Definitive Guide to Sourcing High-Quality Dresser Coupling
Guide to Dresser Coupling
- Introduction: Navigating the Global Market for dresser coupling
- Understanding dresser coupling Types and Variations
- Key Industrial Applications of dresser coupling
- Strategic Material Selection Guide for dresser coupling
- In-depth Look: Manufacturing Processes and Quality Assurance for dresser coupling
- Comprehensive Cost and Pricing Analysis for dresser coupling Sourcing
- Spotlight on Potential dresser coupling Manufacturers and Suppliers
- Essential Technical Properties and Trade Terminology for dresser coupling
- Navigating Market Dynamics, Sourcing Trends, and Sustainability in the dresser coupling Sector
- Frequently Asked Questions (FAQs) for B2B Buyers of dresser coupling
- Strategic Sourcing Conclusion and Outlook for dresser coupling
Introduction: Navigating the Global Market for dresser coupling
In the dynamic landscape of global pipeline infrastructure, dresser couplings play a pivotal role in ensuring secure, flexible, and leak-proof connections across diverse industrial applications. For international B2B buyers—particularly those operating in Africa, South America, the Middle East, and Europe—understanding the nuances of dresser couplings is essential to optimize project outcomes, maintain system integrity, and meet stringent regulatory standards.
This comprehensive guide delves into every critical aspect of dresser couplings, equipping procurement professionals and engineers with the knowledge to make informed sourcing decisions. From an in-depth exploration of various coupling types—such as flexible Style 38, long gap-bridging Style 40, and robust repair clamps—to the selection of appropriate materials tailored for temperature, pressure, and environmental conditions, this resource addresses the complexities buyers face in international markets.
Further, the guide covers manufacturing standards and quality control processes that guarantee reliability and longevity, highlighting trusted suppliers known for their expertise and rapid delivery capabilities. Cost considerations and market trends are analyzed to help buyers balance budget constraints with performance requirements, while a detailed FAQ section answers common technical and logistical queries.
By synthesizing technical detail with market intelligence, this guide empowers B2B buyers in regions like Argentina, South Africa, and beyond to confidently navigate supplier options, comply with local and international standards, and secure high-quality dresser couplings that underpin critical pipeline operations worldwide.
Understanding dresser coupling Types and Variations
Type Name | Key Distinguishing Features | Primary B2B Applications | Brief Pros & Cons for Buyers |
---|---|---|---|
Style 38 Couplings | Flexible, leak-proof design with easy installation | Water, gas, and industrial piping requiring flexible joints | Pros: Quick installation, flexible for misalignment; Cons: Limited for very high-pressure systems |
Style 40 Long Couplings | Extended length to bridge wider pipe gaps | Repairs or installations with irregular pipe end spacing | Pros: Accommodates larger gaps, versatile; Cons: Bulkier, may require more space |
Style 62 Reducing Couplings | Designed for pipe size reduction and joining dissimilar pipes | Transitioning between pipe sizes/materials in pipelines | Pros: Enables size/material transitions; Cons: Specialized use limits universal application |
Style 65 Couplings | Pre-assembled sealing coupling for immediate use | Rapid repair and maintenance in water and gas pipelines | Pros: Ready to use, reduces downtime; Cons: May have higher upfront cost |
Style 118 Repair Clamps | Low-cost band clamp for repairing small leaks or holes | Emergency pipeline repairs in steel piping systems | Pros: Cost-effective, fast repair; Cons: Limited to minor damages, not suitable for major structural repairs |
Style 38 Couplings
Style 38 couplings are recognized for their flexibility and leak-proof sealing, making them ideal for pipelines where slight misalignment or movement occurs. They are extensively used in water, gas, and industrial piping systems. For B2B buyers, these couplings offer ease of installation and adaptability, reducing labor costs and downtime. However, they may not be suitable for extremely high-pressure applications or where rigid connections are required, so assessing pipeline pressure specifications is critical.
Style 40 Long Couplings
These couplings feature an extended body length designed to bridge wider gaps between pipe ends, common in repair or retrofit projects where pipe ends do not meet closely. They are highly valuable in industries with aging infrastructure or irregular pipe configurations. Buyers should consider the available installation space and the coupling’s physical bulk when specifying these products, as well as ensuring compatibility with pipe materials and pressure ratings.
Style 62 Reducing Couplings
Style 62 couplings are specialized for reducing pipe diameter or transitioning between different pipe classes or materials, such as steel to cast iron. This makes them indispensable in complex pipeline networks requiring size or material changes without welding or flanging. For B2B procurement, understanding the exact pipe dimensions and material types is essential to ensure a proper fit and maintain system integrity, especially in high-stress environments.
Style 65 Couplings
Pre-assembled and ready to install, Style 65 couplings are designed for rapid deployment during maintenance or emergency repairs. Their sealing reliability minimizes downtime, which is a significant advantage for operations where pipeline availability is critical. Buyers should weigh the higher initial cost against the value of reduced labor time and operational disruption, making these couplings a strategic choice for critical infrastructure.
Style 118 Repair Clamps
These low-cost, band-type clamps provide a quick and effective solution for repairing small leaks or holes in steel pipelines. They are widely used for emergency repairs, enabling pipeline operators to avoid costly shutdowns. While highly cost-effective, buyers must recognize their limitations; these clamps are not suited for large breaks or structural repairs. Proper assessment of damage size and pipeline conditions is crucial before selection.
