B buyers aiming to optimize spend without compromising quality. The primary cost components typically include:
-
Raw Materials: The choice of metal (e.g., stainless steel, aluminum, carbon steel) significantly impacts cost. Prices fluctuate based on global commodity markets, alloy composition, and sheet thickness. For instance, stainless steel dressers command a premium over carbon steel due to corrosion resistance and durability.
-
Labor: Skilled labor costs vary by manufacturing location. Regions with advanced fabrication capabilities may charge higher wages but offer superior precision and quality control. Consider labor cost differences between suppliers in Europe versus emerging markets in Africa or South America.
-
Manufacturing Overhead: This covers factory utilities, equipment depreciation, and indirect labor. Complex manufacturing processes like CNC machining, laser cutting, or surface finishing increase overhead costs.
-
Tooling and Setup: Initial tooling for custom metal dresser designs or intricate features can add upfront expenses. High-volume orders can amortize these costs more effectively.
-
Quality Control (QC): Inspection, testing, and certification (e.g., ISO, CE marks) contribute to cost but ensure compliance with international standards, reducing risk of defects or returns.
-
Logistics and Freight: International shipping, customs duties, and inland transportation can represent a substantial portion of total cost, especially for buyers in Africa, South America, or the Middle East. Factors such as containerization, Incoterms, and freight modality (sea, air, road) influence final landed cost.
-
Supplier Margin: Each supplier adds a profit margin reflecting market positioning, brand reputation, and service level agreements.
Key Pricing Influencers to Consider
Several factors dynamically affect the quoted price for metal dressers:
-
Order Volume and Minimum Order Quantity (MOQ): Larger orders typically unlock economies of scale, reducing per-unit costs. Buyers should negotiate MOQs aligned with demand forecasts to avoid excess inventory or high unit prices.
-
Specifications and Customization: Tailored dimensions, finishes, or assembly requirements increase complexity and cost. Standardized designs usually offer better pricing.
-
Material Grade and Quality Certifications: Premium grades with certifications for durability, corrosion resistance, or fire safety command higher prices but may reduce lifecycle costs.
-
Supplier Location and Capability: Suppliers closer to buyer markets reduce shipping time and cost but may have higher labor costs. Conversely, distant low-cost regions require balancing freight cost and lead times.
-
Incoterms Selection: Terms like FOB, CIF, or DDP affect who bears transportation and customs responsibilities, impacting pricing transparency and risk exposure.
Strategic Buyer Tips for Cost-Efficient Sourcing
-
Negotiate Based on Total Cost of Ownership (TCO): Focus beyond unit price to include installation, maintenance, durability, and disposal costs. High-quality metal dressers may cost more upfront but yield savings over time.
-
Leverage Regional Trade Agreements: Buyers from Africa, South America, the Middle East, and Europe should explore preferential tariffs and trade zones to reduce import duties.
-
Request Detailed Cost Breakdowns: Insist on transparency in supplier quotations to identify cost-saving opportunities in materials, processes, or logistics.
-
Evaluate Multiple Suppliers: Compare offers from diverse regions to balance price, quality, lead time, and after-sales support.
-
Consider Group Purchasing or Consolidated Shipments: Pooling orders with other buyers or sourcing multiple components from one supplier can reduce logistics and handling fees.
-
Plan for Currency Fluctuations and Payment Terms: Negotiate contracts with flexible payment options or currency hedging to mitigate exchange rate risks.
Pricing Nuances for International Buyers from Target Regions
-
Africa: Infrastructure challenges and import tariffs can increase landed costs. Prioritize suppliers with experience navigating local customs and logistics.
-
South America: Consider local content requirements and regional standards that may affect certification costs.
-
Middle East: Demand for corrosion-resistant metals due to climate increases preference (and cost) for stainless steel or coated metals.
-
Europe: High labor and environmental compliance costs may increase supplier prices but guarantee superior quality and regulatory adherence.
Disclaimer:
The pricing and cost components discussed are indicative and can vary widely based on market conditions, supplier contracts, and specific project requirements. Buyers should conduct detailed supplier due diligence and market research before finalizing procurement decisions.
Spotlight on Potential metal dresser Manufacturers and Suppliers
This section offers a look at a few manufacturers active in the ‘metal dresser’ market. This is a representative sample for illustrative purposes; B2B buyers must conduct their own extensive due diligence before any engagement. Information is synthesized from public sources and general industry knowledge.