Key B2B Considerations:
When selecting dresser coupling types, international buyers should evaluate pipeline specifications including diameter, pressure, temperature, and material compatibility. Regional infrastructure conditions, such as aging pipes in South America or high-pressure gas lines in the Middle East, influence the ideal coupling type. Additionally, sourcing from distributors offering same-day shipping and customization options can significantly improve project timelines and reduce inventory costs. Understanding these variations empowers buyers in Africa, Europe, and beyond to optimize their pipeline solutions effectively.
Related Video: Dresser Coupling – Installation Guide
Key Industrial Applications of dresser coupling
Industry/Sector | Specific Application of dresser coupling | Value/Benefit for the Business | Key Sourcing Considerations for this Application |
---|---|---|---|
Oil & Gas | Pipeline repair and flexible joint connections | Minimizes downtime, maintains pipeline integrity | Compatibility with high pressure and temperature, corrosion resistance, API certification |
Water & Wastewater | Leak-proof sealing and repair of water distribution pipes | Reduces water loss, ensures regulatory compliance | Material suitability for potable water, durability under varying pressures, ease of installation |
Industrial Manufacturing | Connecting and repairing process piping systems | Enhances operational efficiency, reduces maintenance | Chemical compatibility, temperature and pressure ratings, availability of custom sizes |
Mining & Minerals | Heavy-duty pipeline connections for slurry and fluid transport | Ensures reliable transport of abrasive materials | Abrasion resistance, robustness, adaptability to harsh environments |
HVAC & Building Services | Flexible connections in heating and cooling systems | Facilitates thermal expansion, reduces vibration issues | Material compatibility with HVAC fluids, flexibility, long service life |
Oil & Gas
In the oil and gas sector, dresser couplings play a critical role in pipeline repair and creating flexible joints that accommodate pipeline movement and thermal expansion. These couplings help minimize costly downtime by enabling quick repairs without welding, which is crucial for remote or challenging locations common in Africa and the Middle East. Buyers must prioritize couplings that meet stringent API standards and withstand high pressure and temperature conditions while resisting corrosion caused by hydrocarbons and environmental factors.
Water & Wastewater
Dresser couplings are widely used in water distribution and wastewater management to provide leak-proof sealing and efficient pipe repairs. For utilities in South America and Europe, these couplings help reduce water loss and maintain compliance with environmental regulations. International buyers should focus on materials certified for potable water use and ensure the product can endure varying pressures and temperature ranges typical in municipal water systems. Ease of installation is also key to reduce labor costs and downtime.
Industrial Manufacturing
Manufacturing plants rely on dresser couplings for connecting and repairing process piping systems that transport gases, liquids, and chemicals. These couplings improve operational efficiency by allowing maintenance without extensive pipe replacement. For buyers in industrial hubs in Europe and South Africa, it is essential to select couplings compatible with the specific chemicals involved, and those rated for the pressure and temperature conditions of the process. Availability of custom sizes ensures seamless integration into existing systems.
Mining & Minerals
In mining operations, dresser couplings are used to join heavy-duty pipelines that transport abrasive slurries and fluids. The couplings must provide robust, abrasion-resistant connections capable of withstanding harsh environmental conditions found in regions like South Africa and parts of South America. Buyers should consider couplings made from durable materials and designed for easy on-site installation to avoid operational delays and costly shutdowns.
HVAC & Building Services
Dresser couplings facilitate flexible connections in heating, ventilation, and air conditioning systems, accommodating thermal expansion and reducing vibration. This application is vital for commercial and industrial buildings across Europe and the Middle East, where system reliability and longevity are paramount. Buyers should ensure the couplings are compatible with HVAC fluids, provide sufficient flexibility, and offer a long service life to minimize maintenance needs and operational disruptions.
Strategic Material Selection Guide for dresser coupling
Carbon Steel
Key Properties: Carbon steel is widely used for dresser couplings due to its excellent mechanical strength and moderate corrosion resistance when properly coated or painted. It typically supports temperature ranges up to 400°F (204°C) and pressure ratings suitable for most water, gas, and oil pipeline applications.
Pros & Cons: Carbon steel offers a cost-effective solution with high durability and ease of manufacturing. However, it is prone to corrosion if not adequately protected, which can lead to maintenance challenges in humid or corrosive environments. Its weight is higher compared to some alternatives, which may impact handling and installation logistics.
Impact on Application: Carbon steel dresser couplings are ideal for general-purpose pipelines transporting water, natural gas, and non-corrosive fluids. They are less suitable for highly corrosive media or environments with aggressive chemicals unless paired with specialized coatings or liners.
International Buyer Considerations: Buyers in Africa, South America, the Middle East, and Europe should ensure compliance with ASTM A105/A216 standards or equivalent EN/DIN standards common in Europe. In regions like South Africa and Argentina, availability and cost-effectiveness make carbon steel a preferred choice, but corrosion protection strategies must be planned for local climatic conditions.
Stainless Steel (Grades 304 and 316)
Key Properties: Stainless steel, particularly grades 304 and 316, offers superior corrosion resistance, excellent strength, and good temperature tolerance (up to 870°F / 465°C for 304 and higher for 316). Grade 316 has enhanced resistance to chlorides and marine environments.
Pros & Cons: Stainless steel couplings provide longevity and minimal maintenance in corrosive environments, making them suitable for aggressive chemicals and saltwater exposure. The main drawback is the higher cost and more complex manufacturing process compared to carbon steel.
Impact on Application: These materials are preferred for pipelines handling corrosive fluids, seawater, or where hygiene is critical, such as in food processing or pharmaceuticals. Their resistance to rust and staining makes them ideal for Middle Eastern and coastal African markets.
International Buyer Considerations: Compliance with ASTM A182 or EN 1.4301/1.4401 standards is common. Buyers from Europe and South America often require certification for traceability and quality assurance. The higher initial investment is offset by reduced lifecycle costs in corrosive environments.
Ductile Iron
Key Properties: Ductile iron offers high tensile strength and good impact resistance with moderate corrosion resistance. It typically withstands pressures up to 300 psi and temperatures up to 250°F (121°C).
Pros & Cons: It is more resistant to cracking and deformation than traditional cast iron, providing durability in underground and water pipeline applications. However, it is heavier and less corrosion-resistant than stainless steel, often requiring protective coatings.
Impact on Application: Ductile iron dresser couplings are commonly used in water and wastewater systems, especially in municipal infrastructure. Their robustness suits rough handling and installation in developing regions.
International Buyer Considerations: ASTM A536 and EN 1563 standards apply. In South America and Africa, ductile iron is favored for water distribution due to local manufacturing capabilities and cost-effectiveness. Buyers should consider local corrosion conditions and ensure appropriate coatings are applied.
Brass/Bronze
Key Properties: Brass and bronze alloys provide good corrosion resistance, especially against freshwater and mildly corrosive environments, with moderate strength and ductility. They typically tolerate temperatures up to 400°F (204°C).
Pros & Cons: These materials resist scaling and biofouling, making them suitable for potable water and HVAC systems. However, they are less suitable for high-pressure or highly corrosive industrial applications and tend to be more expensive than carbon steel.
Impact on Application: Ideal for smaller diameter couplings in plumbing, water supply, and light industrial applications where corrosion resistance and ease of installation are priorities.
International Buyer Considerations: Compliance with ASTM B62 or EN 1982 is typical. In markets like Europe and the Middle East, brass/bronze couplings are preferred for potable water due to health and safety regulations. Buyers should be aware of lead content restrictions in some regions.
Material | Typical Use Case for dresser coupling | Key Advantage | Key Disadvantage/Limitation | Relative Cost (Low/Med/High) |
---|---|---|---|---|
Carbon Steel | General service pipelines for water, gas, and oil | Cost-effective, strong, widely available | Prone to corrosion without protection | Low |
Stainless Steel (304/316) | Corrosive fluids, seawater, food and pharmaceutical industries | Excellent corrosion resistance, durable | Higher cost, complex manufacturing | High |
Ductile Iron | Water and wastewater infrastructure, municipal pipelines | High strength, impact resistant | Heavy, moderate corrosion resistance | Medium |
Brass/Bronze | Potable water, HVAC, light industrial applications | Good corrosion resistance, easy to install | Less suitable for high pressure, higher cost | Medium to High |
In-depth Look: Manufacturing Processes and Quality Assurance for dresser coupling
Manufacturing Processes of Dresser Couplings
Dresser couplings are precision-engineered pipe joining solutions widely used in industries such as oil and gas, waterworks, and industrial piping systems. Understanding their manufacturing process is critical for B2B buyers seeking reliable, high-performance products. The manufacturing of dresser couplings typically involves the following key stages:
1. Material Preparation
High-grade raw materials form the foundation for durable dresser couplings. Common materials include ductile iron, carbon steel, stainless steel, or specialty alloys depending on application requirements. Material preparation involves cutting billets or castings to size, heat treatment to enhance mechanical properties, and surface cleaning to remove impurities. Suppliers often source materials compliant with international standards (e.g., ASTM, EN) to ensure consistency and traceability.
2. Forming and Machining
Coupling bodies are formed primarily through forging or casting followed by precision machining. Forging enhances strength and toughness by aligning metal grain structures, making it a preferred method for critical couplings. Machining operations such as turning, milling, drilling, and threading are performed on CNC machines to achieve tight dimensional tolerances and smooth surfaces essential for leak-proof joints.
3. Assembly
Assembly includes fitting components such as gaskets, bolts, nuts, and sealing elements. Gaskets, often made from rubber compounds or elastomers, are precision-molded to provide flexible, long-lasting seals. Bolts and nuts are typically high-strength steel with corrosion-resistant coatings. Assembly lines incorporate checks for proper alignment and torque specifications to ensure reliable mechanical integrity.
4. Finishing
Finishing processes involve surface treatments to improve corrosion resistance and aesthetics. Common finishes include epoxy coatings, galvanizing, or powder coating, selected based on the intended operating environment. Final cleaning and drying prepare the coupling for packaging. Some manufacturers also apply protective films or wraps for enhanced storage and shipping protection.
Quality Assurance and Control Protocols
For international B2B buyers, particularly from diverse markets such as Africa, South America, the Middle East, and Europe, quality assurance (QA) and quality control (QC) are paramount to mitigate risks related to performance failure and regulatory compliance. Leading dresser coupling manufacturers adopt rigorous QA/QC systems aligned with global and industry-specific standards.