Essential Technical Properties and Trade Terminology for metal dresser
Key Technical Properties of Metal Dressers
Understanding the critical technical specifications of a metal dresser is essential for international B2B buyers to ensure the product meets operational requirements and quality standards. Here are the primary properties to consider:
-
Material Grade
The metal dresser’s material grade defines the composition and quality of the metal used, such as stainless steel 304 or carbon steel ASTM A36. This affects durability, corrosion resistance, and suitability for specific environments. For buyers, selecting the correct grade ensures longevity and compliance with industry regulations, especially important for applications in harsh climates like coastal Africa or humid regions in South America. -
Dimensional Tolerance
Tolerance refers to the allowable deviation in the dresser’s dimensions (thickness, length, width). Tight tolerances guarantee consistent fit and function in assembly lines or machinery. Inaccurate tolerances can cause operational inefficiencies or increased scrap rates, so buyers should specify tolerance limits based on their precision needs. -
Surface Finish
The surface finish impacts both aesthetics and functionality. Common finishes include polished, brushed, or matte. For industrial metal dressers, a smooth finish may reduce friction and wear during metal dressing operations. Buyers should clarify surface treatment requirements early to avoid additional finishing costs downstream. -
Hardness and Strength
Hardness indicates the dresser’s resistance to deformation and wear, critical for durability in abrasive metalworking environments. Strength specifications, often defined by tensile strength or yield strength, ensure the dresser withstands operational stresses. These properties influence maintenance frequency and replacement cycles, directly affecting total cost of ownership. -
Coating and Corrosion Resistance
Protective coatings (e.g., galvanization, powder coating) enhance resistance to rust and chemical damage. For buyers sourcing metal dressers for outdoor or high-moisture settings—such as Middle Eastern infrastructure projects—specifying appropriate coatings is crucial to extend service life. -
Compatibility with Metal Types
The dresser must be compatible with the range of metals it will process (e.g., aluminum, stainless steel, carbon steel). Compatibility affects dressing efficiency and tool wear rates. Buyers should verify this compatibility with suppliers to optimize performance and reduce downtime.
Common Trade Terminology for Metal Dresser Procurement
Navigating international metal dresser procurement requires familiarity with key industry terms that facilitate clear communication and efficient transactions:
-
OEM (Original Equipment Manufacturer)
OEM refers to the company that originally manufactures the metal dresser or its components. When purchasing OEM parts, buyers ensure compatibility and quality aligned with original specifications, which is critical for maintaining warranty and performance standards. -
MOQ (Minimum Order Quantity)
MOQ is the smallest quantity a supplier is willing to sell in one order. Understanding MOQ helps buyers plan inventory and budgeting, especially for smaller businesses or those entering new markets like Africa or Europe, where demand volumes may vary. -
RFQ (Request for Quotation)
An RFQ is a formal document sent to suppliers requesting detailed pricing, lead times, and terms for specific metal dresser products. Crafting precise RFQs with clear technical specs reduces ambiguity, enabling suppliers to provide accurate and comparable quotes. -
Incoterms (International Commercial Terms)
Incoterms define the responsibilities of buyers and sellers in international trade, including shipping, insurance, and customs clearance. Common terms include FOB (Free on Board) and CIF (Cost, Insurance, and Freight). Buyers must understand Incoterms to manage logistics costs and risks effectively. -
Lead Time
Lead time is the duration from order placement to delivery. For metal dressers, shorter lead times may be critical to meet tight production schedules. Buyers should negotiate lead times upfront and consider supplier capacity and shipping routes, particularly when sourcing globally. -
Batch Number / Lot Number
These identifiers track specific production runs of metal dressers, facilitating quality control and traceability. In regulated industries or large-scale projects, batch tracking helps manage warranties and recall procedures if needed.
By mastering these technical properties and trade terms, international B2B buyers can confidently specify, evaluate, and procure metal dressers that align with their operational demands and supply chain strategies. This knowledge is especially valuable for buyers across diverse regions such as Africa, South America, the Middle East, and Europe, where supplier capabilities and market conditions vary significantly.