Relevant International Standards
- ISO 9001: The backbone of quality management systems globally, ensuring consistent manufacturing practices, continuous improvement, and customer satisfaction.
- API (American Petroleum Institute) Standards: Particularly relevant for oil and gas applications, covering material specifications, pressure ratings, and testing protocols.
- CE Marking: Required in European markets, indicating conformity with health, safety, and environmental protection standards.
- EN Standards (European Norms): Cover material, design, and testing for pipe fittings and couplings within Europe.
- Other Regional Standards: Buyers should verify compliance with local standards such as SABS (South Africa Bureau of Standards) or IRAM (Argentina Institute of Standardization and Certification).
Quality Control Checkpoints
Manufacturers implement QC at multiple stages to ensure product integrity:
- Incoming Quality Control (IQC): Inspection and testing of raw materials, including chemical composition analysis and mechanical property verification, prevent defects at the source.
- In-Process Quality Control (IPQC): Continuous monitoring during forming, machining, and assembly phases, including dimensional inspections and torque checks, ensures adherence to specifications.
- Final Quality Control (FQC): Comprehensive testing on completed couplings, such as pressure tests, leak tests, visual inspections, and coating thickness measurements, validate finished product quality.
Common Testing Methods
- Hydrostatic Pressure Testing: Simulates operating pressures to verify coupling integrity and sealing performance under stress.
- Non-Destructive Testing (NDT): Techniques such as magnetic particle inspection or ultrasonic testing detect internal or surface defects without damaging the coupling.
- Dimensional Inspection: Uses precision gauges and coordinate measuring machines (CMM) to confirm compliance with design tolerances.
- Material Testing: Includes hardness testing, tensile strength, and impact tests to confirm mechanical properties meet standards.
- Coating and Corrosion Resistance Tests: Salt spray tests and adhesion checks assess surface protection efficacy.
How B2B Buyers Can Verify Supplier Quality
For buyers from Africa, South America, the Middle East, and Europe, verifying supplier quality assurance is crucial to avoid costly failures and delays. Recommended strategies include:
- Supplier Audits: Conduct on-site or virtual audits focusing on manufacturing processes, QA/QC systems, and compliance documentation. Audits help verify that the supplier consistently follows prescribed standards and best practices.
- Review of Quality Documentation: Request certificates of conformity, material test reports (MTRs), inspection records, and ISO 9001 certification copies. Thorough document review confirms supplier claims and product traceability.
- Third-Party Inspections: Engage independent inspection agencies to perform factory acceptance tests (FAT), witness pressure tests, and verify final product quality before shipment. This adds an unbiased layer of quality assurance.
- Sample Testing: Where feasible, obtain product samples for in-house or third-party laboratory testing to validate performance characteristics.
- Long-Term Supplier Relationships: Prioritize suppliers with proven track records and references from companies within your region or industry sector.
Quality Assurance Considerations for International Markets
International buyers must navigate additional complexities related to regional compliance, logistics, and environmental conditions:
- Compliance with Local Regulations: Ensure the dresser coupling supplier understands and adheres to local piping codes and environmental standards. For example, European buyers may require CE marking and REACH compliance, while African or South American buyers may focus on SABS or IRAM certifications.
- Adapting to Climate and Operating Conditions: Verify that manufacturing and finishing processes account for environmental factors such as high humidity, temperature extremes, or corrosive atmospheres common in Middle Eastern or coastal African regions.
- Documentation and Language: Insist on complete, clear documentation in your preferred language, including user manuals, maintenance guidelines, and certification translations to ease regulatory approvals and on-site use.
- After-Sales Support and Warranty: Quality assurance extends beyond manufacturing. Choose suppliers offering robust after-sales service, warranty coverage, and technical support to address issues promptly in your region.
- Supply Chain Transparency: Given global logistics challenges, buyers should evaluate supplier capacity for timely delivery, availability of spare parts, and responsiveness to urgent orders, especially critical for infrastructure projects in developing markets.
Summary
Investing in dresser couplings from reputable manufacturers with transparent and robust manufacturing and quality assurance practices is essential for international B2B buyers. Understanding the detailed production stages—from raw material preparation to final finishing—and the rigorous QC checkpoints aligned with international standards empowers buyers to make informed procurement decisions. Leveraging audits, third-party inspections, and thorough document verification helps mitigate risks, ensuring that the couplings delivered meet stringent performance and safety requirements tailored to the diverse needs of markets across Africa, South America, the Middle East, and Europe.
Related Video: Complete Process of Textile Manufacturing Fiber to Complete Garments
Comprehensive Cost and Pricing Analysis for dresser coupling Sourcing
Understanding the Cost Structure of Dresser Couplings
When sourcing dresser couplings, it is crucial for international B2B buyers to dissect the cost components that form the final price. These components typically include:
- Raw Materials: The predominant cost driver, materials such as carbon steel, ductile iron, or stainless steel vary significantly in price depending on global commodity markets. Premium-grade alloys or specialized gaskets (e.g., lifetime sealing gaskets) add to material costs.
- Labor and Manufacturing Overhead: Skilled labor for precision forging, machining, assembly, and quality control contributes to the cost. Overhead includes factory utilities, equipment depreciation, and maintenance.
- Tooling and Equipment: Initial tooling for casting or forging dresser coupling components is capital intensive but amortized over production runs, impacting unit cost especially for smaller orders.
- Quality Control and Certification: Rigorous testing, certifications (e.g., ISO, API standards), and compliance with international standards enhance product reliability but increase costs.
- Logistics and Supply Chain: Shipping costs, customs duties, packaging, and handling fees vary by region. Same-day or expedited shipping options generally come at a premium.
- Margin and Distribution: Distributors and suppliers factor in their margins based on service levels, inventory holding, and after-sales support.
Key Pricing Influencers for International Buyers
Several factors influence the final price of dresser couplings, particularly for buyers in Africa, South America, the Middle East, and Europe:
- Order Volume and Minimum Order Quantities (MOQs): Larger orders typically yield volume discounts. For smaller buyers or those requiring diverse sizes, costs per unit may be higher.
- Product Specifications and Customization: Custom dimensions, temperature or pressure ratings, and special coatings or materials tailored for harsh environments can increase pricing.
- Material Quality and Certification: Higher-grade materials with certified traceability and compliance to international standards command premium pricing but reduce long-term risk.
- Supplier Reputation and Location: Established suppliers with proven track records may price higher but offer reliability, warranty, and technical support. Proximity to manufacturing hubs or distributors affects logistics costs.
- Incoterms and Shipping Terms: Terms like FOB, CIF, or DDP significantly affect landed costs. Buyers should understand responsibilities for shipping, insurance, and customs clearance to avoid unexpected expenses.
Actionable Buyer Tips for Cost-Effective Sourcing
International B2B buyers should adopt strategic approaches to optimize cost-efficiency and total cost of ownership (TCO):
- Leverage Volume Consolidation: Pooling requirements across projects or partners can help achieve better pricing through economies of scale.
- Request Detailed Quotes: Ask suppliers for transparent cost breakdowns, including tooling charges, certification fees, and shipping. This enables targeted negotiation.
- Negotiate Payment and Delivery Terms: Flexible terms such as deferred payments or staggered deliveries can improve cash flow and reduce inventory carrying costs.
- Factor in Lifecycle Costs: Cheaper initial prices may lead to higher maintenance or replacement costs. Prioritize quality and warranty to minimize downtime and rework.
- Understand Regional Import Regulations: Import duties, taxes, and compliance requirements differ by country. Engage local customs experts to avoid delays and additional costs.
- Use Trusted Distributors with Local Presence: Suppliers or distributors with warehouses in your region (e.g., South Africa, Argentina) can reduce lead times and logistics costs.
- Clarify Incoterms: Ensure clarity on shipping terms to avoid hidden fees and disputes. For instance, DDP terms transfer most responsibilities to the seller, easing buyer logistics.
Pricing Nuances by Region
- Africa & Middle East: Infrastructure projects often require robust, certified products. Buyers should emphasize supplier reliability and consider local content rules affecting customs.
- South America: Currency volatility and import tariffs can impact landed cost; negotiating in USD with suppliers and exploring bonded warehouses may mitigate risks.
- Europe: High standards for certification and environmental compliance influence pricing. Buyers benefit from suppliers familiar with EU regulations and standards.
Disclaimer on Pricing
Prices for dresser couplings can fluctuate widely based on raw material markets, geopolitical factors, and supplier capacity. The insights provided are indicative to aid buyer understanding and negotiation strategy but should not be used as fixed pricing benchmarks. Always obtain current, detailed quotations tailored to your exact specifications and sourcing conditions.
By thoroughly understanding these cost and pricing dynamics, international B2B buyers can make informed sourcing decisions, optimize procurement budgets, and establish sustainable supply partnerships for dresser coupling products.
Spotlight on Potential dresser coupling Manufacturers and Suppliers
This section offers a look at a few manufacturers active in the ‘dresser coupling’ market. This is a representative sample for illustrative purposes; B2B buyers must conduct their own extensive due diligence before any engagement. Information is synthesized from public sources and general industry knowledge.
Essential Technical Properties and Trade Terminology for dresser coupling
Critical Technical Properties of Dresser Couplings
Understanding the essential technical specifications of dresser couplings is key for international B2B buyers to ensure compatibility, safety, and long-term performance in pipeline applications.
-
Material Grade
Dresser couplings are commonly manufactured from ductile iron, carbon steel, or stainless steel. Material grade affects corrosion resistance, strength, and suitability for different environments—such as water, gas, or industrial fluids. Selecting the correct material grade is crucial to meet regional standards and operational conditions, especially in diverse climates found across Africa, South America, the Middle East, and Europe. -
Pressure Rating
The pressure rating (usually expressed in PSI or bar) indicates the maximum internal pressure the coupling can safely withstand. Buyers must verify that the coupling’s pressure rating aligns with the pipeline’s operating pressure to prevent leaks or failures. Dresser couplings often support a wide range of pressure classes to accommodate different industrial needs. -
Temperature Range
Couplings are designed to function within specific temperature limits, often from sub-zero to high temperatures depending on gasket and material composition. This is particularly important for buyers in regions with extreme weather or processes involving high-temperature fluids. Ensuring the coupling can operate safely within the temperature spectrum of the application reduces the risk of gasket failure or metal fatigue. -
Pipe Size and Dimensional Tolerance
Dresser couplings are sized by the pipe’s outside diameter (OD) and must fit precisely. Dimensional tolerance defines acceptable variations in pipe and coupling dimensions. Precise sizing ensures leak-proof sealing and mechanical integrity. For international buyers, confirming that couplings meet recognized standards (e.g., ANSI, ISO) for dimensions avoids compatibility issues with locally sourced pipes. -
Gasket Type and Sealing Technology
Gaskets inside dresser couplings provide the seal between pipes. Common gasket materials include EPDM, Nitrile, or Life-Time gaskets that offer long-lasting flexibility and chemical resistance. The gasket’s design and material must match the pipeline medium (water, gas, oil) and environmental conditions, ensuring leak-proof connections and minimizing maintenance. -
Expansion and Movement Accommodation
Certain dresser couplings, such as expansion joints, are engineered to absorb pipe movement caused by thermal expansion, ground settlement, or vibration. This property is critical for pipeline longevity and safety, especially in seismic zones or large infrastructure projects common in many international markets.