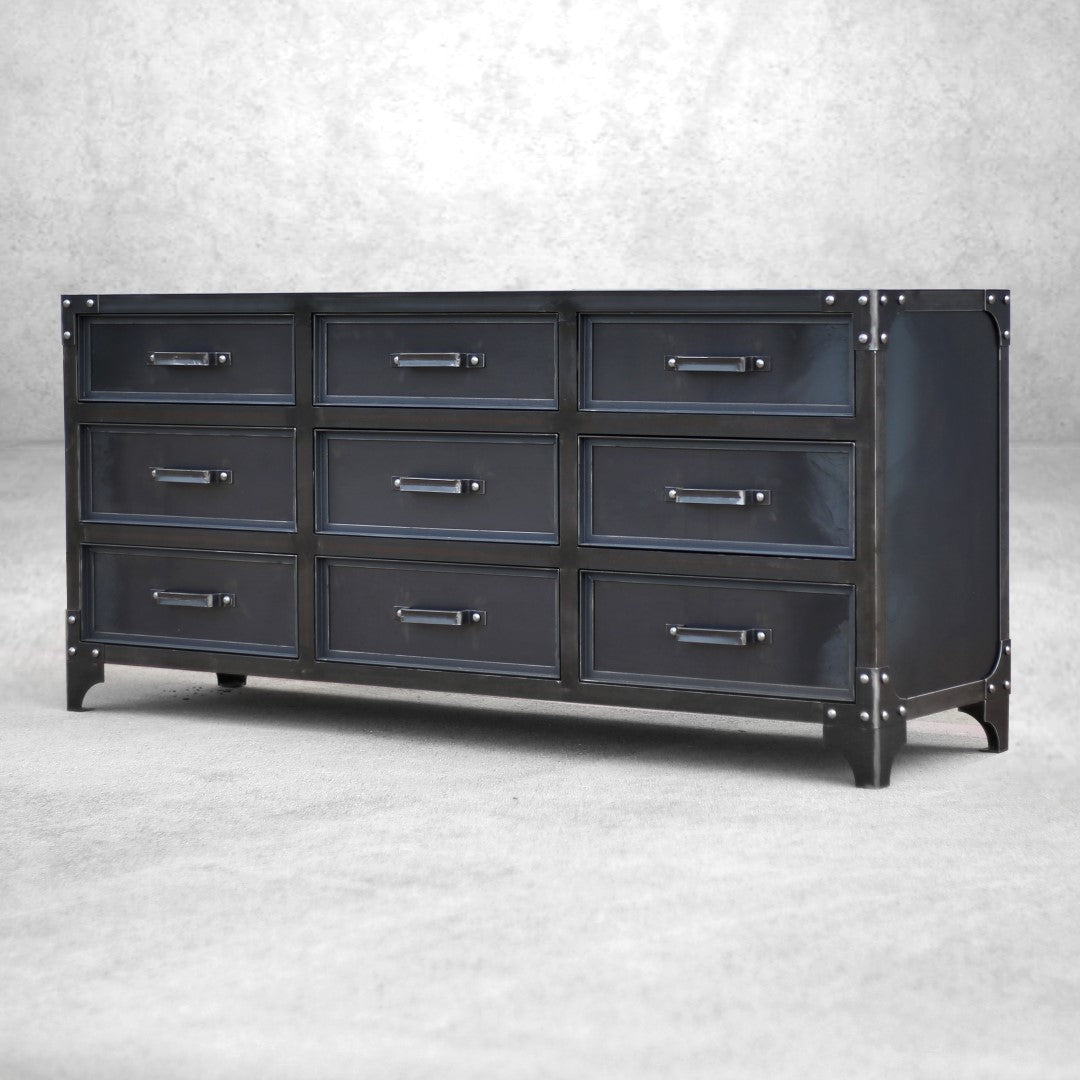
Illustrative Image (Source: Google Search)
Navigating Market Dynamics, Sourcing Trends, and Sustainability in the metal dresser Sector
Market Overview & Key Trends
The global market for metal dresser components is shaped by robust industrial growth, expanding infrastructure, and rising demand for durable, precision-engineered metal products. Key drivers include urbanization and industrialization across Africa, South America, the Middle East, and Europe, with countries like Nigeria, Argentina, Saudi Arabia, and France investing heavily in construction, manufacturing, and energy sectors. This growth fuels demand for metal dressers used in heavy machinery, equipment housings, and architectural metalwork.