Key Trade Terminology for International B2B Buyers
Familiarity with common trade and industry terms will empower buyers to communicate effectively with suppliers and negotiate better deals.
-
OEM (Original Equipment Manufacturer)
Refers to the company that originally manufactures the dresser coupling. Purchasing directly from OEMs or authorized distributors ensures product authenticity, warranty coverage, and access to technical support. -
MOQ (Minimum Order Quantity)
The smallest number of units a supplier is willing to sell in one order. Understanding MOQ helps buyers plan procurement efficiently, especially when balancing inventory costs and project timelines. MOQ can vary by coupling style, size, or customization. -
RFQ (Request for Quotation)
A formal inquiry sent by buyers to suppliers requesting detailed pricing, availability, and delivery terms for specific dresser coupling products. RFQs are essential for comparing offers and securing competitive pricing in international trade. -
Incoterms (International Commercial Terms)
A set of standardized trade terms published by the International Chamber of Commerce that define responsibilities for shipping, insurance, and tariffs between buyers and sellers. Common Incoterms include FOB (Free on Board), CIF (Cost, Insurance, and Freight), and DDP (Delivered Duty Paid). Clarity on Incoterms ensures smooth customs clearance and cost transparency. -
Lead Time
The period between placing an order and receiving the product. Knowing lead times is vital for project scheduling and avoiding costly delays, especially when sourcing products from distant suppliers or during peak demand seasons. -
Certification and Standards Compliance
Products may carry certifications such as ISO, ASTM, or regional approvals that verify quality and safety compliance. Buyers should request documentation confirming compliance to meet regulatory requirements and facilitate local approvals.
Equipped with a clear understanding of these technical properties and trade terms, international B2B buyers can make informed purchasing decisions, optimize supply chain logistics, and ensure successful pipeline project outcomes using dresser couplings.
Navigating Market Dynamics, Sourcing Trends, and Sustainability in the dresser coupling Sector
Market Overview & Key Trends
The global dresser coupling market is experiencing steady growth driven by expanding infrastructure projects and rising demand in oil, gas, water, and industrial pipeline sectors. For international B2B buyers from regions such as Africa, South America, the Middle East, and Europe, understanding local market dynamics and global supply trends is critical for effective sourcing and procurement.
Key market drivers include:
- Infrastructure development: Emerging economies in Africa and South America, including countries like South Africa and Argentina, are investing heavily in pipeline networks to improve water distribution, natural gas transportation, and industrial fluid handling. This fuels demand for versatile and reliable coupling solutions.
- Energy sector growth: The Middle East and parts of Europe continue to see robust activity in oil and gas exploration and transmission, necessitating high-performance pipeline components that withstand pressure and temperature fluctuations.
- Technological advancements: Modern dresser couplings incorporate enhanced gasket materials and corrosion-resistant alloys, improving durability and reducing maintenance costs. Buyers should prioritize suppliers offering these innovations to extend asset life.
- Supply chain agility: Same-day or expedited shipping options, as well as local stocking of popular sizes and styles (e.g., Style 38, Style 65, Style 90), are increasingly important for minimizing downtime. Distributors with strong regional presence and flexible logistics solutions provide a competitive advantage.
- Customization capabilities: The ability to source couplings tailored to specific pipe diameters, materials, and pressure ratings is highly valued. Suppliers offering made-to-order or engineered solutions help buyers address unique project requirements efficiently.
Emerging sourcing trends:
- Growing preference for suppliers who provide comprehensive product portfolios, including repair clamps, expansion joints, and flange adapters, enabling consolidated procurement.
- Increased digital integration, with buyers leveraging online catalogs, instant quoting tools, and real-time inventory visibility to streamline purchasing.
- Focus on supplier reliability and certifications, particularly in regions where regulatory standards are evolving or becoming more stringent.
Understanding these market and sourcing trends enables international buyers to optimize their procurement strategies, reduce lead times, and ensure pipeline integrity across diverse applications.
Sustainability & Ethical Sourcing in B2B
Sustainability is becoming a decisive factor in the dresser coupling sector as industries worldwide intensify efforts to reduce environmental impact and promote responsible supply chains. For B2B buyers across Africa, South America, the Middle East, and Europe, integrating sustainability into sourcing decisions is increasingly essential to meet regulatory requirements and stakeholder expectations.