From a sourcing perspective, international B2B buyers face a complex landscape influenced by fluctuating raw material prices—particularly steel and aluminum—alongside evolving trade policies and regional supply chain disruptions. Buyers increasingly prioritize suppliers offering flexibility in customization, just-in-time delivery, and compliance with international quality standards such as ISO 9001 and EN 1090 (for structural metal components). Technological advancements like CNC machining and laser cutting have become standard expectations, enhancing precision and reducing lead times.
Emerging trends include a growing preference for lightweight, corrosion-resistant alloys (such as aluminum and stainless steel) in metal dresser manufacturing, driven by demands for longevity and lower maintenance costs. Digital procurement platforms and blockchain are gaining traction to improve transparency and traceability, particularly in markets with complex logistics like South America and Africa. Furthermore, partnerships with regional fabricators in Europe and the Middle East are rising to mitigate risks related to geopolitical tensions and shipping delays.
For buyers in these regions, understanding local regulatory frameworks, import tariffs, and certification requirements is critical. Leveraging regional trade agreements (e.g., Mercosur in South America or the African Continental Free Trade Area) can provide cost advantages and smoother customs clearance. Overall, the market is moving toward integrated supply solutions that combine quality, sustainability, and agility.
Sustainability & Ethical Sourcing in B2B
Sustainability has become a pivotal factor in sourcing metal dresser products, driven by stricter environmental regulations and growing stakeholder demand for responsible supply chains. The metal industry’s environmental impact—especially from mining, refining, and fabrication—includes high energy consumption and greenhouse gas emissions. Therefore, B2B buyers are increasingly seeking suppliers that demonstrate commitment to reducing carbon footprints through energy-efficient manufacturing and recycling initiatives.
Ethical sourcing is equally critical, with buyers prioritizing transparency around labor practices, conflict-free raw materials, and compliance with international human rights standards. Certifications such as ISO 14001 (Environmental Management), ResponsibleSteel™, and the Aluminium Stewardship Initiative (ASI) are becoming benchmarks for suppliers. These certifications assure buyers that their metal dresser components originate from environmentally and socially responsible sources, a growing requirement especially in Europe and the Middle East where regulatory scrutiny is stringent.
Material selection also plays a significant role in sustainability. Metals like recycled aluminum and stainless steel reduce environmental impacts by lowering raw material extraction and energy use. Additionally, sourcing from suppliers who implement circular economy principles—such as reclaiming scrap metal and minimizing waste—can enhance supply chain resilience and cost efficiency.
For international buyers, integrating sustainability criteria into supplier evaluation and contract negotiation helps mitigate risks related to reputational damage and regulatory non-compliance. It also aligns with corporate social responsibility goals increasingly demanded by end customers and investors across Africa, South America, and Europe.
Evolution and Historical Context
The metal dresser sector has evolved significantly from its origins in basic metal fabrication to a highly specialized industry characterized by advanced materials and precision engineering. Historically, metal dressers were simple sheet metal structures designed primarily for protection and aesthetic purposes. However, the rise of industrial manufacturing and modern construction in the 20th century drove the demand for more durable, corrosion-resistant, and customizable metal components.
Technological innovations such as automated CNC machining, laser cutting, and advanced welding techniques have transformed production capabilities, enabling complex designs and tighter tolerances. Simultaneously, globalization expanded supply chains, allowing buyers worldwide to access diverse metal types and fabrication expertise.
Today’s metal dresser market reflects a blend of tradition and innovation, where legacy manufacturing hubs in Europe coexist with emerging suppliers in Africa and South America. This evolution underscores the importance of strategic sourcing decisions that balance quality, cost, and sustainability in a dynamic global environment.
Related Video: International Trade Explained
Frequently Asked Questions (FAQs) for B2B Buyers of metal dresser
-
How can I effectively vet suppliers of metal dressers for international B2B purchases?
To vet suppliers, start by verifying their business licenses and certifications such as ISO 9001 for quality management. Request samples and check product specifications against your requirements. Assess their track record through client references, particularly those in your region (Africa, South America, Middle East, Europe). Evaluate their manufacturing capabilities, compliance with international standards, and responsiveness. Utilize third-party inspection services for audits if possible. Supplier transparency about materials, production processes, and quality assurance is critical to minimize risks in long-distance B2B transactions. -
What customization options are typically available for metal dressers in international trade?