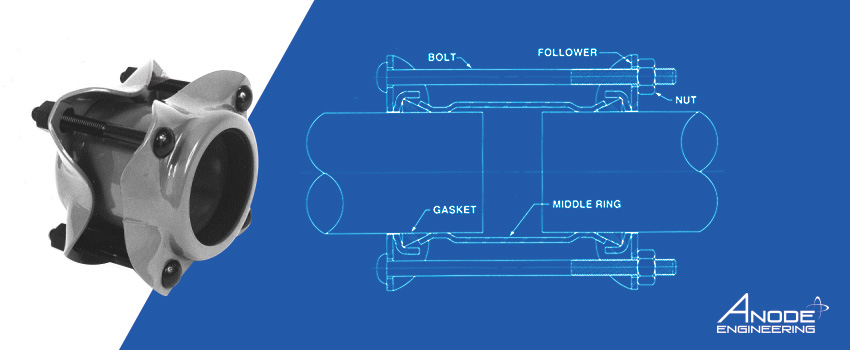
Illustrative Image (Source: Google Search)
Environmental impact considerations:
- Manufacturing processes for couplings involve significant energy consumption and raw material use, particularly steel and rubber for gaskets. Selecting suppliers who implement energy-efficient production methods and waste reduction protocols can lower the overall carbon footprint.
- Durable, leak-proof coupling designs contribute to preventing pipeline leaks and minimizing environmental contamination, thereby supporting long-term sustainability goals.
- Preference for materials with recycled content or those sourced from suppliers with certified sustainable practices helps reduce resource depletion.
Ethical supply chain importance:
- Transparency in sourcing raw materials ensures compliance with international labor standards and avoids association with conflict minerals or unethical practices.
- Buyers increasingly demand traceability and certification from suppliers, such as ISO 14001 for environmental management or third-party audits verifying social responsibility.
- Partnering with manufacturers who maintain strict quality controls and uphold ethical labor conditions enhances brand reputation and mitigates supply risks.
Green certifications and materials:
- Some dresser coupling manufacturers are adopting eco-friendly gasket compounds that reduce hazardous substances and improve recyclability.
- Certifications related to environmental stewardship and sustainable manufacturing processes are becoming differentiators in supplier selection.
- Buyers should inquire about life-cycle assessments and supplier initiatives toward circular economy principles to align procurement with broader corporate sustainability policies.
By prioritizing sustainability and ethical sourcing, international B2B buyers not only contribute to global environmental goals but also secure resilient, compliant supply chains that support long-term business success.
Evolution and Historical Context
Dresser couplings have a rich history dating back to the early 20th century, originally developed to provide reliable, flexible connections in pipeline systems without the need for welding. Over the decades, the technology has evolved significantly, adapting to the increasing complexity and scale of industrial infrastructure.
Initially designed for oil and gas pipelines, dresser couplings expanded their application to water, wastewater, and industrial piping markets. Innovations such as improved gasket materials, bolted designs, and specialized styles (e.g., reducing couplings, expansion joints) have enhanced their versatility and performance.
For international buyers, understanding this evolution highlights the reliability and proven track record of dresser couplings in diverse environments. Their adaptability to different pipe materials and conditions makes them a cornerstone in modern pipeline construction and maintenance worldwide.
Related Video: Global Trade & Logistics – What is Global Trade?
Frequently Asked Questions (FAQs) for B2B Buyers of dresser coupling
-
How can I verify the credibility of a dresser coupling supplier for international procurement?
When sourcing dresser couplings internationally, prioritize suppliers with established industry experience and recognized certifications such as ISO 9001 or API standards. Request references from existing clients, particularly those in your region (Africa, South America, Middle East, Europe). Conduct due diligence by reviewing product datasheets, factory audits if possible, and verifying compliance with local and international standards. Partnering with authorized distributors or master distributors of reputable brands can further reduce risk and ensure product authenticity and quality. -
Are dresser couplings customizable to meet specific pipe dimensions and operating conditions?
Yes, many suppliers offer customization options for dresser couplings, including tailored sizes, materials, pressure ratings, and gasket types to fit unique pipeline requirements. For international buyers, it is crucial to provide detailed specifications such as pipe outer diameter (OD), material type, operating temperature, pressure, and fluid type. Early engagement with the supplier’s technical team helps ensure the coupling meets your system’s needs and complies with regional regulations or standards. -
What are typical minimum order quantities (MOQ) and lead times when ordering dresser couplings internationally?
MOQ and lead times vary widely depending on the supplier and product type. Standard stock items may have low MOQs and same-day or short lead times, while custom or large-diameter couplings often require higher MOQs and longer production cycles (4-8 weeks or more). Buyers from regions like Africa or South America should factor in additional shipping and customs clearance times. Negotiate terms upfront and request a detailed production and delivery timeline to align procurement planning with project schedules. -
Which payment terms are common for international B2B purchases of dresser couplings?
International transactions typically involve payment methods such as Letters of Credit (LC), Telegraphic Transfers (T/T), or open account terms for established buyers. LC offers added security by ensuring payment upon meeting agreed shipment and quality conditions. For new buyers, partial upfront payments combined with balance upon delivery are common. Always clarify payment terms in the contract, considering currency exchange risks and banking regulations in your country to avoid delays or disputes.