Metal dresser suppliers often offer customization in dimensions, metal type (e.g., stainless steel, aluminum), finish (powder coating, galvanization), drawer configurations, and locking mechanisms. For international buyers, clearly communicate your functional needs, environmental conditions, and aesthetic preferences. Confirm the supplier’s ability to accommodate custom sizes or special features like anti-corrosion treatments for humid climates common in Africa or the Middle East. Early engagement on customization reduces delays and ensures the product aligns with your market demands and regulatory requirements. -
What are common minimum order quantities (MOQs) and lead times for metal dressers in B2B sourcing?
MOQs vary widely depending on supplier scale and customization level, ranging typically from 50 to 500 units. Lead times can range from 4 to 12 weeks, influenced by order complexity, raw material availability, and logistics. Buyers from regions like South America or Europe should factor in customs clearance and transport delays. Negotiate MOQs upfront to balance cost efficiency and inventory risk. Some suppliers offer tiered pricing or trial orders for new international clients to build trust and test market fit. -
Which payment terms are standard when importing metal dressers internationally?
Common payment terms include 30% upfront deposit with balance paid upon shipment or after inspection, often via Letter of Credit (L/C), Telegraphic Transfer (T/T), or Escrow services. Letters of Credit provide greater security for both parties, particularly in cross-border deals involving Africa or the Middle East. Negotiate terms that protect cash flow while ensuring supplier commitment. Always confirm payment schedules and penalties for delays in the contract to avoid disputes.
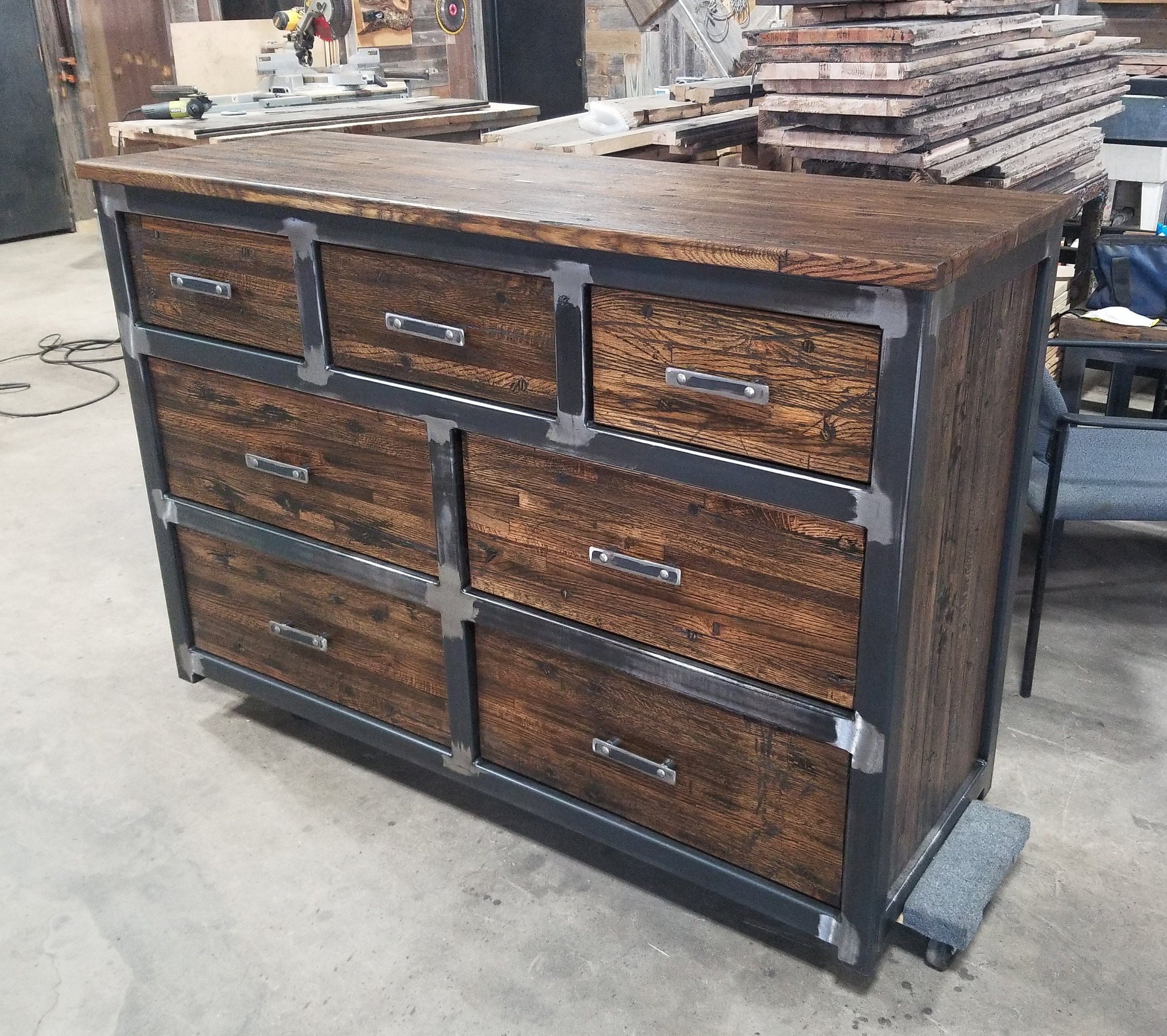
Illustrative Image (Source: Google Search)
-
What quality assurance certifications should I look for in metal dresser suppliers?