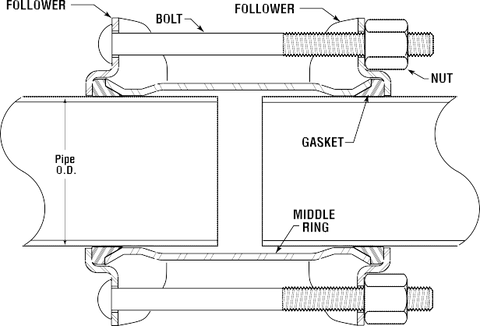
Illustrative Image (Source: Google Search)
-
What quality assurance and certifications should I expect with dresser couplings?
High-quality dresser couplings should come with certifications including ISO 9001 quality management, API (American Petroleum Institute) compliance, and material test reports (MTRs) confirming chemical and mechanical properties. Additionally, gaskets and seals must meet industry standards for durability and leak prevention. Request detailed quality documentation and inspection reports before shipment. For international buyers, certifications recognized by your country’s regulatory authorities or industry bodies are essential to facilitate customs clearance and project approvals. -
How can I optimize logistics and shipping for dresser couplings across continents?
To streamline international logistics, select suppliers experienced in exporting to your region who can handle customs documentation, packaging for long-distance transport, and compliance with import regulations. Consolidate orders to reduce freight costs and consider shipping modes (air, sea, or land) based on urgency and budget. Use freight forwarders familiar with your country’s customs procedures. Early coordination of delivery schedules with suppliers helps mitigate delays, especially in regions with complex import regulations like Africa and the Middle East. -
What steps should I take if there is a quality or delivery dispute with my dresser coupling supplier?
First, document all issues clearly with photographs, inspection reports, and delivery records. Communicate promptly with the supplier’s customer service or sales team to seek resolution, referencing contractual terms and warranty policies. For international disputes, leverage third-party inspection agencies or arbitration if necessary. Maintain all correspondence and quality certifications as evidence. Building relationships with suppliers who offer responsive after-sales support and clear dispute resolution mechanisms is critical to minimizing project disruptions. -
Are there specific regional considerations for sourcing dresser couplings in Africa, South America, the Middle East, and Europe?
Yes, regional factors such as local standards, climate conditions, and supply chain infrastructure impact sourcing decisions. For example, corrosive environments may require stainless steel couplings or special coatings. Compliance with regional certifications (e.g., CE marking in Europe) and import regulations is mandatory. Additionally, consider local currency fluctuations, trade tariffs, and political stability when negotiating contracts. Partnering with distributors or agents familiar with local market dynamics can provide valuable insights and smoother procurement processes.
Strategic Sourcing Conclusion and Outlook for dresser coupling
Key Takeaways and Strategic Sourcing Insights for Dresser Couplings
For international B2B buyers from Africa, South America, the Middle East, and Europe, sourcing dresser couplings effectively requires a clear understanding of product variety, quality standards, and supplier reliability. Dresser couplings offer versatile solutions ranging from flexible pipe connections to repair clamps and expansion joints, accommodating diverse pipeline materials and pressure requirements. Prioritizing suppliers with comprehensive inventory, same-day shipping capabilities, and technical support ensures minimized downtime and optimized project timelines.
Strategic sourcing should emphasize:
- Supplier partnerships with proven industry experience to guarantee product authenticity and performance.
- Customization options for specific pipe dimensions, materials, and environmental conditions prevalent in your region.
- Transparent pricing and logistics support, including currency considerations and import regulations for smooth procurement.
- Access to technical expertise to assist in product selection and compliance with local standards.
Looking Ahead: Embracing Innovation and Partnership
As infrastructure development accelerates globally, dresser coupling technologies continue to evolve, emphasizing durability and ease of installation. Buyers in emerging and established markets alike should leverage strategic supplier relationships to stay ahead of market demands and regulatory changes. Engaging with trusted distributors who offer rapid fulfillment and expert consultation will empower your operations, reduce risk, and enhance system longevity.
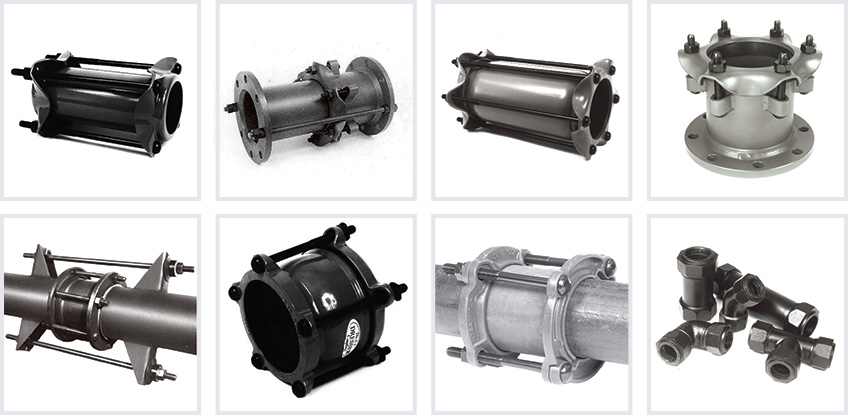
Illustrative Image (Source: Google Search)
Take action today by evaluating your current sourcing strategies and exploring partnerships with reputable dresser coupling suppliers who understand your regional needs. This proactive approach will position your business for resilience and growth in the dynamic global pipeline market.