Look for ISO 9001 certification to ensure quality management systems are in place. Additional relevant certifications include ASTM standards for metal properties and RoHS compliance if electrical components are involved. Suppliers should provide material test reports (MTRs) confirming metal grade and treatment. For European buyers, CE marking may be necessary. Request third-party quality inspection reports or factory audit certificates, especially when sourcing from emerging manufacturing hubs. -
How can I optimize logistics and shipping for international metal dresser orders?
Plan shipments via sea freight for large volumes to reduce cost, with air freight reserved for urgent or smaller orders. Partner with freight forwarders experienced in your region’s import regulations (e.g., customs in Argentina or Nigeria). Consolidate shipments to minimize costs and verify packaging standards to protect metal dressers from corrosion or damage during transit. Track shipments actively and prepare for customs clearance by having all documentation—commercial invoice, packing list, certificates of origin—accurate and ready to avoid delays. -
What steps should I take if there is a dispute or quality issue with my metal dresser order?
First, document the issue thoroughly with photos, inspection reports, and communication records. Engage the supplier promptly to seek resolution, such as replacement, repair, or refund. Refer to contract terms regarding dispute resolution, which often specify mediation or arbitration venues. Employ third-party inspection agencies to provide unbiased verification. For international disputes, understanding local legal frameworks and leveraging trade bodies or chambers of commerce in your country can facilitate amicable settlements. -
How do regional differences affect sourcing metal dressers from international suppliers?
Regional factors such as climate, infrastructure, and regulatory standards influence material choice and design. For instance, buyers in humid African or Middle Eastern markets should prioritize corrosion-resistant metals and protective coatings. European buyers must ensure compliance with stringent EU regulations. Logistics infrastructure in South America may affect delivery timelines. Understanding these regional nuances helps tailor specifications, select suitable suppliers, and anticipate challenges, ensuring your metal dresser procurement aligns with local market conditions and operational needs.
Strategic Sourcing Conclusion and Outlook for metal dresser
In today’s dynamic industrial landscape, sourcing a metal dresser requires a strategic approach that balances quality, cost-efficiency, and supplier reliability. For international B2B buyers—especially those in Africa, South America, the Middle East, and Europe—understanding the nuances of metal types, fabrication methods, and global supply chain intricacies is essential. Prioritizing suppliers with proven expertise, certifications, and adaptive manufacturing capabilities will safeguard your projects against delays and quality risks.
Key takeaways for effective procurement include:
- Material selection aligned with application needs, ensuring durability and compliance with regional standards.
- Supplier vetting based on capacity, innovation, and responsiveness, enabling scalable and flexible sourcing.
- Leveraging technology and data-driven insights to anticipate market shifts and optimize inventory management.
Looking ahead, the metal dresser market is poised for continued evolution driven by sustainability demands, digital transformation, and regional manufacturing growth. Buyers who embrace strategic partnerships and proactive sourcing will unlock competitive advantages and resilience in their supply chains.
Actionable Insight: Engage early with trusted global suppliers to co-develop tailored metal dresser solutions that meet your specific operational and environmental requirements. This approach will position your business for long-term success and adaptability across diverse markets.